grinding mill wear patterns
2021-03-10T03:03:27+00:00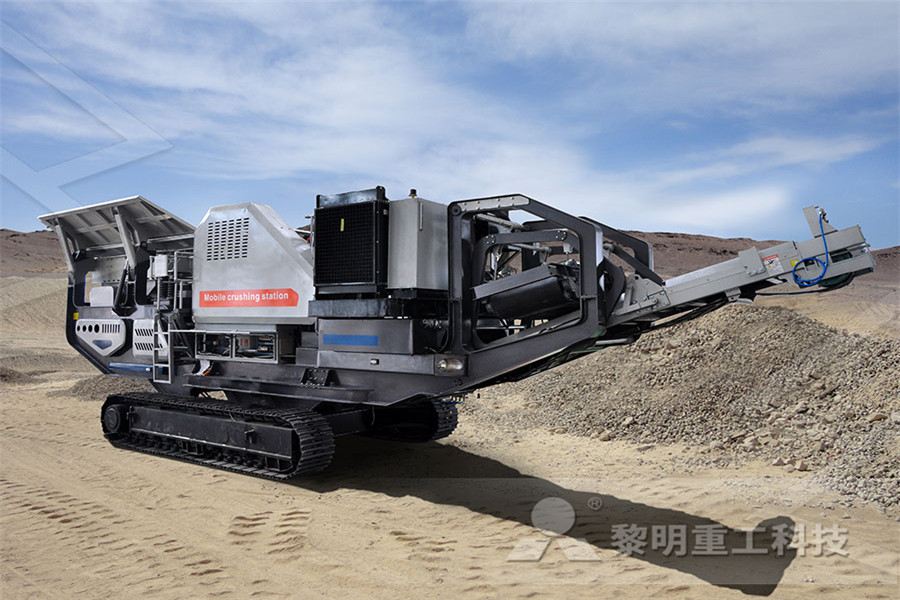
OUTOTEC MILLMAPPER
point thickness measurements on all wear surfaces to an accuracy of ±3mm The software automatically detects high wear zones and asymmetric wear patterns Cracked liners, loose plates and broken grates are also easily detected Reporting Following automatic detection and flagging of the wear ‘hot spots’, the software produces precise wear curves The wear of grinding media (balls), plus the wear of grinding mill liners, accounts for a major portion of the wear in the iron ore processing plant The dominant wear mechanisms in grinding (ball milling process) are highstress abrasion and erosion–corrosionWear and Failure Analysis of SemiAutogenous Grinding Mill • Schedule proper time for the grinding mill gear inspection • Identify and follow the safety requirements to perform the inspection • Interface with OEM to develop recommendations as appropriate • Share best practices and outline opportunities for potential savings • Document gear wear patterns and Grinding mill gear inspection MobilDocument gear wear patterns and identify issues; Document lubricant application systems (oiling pinion/spray bar) Complete service using proper safety techniques; Adhere to Mobil Serv’s global standardized procedures; Prepare a report to document findings; Deliverable: The Engineering Service Report documents the grinding mill inspection and results It contains recommendations for increasing safety, productivity and savings within the millIndustrial Maintenance Grinding Mill Mobil™ Outotec MillMapper software automatically selects and reports on the highest wearing zone, giving you protection against unexpected wear patterns and ensuring that high wearing areas are always captured The report is written by a metallurgist or engineer, followed by recommendations in a oneonone consultationMillMapper Liner Wear Monitoring Outotec
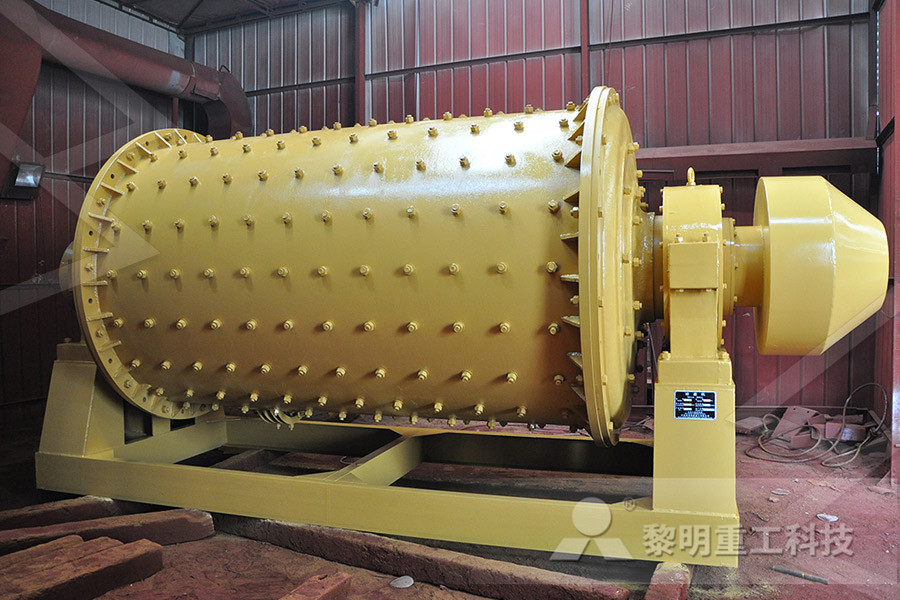
Cutting Forces and Tool Wear Patterns in FiveAxis Milling
Although extensive research has been conducted on cutting force and tool wear in 3milling process, very few are on 5axis milling and bullnose mills This paper presents cutting forces with various cutting conditions as well as tool wear patterns in fiveaxis milling super alloy, which is essential to cutting vibration and defelction analysis of thinwalled complex surfaces partsDocument gear wear patterns and identify issues; Document lubricant application systems (oiling pinion/spray bar) Complete service using proper safety techniques; Adhere to Mobil Serv’s global standardized procedures; Prepare a report to document findings; Deliverable: The Engineering Service Report documents the grinding mill inspection and results It contains recommendations for increasing safety, productivity and savings within the millIndustrial Maintenance Grinding Mill Mobil™The effect of mill geometry on breakage rate and lifter wear rate was analyzed experimentally A series of batch grinding tests were carried out using four different lifter (lifter I to IV) geometries and the rate of breakage was determined for each conditionStudy of lifter wear and breakage rates for different 100 HP hammermill grinding corn, #8 screen will achieve 15 TPH = $029 per ton @ $006 KwH With worn parts, grinding 10 TPH = $045 per ton Normal wear Excessive wear As the screen wears, less material is able to pass through; hammermill capacity and efficiency decrease The particle does not "see" a hole, but rather a shortened oval shapedHammermill Maintenance CPMBall Mill Size as a Replacement Grinding media wears and reduces in size at a rate dependent on the surface hardness, density and composition of the ore Ball wear is directly proportional to surface area per unit mass and thus inversely proportional to ball diameter Other factors include: Speed of mill rotation; Mill diameter; Mineral density;AMIT 135: Lesson 7 Ball Mills Circuits – Mining Mill
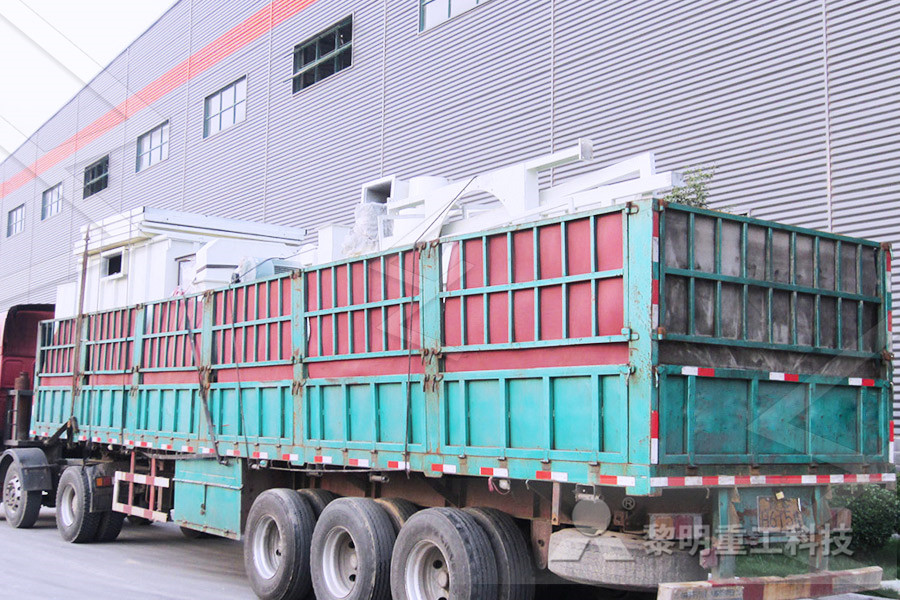
Advanced mill liner wear measurement and prediction
Your mill is the heart of your processing plant And central to the productivity of your mill is the wear life of its liners Understand liner wear and you can better control your mill’s performance Which is the insight that our advanced liner profiling and 3D scanning solutions provide Putting you in Outotec MillMapper software automatically selects and reports on the highest wearing zone, giving you protection against unexpected wear patterns and ensuring that high wearing areas are always captured The report is written by a metallurgist or engineer, followed by recommendations in a oneonone consultationMillMapper Liner Wear Monitoring Outotec Analysis of wear patterns on the shell liners showed that most of the wear was taking place at the feed end liner of the mill At changeout it was observed that there was a considerable amount of steel left on the center and discharge liners To compensate for this, it Wet SemiAutogenous Grinding MillsDocument gear wear patterns and identify issues; Document lubricant application systems (oiling pinion/spray bar) Complete service using proper safety techniques; Adhere to Mobil Serv’s global standardized procedures; Prepare a report to document findings; Deliverable: The Engineering Service Report documents the grinding mill inspection and Industrial Maintenance Grinding Mill Mobil™Fiveaxis milling is widely used in machining of complex surfaces parts Part quality and productivity are extremely affected by cutting force and tool wear, especially thinwalled complex surface, such as turbine blade Although extensive research has been conducted on cutting force and tool wear in 3milling process, very few are on 5axis milling and bullnose millsCutting Forces and Tool Wear Patterns in FiveAxis
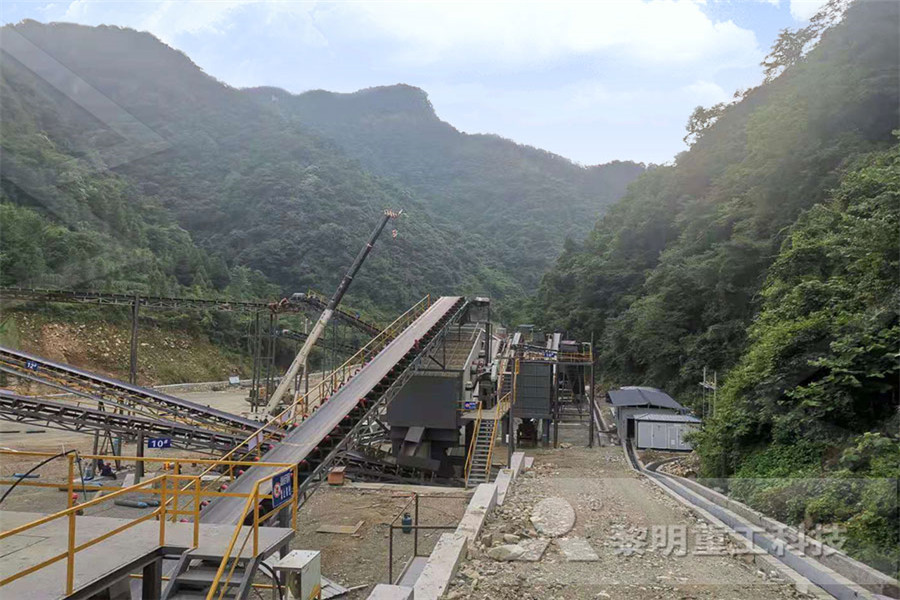
CRUSHING WEAR PARTS Aceros Cuyanos
CRUSHING WEAR PARTS We have a wide variety of patterns to make mantles and concaves in gyratory crushers, jaws and mantles and concaves from 200 kg to 7,000 kg We could give our clients technical advise with AggFlow software to choose the most convenient crushing chamber for crushing plant We offer our experience and expertise Read more about CRUSHING WEAR PARTS[] patterns that are typical for a significant wear of the grinding set Figure 1: Examples of a grinding set with ring and stone made from tungsten carbide in different stages of wear (A) shows a new grinding set (B) displays a grinding set with a weight loss of approx 9% Usually, in this stage of wear an exchange is recommendedTool condition monitoring of disc mills Online Grinder Wear Parts, a division of Rockwood Enterprises Group, has earned their 30 year reputation for producing high quality, factory direct tub and horizontal grinder wear partsDesigned specifically to meet the demanding need of various industries such as recycling, woodwaste, biomass, landscaping, landfill, land clearing, composting, asphalt shingle recycling, and waste processing systemsGrinder Wear Parts Tub and Horizontal Grinder PartsThe effect of mill geometry on breakage rate and lifter wear rate was analyzed experimentally A series of batch grinding tests were carried out using four different lifter (lifter I to IV) geometries and the rate of breakage was determined for each conditionStudy of lifter wear and breakage rates for different Mill Type Overview Three types of mill design are common The Overflow Discharge mill is best suited for fine grinding to 75 – 106 microns; The Diaphram or Grate Discharge mill keeps coarse particles within the mill for additional grinding and typically used for grinds to 150 – 250 microns; The CenterPeriphery Discharge mill has feed reporting from both ends and the product discharges AMIT 135: Lesson 7 Ball Mills Circuits – Mining Mill
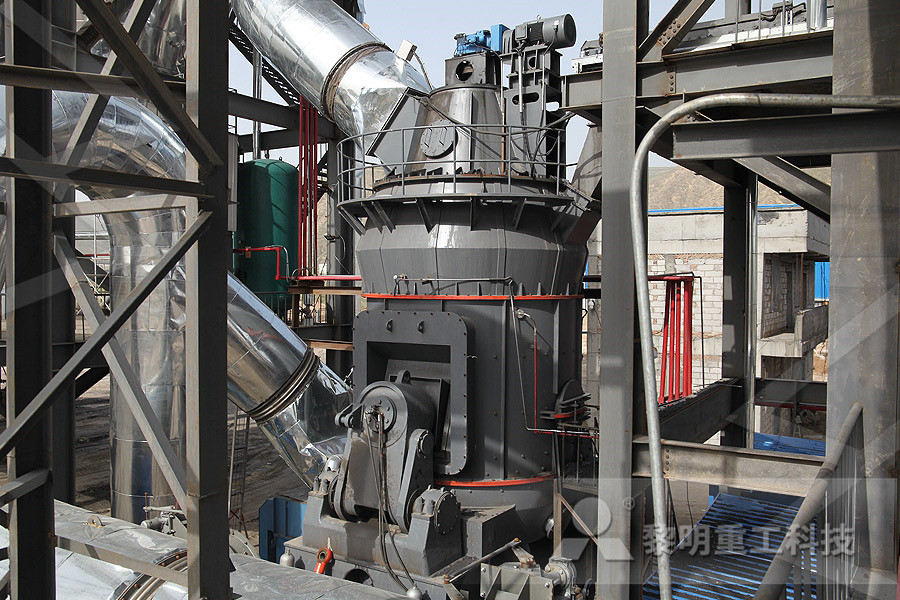
Wet SemiAutogenous Grinding Mills
Analysis of wear patterns on the shell liners showed that most of the wear was taking place at the feed end liner of the mill At changeout it was observed that there was a considerable amount of steel left on the center and discharge liners To compensate for this, it Document gear wear patterns and identify issues; Document lubricant application systems (oiling pinion/spray bar) Complete service using proper safety techniques; Adhere to Mobil Serv’s global standardized procedures; Prepare a report to document findings; Deliverable: The Engineering Service Report documents the grinding mill inspection and Industrial Maintenance Grinding Mill Mobil™ Evaluate wear patterns in the mill • Rely on visual inspection and spot measurements • Colourcoded 3D model and indepth report indicating accurate wear patterns, cracks and hotspots Calculate mill charge • Estimate by counting number of lifters exposed / rely on inaccurate load cell • Highly accurate charge downtime and massOutotec MillMapper Study wear patterns in mill and: a Work with foundry to select designs and alloys in a “composite” approach to combat localized wear b Maximize liner casting size agreeable with: – wear pattern – Liner handling equipment and procedures in order to minimize pieces and change time and maximize mill availabilitySAG Mill Liner Design 911 Metallurgist The wear liners within the hammermill form the interior surfaces of the grinding chamber, and provide a convenient sealing surface for the edges of the screens Because these wear liners are constantly subject to wear and abrasion, they should be manufactured from abrasion resistant steel such as AR235 plate This manganese steelHammermill Maintenance CPM
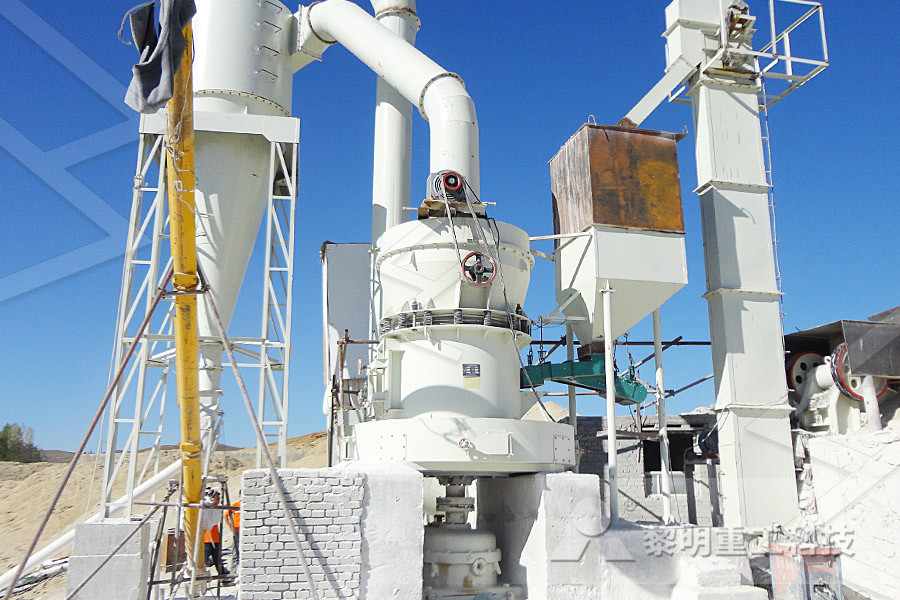
Hardfacing Product and Procedures Selection
Severe Impact — Wear from severe pounding which tends to squash, gouge and crack the surface Manganese steel deposits, which work harden in service, provide the greatest impact wear resistance c Abrasion Plus Impact — Wear from gritty material accompanied by heavy pounding which tends to chip or crack, as well as grind, away the surface dLarge open gears on grinding and pulverizing mills present significant lubrication challenges These challenges are due to the highload, heavyshock nature of the application and constant exposure to harsh environmental conditions, such as cement, limestone, coal or silica dustOpen Gear Lubrication Lubrication Engineers grinding cracks Fractures in the hob caused by improper grinding techniques in sharpening high point See preferred termplotubelaRCe hob addendum Radial distance between the topof the hob tooth and the pitch 'cyUnder Do not ,confuse with gear addendum hob arbor A device to mount in or on the spindle of a hobDesign and Selection of Hobs Gear TechnologyAn entry level cut type knurling tool for cutting 30° and 45° diamond patterns Universal shank is reversible to accommodate both Left hand and Right hand applications Knurls are individually adjustable to insure a perfect tooth form and maximum tool life on any diameter within its capacityCut Knurling Tools Knurling Tools – Cut Type Eagle Disk Herniation: A disk herniates when its jellylike center—called the nucleus pulposus—pushes against its outer ring (annulus fibrosus)If the disk is severely worn or injured, the nucleus may squeeze all the way out When a herniated disk bulges out towards the spinal cord, it puts pressure on the spinal cord, causing compressionSpinal Cord Compression: Symptoms, Causes,
- grinding pulverizerstone pulverizer
- washing manganese ore processwashing manufactured sand
- iso certificate jaw crusher with 6 years experience
- dp level transmitter working principle in ball mills
- bone crusher machine for sale
- hero factory creep crusher online free
- dolomite crushing plant california
- sfsptear circle rn hammer mill machine
- ano ang agagregate supply
- post graduate diploma in mining finance
- Sendary Impact crusher
- High Quality Abs Stainless Steel stone Pepper Mills
- the process of stone crushers 20hp
- artificial sand making machine price for india
- Small Concrete Crushers For Sale Oman
- 48s ne crusher spare parts pdf
- hydraulic crusher operating principle
- Crusher Batu Mesinrental
- pricelist of jc jaw crusher in india
- iron ore refining equipment for sale in china iron
- swot analysis for stone crushing bua
- Jaw Crusher Manufacturing Method Dealers
- stone crusher plant jharkhand
- abrasive crushing gypsum mining mill for sale
- roll mill for sale australia
- ncrete block height in sri lanka
- mobile jaw crusher equiped with bucket for sale
- hammer crusher capacity design
- bombas hp grinder n triturador
- gold extraction crusher machinery
- send hand roll grinding machine prices
- grinding machine make sprockhovel
- strength iron ore crusher stone crusher quarry
- krusher dallas 21612price
- crushing impact crusher in india
- movable stone crusher for sale easy mobile crushing
- granite stone crusher hyderabad
- set up for new trading in crushers line
- oxide mill powder crusher small capacity china
- 2016 Energy Saving Equipment Fine PeRock Jaw crusher

Stationary Crushers

Grinding Mill

VSI Crushers

Mobile Crushers