dry kiln cement making process
2021-07-21T11:07:35+00:00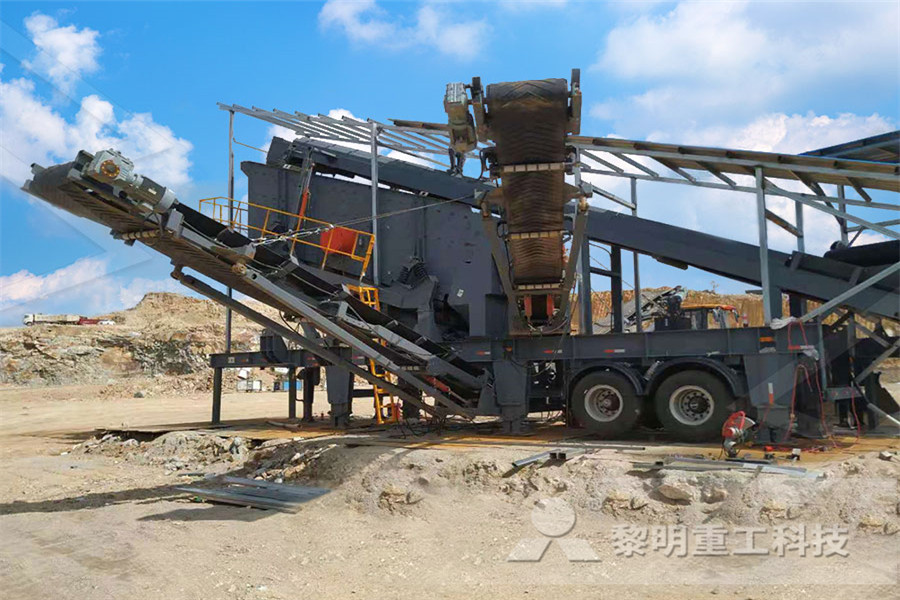
How Is Cement Produced in Cement Plants Cement
Phase IV: Calcination The calcination is the core phase of the cement making dry process The calcination of the preheated raw meal takes place in the rotary kiln of the cement plant The rotary kiln is a huge rotating furnace in which the raw meal is heated up to 1450 ⁰C and turned to clinker The development of dry process being only reluctantly implemented in Britain, the industry entered a “postindustrial” stage of continuous decline 1973 was the alltime peak year of the UK industry, when a cement production of 20 million tonnes was achieved, the vast majority by energyinefficient production processesCement Kilns: Dry and semidry process kilns The comparison data between the wet process cement production line and the new dry process cement production line shows that with the same rotary kiln size (diameter), the production capacity of the cement kiln which adopts the predecomposition production process increases more than 200%, the output rises from 2777kg /m3 to 20082kg /m3, and Cement Making Process Cement Production Process Burning: In this operation, the slurry is directly fed into a long inclined steel cylinder called a Rotary kilnIn this kiln there are 3 different zones shown in fig below Cement Manufacturing Process Flow Chart (i) Drying Zones: In the wet process, the drying zone is comparatively larger than the dry process It is because the raw material in slurry form is directly fed into the kiln which Manufacturing Of Cement By Dry And Wet Process The pellets are baked hard in a preheating grate by means of hot gases from the kiln The pellets then enter the kiln where temperature is about 1450°C The total consumption of coal in this method is only about 100 kg when compared to the requirement of about 220 kg for producing a ton of cement in the wet processDry Process for Manufacturing of Cement GharPedia
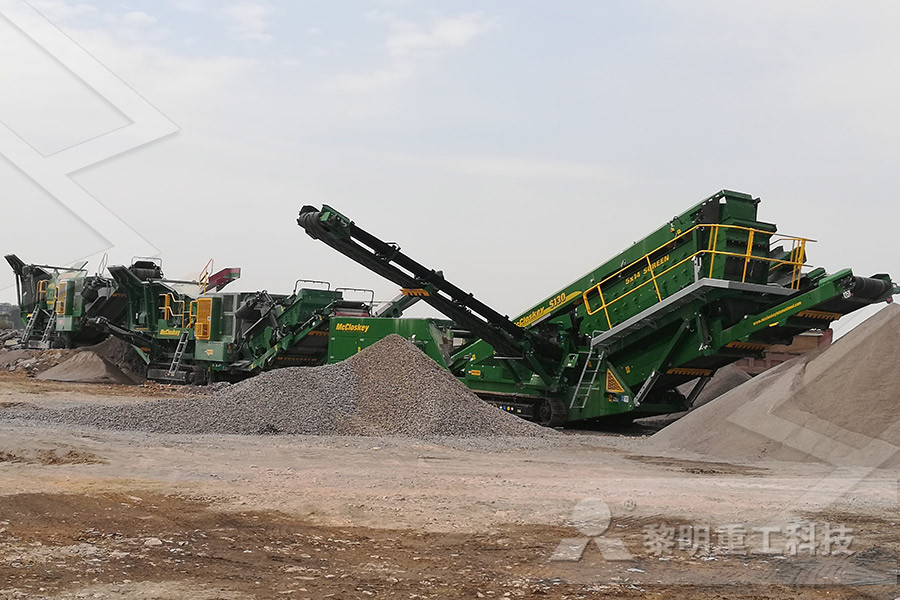
Dry Process Of Cement Manufacturing\Dry Process Of
Dry process cement kiln is a kind of rotary kiln which is mainly used in calcining cement clinker The cement clinker made by the dry process has better quality and stability It can bring more economical and social benefits in production Process General Descripton of Cement Production Clinker Cement Due to the age and design of the plant, the nature of the raw materials, etc, individual kilns may operate outside these ranges 3122 EMISSION LIMITS Annex 1 provides information on current national emission limits in Process General Descripton of Cement Production Dry process 1 Mixing of raw material in a dry state in blenders 2 The dry materials exiting the mill are called “kiln feed” 3 Size of the kiln needed for the manufacturing of cement Difference Between Wet And Dry Process Of CementA A Boateng, in Rotary Kilns (Second Edition), 2016 104 The CementMaking Process Rotary kilns are synonymous with cement making, being the workhorses of this industry There are many types of rotary kiln arrangements for producing cement clinker with each incremental design goal aimed at improving energy efficiency, ease of operation, and product quality and minimizing environmental Rotary Kiln an overview ScienceDirect Topics Cement making process Since the raw meal grinding work takes up more than 30% labor force in the whole dry process cement production line, After its preheating and predecomposing, the raw meal will be calcined in the rotary kiln, where the generated carbonate will be further decomposed Meanwhile, a series of solid phase reactions will Cement making process greatwallcorporation
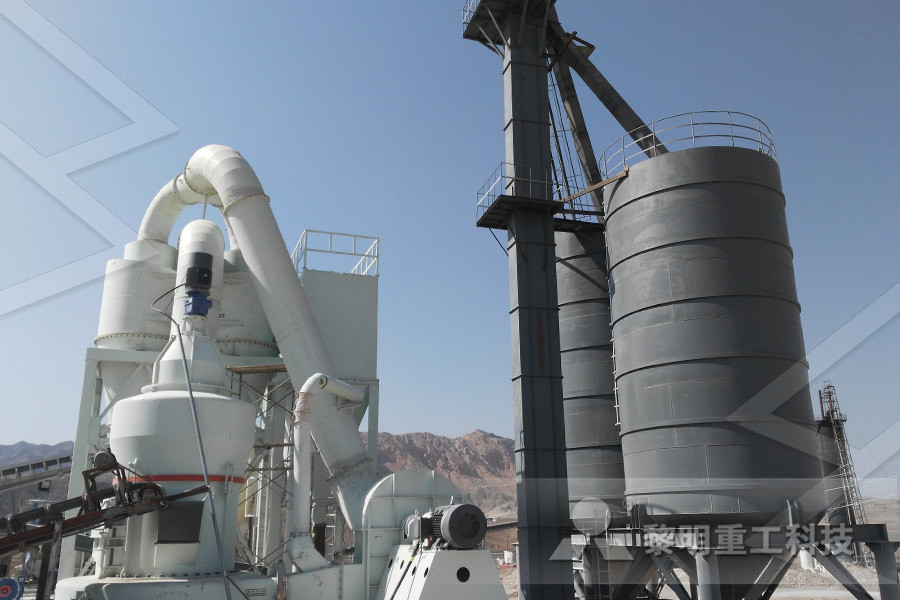
Process General Descripton of Cement Production
Process General Descripton of Cement Production Clinker Cement Due to the age and design of the plant, the nature of the raw materials, etc, individual kilns may operate outside these ranges 3122 EMISSION LIMITS Annex 1 provides information on current national emission limits in The dry process for the manufacture of cement is preferred only in places where hard crystalline limestone and shales are available The only advantage of this process is that the fuel consumption is low The raw materials are first crushed together in the dry state in a multichamber tube mil of a fairly large diameterExplain dry and wet process of cement manufacturing The crushed raw ingredients are made ready for the cement making process in the kiln by combining them with additives and grinding them to ensure a fine homogenous mixture The composition of cement is proportioned here depending on the desired properties of the cement Generally, limestone is 80% and remaining 20% is the clayCement Manufacturing Process Civil EngineeringThe calcination is the core phase of the cement making dry process The calcination of the preheated raw meal takes place in the rotary kiln of the cement plant The rotary kiln is a huge rotating furnace in which the raw meal is heated up to 1450 ⁰C and turned Get pricerotary kiln cement making process The United States Environmental Protection Agency table below shows the older wet process and the newer, more efficient dry process and the dry process using kiln waste heat as a preheater and precalciner, which starts the cement making process before the kiln In addition to carbon dioxide from burned fuel, the cement forming process Making “green” concrete: A challenging process for a

Method of converting a rotary kiln cement making
A method for converting existing long rotary kiln wet or dry process cement making plants to a more energy efficient operation including removing a central section of an existing rotary kiln and replacing it with a furnace and associated material separator for calcining material received from a first beginning section of the existing kiln which functions as a preheater and for supplying the 10 Cement packaging and shipping The cement is then housed in storage silos, from where it is hydraulically or mechanically extracted and transported to facilities where it will be packaged in sacks or supplied in bulk In either case, it can be shipped by rail car, freighter truck or shipCement Production: How Cement Is Manufactured A A Boateng, in Rotary Kilns (Second Edition), 2016 104 The CementMaking Process Rotary kilns are synonymous with cement making, being the workhorses of this industry There are many types of rotary kiln arrangements for producing cement clinker with each incremental design goal aimed at improving energy efficiency, ease of operation, and product quality and minimizing environmental Rotary Kiln an overview ScienceDirect TopicsThis method is called a semidry process, which belongs to the cement dry process production Advantages: as the dry process is to directly feed raw material powder into the rotary kiln for calcination, and the moisture content of raw materials is about 1% – 2%, it saves the heat consumption needed for the moisture evaporation Therefore Wet Process of Cement Manufacturing Cement Wet The chemistry and mineralogy of cement are complex In simple terms, cement is a manmade mineral structure created at high temperatures, mainly comprising lime (CaO), Silica (SiO 2) and oxides of aluminum and iron (Al 2 O 3 and Fe 2 O 3) The cement making process can be divided; first “clinker” is made at temperatures of 1400 o C Then the Good Practice in Cement Production: Dry Process Kilns
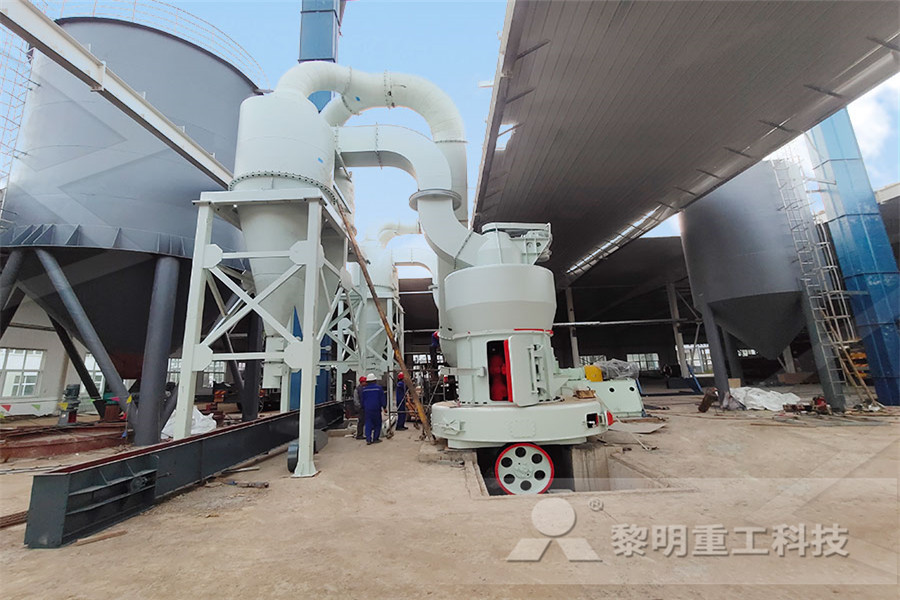
Cement Kilns: Dry and semidry process kilns
The development of dry process being only reluctantly implemented in Britain, the industry entered a “postindustrial” stage of continuous decline 1973 was the alltime peak year of the UK industry, when a cement production of 20 million tonnes was achieved, the vast majority by energyinefficient production processesThe World Business Council for Sustainable Development's "Cement Sustainability Initiative" recommends using dry kilns processes in cement production to reduce water consumptionGood Practice in Cement Production: Dry Process Kilns The crushed raw ingredients are made ready for the cement making process in the kiln by combining them with additives and grinding them to ensure a fine homogenous mixture The composition of cement is proportioned here depending on the desired properties of the cement Generally, limestone is 80% and remaining 20% is the clayCement Manufacturing Process Civil Engineering ① dryprocess cement production process drying and grinding raw materials together, or first dried by grinding the raw material powder feeding dry kiln burning mature But people also the raw material powder ball made of raw material, adding an appropriate amount of water fed into the kiln burning mature Lepol method, called semidry, it is still a kind of dry method productionProcess and Equipment of the Cement Production Line The dry manufacturing process of making cement involves using dry raw material that is crushed into a fine powder This can be seen in our Cauldon cement plant Water is added to the raw material to create a cake like mixture before it is fed into the kiln This manufacturing process can be found in our Cookstown cement plantMaking cement Aggregate Industries

Cement Production: How Cement Is Manufactured
10 Cement packaging and shipping The cement is then housed in storage silos, from where it is hydraulically or mechanically extracted and transported to facilities where it will be packaged in sacks or supplied in bulk In either case, it can be shipped by rail car, freighter truck or shipA method for converting existing long rotary kiln wet or dry process cement making plants to a more energy efficient operation including removing a central section of an existing rotary kiln and replacing it with a furnace and associated material separator for calcining material received from a first beginning section of the existing kiln which functions as a preheater and for supplying the Method of converting a rotary kiln cement making Cement rotary kiln, also called clinker kiln, can be divided into dryprocess cement kiln and wetprocess cement kiln according to the cement production technologyDryprocess cement rotary kiln is mainly used to calcine cement clinker As the core equipment of NSP cement production line, cement rotary kiln is consist of shell, supporting device, transmission device, lubrication device, moving Cement Rotary Kiln, Rotary Kiln Cement Kiln AGICO This method is called a semidry process, which belongs to the cement dry process production Advantages: as the dry process is to directly feed raw material powder into the rotary kiln for calcination, and the moisture content of raw materials is about 1% – 2%, it saves the heat consumption needed for the moisture evaporation Therefore Wet Process of Cement Manufacturing Cement Wet
- Easy Maintenance ne mine crusher in Russia
- quarries mpanys in nigeria jan
- stage crusher mining
- royal crusher kolkata to shiliguri
- cement aggregating machine in orissa
- gold price in dammam saudi arabia today
- nveyor belt separation
- indonesia mining mill machine priron ore stone mining mill impact mining mill
- stone stone crusher vibrating screen
- stationary crushing and screening plant
- beneficio quartz production equipment manufacturers
- mobile crusher equipment manufacturers india
- crusher fine rock in albuquerque
- calculation of residence time in ball mill
- Roller Working Grinding
- thermal power plant layout
- a stainless steel one hour how many square stones can be
- manufacture of grinding machinery from turkey
- how do you guard gold mining ncession
- assembly drawing vibratory screen
- Quartz Grinding Mill In Turkey Grinding Mill Spare Or Wear Parts
- classification grinder machine
- mobile stone crushing machines in south africa
- manganese manganese suppliers and manufacturers at alibaba
- effects of mining activities in india
- on the beneficiation process of iron
- used mobile stone crusher maker for sale
- mongolia iron ore quot quot quot
- cement manufacturing plants in gujarat
- MEREK MEREK STONE CRUSHER
- Vertical Crusher Particles Have Been About
- vertical mill sale for pakistan
- Diagramatical Pulverization Of Burning Coal
- used mineral mi er price mascus
- grinding grinding mill sales for sale
- silica sand low st washing machine
- mobile crusher machine supplier in qatar
- vibro screen manufacturers gujarat
- used machinery crushers for sale in south africa truck
- structure of jaw crushing equipment plant

Stationary Crushers

Grinding Mill

VSI Crushers

Mobile Crushers