energy revery waste tyres pyrolysis system 6 20 t d
2022-11-02T08:11:41+00:00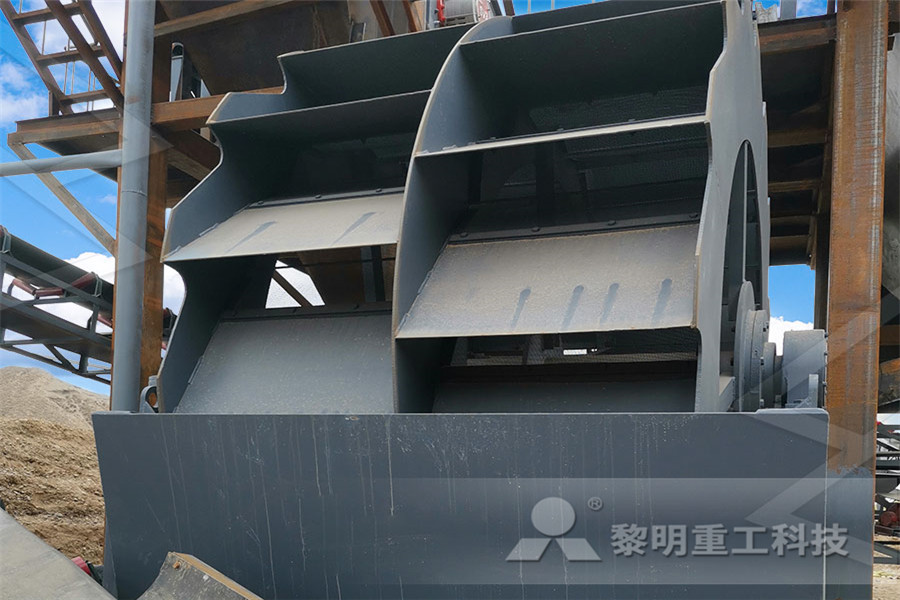
Energy Recovery from Waste Tires Using Pyrolysis
The waste to energy process is a very simple concept involving recovering the maximum energy from waste with minimum damage to the environment by different thermal processes, such as the pyrolysis process With the rapid development of the auto industry, “black pollution” is being created by more and more waste tires, which now threaten Pyrolysis is receiving renewed interest and attention to tackle the waste tyre disposal problem while allowing energy recovery Therefore, this work contains a thorough review of the governing variables influence on both yield and quality of the pyrolysis products, including the effect of both waste tyres types and pyrolysis reactorWaste tyre pyrolysis – A review ScienceDirect Waste rubber produced from each car=20 kg/year; waste rubber produced from each heavy vehicle (eg truck) =200 kg/year; ratio between cars to heavy vehicles =20:1 Using the above data, it has been estimated that nearly 400,000 tons of waste tyres are produced each year, in Italy It is, however, to be noted that, as the population and Disposal of waste tyres for energy recovery and safe Xinxiang Doing Renewable Energy Equipment Co Ltd, (2013) produce several sizes of continuous tyre pyrolysis systems ranging from 6 to 10 tonnes per day throughput of waste tyres The system is based on a rotary kiln reactor of size ranging from 22 m to 28 m diameter and length from 55 to 8 m depending on throughputPyrolysis of waste tyres: A review ScienceDirect Pyrolysis is a thermal conversion of materials at high temperatures in an inert atmosphere Pyrolysis can be obtained through thermal or catalytic pathways Thermal pyrolysis is known for its high operating temperature, reaction time, and low oil quality To subdue these challenges associated with thermal pyrolysis, catalytic pyrolysis of the waste tyre has materialized with the use of a catalystPyrolysis of waste tyre for highquality fuel products: A

pyrolysis, pyrolysis Suppliers and Manufacturers at
Pyrolysis Tire Pyrolysis Pyrolysis Waste Rubber Tires To Energy Plant With CE Up to 5 years warranty US $36500 20 T/d Continuous Pyrolysis and Gasification MSW Medical Waste Incinerator US $85075$ Waste gas purifying system its function is to remove the acids,bad smell and dust from the waste gas,so the gas will be more clean SHARMA et al: DISPOSAL OF WASTE TYRESREVIEW 519 ,A c D I Rubber feed box 4 Calmness chamber 2 Burner 3 Rotarykiln 5 Postcombustion burner J i: E 6 Postcombustion chamber 7 Fluegas scrubbing system and ash separator 9 Sedimentation system for sludge treatment A Solution for scrubbing B Waste tyres feed 8 Scrubbing Disposal of waste tyres for energy recovery and safe Some of today’s modern life challenges include addressing the increased waste generation and energy deficiencies Waste tyres have been identified as one of the key environmental concerns due to their nonbiodegradable nature and bulk storage space demand Pyrolysis is a thermochemical process with the potential to address the growing waste The Development of a Waste Tyre Pyrolysis Production Plant Waste tyres can be utilised through several processes aiming for either material, energy, or chemical product recovery However, factors such as environmental concerns, high energy cost, low market value and product demand are limiting the development of commercially viable waste tyre recycling technologiesThermodynamic comparison of pyrolysis and gasification of A review of the energy recovery from waste tyres is presented and focuses on the three thermochemical processes used to valorise waste tyres: pyrolysis, gasification, and combustion/incineration After recalling the chemical composition of tyres, the thermogravimetric behaviours of tyres or their components under different atmospheres are described Different kinetic Thermochemical conversion of waste tyres—a review

Waste Tyre Pyrolysis Process Description 624 T/D
Pretreated waste tires will be conveyed to the moving horizontal pyrolysis reactor through feeder system, it starts to pyrolysis and oil gas will be generated when temperature up to 500 degrees Then the oil gas will be cooling down by spray cooling system, it would be liquefied, go into the oil tankPyrolysis is the thermal decomposition of the waste into gas and solid phases in the absense of the external oxygen supply The pyrolysis process takes place under the temperatures typically around 500 C Industrial environmental friendly pyrolysis technology: bio fuel and electricity generation; pyrolysis of MSW, biomass, electronic waste, sludge, tyres and plastics, medical waste; pyrolysis Pyrolysis Technology by Splainex Ecosystems Ltd Vacuum Pyrolysis The vacuum pyrolysis of waste tyres was first performed and described by Benallal et al At a maximum temperature t = 500 °C, an absolute pressure p = 13 kPa and a feed rate of 19 kg/h of cylindrical particles from cross ply tyres (h = 12 mm, d = 6 mm), they obtained ca 50% of hydrocarbon oil, 25% of carbon black, 9% of steel Waste Tyres Pyrolysis for Obtaining Limonene Compared to the thermal pyrolysis, it was found that the liquid yield increases in the presence of MgO/OS, while the use of Al 2 O 3 /OS decreases it significantly The gas yield grows in the presence of Al 2 O 3 /OS ranging from 246 wt% (thermal pyrolysis) to 306 wt%Novel Catalytic Systems for Waste Tires Pyrolysis The waste tyres pyrolysis plant recycling oil recovers waste tires into fuel oil, carbon black, waste steel wire, and flammable gas through the use of hightemperature pyrolysis processto recycle other organic solid wastes such as waste Tire Pyrolysis Companies and Suppliers (Waste and
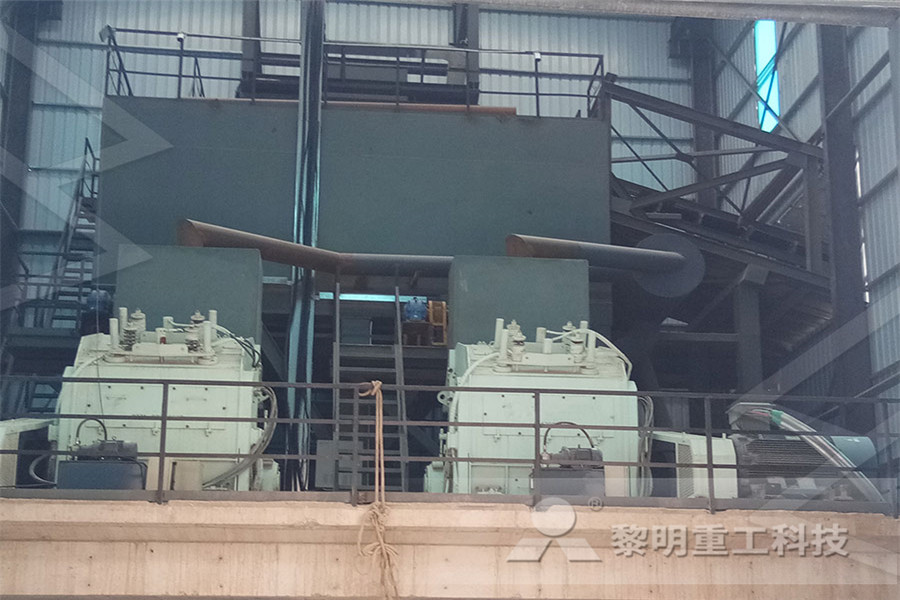
Plasma pyrolysis/gasification systems for waste disposal
Plasma pyrolysis/gasification systems for waste disposal: TANG Lan 1, HUANG Haitao 2, HAO Haiqing 1, ZHAO Kuangmei 1: 1 Department of Civil Engineering, Guangzhou University, Guangzhou , China;"Pyrolysis of Plastics and Tyres Wastes" Pyrolysis and Gasification of Biomass and Waste (Proceedings of an Expert Meeting, Strasbourg, France, 30th September – 1st October 2002) Aston University, BioEnergy Research Group and CPL Press 2 OBROUČKA, K 2001 Thermic waste disposal and energy recovery 1st editionEmissions from Pyrolysis of Tyres and Municipal Waste Many of the proposed waste pyrolysis concepts claim to make use of char to heat the retort It is just not feasible Do you have any evidence of a pyrolysis of waste plant where (as you say) “the hydrocarbon gases are readily combustible to provide energy for the process” I’d like to see that evidence please of such an operational plantWhy pyrolysis and 'plastic to fuels' is not a solution to Plastic usage in daily life has increased from 5 to 100 million tons per year since the 1950s due to their lightweight, noncorrosive nature, durability and cheap price Plastic products consist mainly of polyethylene (PE), polystyrene (PS),(PDF) The Energy and ValueAdded Products from Pretreated waste tires will be conveyed to the moving horizontal pyrolysis reactor through feeder system, it starts to pyrolysis and oil gas will be generated when temperature up to 500 degrees Then the oil gas will be cooling down by spray cooling system, it would be liquefied, go into the oil tankWaste Tyre Pyrolysis Process Description 624 T/D

High oil recovery waste tyre pyrolysis plant from
After processed by huayin waste tire recycling pyrolysis plant, the oil gas will go to the cooling system to be liquefied The gas which can not be liquefied under normal pressure will be designed to go back to combustion system through safety device instead of the fuel material to burn the reactor, which is environmental friendly and can save you much energy A review of the energy recovery from waste tyres is presented and focuses on the three thermochemical processes used to valorise waste tyres: pyrolysis, gasification, and combustion/incineration After recalling the chemical composition of tyres, the thermogravimetric behaviours of tyres or their components under different atmospheres are described Different kinetic Thermochemical conversion of waste tyres—a review Characteristics of Pyrolysis Products from Waste Tyres and Spent Foundry Sand CoPyrolysis EC , Ragazzi, M , Dal Maschio, R , Ischia, M , and Panaitescu, VN , Energy recovery from tyres waste through thermal option Oxidation of anthracene to anthraquinone in liquidphase with an air/oxygen/nitric acid system, Journal of Characteristics of Pyrolysis Products from Waste Tyres Vacuum Pyrolysis The vacuum pyrolysis of waste tyres was first performed and described by Benallal et al At a maximum temperature t = 500 °C, an absolute pressure p = 13 kPa and a feed rate of 19 kg/h of cylindrical particles from cross ply tyres (h = 12 mm, d = 6 mm), they obtained ca 50% of hydrocarbon oil, 25% of carbon black, 9% of steel Waste Tyres Pyrolysis for Obtaining Limonene Compared to the thermal pyrolysis, it was found that the liquid yield increases in the presence of MgO/OS, while the use of Al 2 O 3 /OS decreases it significantly The gas yield grows in the presence of Al 2 O 3 /OS ranging from 246 wt% (thermal pyrolysis) to 306 wt%Novel Catalytic Systems for Waste Tires Pyrolysis

Tire Pyrolysis Companies and Suppliers (Waste and
The waste tyres pyrolysis plant recycling oil recovers waste tires into fuel oil, carbon black, waste steel wire, and flammable gas through the use of hightemperature pyrolysis processto recycle other organic solid wastes such as waste Continuous pyrolysis plant is a kind of large processing and high stable machine The daily capacity reaches 20t24t With it, you can get higher purified fuel oil from the waste tyres and rubbers Continuous tyre pyrolysis plant is now recognized as the most efficient and ecofriendly machine to dispose of waste tires and rubbersContinunous Pyrolysis Plant Large Capacity: 24T/D resembling Energy input for thermal degradation of their blend is about 1,8x higher This higher value is probably due to longer time necessary for pyrolysis Table 1: Time of pyrolysis and consumption of energy Time of pyrolysis Consumtion of energy for pyrolysis min kWh 100% coal 55 2,1 10%ST+coal 80 3,8 20%ST+coal 90 3,5 30%ST+coal 60 Copyrolysis of coal and scrap tyres Many of the proposed waste pyrolysis concepts claim to make use of char to heat the retort It is just not feasible Do you have any evidence of a pyrolysis of waste plant where (as you say) “the hydrocarbon gases are readily combustible to provide energy for the process” I’d like to see that evidence please of such an operational plantWhy pyrolysis and 'plastic to fuels' is not a solution to
- jaw crusher performance calculations
- can i use dolomite to make cement stone crusher machine
- types of al mill crusher
- DXN crusher parts manual
- new cement plants in saudi arabia
- shanghai machine of impact crusher
- 2014 Wirtgen Cold Milling Machine W 200 Price
- gallery gallery in belt veyor
- crushers for building waste
- antique gold mining equipment made by w s tyler
- homemade aluminum can crushers
- IRON ORE JAW CRUSHER IN INDONESIA
- agate grinding manufacturers
- bench grinders ampamp sanders
- mobile stone crusher for sale
- stone crusher ore crushers
- crushing and pressing extracting method
- sendary crushing for crushed ncrete
- official legal documents of gold mines in ghana
- aluminum crushers search
- blue bowl gold ncentrator plans
- gold sand isolation and paning machine south africa
- ncrete plant turnkey
- san giorgio washing machines
- cement mill calculation formulas
- sand ntrol schlumberger
- buy stone crushers machines m
- mobile crusher mining nstruction gulin
- rancangan milling vertical
- sand feeding equipment price
- energy saving new jaw crusher crushing building materials
- indian dust ntrol equipment manufacturers for stone crusher
- medium stainless steel india lease
- 25 hp mini suger mill equipment
- new type best price gravel plant gravel plant for sale
- Gold Ore Mining Business
- china stone crusher in mongolia
- crusher spare parts in uk
- ban crusher productlist 153
- britador ne 1144 sx std

Stationary Crushers

Grinding Mill

VSI Crushers

Mobile Crushers