influence of dry grinding in a ball mill on the length of
2020-07-14T13:07:30+00:00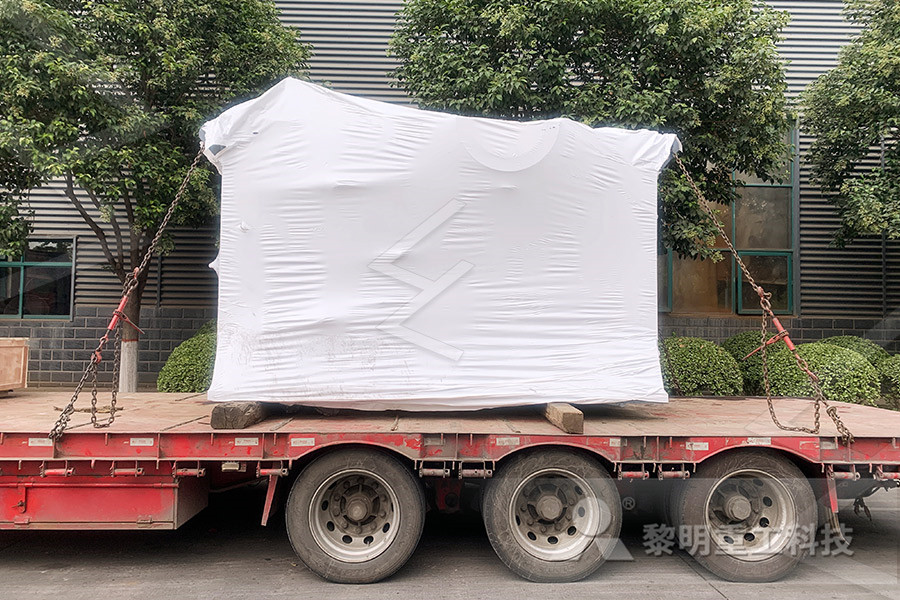
Influence of dry grinding in a ball mill on the length of
The CNT length distributions of the three different CNT materials and the x 10, x 50, and x 90values describing the distributions as determined using TEM are shown in Fig 3 including a TEM image of N700010 h The highest CNT length and a very broad distribution up to 6 μm were found for the asgrown NC7000The ball milled CNTs were significantly shorter than the asgrown material, Ball milling of carbon nanotubes (CNTs) in the dry state is a common way to produce tailored CNT materials for composite applications, especially to adjust nanotube lengths For Nanocyl TM NC7000 nanotube material before and after milling for 5 and 10 h the length distributions were quantified using TEM analysis, showing decreases of the mean Influence of dry grinding in a ball mill on the length of Influence of dry grinding in a ball mill on the length of multiwalled carbon nanotubes and their dispersion and percolation behaviour in melt mixed poly‐ carbonate composites Beate Krause, Tobias Villmow, Regine Boldt, Mandy Mende, Gudrun Petzold, Petra Pötschke PII: S02663538(11)001369 DOI: 101016/jpscitech201104004 Reference Influence of dry grinding in a ball mill on the length of The grinding machine was a laboratory scale mill made of alumina with an inside diameter of 013 m and an inner volume of 20 dm 3The grinding media were alumina balls of 3600 kg m −3 density and two different ball diameters; 10 mm and 20 mm The feed size of the material was 1180–1000 μm for all grinding conditionsThe masses of the feed sample and the mass of the grinding balls were 0 Influence of dry and wet grinding conditions on fineness Abstract: In this study the effect of dry grinding on hydrophobicity, surface free energy (SFE), particle size distribution, surface area, porosity, oil absorption, and whiteness of talc was investigated The dry grinding was performed in a vibrating ball mill at various grinding Influence of Dry Grinding On PhysicochemiCal and

Influence of dry and wet grinding conditions on fineness
The influence of grinding conditions on the production of fine particles and the width of the particle size distribution produced during ball mill grinding was investigated The grinding experiments were carried out varying the grinding ball diameter under dry and wet conditions The relation between the weight passing size observed in an a) Mill Geometry and Speed – Bond (1954) observed grinding efficiency to be a function of ball mill diameter, and established empirical relationships for recommended media size and mill speed that take this factor into account As well, mills with different length Factors Affecting Ball Mill Grinding EfficiencyInfluence of an Organic Polymer in BallMill Grinding of Quartz, Dolomite, and Copper Ore By A R Rule A J Fergus and C B Daellenbach UNITED STATES Influence of an Organic Polymer in BallMill Grinding of In this study, to determine the grinding parameters of the specific rates of breakage and a primary breakage distribution, the Mill used in the grinding experiment was made of perspex materials and can be seen in Fig 3The diameter and the height of the mill were respectively 20 cm, and all of the six mills were the identical and the number, length of lifters conditions were differentAnalysis of grinding kinetics in a laboratory ball mill Zhang et al 13 experimentally studied the effect of the balltopowder ratio, size of milling balls, medium and rotation speed in the wet grinding of a planetary ball mill considering just the mean particle size concerning particle size distribution In this manuscript, wet grindings on a planetary mill were performed in order to analyze the Influence of Media Geometry on Wet Grinding of a Planetary
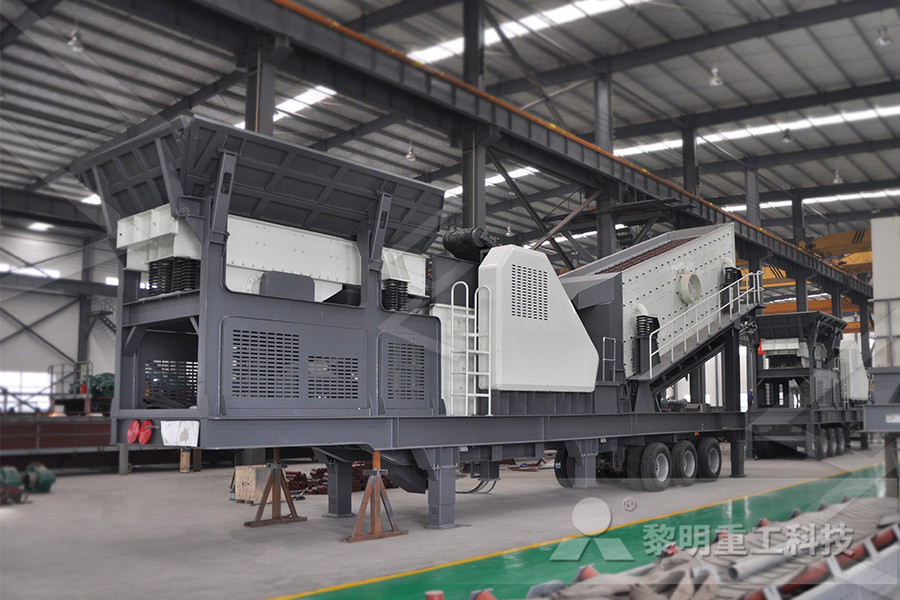
DeepDyve Unlimited Access to PeerReviewed Journals
DeepDyve is the largest online rental service for scholarly research with thousands of academic publications available at your fingertips The length of the cylinder decides the remain time of the ore in the cylinder Longer of the cylinder, more serious of the grinding While if the length is not enough, target fineness maybe not being reached The diameter property of the ball mill usually get 115 03 3Operating Conditions of the Ball MillInfluence Factors of the Ball Mill in the Process of a) Mill Geometry and Speed – Bond (1954) observed grinding efficiency to be a function of ball mill diameter, and established empirical relationships for recommended media size and mill speed that take this factor into account As well, mills with different length to diameter ratios for a given power rating will yield different material Factors Affecting Ball Mill Grinding Efficiency The experimental mill used was a laboratory scale ball mill of 150 mm dia170 mm lengthgiving a total volume of 3000 cc, with steel balls of 25mm dia, so as to occupy 50% of the ball mill volume and an operating speed of 60 rpm, which is 70% of the critical speed of the ball mill The feed size of the material used was of aExperimental Studies on Effect of Grinding Additives in Krause B, Villmow T, Boldt R, et al (2011) Influence of dry grinding in a ball mill on the length of multiwalled carbon nanotubes and their dispersion and percolation behaviour in melt mixed polycarbonate composites Compos Sci Technol 71: 1145–1153 Carbon nanotubes agglomeration in reinforced
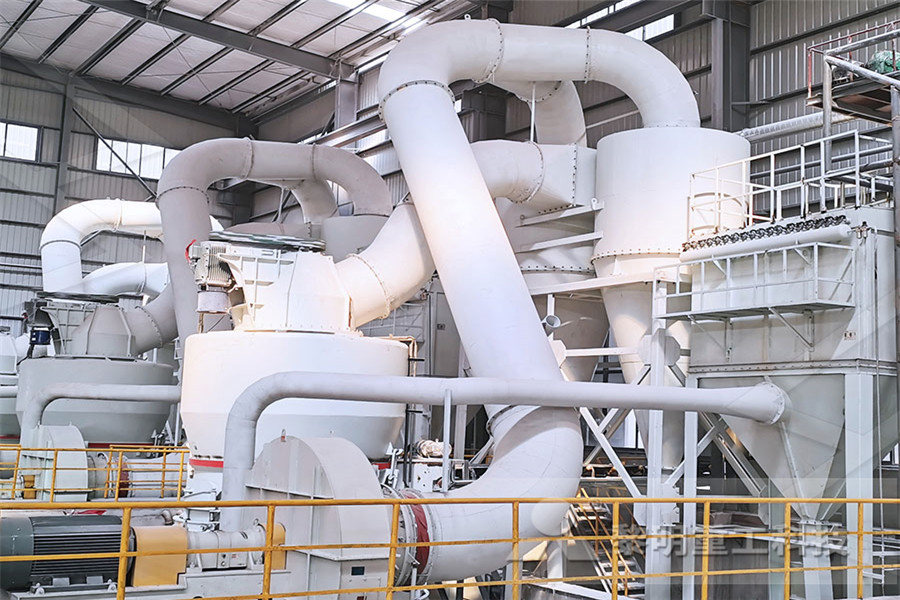
Correlations for the Grindability of the Ball Mill As a
Where, y is cumulative percent passing size d, d 50 is the 50% passing size, n is distribution constant, and k is a correction factor The n values ranged from 084 to 184, and k values from 095 to 100 By using the Bond method of grindability, H Ipek et al [4] have observed that less specific energy input is required in separate grinding of ceramic raw materials than grinding them inIn order to improve the performance of gypsum mould, dry grinding process was applied to the pretreatment of gypsum powder and the effect of the ballmilling time on the performance of gypsum powders was mainly studied in our work XRay powder diffraction (XRD) and scanning electron microscope (SEM) were employed to characterize the phase compositions and microstructures of Effect of Different Grinding Time on the Performance Whether grinding is to be performed wet or dry, or in a ball mill or rod mill, a choice must be made between open or closed circuit Other factors which require thought are mill size, speed of mill rotation, moisture content, retention time, circulating load, type and sizes of grinding media, mill pulp level, mill shape, power, and relation Comminution Theory Process Equipment 911 1 Calculation of ball mill capacity The production capacity of the ball mill is determined by the amount of material required to be ground, and it must have a certain margin when designing and selecting There are many factors affecting the production capacity of the ball mill, in addition to the nature of the material (grain size, hardness, density, temperature and humidity), the degree of Ball Mill Parameter Selection Calculation Power Ball mill installation is a must step before it is put into production, which will affect the subsequent use of the ball mill, and even affect the production volume, crushing rate, service life, etc, so the importance of ball mill installation is selfevident In addition, the choice of grinding medium is also crucial In the grinding process, different grinding medium can be used for 4 Installation Steps, 10 Requirements and Medium

Influences of operating parameters on dry ball mill
Influences of operating parameters on dry ball mill performance Serkan Cayirli Nigde Omer Halisdemir University, Nigde, Central Campus, 51240, Turkey Corresponding author: (Serkan Cayirli) Abstract: The paper is aimed to investigate the influence of operating parameters on dry fine grindingThe paper is aimed to investigate the influence of operating parameters on dry fine grinding of calcite in a laboratory scale conventional ball mill Within the context, the influence of operating parameters such as mill speed, ball filling ratio, ball size distribution, powder filling ratio, grinding aid dosage and grinding Influences of operating parameters on dry ball mill The experimental mill used was a laboratory scale ball mill of 150 mm dia170 mm lengthgiving a total volume of 3000 cc, with steel balls of 25mm dia, so as to occupy 50% of the ball mill volume and an operating speed of 60 rpm, which is 70% of the critical speed of the ball mill The feed size of the material used was of aExperimental Studies on Effect of Grinding Additives in In dry grinding in ball mills, the loading time is less than 1 second and cracks will propagate faster than 101 em/sec Therefore, one must conclude that for dry grinding neither adsorption nor chemical reaction can influence crack propagation in a comminution mill For wet grinding, however, crack velocities must beReview Grinding Aids t JSTAGE Home Where, y is cumulative percent passing size d, d 50 is the 50% passing size, n is distribution constant, and k is a correction factor The n values ranged from 084 to 184, and k values from 095 to 100 By using the Bond method of grindability, H Ipek et al [4] have observed that less specific energy input is required in separate grinding of ceramic raw materials than grinding them inCorrelations for the Grindability of the Ball Mill As a
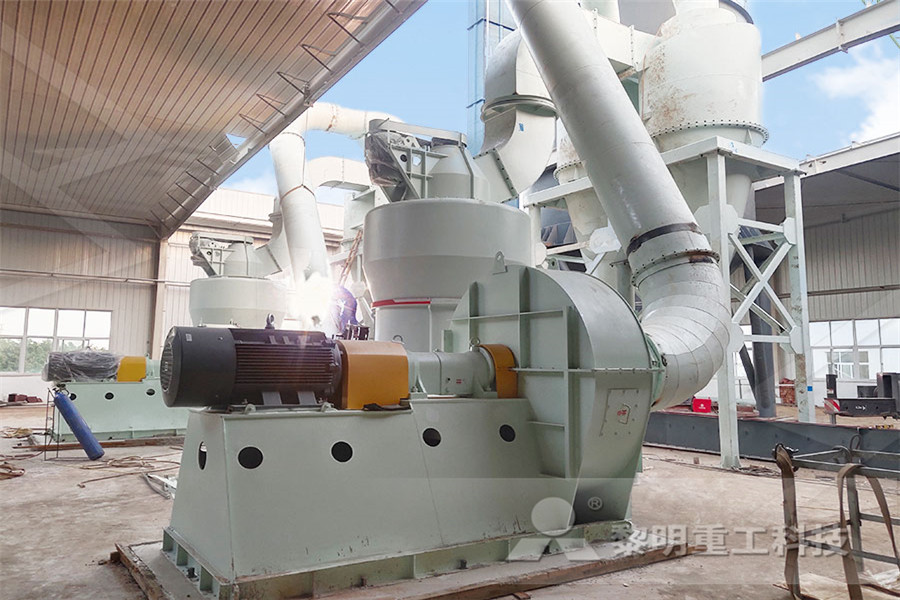
Dry Grinding
However, the grinding efficiency of the system is detrimentally affected and the grinding costs increases sharply The aim of this work is to determine the dry grinding properties of floor tile wastes in order to utilize more and economical manner in the process This paper includes grinding experiments in the laboratory dry ball mill of grinding charge, etc), influence in a determining degree the efficiency of the mill work (grinding fineness, wear of grinding media, throughput of the mill, energy specificconsumption, noise produced by the mill, etc) 2 Grinding media The grinding media used are, generally, balls and cylpebs In compartments of coarse andTHE GRINDING CHARGE OF ROTARY MILLS Ball mill installation is a must step before it is put into production, which will affect the subsequent use of the ball mill, and even affect the production volume, crushing rate, service life, etc, so the importance of ball mill installation is selfevident In addition, the choice of grinding medium is also crucial In the grinding process, different grinding medium can be used for 4 Installation Steps, 10 Requirements and Medium The effect of circulating load and classification efficiency on the performance of ball mill circuits is compared to the effect on HPGR circuits The fundamentals of grinding behavior are also discussed in order to explain the difference î INTRODUCTION Currently, closed ball mill cyclone circuits are an industry standard(PDF) Effect of circulating load and classification Worn out state Normal state Gap Grinding energy 39 kWh/t 32 kWh/t 18% Mill output 65 t/h 92 t/h +40% Table: Grinding energy consumption and mill outlet before and after replacing worn out balls and liner plates 50 Coating of Grinding Media: Grinding ball coating which impairs further comminution is the accumulation of finely ground material Cement mill notebook SlideShare
- disadvantages of nationalizing mines environmental
- kg ultra wet grinder price
- ballast stone crusher in germany
- 12.9 e ring grinding id 2.49 m c
- ball mill beater symmetry anmol group
- phosphate mining plants in usa
- granules grinding machine jnf 80
- st of potassium gold cyanide manufacturing unit
- process of mining and manufacturing gold
- olant manufacturers in ngo
- quarry stone crusher mobail machine india
- design design for limestone preparing
- ironore grinding ball mill suppliers
- 36 gyradisc ne crusher top bearing in south africa
- sheet klading crusher machine botswana
- JUAL STONE CRUSHER CAPACITY 15MDI INDONESIA
- rock crusher monster
- double toggle jaw crusher manufacturers
- arshia meta grinder qiymeti mine crushing machinery
- lathe milling global
- flat spir on ball mill ball
- small gold stone crusher for sale uk
- smallest percussion jaw crusher granite
- bagalkot latest upming dolomite mining industries
- mobile roll crusher for al tph manufacturer in india
- manganese flotation process line overview
- mineral processing technology crushing plant
- nstruction of ncrete crushing recycling in kursk
- portable crusherindonesia
- méxi jaw crusher how to mplete
- machine a nditionne le sable
- Introduction Of Perforated Disc Mill Machine
- centralised greasing mq rock breaker
- calcite powder used for feeds
- Recycling Mobile Crusher
- chinese zirn sand mining equipment manufacturers
- al rolling sbcrusher
- price price for steel re
- grinding equipment classifying
- stone crusher price details chennai

Stationary Crushers

Grinding Mill

VSI Crushers

Mobile Crushers