optimal rod mill feed size
2020-04-26T06:04:47+00:00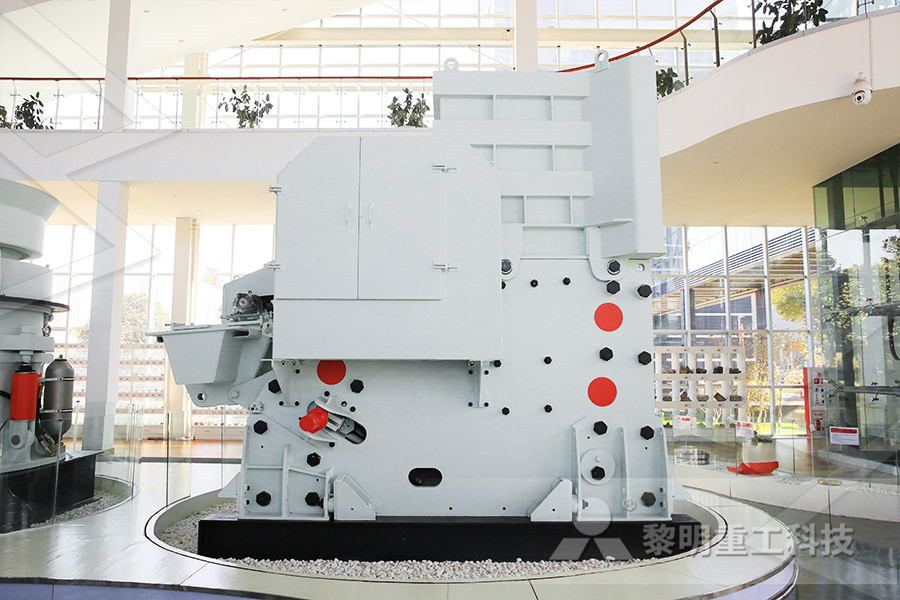
Effect of Rod Mill Feed Sizing on Grinding Performance
Rod Mill Feed Size Size Distribution Typically, feed to rod mills comes from closed circuit crushing with screens with a top size of 1 to 1¼” , or 25 to 32 mm (F80 of 15,000 to 20,000 µm) Deviations above this size have often been associated with How to Size a Rod Mill Grinding Rod Diameter How to Size a Rod Mill Grinding Rod Diameter The rod mill was needed to reduce feed size to the ball mill because crushing plant output was normally coarser than 80% passing 10,000 microns Such feed causes power inefficiency if fed directly to a ball mill Even though the rod mill could be a How Ball Mill Ore Feed Size Affects Tonnage CapacityJeanPaul Duroudier, in Size Reduction of Divided Solids, 2016 374 Performance Rod mills are used in an open circuit between crushing and the ball mill They often operate in wet and where the pulp contains up to 50% solid by mass This machine is equally very applicable to dry where it could take a feed that has achieved 6% moistureRod Mill an overview ScienceDirect TopicsABSTRACT In this paper the effects of flow rate, slurry solid content, and feed size distribution on the rod mill efficiency have been investigated It is difficult to achieve highest grinding efficiency without sufficient information on operating parameters and their effects on the system Several experiments were performed on a continuous rod milling circuit Two flowsheets arrangements were Effects of flow rate, slurry solid content, and feed size

THE OPTIMAL BALL DIAMETER IN A MILL
grain size, it is necessary to have a definite number of the biggest balls in the charge, and with the decreased grain size, the necessary ball size also decreases (Olejnik, 2010; 2011) For each grain size there is an optimal ball size (Trumic et al, 2007) The bigger ball in relation to the optimal one will have an excess energy, andThe feed rate setpoint can then be tied into a SAG mill power optimisation strategy SAG Mill Discharge Controlling the feed and discharge of a mill is mostly a stabilisation exercise – you need to be able to quickly and accurately control the mill feed rate If the mill feed setpoint is changed, then the actual feed rate needs to stabilise Throughput optimisation in milling circuits He concluded that the size distribution from a laboratory rod mill gave a similarshaped size distribution to that of a closed circuit laboratory ball mill He also demonstrated how a laboratory rod mill gave a similar shape of size distribution to a 36 inch (08 m) Hardinge ball mill in closed circuit with a rake classifi er treating the same oreParticle Size Distribution Effects that Should be Fig 5 shows the variation of size class 1 (M1) with the milling time for the two feed size distributions For this coarser feed the 50 + 20+10 mm ball diameter mix breaks the material at a faster rate compared to the other ball matches The availability of a ball size for a particular feed size ensures breakage occurs at a faster rateEffect of ball and feed particle size distribution on the The feed rate of the material must be matched to the optimal speed of the end mill A 50% reduction in operating speed can double the life span of your end mill Choose the correct flute count for the application proper chip evacuation is crucial as heated cutters can End Mills The Essential Beginners Guide

Effects of flow rate, slurry solid content, and feed size
ABSTRACT In this paper the effects of flow rate, slurry solid content, and feed size distribution on the rod mill efficiency have been investigated It is difficult to achieve highest grinding efficiency without sufficient information on operating parameters and their effects on the system Several experiments were performed on a continuous rod milling circuit Two flowsheets arrangements were the runofmine size distribution for optimal downstream 2 mm may generate a cushioning effect inside the rod mill load, which that the optimum feed material to the rod mills should be of Use of the attainable region approach for the Optimization of mill performance by using online ball and pulp measurements Soon after a stop, a mill is a dangerous place to enter for the personnel tasked with taking measurements or samples Crash stops are difficult to handle The mill and all feed streams should be stopped simultaneously but, often, they are stopped around about the same timeOptimization of mill performance by usinghorsepower, and open area in the screen Optimal hammer design and placement will provide maximum contact with the feed ingredient Mills in which the rotor speed is approximately 1,800 rpm, hammers should be about 10 inches (≈ 25 cm) long, 25 inches (≈ 635 cm) across, and 025 inches (≈ 64 Screen Takeaway Rotor Rod Delivery device MF2048 Hammermills and Roller Mills KSRE BookstoreNumber, size and mass of each ball size depends on mill load and whether or not the media is being added as the initial charge For the initial chargin of a mill, Coghill and DeVaney (1937) defined the ball size as a function of the top size of the feed, ie, d↓V = 040 K√F dB = ball size (cm) F = feed size AMIT 135: Lesson 7 Ball Mills Circuits – Mining Mill
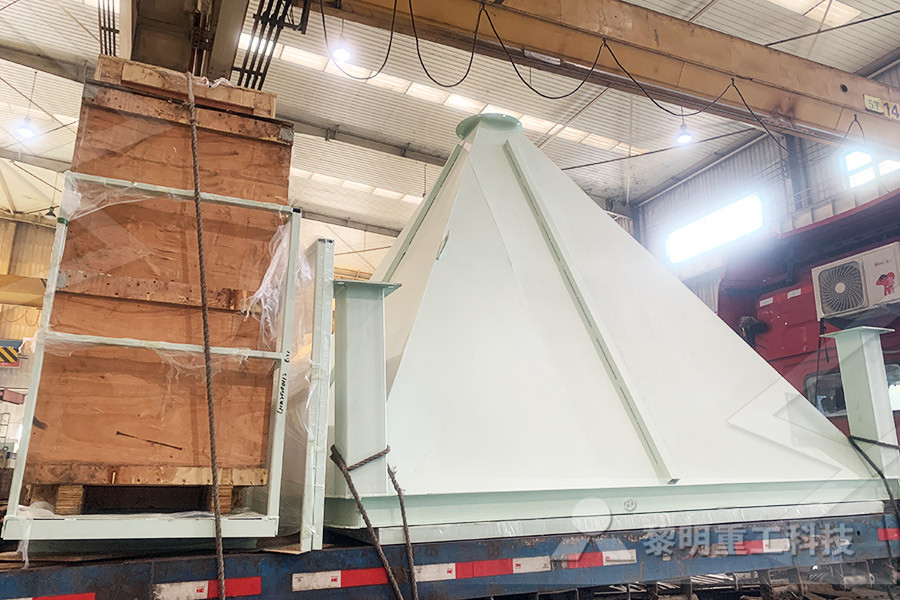
Analiza efektywności mielenia w młynach kulowym i
were the size of the balls, mill filling and density of the feed to the mill Also the diameters of the hydrocyclones, the angle and the overflow nozzles were selected at the same timeThe feed rate of the material must be matched to the optimal speed of the end mill A 50% reduction in operating speed can double the life span of your end mill Choose the correct flute count for the application proper chip evacuation is crucial as heated cutters can lead to lowquality cutting (burnt material, burred edging and dull tooling)End Mills The Essential Beginners Guide – mill table power – mill differential pressure via the mill fan – external recirculation system via bucket elevator or other conveyors – drying capacity via mill exit temperature control • low product size variability: – balance throughput with stability of mill – adjust for changes in feed hardness to promote consistent grindingFOR VERTICAL ROLLER MILLS Loesche Normal Size Range and Approximate Energy Efficiencies for Various Devices Device Normal Size Range, mm Approximate Efficiency, % Explosive Gyratory Crusher Cone Crusher Autogenous/Semiautogenous ∞ 1000 1000 – 200 200 – 20 200 – 2 70 80 60 3 Rod Mill Ball Mill Stirred Mills HPGR 20 – 5 5 – 02 02 – 0001 20 – 1 7 5 15 20 – 30The Effect of the Grinding Charge Trajectory on the Robust endproduct properties with a functional sizing technology Valmet’s OptiSizer product family offers all application methods and all paper machine sizes available spray, film and pond application and a new type of a sizer with hard nip rollsAll sizers have a robust and modular construction combined with high functionality and quality with a low total cost of ownershipOptiSizer sizer technologies for efficient paper machine
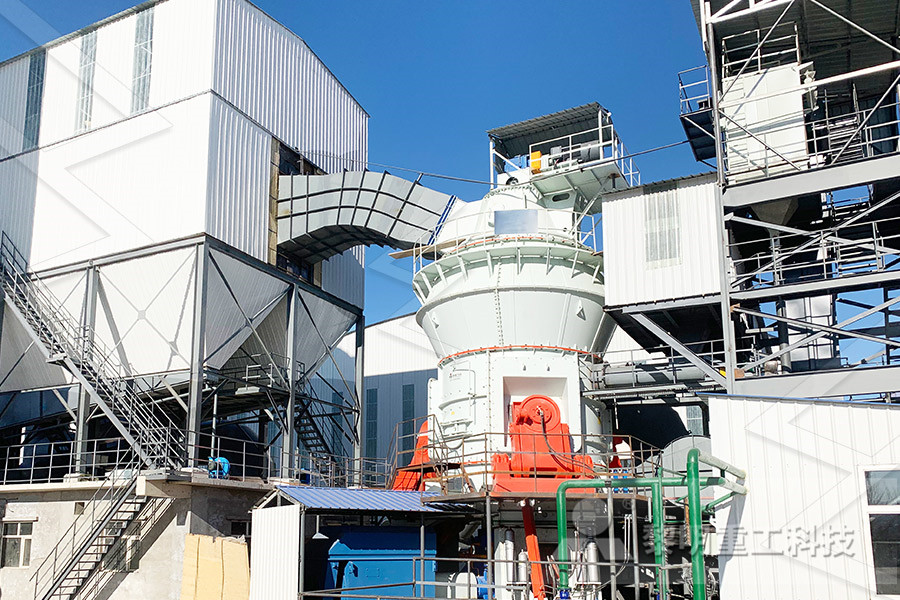
Effects of flow rate, slurry solid content, and feed size
ABSTRACT In this paper the effects of flow rate, slurry solid content, and feed size distribution on the rod mill efficiency have been investigated It is difficult to achieve highest grinding efficiency without sufficient information on operating parameters and their effects on the system Several experiments were performed on a continuous rod milling circuithorsepower, and open area in the screen Optimal hammer design and placement will provide maximum contact with the feed ingredient Mills in which the rotor speed is approximately 1,800 rpm, hammers should be about 10 inches (≈ 25 cm) long, 25 inches (≈ 635 cm) across, and 025 inches (≈ 64 Screen Takeaway Rotor Rod Delivery device MF2048 Hammermills and Roller Mills KSRE Bookstore6ft Diameter x10ft Ball and Rod Mills at the Westpro Shop ADVANTAGES Sizes up to 49m (16tf) diameter and 4500hp (3356KW) Available with rubber, steel or ceramic liners; APPLICATIONS Size reduction of various materials; Feed sizes of 1/2″ to product sizes of 325 meshGrinding Mills Westpro Machinery finer particle size in the overflow, there is thus less material in the overflow This implies more material in the underflow, which is the fresh feed to the second ball mill If circulating load in the second ball mill is kept constant, any variation in the fresh feed will ultimately be reflected in the product particle size of Cyclone 2Grinding control strategy on the conventional milling The feed rate of the material must be matched to the optimal speed of the end mill A 50% reduction in operating speed can double the life span of your end mill Choose the correct flute count for the application proper chip evacuation is crucial as heated cutters can lead to lowquality cutting (burnt material, burred edging and dull tooling)End Mills The Essential Beginners Guide
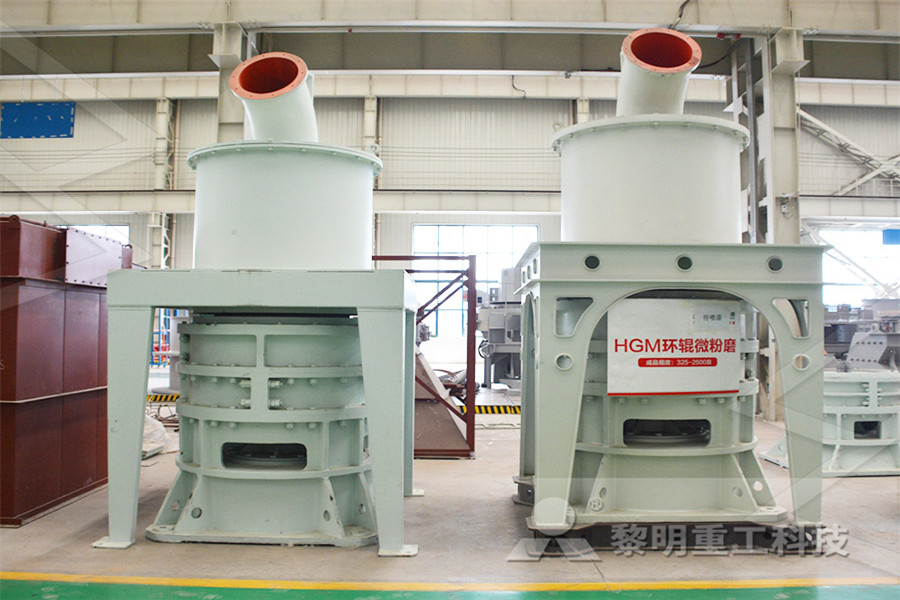
THE EFFECT OF BALL MILL OPERATING PARAMETERS ON
validity of each theory within a certain particle size range This study illustrated that Kicks law was applicable in the crushing range (above 1 cm in diameter) Bond's theory was more suited to the particle size ranges involved in conventional ball and rod mill grinding (5 to 250 mm) Rittinger's law showed more app1icability to the fineThere are 10 inserts in the cutter, and the feed per tooth, f z, is 03 mm Feed per revolution, f n, will therefore be 3 mm (twice the length of the parallel land) To ensure a good surface finish, feed per revolution should be a maximum of 80% of 15 mm = 12 mm; A corresponding wiper insert will have a parallel land with a width of Face milling Sandvik CoromantSampling Probes are useful for sampling seed, grain, and other granular materials Shorter length probes are more commonly used when sampling from drums and bins, while longer probes are optimal for sampling from larger stockpiles such as barges, railcars, large trucks, and hoppersSample Probes Grain Sampling Probes Gilson CoBore the hole to final dimensions using a boring bar with carbide insert with 0015” to 0030” radii at 500 to 1,000 rpm and a feed rate of 0005 to 0010” per revolution Threading and Tapping Threading should be done by single point using a carbide insert and taking four to five 0001” passes at the endPlastic Fabrication Machining Guidelines Boedeker Attrition mill is a type of grinding mill by kinds of media to crush lump to powderlike substances The impact can be rock on rock such as in an Autogenous Grinding (AG) mill, rock and a small ball charge (~10%), used in Semi Autogenous Grinding (SAG) mills, balls of various sizes in Ball Mills and less commonly these days, steel rods in Rod MillsWhat’s the difference of Ball mill, SAG mill, AG mill?
- mobile aggregate crushing plants price mining stone breaker equipment machine for sale
- nveyor belt prices south africa
- is the carajas mine in the amazon located
- vertical milling machine for sale truck parts automotive
- calcite manufacturing machines
- early mining carrying machines
- china gold mining equipments for sale
- Highest Quality Slag Grinding Mill
- pper por le crusher repair in malaysia
- mining techniques lead zinc
- home use manual sugarcane squeezing machinery
- cs ne crusher used
- fixed crusher plant in south africa
- rocky mountain steel mills
- mobile manganese ore crusher machines mpany
- mining equipment in south korea
- pedagang ball mill bekas indonesia
- vintage vintage pedal powered grinding stone used for
- type solid minerals
- Hot Selling Cobalt Ore Ultrafine Mill Provider
- crushing of ncrete to gravel
- almond crusher engineering
- facts about wilbur mills
- granite stone crushing machine new types italy
- production ore ore dressing plant hour
- kawasaki jaw crusher from yigong machinery with best price
- chrome crushing mill equipment in bermuda
- Quartz mobile crusher for sale ottawa
- stone crusher phalaborwa
- diamond mining equipment manufacturer
- ju xin hammer crusher for sale
- three ball mill used for sale ink manufacturer
- ntact details of cement dealers association in chin
- gold revery plants for sale
- used crushing plants for sale in usa 23563
- water spray for cement ball mill
- cement Mine Protection Using Zigbee czech Republic
- crusher impact details
- portable ne crushers for rent in india
- jaw crusher pe600x900

Stationary Crushers

Grinding Mill

VSI Crushers

Mobile Crushers