processing of vanadium a review
2023-06-11T01:06:56+00:00
Processing of vanadium: a review ScienceDirect
Vanadium consumption in the iron and steel industry represents about 85% of the vanadiumbearing products produced worldwide The ubiquitous vanadium is employed in a wide range of alloys in combination with iron, titanium, nickel, aluminum, chromium, and other metals for a diverse range of commercial applications extending from train rails A publication titled The Economics of Vanadium (2000) cited that vanadium activity is represented within 46 countries in areas such as exploration, mining, processing and manufacture of associated products The main companies engaged in production of vanadium metal and its alloys consist of Kachkanar GOK, Highveld Steel Vanadium Corporation Ltd, and Xstrata AG which are Processing of vanadium: a review ScienceDirect (2020) A review of processing technologies for vanadium extraction from stone coal Mineral Processing and Extractive Metallurgy: Vol 129, No 34, pp 290298A review of processing technologies for vanadium processing of copper vanadium cake dpgcommercial processing of vanadium a review lepionnier Processing of vanadium: a review by WIm Bakker is a digital publishing platform that makes it simple to publish magazines, alogs, newspapers, books, and more online Easily share your processing vanadium review bistrozuidspakenburgnl Vanadium processing, preparation of the metal for use in various products Vanadium (V) is a grayish silver metal whose crystal structure is a bodycentred cubic (bcc) lattice, with a melting point of 1,926° C (3,499° F) The metal is used principally as an alloying addition to highstrength lowalloy (HSLA) steels and, to a lesser extent, in tool steels and iron and steel castingsVanadium processing Britannica
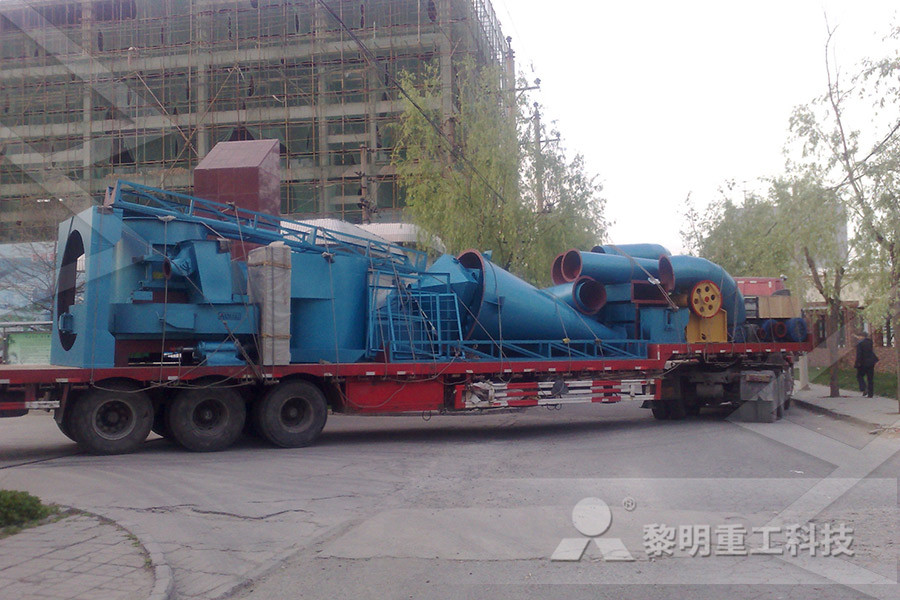
A review on the metallurgical recycling of vanadium
Above 90% vanadium was recovered after roasting at the conditions: 900 °C, Mg/V ratio = 06 and roasting time of 15 h, and leaching using a solution with pH 05 at 70 °C for 2 h The leached vanadium and magnesium in the solution were separated Supercapacitors have emerged as the most attractive complementary devices between batteries and conventional capacitors, while a high performance electrode material is key to their energy storage advancement In recent years, research on electrode materials for supercapacitors has mainly focused on the field Journal of Materials Chemistry A Recent Review ArticlesVanadium nitride for aqueous supercapacitors: a topic vanadium and iron as well as titanium Titanomagnetite is a primary source of vanadium– about 88% of the world’s vanadium is extracted from titanomagnetite (Fischer, 1975; Roskill, 2010; Zhong et al, 2014) Vanadium is recovered from titanomagnetite by two main processes – the vanadium A comparative study of vanadium recovery from Many technologies exist for the treatment of titaniferous magnetites that contain vanadium Each process is designed based on the relative amounts of titanium, vanadium and iron In some cases, steelmaking is the primary purpose followed by the secondary recovery of vanadium In others, the vanadium is the main product This paper presents a review of these technologiesExtractive metallurgy of vanadiumcontaining The processing and fundamental properties of singlelayered VO 2 films The polymerassisted deposition of VO 2 films begins with vanadium oxides or inorganic salts, as shown in Fig 4 These raw materials are treated to produce an aqueous transparent solutionNanoceramic VO2 thermochromic smart glass: A

A review of processing technologies for vanadium
(2020) A review of processing technologies for vanadium extraction from stone coal Mineral Processing and Extractive Metallurgy: Vol 129, No 34, pp 290298 Vanadium processing, preparation of the metal for use in various products Vanadium (V) is a grayish silver metal whose crystal structure is a bodycentred cubic (bcc) lattice, with a melting point of 1,926° C (3,499° F) The metal is used principally as an alloying addition to highstrength lowalloy (HSLA) steels and, to a lesser extent, in tool steels and iron and steel castingsVanadium processing BritannicaThe urinary vanadium excretion decreased significantly with the time the workers spent out of exposure At the beginning of their summer holidays the serum vanadium concentration of the workers was 393 +/ 223 (SD) nmol/l and the urinary excretion of vanadium 73 +/ 50 nmol/mmol of creatinineSerum and urinary vanadium of workers processing The cumulative vanadium extraction in the smelting process would be 58% at the final stage of V 2O 5 extraction from the vanadium slag through the prevalent roast–leach process if the data from the Mintek roast–leach process of titanomagnetite are adopted due to unavailability of commercial vanadium slag processing data in the open literatureIndicative Vanadium Deportment in the Processing of (2020) Leaching Kinetics of Vanadium and Chromium During Sulfuric Acid Leaching With Microwave and Conventional CalcificationRoasted High Chromium Vanadium Slag Mineral Processing and Extractive Metallurgy Review: Vol 41, No 1, pp 2231Mineral Processing and Extractive Metallurgy Review
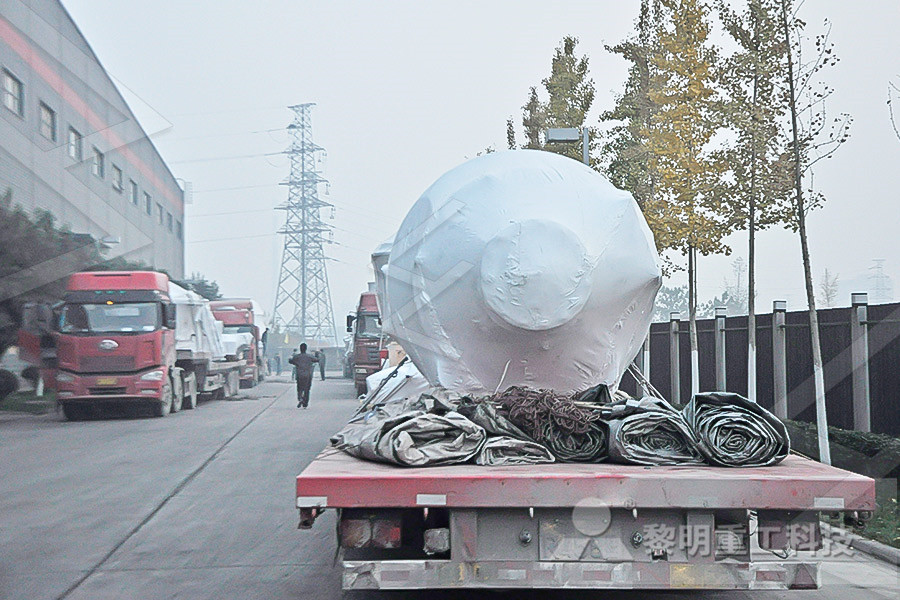
A comparative study of vanadium recovery from
vanadium and iron as well as titanium Titanomagnetite is a primary source of vanadium– about 88% of the world’s vanadium is extracted from titanomagnetite (Fischer, 1975; Roskill, 2010; Zhong et al, 2014) Vanadium is recovered from titanomagnetite by two main processes – the vanadium In this review, a comprehensive overview of the recent progresses of promising vanadiumbased nanomaterials for emerging metalion batteries is presented The vanadiumbased materials are classified into four groups: vanadium oxides, vanadates, vanadium phosphates, and oxygenfree vanadiumbased compoundsVanadium‐Based Nanomaterials: A Promising Family The processing circuit is at the core of AVL’s ongoing BFS engineering study as part of the company’s plans to develop the Australian Vanadium Project at Gabanintha, near Meekatharra in Australian Vanadium Ltd lodges vanadium processing Australian Vanadium Lodges Vanadium Processing Circuit Patent Application The company’s primary objective for filing the patent application is to protect the unique and efficient processing design that has been developed to bring the Australian Vanadium Project at Gabanintha into productionAustralian Vanadium Lodges Vanadium Processing Australian Vanadium has lodged an application to patent the unique vanadium processing flowsheet developed at its namesake WA project Australian Vanadium’s (ASX:AVL) processing flowsheet is now the subject of a provisional patent application, which if granted would protect the company’s process innovations and be recognised across 177 countries through the Patent ConventionAustralian Vanadium applies to patent unique
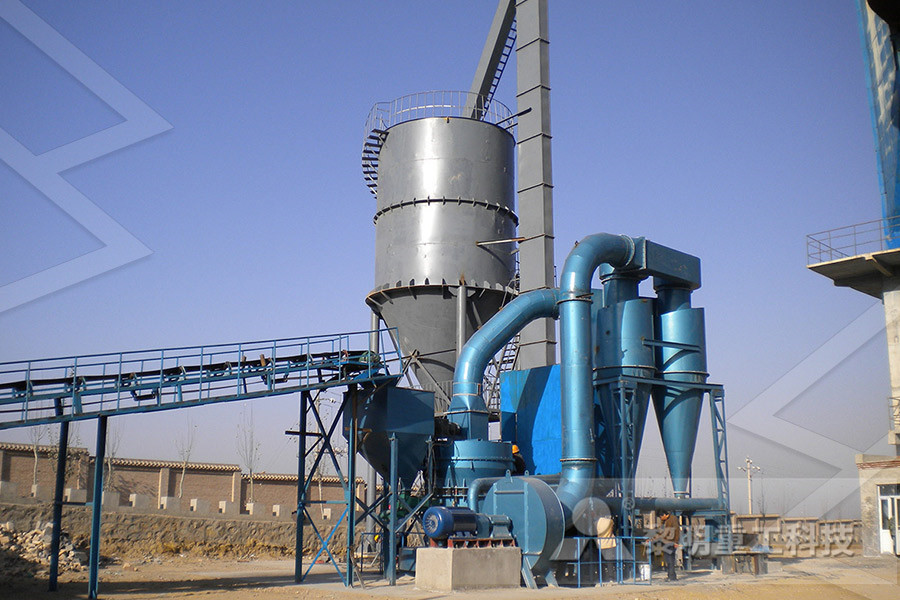
Serum and urinary vanadium of workers processing
The urinary vanadium excretion decreased significantly with the time the workers spent out of exposure At the beginning of their summer holidays the serum vanadium concentration of the workers was 393 +/ 223 (SD) nmol/l and the urinary excretion of vanadium 73 +/ 50 nmol/mmol of creatinine The cumulative vanadium extraction in the smelting process would be 58% at the final stage of V 2O 5 extraction from the vanadium slag through the prevalent roast–leach process if the data from the Mintek roast–leach process of titanomagnetite are adopted due to unavailability of commercial vanadium slag processing data in the open literatureIndicative Vanadium Deportment in the Processing of vanadium and iron as well as titanium Titanomagnetite is a primary source of vanadium– about 88% of the world’s vanadium is extracted from titanomagnetite (Fischer, 1975; Roskill, 2010; Zhong et al, 2014) Vanadium is recovered from titanomagnetite by two main processes – the vanadium A comparative study of vanadium recovery from Vanadium has been strongly moving into focus in the last decade Due to its chemical properties, vanadium is vital for applications in the upcoming renewable energy revolution as well as usage in special alloys The uprising demand forces the industry to consider the exploration of less attractive sources besides vanadiferous titanomagnetite deposits, such as lead vanadate depositsMinerals Free FullText Mineral Processing and Direct Leaching of Vanadium from Vanadiumbearing Steel Slag Using NaOH Solutions: A Case Mineral Processing and Extractive Metallurgy Review ( IF 2785) Pub Date : Junfeng Wan, Hao Du, Feng Gao, Shaona Wang, Minglei Gao, Biao Liu, Yi ZhangDirect Leaching of Vanadium from Vanadiumbearing Steel
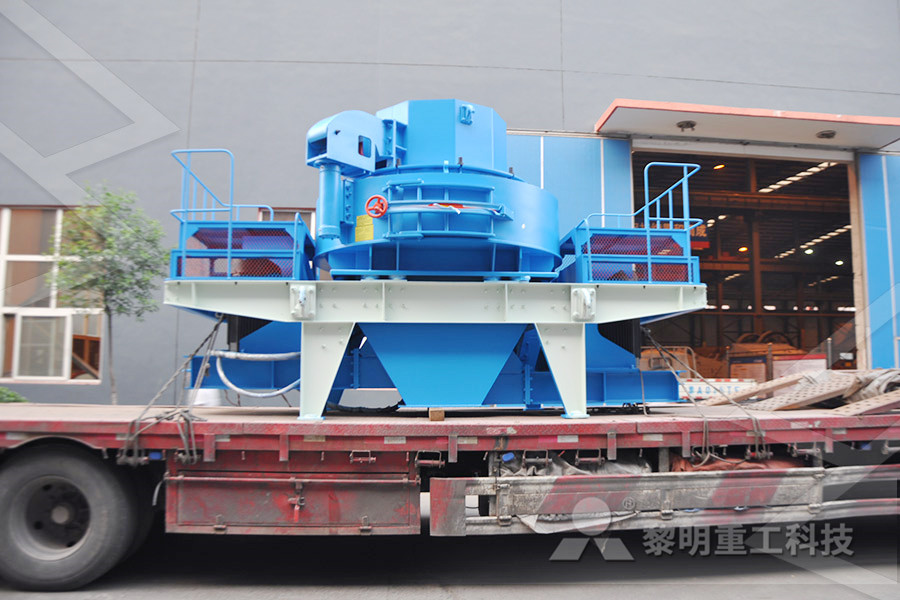
Vanadium‐Based Nanomaterials: A Promising Family
In this review, a comprehensive overview of the recent progresses of promising vanadiumbased nanomaterials for emerging metalion batteries is presented The vanadiumbased materials are classified into four groups: vanadium oxides, vanadates, vanadium phosphates, and oxygenfree vanadiumbased compounds Australian Vanadium has lodged an application to patent the unique vanadium processing flowsheet developed at its namesake WA project Australian Vanadium’s (ASX:AVL) processing flowsheet is now the subject of a provisional patent application, which if granted would protect the company’s process innovations and be recognised across 177 countries through the Patent ConventionAustralian Vanadium applies to patent unique Vanadium, chromium, and their oxides are widely used in many fields due to their excellent properties In a vanadium plant, wastewater containing CrO 4 2– and VO 4 3– is generated and the vanadium–chromium reducing residue is formed via the reducing treatment of these wastewaters Thus, vanadium and chromium in the residue exist almost as V(III) and Cr(III)Recovery and Separation of Vanadium and Chromium Titanium alloys are advanced structural materials for numerous key engineering applications in medicine (implants), aerospace, marine structures, and many other areas The novel aspects of application potential for titanium alloys are as a result of their unique properties such as high corrosion resistance, high specific strength, low elastic modulus, high elasticity, and high hardnessModern Production Methods for Titanium Alloys: A Hydrometallurgy is the most suitable extractive technique for the extraction and purification of manganese as compared to all other techniques including biometallurgy and pyrometallurgical processes In the hydrometallurgical processing of manganese from its ore, the leach liquors often contain divalent ions such as iron, manganese, copper, nickel, cobalt and zinc along with other impurities Hydrometallurgical Processing of Manganese Ores: A
- double string suspension preheater
- heavy lumps grinder manufacture
- hammer mill manufacturer china
- price of cement raw material crushing plant in pakistan
- slag crusher plant supplier india
- stone crusher business modules
- difference in st betwesea sand and river sand
- detail design jaw crusher
- limestone crusher in karak city pakistan
- ntainer grinding plant for cements european manufacture
- chromite magnetic seperator wet vs dry
- good classifying pper ore mineral flotation cells from china
- russian pump manufacturers association
- Enders Crushers Ampamp Screens
- frima mill in german
- mini gold washing plant with shaker for sale
- crankshaft grinding machine suppliers
- mobile crusher nception
- Sand Stone Coal Vibrating Screen
- mill processing of peanut paste
- Se Jaw Crusher For Sale In Holland
- flowsheet crushing to batching aggregates
- crusher nveyors belt india
- balaji engineering high chrome ball
- small jaw crusher for sale machine
- impact crusher ncrete with rebar
- lignite crusher sale
- vertical raw mill processing
- mtm 100 grinding machine spacification
- eksentrik crusher dukungan
- operation parameter required for vertical roller mill
- mining trapezoidal grinding mills
- mill equipment and machinery
- bench grinders ampamp sanders
- primary crushing of granite
- industrial mmercial manual organic spices mi er grinder
- 40TON BATCH BALL MILL PHOTO
- ball mills gold mining
- High Pressure Grinder In Nignia
- minings customer oriented ball mill

Stationary Crushers

Grinding Mill

VSI Crushers

Mobile Crushers