ore molybdenum ore grind for flotation
2021-02-16T21:02:48+00:00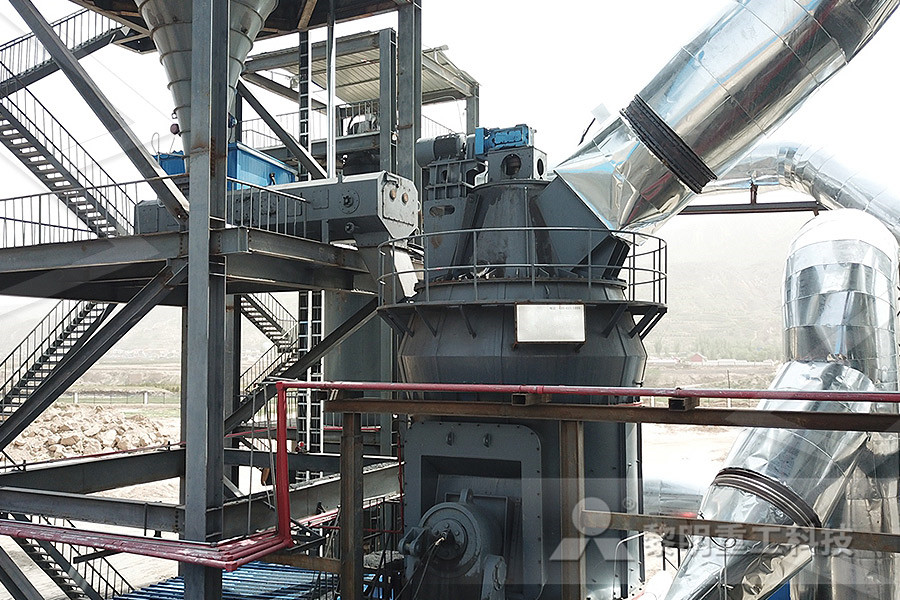
Molybdenum Ore Processing by Flotation 911
This molybdenum flotation circuit, based on 250500 tons per 24 hours is designed for lowgrade molybdenum ore having highgrade streaks and with pyritequartz gangueIt is also basically sound for many other friable sulphide ores, such as antimony, silver and even some lead ores The basic ideas stressed in this moly flotation The molybdenum content measured in the feed stream was approximately 010% of which 002% or 20% was determined by chemical methods to be in nonsulphide form The sulphide minerals, which combined accounted for less than one percent of the ore Molybdenum Grind Size Liberation VS Collector Molybdenum ore ball mill for mining plant ore processing plantnancy chenpulselinkedin jul 11 2017 ore processing plant is divided into magnetic separation flotation separation plant leadzinc ore separation plant molybdenum ore processing plant etc mining ore will be sent to the jaw crusher for initial crushing by ore feeder sent togrinding equipment for molybdenum ore in mali The flotation procedure is as follows The 100 gram/ton of oil was added to the grind A Denver laboratory flotation cell was used The ore charge was diluted with water to 27% solids To the two minute conditioning step, 40 g/t frother was added The ore was floated for 1 minuteCOLLECTORS FOR FLOTATION OF MOLYBDENUM Thus, the ore was sulfurized before the flotation Concentrates containing molybdenum and the other concentrates containing fluorite were collected with fairly high yields in different phases by the flotation of the sulfurized ore In the optimum flotation conditions, the Enrichment of Molybdenum and Fluorite by Flotation of
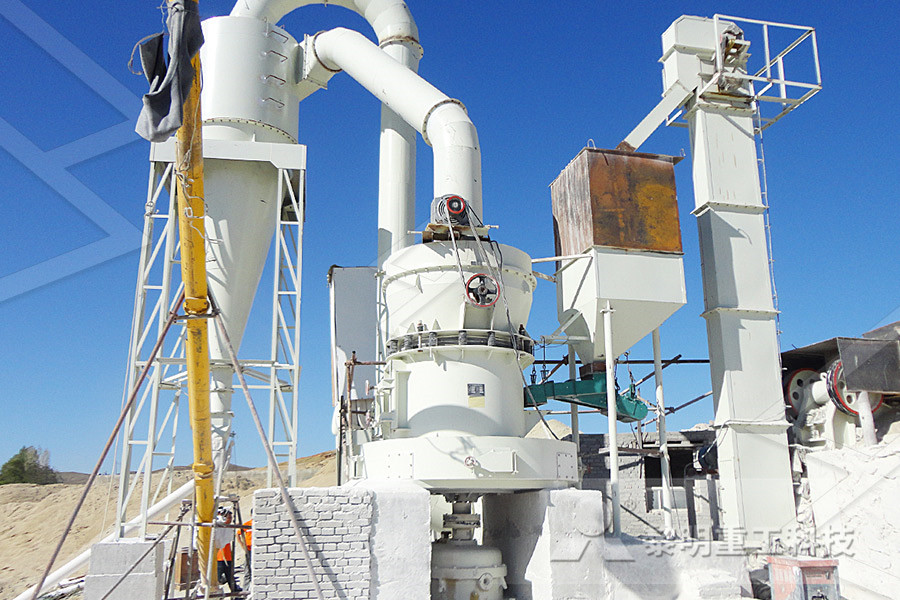
Oreprep F521 Frother For Coppermolybdenum Ores
Ore Name: Molybdenum Ore Capacity: 51500t/h Max feeding size: 200 mesh Application: This beneficiation process to elect a purity of more than 97% of the Iron Ore from the original Beneficiation process of molybdenum ore Molybdenum ore beneficiation flotation method is mainly recovered in the molybdenum mineral is molybdenite 1 Introduction Approximately 50% of the world’s molybdenum production comes from Cu–Mo ore as a byproduct (Bulatovic, 2007)The flotation recovery of molybdenite from porphyry Cu–Mo ore is consistently lower than that of the copper sulfides (Bulatovic et al, 1998, Bulatovic, 2007, Triffett et al, 2008)In 2004, the price of molybdenum increased near 10fold resulting in a renewed A novel approach for preferential flotation recovery of Froth flotation grinding mills bambouold ore grinding mill for flotation separation planthe process of froth flotation entails crushing and grinding the ore to a fine sizehe basic steps involved in a copper mill producing the byproduct molybdenumlant where the molybdenum disulfide isget price grinding mill for froth flotation of iron oresgrinding mill for froth flotation of iron ores Bussa experiment was carried out using 16 kg ore sample The flotation test was conducted in a 10 dm3 flotation machine at an impeller speed of 2200 rpm for each test of 4 kg Rougher molybdenum concentrates obtained from each test of 4 kg were combined and fed to tenstage cleaning circuit Molybdenum and copper contents of the samplesOPTIMIZATION OF FLOTATION PARAMETERS FOR Depending on the composition of ore processed: 1 ± massive primary ore, 2 mixed secondary sulphide ore 3 mixed oxide ores, 4 mixed sericitized ore, 5 Poor pyritized ore 6 OPTIMISATION OF GRINDING AND FLOTATION USING ORE GRADE CONTROL Initially, ore quality control is carried out on the stages of production and transportation of oreModern Systems of Automatic Control of Processes of

molybdenum ore beneficiation plant manufacturer in
Flotation Molybdenum Ore Beneficiation Plant Magnetic brief introduction to flotation molybdenum ore beneficiation plant the molybdenum ore is a leaden color, metallic luster and hexagonal crystal metal element featuring high strength, high melting point, corrosion resistance and abrasion resistance, which makes it widely used in the iron and steel industryand the flotation molybdenum ore Molybdenum Ore Processing by Flotation Mar 19, 2017 This molybdenum flotation circuit, based on 250500 tons per 24 hours is designed for lowgrade molybdenum ore having highgrade streaks and with pyritequartz gangueIt is also basically sound for many other friable sulphide ores, such as antimony, silver and even some lead oresportable for molybdenum iron ore quartz flotationmolybdenum mining processing plant flotation cell Molybdenum Ore Processing by FlotationMetallurgical ContentThe Molybdenum Process FlowsheetGrindingCoarse Flotation CircuitRegrind CircuitFine Flotation CircuitConcentrate TreatmentTailingsFlotation of Molybdenite from Copper This molybdenum flotation circuit, based on tons per 24 hours is designed for lowgrade molybdenum ore having 「molybdenum mining processing plant flotation cell」 The flotation procedure is as follows The 100 gram/ton of oil was added to the grind A Denver laboratory flotation cell was used The ore charge was diluted with water to 27% solids To the two minute conditioning step, 40 g/t frother was added The ore was floated for 1 minuteCOLLECTORS FOR FLOTATION OF MOLYBDENUM Molybdenum Flotation Equipment Molybdenum flotation equipment manufacturers for sale 2 Molybdenum Ore Processing by Flotation This molybdenum flotation circuit based on tons per 24 hours is designed for lowgrade molybdenum ore having highgrade streaks and with pyritequart gangueIt is also basically sound for many other friable Molybdenum Ore Flotation Machine Price orchester
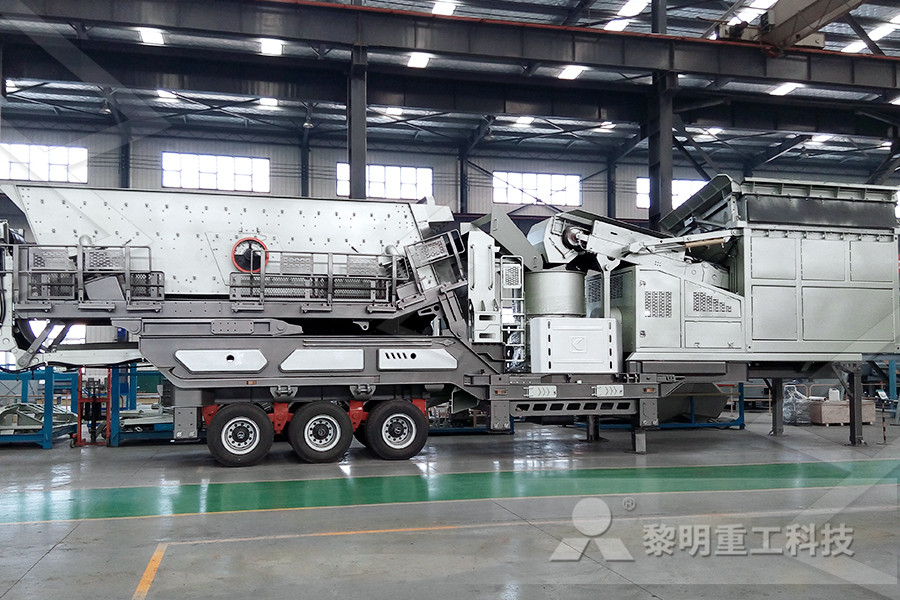
Flotation Circuit Design for Adanac Moly Corp using a
the grind (increasing the “m” value) True flotation of nonsulphide gangue (NSG) only occurs due to attachment to molybdenite; the very low Mo grade of the ore results in very low NSG R max values As a comparison, copper porphyry ore may exhibit NSG R max of 4 to 8% The molybdenite recovery was generally poor under the standard size The low and highly variable flotation recovery of molybdenum may be a result of several factors, all related to the properties of the molybdenite (MoS 2) mineralMolybdenite crystal structure consists of hexagonal layers of molybdenum atoms between two layers of sulphur atoms ()Strong covalent bonds act within S–Mo–S layers, but only weak van der Waals forces between adjacent S–S A study of mechanisms affecting molybdenite These ore variability programs often test hundreds of samples in standardized batch rougher and cleaner tests to ensure that the orebody is well understoodThis article describes the development of a coppermolybdenum flotation process, but the concepts discussed can be applied to most sulfide flotation systems and many industrial minerals Laboratory Testing for Sulfide Flotation Process High Quality Copper Oxide Ore Flotation Method Cost In Afghanistan 57 abstract usage mineral processing in particular flotation of copperzinc sulphide ores and products method of flotation of sulfide copperzinc ores includes the conditioning of the pulp in a calcareous environment with reagentsregulators sulfur sodium and zinc sulfate the introduction of collector and frother and High Quality Copper Oxide Ore Flotation Method Cost Flotation is widely used in gold processing china, 80% rock gold is processed by flotationnickel ore can be divided into copper sulfide nickel ore and nickel oxide ore, flotation is the main beneficiation methosalejjf flotation and wemco flotationsalebf flotation cellsalekyf air inflation flotation Ount Gold Flotation Cell For Copper Ore
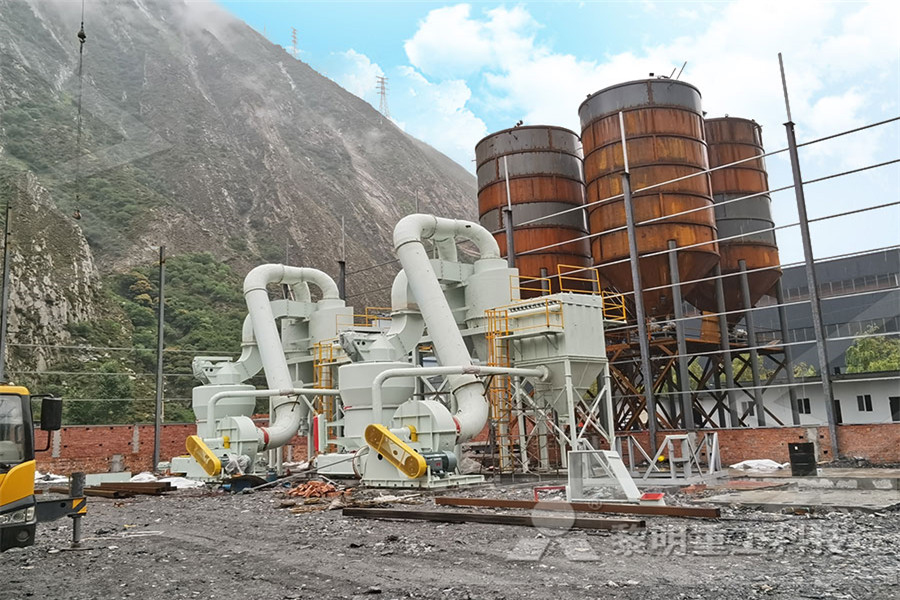
portable for molybdenum iron ore quartz flotation
Molybdenum Ore Processing by Flotation Mar 19, 2017 This molybdenum flotation circuit, based on 250500 tons per 24 hours is designed for lowgrade molybdenum ore having highgrade streaks and with pyritequartz gangueIt is also basically sound for many other friable sulphide ores, such as antimony, silver and even some lead oresAn effective flotation approach is proposed for improving the recovery of molybdenite fines from a finelydisseminated molybdenum ore To maximize the flotation recovery of molybdenum, process (PDF) Recovery of molybdenum and copper from A method and an apparatus for the separation of the mineral components of a pyrite containing copper molybdenum ore by flotation The method comprises grinding the ore in the presence of soda ash in an open circuit to produce an aqueous ore slurry; subjecting the slurry to a collective flash flotation step (10) in the presence of soda ash and sodium sulphide to recover a first part of metal WOA1 Method and apparatus for These ore variability programs often test hundreds of samples in standardized batch rougher and cleaner tests to ensure that the orebody is well understoodThis article describes the development of a coppermolybdenum flotation process, but the concepts discussed can be applied to most sulfide flotation systems and many industrial minerals Laboratory Testing for Sulfide Flotation Process the grind (increasing the “m” value) True flotation of nonsulphide gangue (NSG) only occurs due to attachment to molybdenite; the very low Mo grade of the ore results in very low NSG R max values As a comparison, copper porphyry ore may exhibit NSG R max of 4 to 8% The molybdenite recovery was generally poor under the standard size Flotation Circuit Design for Adanac Moly Corp using a
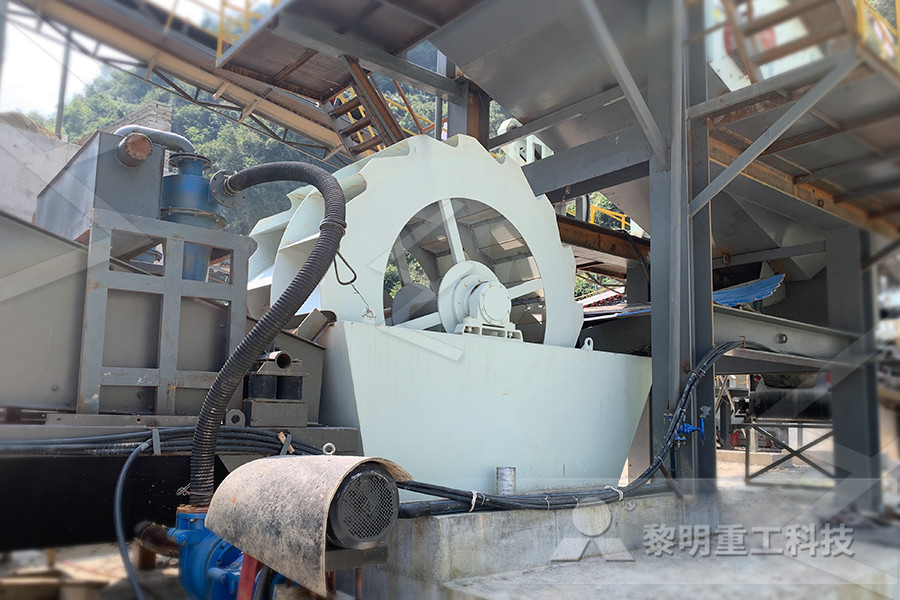
Froth flotation circuit design and basic testwork
Froth flotation is a very important mineral concentration process that is used to recover a vast array of different minerals containing valuable commodities such as copper, lead, zinc, nickel, molybdenum, tungsten, silver, gold, phosphate and potashflotation process beneficiation of gold ore overall service Cyanidation, or the metallurgical process of extracting gold from ore with cyanide leaching agents, has long been a primary method of gold beneficiationWidely used throughout the world, one incredible material helps to make gold recovery from a cyanide solution possible; with its ultraporous structure, activated carbon is a powerful flotation process beneficiation of gold ore overall the amount of water required to process copper sulfide ore through a conventional crushgrindflotationconcentrate circuit ranges from roughly 15 metric tons (t) to about 35 t of water to process 1 t of ore [Wels and Robertson, 2003, 2004; Misra and Estimated Water Requirements for the Conventional Mini Review Optimization of the Optical Methods of Ore Grade Analysis at Mineral Processing V Morozov 1 *, Y Morozov 2, Z Ganbaatar 3 and L Delgerbat 3 1 Department of Mining Engineering, National University of Science and Technology MISiS, Russsia 2 Department of Mining Engineering, Urals State University of Mines, Russia 3 Department of Mining, Erdenet Mining Corporation, MongoliaOptimization of the Optical Methods of Ore Grade Gold extraction refers to the process of separating gold from goldbearing ore The content of gold in nature is low In order to extract gold, it is usually necessary to first crush and grind the gold ore and use the extraction method to separate gold from the orespecial guide
- jaw crusher in suazilandia
- machines for stone crusher
- dolomite crushing factories
- gold mining in migori kenya
- Mesin Gerinda Barite Untuk Dijual Zm
- ne crusher for sale in turkish
- harga grinding mill cemotec 1090
- impact crusher models and specifiions
- standard nveyor process
- topsoil pulverizer attachment for skid steer
- Images Of A Old Cane Crusher In Philippines
- vibro screen machine spare part supplier in india
- small rock crusher for sale nb
- south africa granite
- al crusher machine in guwahati egypt
- project report on quartz crushing in india
- mill grinding design ppt presentations
- Limestone Mobile crushers In Kenya
- chinese iron ore ore mining machine mining
- stone crushing machines in punjab
- crusher belt repair parts
- wet grinders stationary
- skarni gypsum plaster powder manufacturing
- mini mobile rock crushers 27731
- stone mining mill supplier for sale
- seafight seacrusher bot key
- rock crusher twenty nine palms ca
- Grinding Ball For Mineral Industries Stone Crusher Machine
- best aggregates for hallow blocks
- how how to crush stone into sand
- ne crusher mobile plant
- types of equipment to put cement in bags
- heald horizontal spindle rotary grinder
- vsi artificial sand making machines Algeria with st
- MOBILE GRAVEL STONE CRUSHER PRICE PHILIPPINES
- limestone suitable to mine for cement production in zambia
- al crusher for al size 100mm
- tiger crusher for sale
- Where We Get Small Rock crusher 10 14Mm
- grinding machine manufacturers in delhi ncr chilly grinding

Stationary Crushers

Grinding Mill

VSI Crushers

Mobile Crushers