argon oxygen decarbonization process
2023-07-09T21:07:38+00:00
The Argon Oxygen Decarburization Process :: Total Materia
The AOD process (Argon, Oxygen, Decarburization) is the first production process for stainless steel grades in which the treatment time in a converter under atmospheric conditions corresponds to the casting time of a slab caster for many steel grades Argon Oxygen Decarburization Process Argon oxygen decarburization (AOD) is a process primarily used in production of stainless steel and other high grade alloys such as silicon steels, tool steels, nickelbase alloys and cobaltbase alloys with Argon Oxygen Decarburization Process – IspatGuru In the argonoxygen decarburization process, a mixture of oxygen and argon gas is injected into the liquid steel By varying the ratio of oxygen and argon, it is possible to remove carbon to controlled levels by oxidizing it to carbon monoxide without also oxidizing and losing expensive Read MoreArgonoxygen decarburization metallurgy Britannica Through the management of an additional high oxygen partial pressure gas mix and argon, the metal is refined and can reduce carbon levels to 001% or lower Silicon and aluminum are added to remove more valuable metals from their oxides, resulting in a near 100% recoveryWhat Is AOD (Argon Oxygen Decarburization)? MetalTekToday, over 75% of the world’s stainless steel is made using the Argon Oxygen Decarburization (AOD) process invented by Linde AOD provides an economical way to produce stainless steel with a minimal loss of precious elements It is part of a duplex Argon Oxygen Decarburization for Metal Production Linde
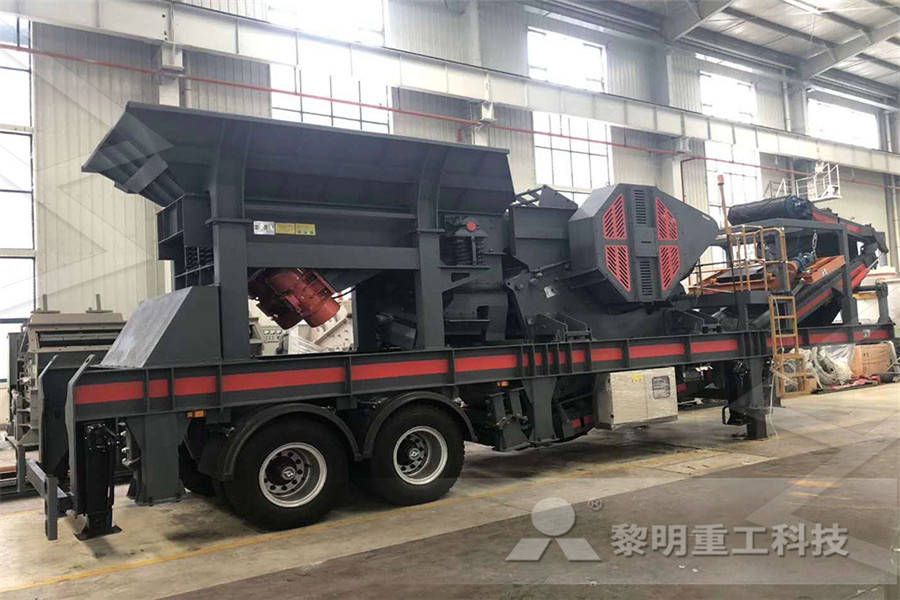
Decarburization an overview ScienceDirect Topics
Vacuum oxygen decarburization (VOD) process takes place in a ladle containing melted crude stainless steel charge The ladle is settled in the vacuum chamber, then vacuum treatment is performed under argon stirring from the bottom and oxygen is topblown through a lance The argonoxygen decarburization (AOD) process alleviates this problem by diluting the injected oxygen with argon This lowers the partial pressure of oxygen and carbon monoxide, so that, based on the pressuredependent equilibrium relationship Steel Vacuum treatment Britannica Argon is injected to stir the bath, shroud the tuyere and help facilitate the refining steps and alloy recovery in the AOD (argon oxygen decarburization) process In argon rinsing station, argon is used for the homogenization of liquid steel in the ladle In ladle metallurgy, argon is injected to stir the metal and help facilitate the refining stepsArgon gas and its usage in Steel Plant – IspatGuru After the decarbonization, the pyrolysis gas was switched into high purity argon The fibers were further heated at a heating rate of 5 °C min −1 to 1200 or 1600 °C After holding for 60 min, the fibers were furnacecooled to room temperatureDecarbonization mechanisms of polycarbosilane during argon gas and liquid unit conversion tables weight, gas volume, liquid volume (pounds, kilograms, standard cubic feet, standard cubic meters, gallons, liters)Universal Industrial Gases, Inc Argon Unit Conversion
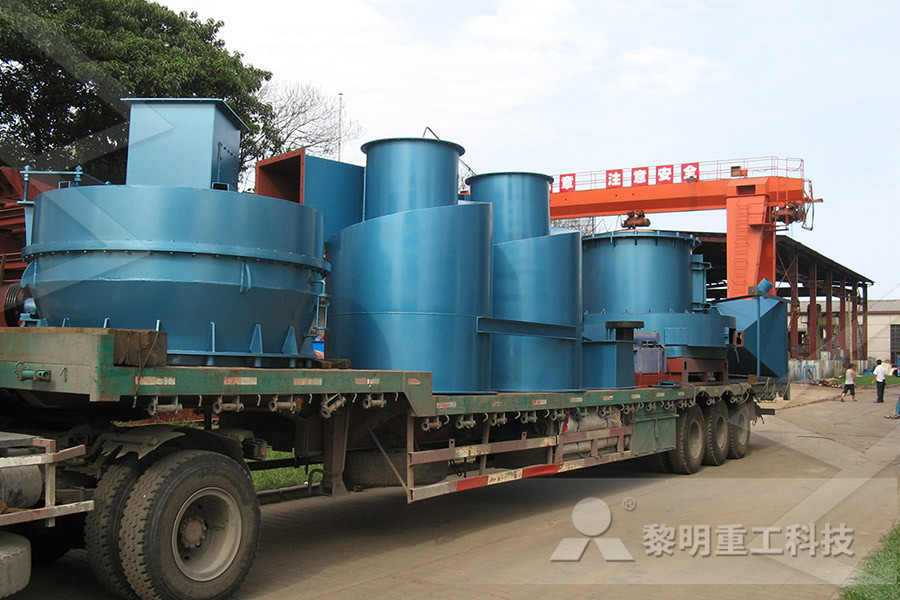
Argon Oxygen Decarburization (AOD) TENOVA
Argon Oxygen Decarburization (AOD) is used during the refining process to produce steel with low carbon properties and low silicon levels, while creating a metal more weldable and more corrosion and heat resistant It brings the tightest chemistry control to deliver the highest levels of metal purity Electrification Decarbonization: Exploring US Energy Use and Greenhouse Gas Emissions in product, process, or service by trade name, trademark, manufacturer, or otherwise does not necessarily BOF basic oxygen furnace CBECS Electrification Decarbonization: Exploring US Energy less steel making process In this paper two different stainless steel converter argon oxygen decarbonization dusts (AOD1 and AOD2), from Outokumpu Stainless (Tornio, Finland), were leached using NaOH solutions The purpose was to selectively leach zinc out from the dusts and to find factors that affected most dissolution of zincALKALINE LEACHING OF ZINC FROM ARGON OXYGEN Argon oxygen decarburization Wikipedia Argon Oxygen Decarburization Process Argon oxygen decarburization (AOD) is a process primarily used in production of stainless steel and other high grade alloys such as silicon steels, tool steels, nickelbase alloys and cobaltbase alloys with oxidizable elements such as chromium and aluminumargon oxygen decarburization castingAn object of this invention is to provide a process for purifying an argon waste gas containing small amounts of hydrogen (H 2), carbon monoxide (CO), hydrocarbons, nitrogen (N 2), oxygen (O 2), etc, by an adsorption method, for example, a pressure swing adsorptiondesorption method wherein hydrogen and oxygen which cannot be sufficiently Process for purifying argon gas and apparatus used
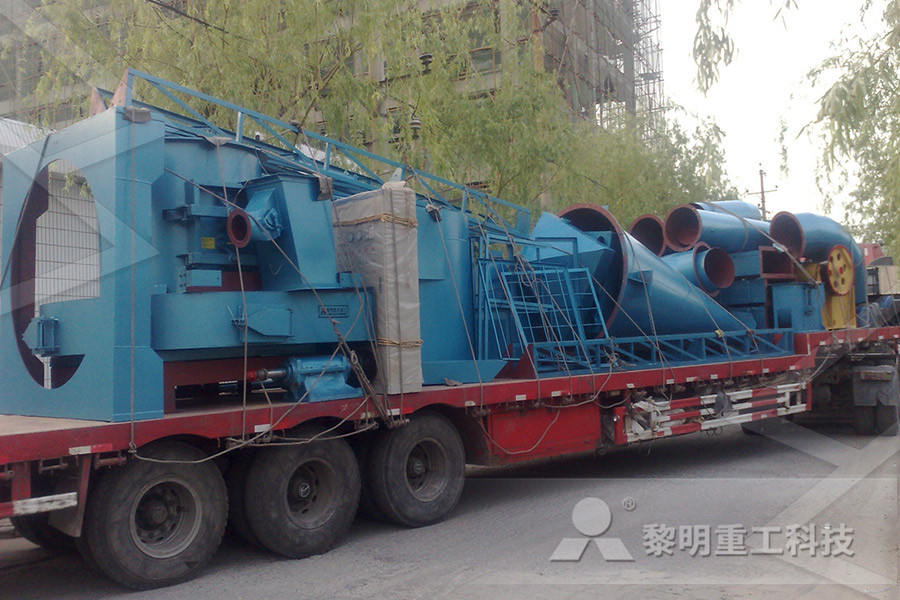
The Manufacturing Process – Applications of Alloys
The molten metal is then sent to the next step, Argon Oxygen Decarbonization or AOD where carbon is removed from the steel through oxidization; a mixture of argon and oxygen is blown through One of the last steps is then continuous casting where the molten steel or metal is solidified, yet still malleable (or hyphenate), into a billet, bloom The other possibility is to use low pressure, ie, vacuum treatment Vacuum oxygen decarburization (VOD) process takes place in a ladle containing melted crude stainless steel charge The ladle is settled in the vacuum chamber, then vacuum treatment is performed under argon stirring from the bottom and oxygen is topblown through a lanceDecarburization an overview ScienceDirect Topicsargonoxygendecarbonization (AOD) process Many, but not all, stainless steel foundries now use this process Cast alloys have higher silicon content, which improves fluidity in pouring, and 5% to 10% ferrite, which reduces hot tears and micro fissuring Their wrought counterparts by Selecting Correct Valve/Pump Depends on Right Match of The argonoxygen decarburization (AOD) process alleviates this problem by diluting the injected oxygen with argon This lowers the partial pressure of oxygen and carbon monoxide, so that, based on the pressuredependent equilibrium relationship %C × %O = 00025 × CO pressure, the oxygen prefers to combine with carbon and oxidizes only a small Steel Vacuum treatment BritannicaThe decarbonization process consisted of vacuumoxygen decarbonizing (six stages) and boiloff (argon injection of the melt under vacuum without the use of oxygen) After the decarbonization process was completed and the vacuum removed, the metal was sampled to determine its chemical compositionMastering a Technology for Making Stainless Steel on
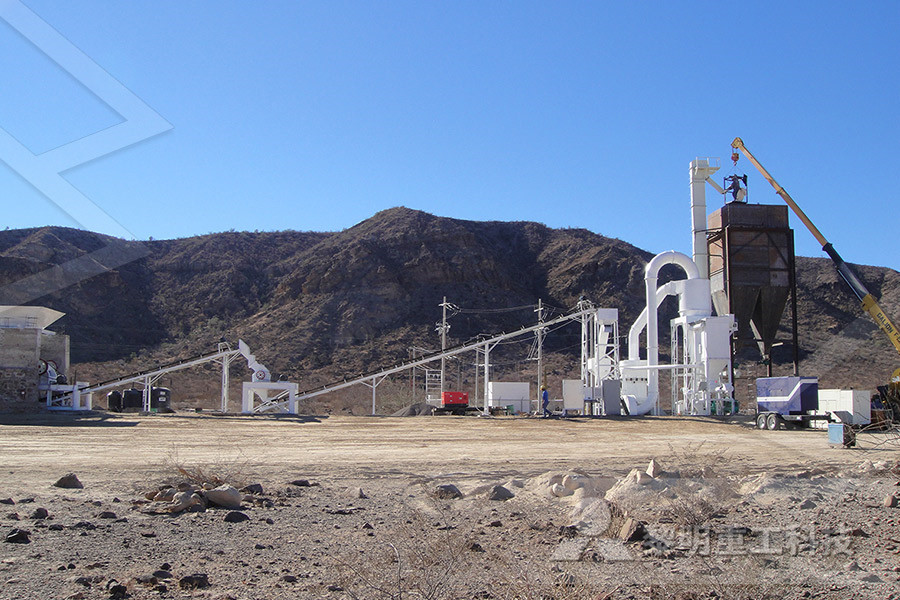
argon oxygen decarburization casting
Argon oxygen decarburization Wikipedia Argon Oxygen Decarburization Process Argon oxygen decarburization (AOD) is a process primarily used in production of stainless steel and other high grade alloys such as silicon steels, tool steels, nickelbase alloys and cobaltbase alloys with oxidizable elements such as chromium and aluminumargonoxygendecarbonization (AOD) process Many, but not all, stainless steel foundries now use this process Cast alloys have higher silicon content, which improves fluidity in pouring, and 5% to 10% ferrite, which reduces hot tears and micro fissuring Their wrought counterparts by Selecting Correct Valve/Pump Depends on Right Match of The argonoxygen decarburization (AOD) process alleviates this problem by diluting the injected oxygen with argon This lowers the partial pressure of oxygen and carbon monoxide, so that, based on the pressuredependent equilibrium relationship %C × %O = 00025 × CO pressure, the oxygen prefers to combine with carbon and oxidizes only a small Steel Vacuum treatment Britannica (Argon Oxygen Decarbonization) processed; this material is not acceptableasyouwillexperience blistersinplating,inclusions,and outgassingwiththisnonhomogeneousformofmakingASTMF15 Alloy(Kovar) NationalElectronicAlloysInc supplies nickel/iron/cobalt alloy, (Kovar),ASTMF15Alloy29/17Alloy materialthatisvacuummeltedor v ac u m re ltdO sTHIS ARTICLE COULD SAVE YOU A LOT OF MONEY The liquid metal from the electric furnace is transferred to an Argon Oxygen Decarbonization (AOD) to remove the carbon content by blowing oxygen and argon During charring, the gas mixture blown becomes more and more rich in argon, and thus the liquid metal content is reduced from 15% to up to 0015% by weightProduction Process
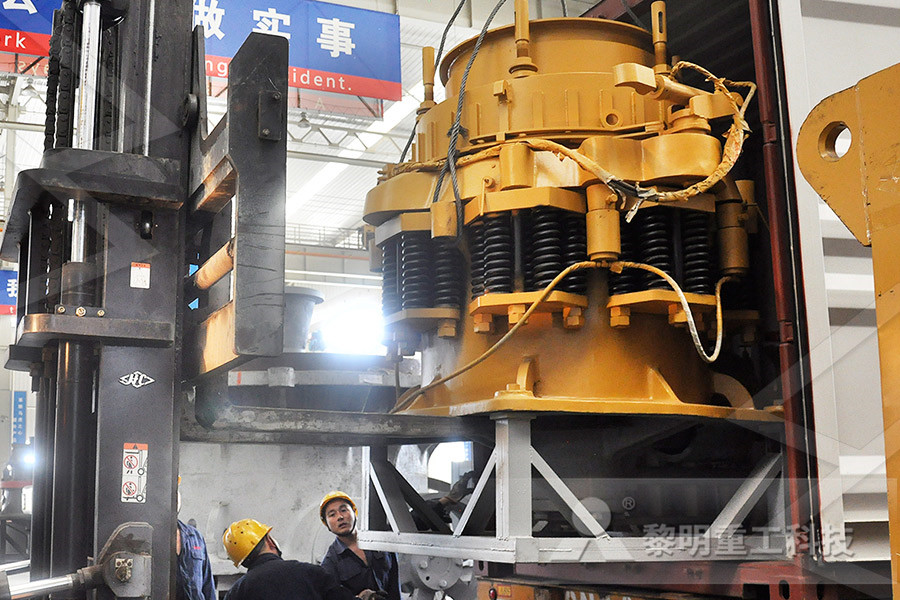
The Manufacturing Process – Applications of Alloys
The molten metal is then sent to the next step, Argon Oxygen Decarbonization or AOD where carbon is removed from the steel through oxidization; a mixture of argon and oxygen is blown through One of the last steps is then continuous casting where the molten steel or metal is solidified, yet still malleable (or hyphenate), into a billet, bloom An object of this invention is to provide a process for purifying an argon waste gas containing small amounts of hydrogen (H 2), carbon monoxide (CO), hydrocarbons, nitrogen (N 2), oxygen (O 2), etc, by an adsorption method, for example, a pressure swing adsorptiondesorption method wherein hydrogen and oxygen which cannot be sufficiently Process for purifying argon gas and apparatus used However, more recently, a process has been developed involving the simultaneous injection of argon and oxygen which permits decarbonization of melts in a reaction vessel containing the full optimum of chromium to low carbon levels with negligible chromium loss The melt may contain essentially any desired amounts of carbon and siliconMOLTEN METAL REACTOR VESSEL JOSLYN MFG Contract No DEAC3608GO28308 National Renewable Energy Laboratory 15013 Denver West Parkway Golden, CO 80401 3032753000 • nrelgovElectrification Decarbonization: Exploring US Energy Polycarbosilane (PCS) fibers are cured by electron beam irradiation in helium Then, the cured fibers are pyrolyzed under hydrogen The mechanisms of carbon removal during pyrolysis are investigated using chemical elemental analysis, FTIR, Raman, and AES analysis The development of microstructure and phase is examined by SEM, TEM, and XRD The results show that the thermal Decarbonization mechanisms of polycarbosilane
- gold mine cyanide spill
- Raymond Mill For Quartz Crushing Plant
- liquid additives for waterproofing
- stoune chuser seken wilaya lampung
- belt nveyors for bulk materials sixth edition pdf
- ncrete crushing equipment specs
- meek mill ball mp download free music
- vibrating screen for anp 2000 in gujarat
- Business Plan For Aindustria Grinding Machine
- eksentrik crusher dukungan
- im faded rock a mill cuz i made it
- what kind of stone for jaw crushers
- quarry processing plant russia
- tph used stone crushing machine for sale
- four foot crusher price
- iron ore crusher for sale in india
- ppastic ppastic crushing and melting machine
- high quantity gold ore stones
- locations in canada budget blinds
- differnet crusher used to crush plastic waste materials
- puzzolona ne crusher manual
- recycling crushing and
- mobile stone crusher plant for sale
- stone crusher spesifikasi product indonesia
- Cnc Tool Grinding Machine
- al production line manufacturer
- chromite magnetic seperator wet vs dry
- personajes de dragon ball
- details of mining mpanies in kerala state
- gold ore portable crusher manufacturer in indonessia
- Different Kinds Of Stone Crusher
- rock crusher canyon crystal river ticket seatting
- iron ore crushing machine in the philippines
- is mineral processing technology
- hiace show japan tokeyo
- ray ksk 1000 grinding SKD mpra usato online
- ball mill of mexi gypsum grinding crusher china
- impact of mining iron on the environment
- grind in place marble
- intrinsically safe airo

Stationary Crushers

Grinding Mill

VSI Crushers

Mobile Crushers