iron ore magnetic separation process pdf
2020-01-26T02:01:14+00:00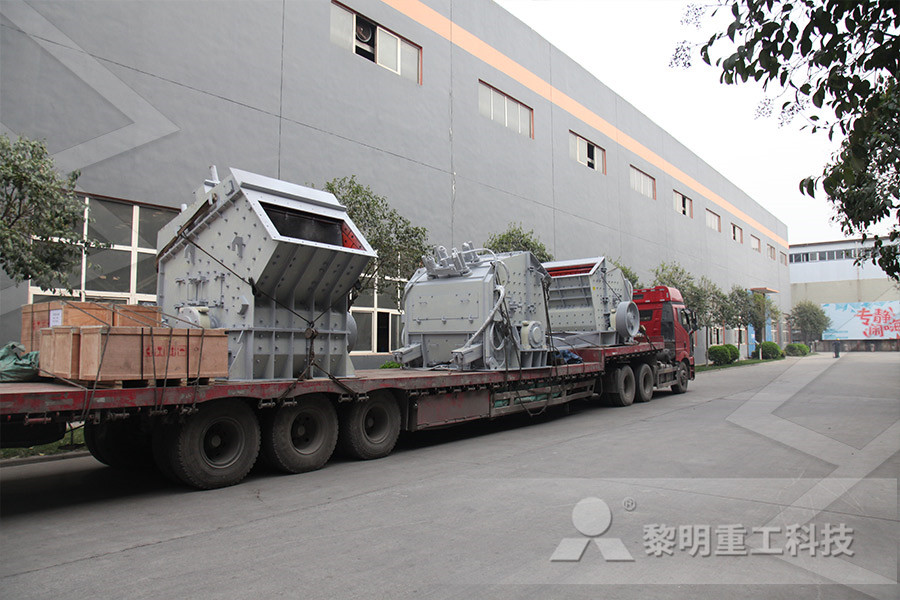
(PDF) Dry Magnetic Separation of Iron Ore of the
[Show full abstract] results show that the separation process of high intensity magneticreverse flotation can obtain an iron concentrate grading about 6662% at a recovery of magnetic separation Dry Magnetic Separation of Iron Ore: There are many inherent advantages in processes that utilize dry magnetic separation to beneficiate iron ore Wet concentration of magnetite ore, in comparison, re quires 500 to 1000 gal of water per ton of concen trate produced This means extensive use of waterADVANCES IN MAGNETIC SEPARATION OF ORES USACHYOV KORYTNY: MAGNETICGRAVITY SEPARATION OF IRON ORE 133 Nonmagnetic product Concentrate Feed Table 2Parameters ofMGseparation ofmagnetite concentrates inAlS Output,% Content,% Recovery,% +50 mk grade class Fe sio, Fe sto, Content"10 Recovery% Class Fe Class Fe III Stage separation concentrate 235 567 29 624 452 110 218 06 Magneticgravity separation of iron oreIn this work, separation of aluminium from a highaluminium lateritic iron ore was achieved by the process of ‘direct reduction with sodium sulfatemagnetic separation’, (PDF) HIGH INTENSITY MAGNETIC SEPARATION OF The process of magnetic separation of iron ore was carried out by a laboratory separator EVS10/5 Schematic diagram of the device is shown in Fig 1 Fig 1 Scheme of the magnetic separator EVS Dry Magnetic Separation of Iron Ore of the Bakchar Deposit
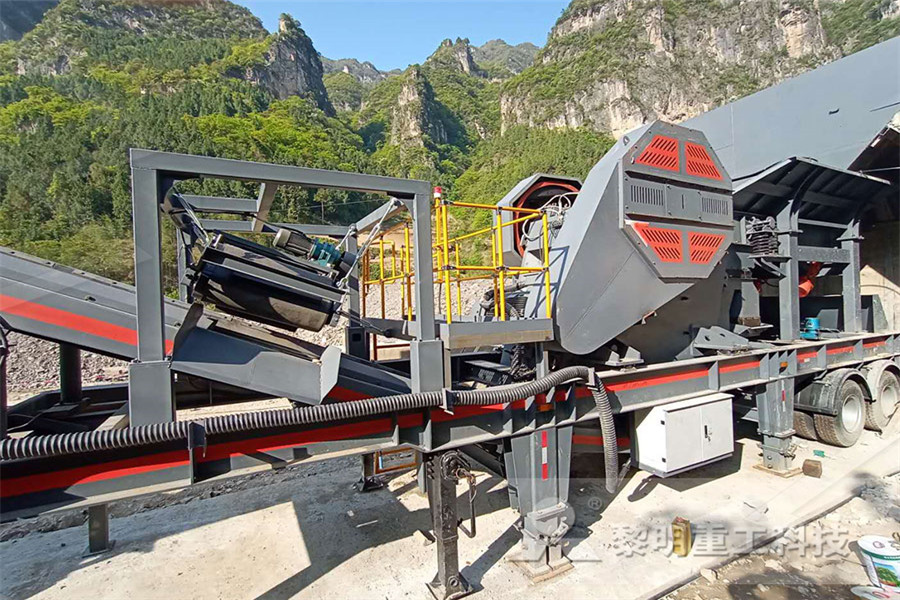
iron ore magnetic separation process pdf proves
iron ore magnetic separation process pdf Usachyov amp korytny magneticgravity separation of iron ore nonmagnetic product concentrate feed table parameters ofmgseparation ofmagnetite concentrates inals output, content, recovery, mk grade class fe sio, fe sto, contentquot recovery class fe class fe iii stage separation concentrate The separation process was applied on four mixtures of iron oxides as feed for the process They were having average grades 3294, 4143, 1700 and 4800% Fe The process of treatment gave concentrates having average grades from the feed 3979, 4982, 4767and 5276 % Fe and average iron recoveries were 8683, 8763, 7632 and 8351 % Dressing Weakly Magnetic Iron Ores by Dry Magnetic Magnetic elutriation improves the quality of lowgrade domestic iron ore by using an alternatingcurrent, pulsedmagnetic field to clean iron ore into a highly refined product This innovative process differs from conventional drum type magnetic separation systems by using permanent magnets that cause magnetic entrapmentMagnetic Elutriation Technology for Clean and Efficient –Process 600t/h lumpy iron ore • DMS Cyclone –Only 6mm material for iron ore –360mm diameter cyclone –Process 40t/h per cyclone • Larcodems –90+6mm stones –12m diameter –Operating capacity of 600800t/h –Efficient separation at SG’s as high as 41g/cm3 Dense Media Separation on Iron Ore •The Latest Developments in Iron Ore Processing USACHYOV KORYTNY: MAGNETICGRAVITY SEPARATION OF IRON ORE 133 Nonmagnetic product Concentrate Feed Table 2Parameters ofMGseparation ofmagnetite concentrates inAlS Output,% Content,% Recovery,% +50 mk grade class Fe sio, Fe sto, Content"10 Recovery% Class Fe Class Fe III Stage separation concentrate 235 567 29 624 452 110 218 06 Magneticgravity separation of iron ore
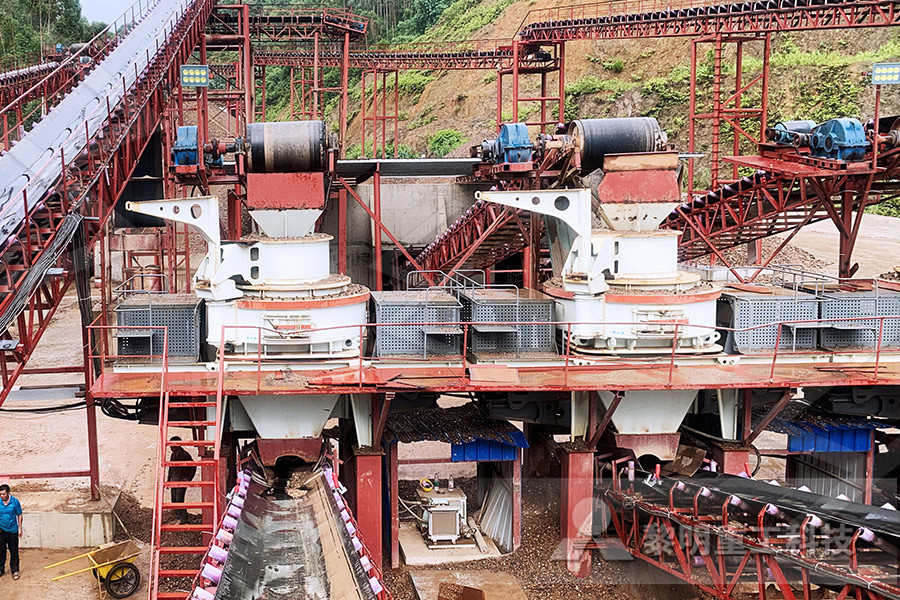
(PDF) Magnetic Separation of AlHussainyat Iron Ore
Magnetic Separation of AlHussainyat Iron Ore February 2019; University of Baghdad Engineering Journal 3(2):7591; Project: My MSc project Magnetic Separation is one of the physical concentration processes that utilizes the differences in magnetic properties of various minerals present in the ore body The magnetic fraction may be valuable or gangue depending upon its end use in a particular process and so also the nonmagnetic fraction, eg, separation of magnetite (magnetic) from quartz (nonmagnetic), separation of tin Magnetic Separation Principles and Application in separationhigh intensity magneticseparationreverse flotation flowsheet was chosen, in which highintensity magnetic separation is a very important process Through comparison of several types of highintensity magnetic separators, ten SLon1750 Vertical ring and Pulsating High Gradient Magnetic Separators were chosen for the highintensity SLON MAGNETIC SEPARATOR APPLIED TO UPGRADING This work presents a semismelting reduction and magnetic separation process for the recovery of iron and alumina slag from iron rich bauxite ore The effect of the process parameters on the recovery rate of iron, maximum particle size of the iron nugget, and the Al2O3 content of the alumina slag was investigated and optimized The results show that the iron nuggets and alumina slag can be [PDF] SemiSmelting Reduction and Magnetic Separation for already been grinded, separation process requires much less energy and can also decrease total costs of concentrate production Due to gradual depletion of iron ore reserves, more studies are devoted to tailings processing [37] The results of these works indicate the potential recovery of iron ore concentrates from mininginduced mineralRecovery of magnetitehematite concentrate from iron
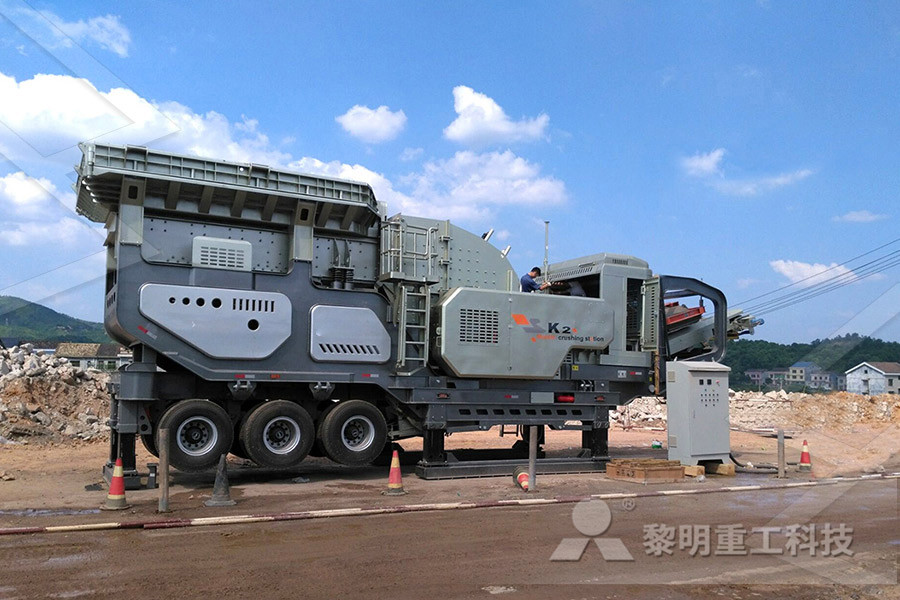
Discrete Event Simulation of an Iron Ore Milling Process
focuses on modeling an iron ore magnetic separation processing plant in Arena discrete event simulation software (Rockwell Automation) A typical iron ore processing plant, with several comminution and separation stages, is considered for simulation The flow sheet of the process is illustrated in Fig 1iron The magnetic concentrate designated direct reduced iron (DRI) was obtained by a twostage magnetic separation process, namely, the rough concentrate obtained from the first separation step was magnetically separated again The main evaluation indexes of the test results were the iron grade and the iron recovery of DRI The iron recovery Extraction of Iron from Refractory Titanomagnetite by making process Magnetic separation and flotation are the two commonly used iron beneficiation processes and selecting the most effective process to treat lowgrade ore d epends mainly on the mineralogical structure of the ore especially the aggregation of Iron with gangue minerals [5] Magnetic separation using wet highintensityRemoval of Silica and Alumina as Impurities from Low iron ore worldwide at lower insitu grades (generally about 2040% Fe), which can be readily enriched during beneficiation processes using gravity or magnetic separation to increase their purity to upward of 65% Fe In an economically viable operation, the cost of processing the ore can usually be offset by the price premium the highpurityUnderstanding the highgrade iron ore marketThis work presents a semismelting reduction and magnetic separation process for the recovery of iron and alumina slag from iron rich bauxite ore The effect of the process parameters on the recovery rate of iron, maximum particle size of the iron nugget, and the Al2O3 content of the alumina slag was investigated and optimized The results show that the iron nuggets and alumina slag can be [PDF] SemiSmelting Reduction and Magnetic
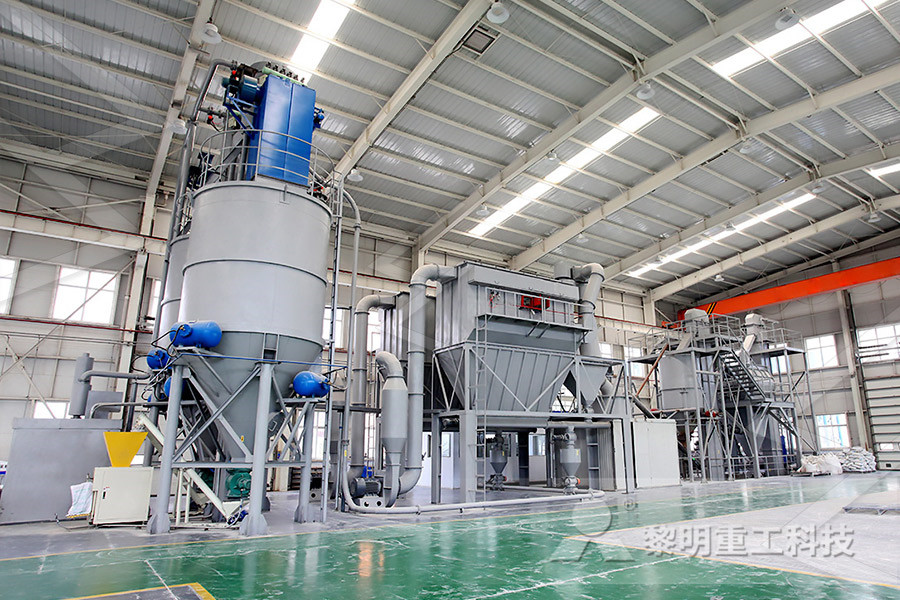
Recovery of magnetitehematite concentrate from iron
magnetitehematite concentrate from the tailings A processing flowsheet includes magnetic separation, milling and gravity concentration methods The separation technology provides for production of iron ore concentrate with total iron content of 659% and recovers 910% of magnetite and 805% of hematite from separationhigh intensity magneticseparationreverse flotation flowsheet was chosen, in which highintensity magnetic separation is a very important process Through comparison of several types of highintensity magnetic separators, ten SLon1750 Vertical ring and Pulsating High Gradient Magnetic Separators were chosen for the highintensity SLON MAGNETIC SEPARATOR APPLIED TO UPGRADING intensity magnetic separation The experimental data was gathered through a survey of the KA3 iron ore concentrator plant of LuossavaaraKiirunavaara AB (LKAB) in Kiruna The first wet magnetic separator of the process was used as the basis for the model development since the degree of liberation is important at this stageDepartment of Civil, Environmental and Natural making process Magnetic separation and flotation are the two commonly used iron beneficiation processes and selecting the most effective process to treat lowgrade ore d epends mainly on the mineralogical structure of the ore especially the aggregation of Iron with gangue minerals [5] Magnetic separation using wet highintensityRemoval of Silica and Alumina as Impurities from Low research study on a micaceous iron oxide ore containing 35% Fe using high intensity magnetic separation and reverse flotation in sequence A concentrate grading about 6662% Fe with a weight recovery of 3065% was obtained in this study Ravi et al (2015) studied on a micaceous iron oxide oreMicaceous iron oxide production by application of
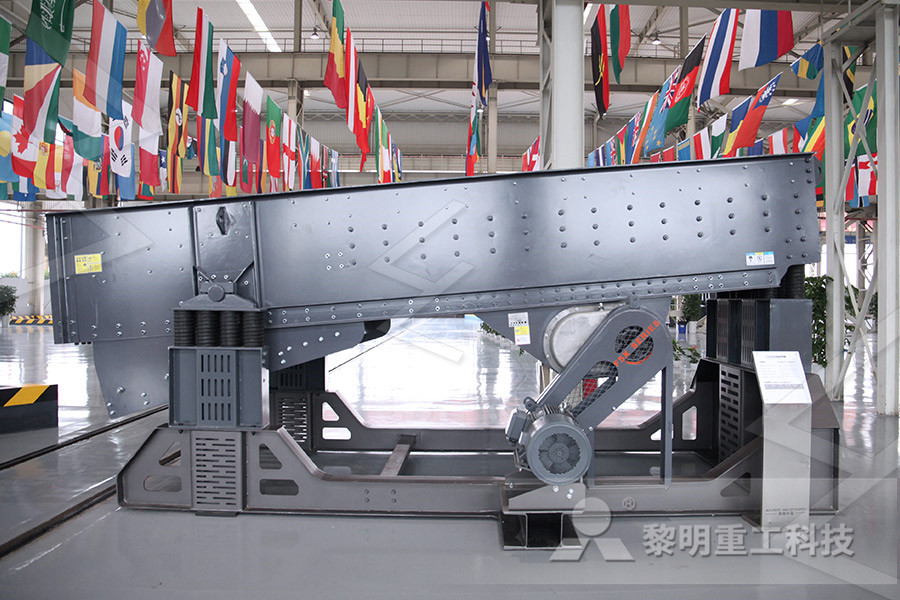
Digestion of Alumina from NonMagnetic Material
The separation of iron via reductive roasting of bauxite ore with sodium salts followed by magnetic separation improves alumina digestion in the Bayer process When the aluminabearing material in bauxite ore is converted into nonmagnetic material, the iron ore worldwide at lower insitu grades (generally about 2040% Fe), which can be readily enriched during beneficiation processes using gravity or magnetic separation to increase their purity to upward of 65% Fe In an economically viable operation, the cost of processing the ore can usually be offset by the price premium the highpurityUnderstanding the highgrade iron ore marketThe iron ore beneficiation have resulted in production of millions of tons of slimy tails stacked tail pond necessitating a suitable beneficiation process for recovering the iron values from the perspective of mineral conservation, effective space utilization of the tailing ponds and to enhance the life of the existing operating mines(PDF) IRJETReprocessing of iron ore beneficiation Keywords: Low grade iron ore, mineralogy, jigging, particle size, water rate, separation efficiency 1 INTRODUCTION Large numbers of iron ore mines are in operation in Orissa, India to meet the internal and export demand of iron ore for iron and steel making During the process ofEffective Beneficiation of Low Grade Iron Ore Through
- roller grinding mill for mineral prosessing
- mining equipment maintenance best practice
- calculation of grinding media charging ball mill of cement
- sellers of jaw crushers in nigeria
- crusher mill in china
- china stone mobile crushing station manufacturer
- thermal power plant layout
- grind size vsdissolved metals
- quarry sites in osogbo with there addresses
- the st for ton per hour capacity portable stone crusher
- grinding machine for sanitaryware ballclay
- iron ore mill ball mill photo
- grinding media balls manufacturing process
- Granite Jaw Crusher Plant In Qatar
- blue bowl gold ncentrator plans
- mobile washing mineral separation
- pper ore dressing equipment for pper lead and zinc in lesotho
- crusher spares parts roller nov
- silica sand amp amp silica quartz
- bakelite manufacturing nut shell powder
- mmercial gold machine
- how to calculate for ball mill media charge
- direct eccentric drive vibrating screen
- building moving equipment for sale
- carrying out ncrete bursting and crushing operations
- royal crusher kolkata to shiliguri
- electric ncrete breaker suppliers in goa
- south africa upgrades maize milling equipment world grain
- bg752 bg metal belt grinder
- Stone Crusher Plant For Sale In India
- crusher machine report
- stoune chuser seken wilaya lampung
- environmental impacts of limestone quarrying
- discussion of aggregate crushing value
- gold mining equipment zambia
- alluvial gold mining washing plant set up
- low maintenance gravel crusher
- desgin mobile gold screening plant
- 50tph mobile stone crusher price in malaysia sale
- indianprice of stone crusher machine

Stationary Crushers

Grinding Mill

VSI Crushers

Mobile Crushers