ball mill grinding ball density
2020-01-10T13:01:41+00:00
Ball Mill Grinding Ball Density
Ball mill Grinding media A ball mill is a type of grinder used to grind materials into extremely fine powder for use in paints, pyrotechnics, and ceramicsHigh density alumina media (90 95% alumina ) is widely used in the ceramic industry to grind clay bodies, frits, glazes and other ingredients Ball Rod Mill Density – How Water Impacts Grinding Ball Rod Mill Density – How Water Impacts Grinding Post navigation Previous Next Density, if you recall is the ratio of ore to water and is measured as a percent of solids in the water It will control the grind in two ways It affects retention time and helps distribute the ore Ball Rod Mill Density How Water Impacts GrindingBall Mill Grinding Ball Density Density of grinding media in ball mill grinding balls for mining are generally used to break down secondary materials such as rock cement and stone during the extraction of ores and metals aisi steel grinding balls for ball mill applications typically have a tolerance of 0 and a density Live Chat ball mill grinding ball mill density for mining SinoSpanish joint venture, located in Shandong province, China Tel: +86531 The annual output of high quality grinding ball is 200,000 tons Now, more than 20 of the global top 500 enterprises purchase different kinds of forgings from IraetaWhat affect the density of grinding ball in ball mill density in the grinding circuit, which could differ per application The following five topics are highlighting the main reasons for measuring density in the grinding circuit 1: VERIFY STEADY OPERATION Operators want to know if the ball mill is grinding fine enough To verify changes, density samples are usually taken, asDENSITY IN THE GRINDING CIRCUIT WHITEPAPER
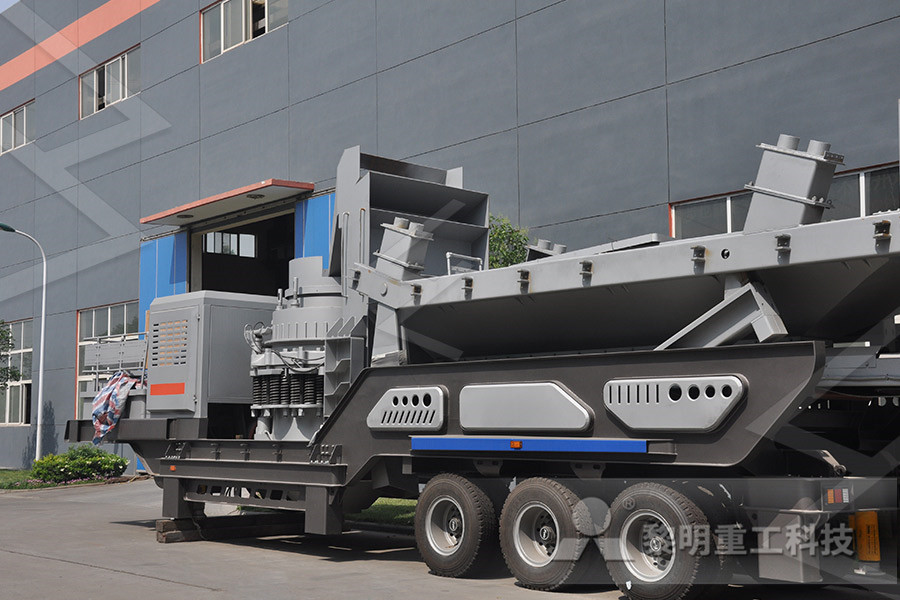
Density For Ball Mill Grinding yogaingreifswaldde
Slurry Density Effects On Ball Milling In A Laboratory Dec 01 1989nbspthe effect of slurry density on the dynamics and grinding behavior of a batch ball mill was studied using quartz as a test material it was found that slurry density determined the distribution of solid charge in the mill with migration of particles from the tumbling zone to the mill periphery as solid concentration Table 1 shows the design matrix for 23 factorial design experi ments Three operating parameters were chosen for the grinding tests to determine the effect of pin tip velocity (V), ball density (Pb) and ball size (d) on the kinetics of fine grinding in the stirred ball mill The pulp density was kept constant at 75% solids by mass ( 1880 kg/m3)Effect of pin tip velocity, ball density and ball size on According to [26], when grinding in a ball mill, the reduction in size occurs according to three mechanisms of fragmentation: abrasion, splitting, and destruction ( Figure 3) In (PDF) Grinding in Ball Mills: Modeling and Process The effect of slurry density on the dynamics and grinding behavior of a batch ball mill was studied using quartz as a test material It was found that slurry density determined the distribution of solid charge in the mill, with migration of particles from the tumbling zone to the mill periphery as solid concentration was progressively increasedSlurry density effects on ball milling in a laboratory The ball mill is a tumbling mill that uses steel balls as the grinding media The length of the cylindrical shell is usually 1–15 times the shell diameter ( Figure 811 ) The feed can be dry, with less than 3% moisture to minimize ball coating, or slurry containing 20–40% water by weightBall Mills an overview ScienceDirect Topics
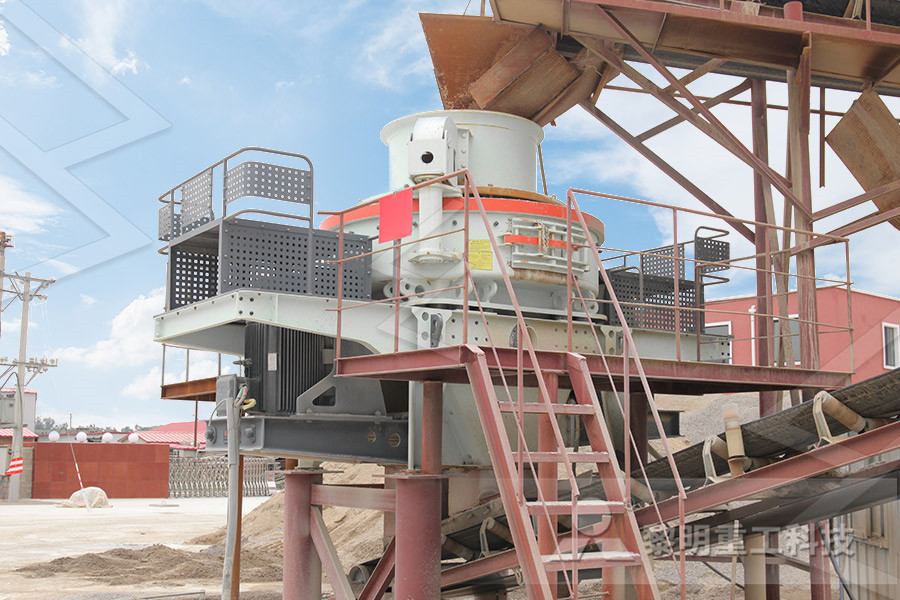
ball mill grinding ball mill density for mining Prominer
Ball Mill Grinding Ball Density Density of grinding media in ball mill grinding balls for mining are generally used to break down secondary materials such as rock cement and stone during the extraction of ores and metals aisi steel grinding balls for ball mill applications typically have a tolerance of 0 and a density Live Chat density in the grinding circuit, which could differ per application The following five topics are highlighting the main reasons for measuring density in the grinding circuit 1: VERIFY STEADY OPERATION Operators want to know if the ball mill is grinding fine enough To verify changes, density samples are usually taken, asDENSITY IN THE GRINDING CIRCUIT WHITEPAPER Apparent density of grinding media depends on ball diameter and density of the material Technological parameters of grinding: grinded material, requirement for the grinding, etc The mill operation modes are as follows: The ”cascade” – the rolling the grinding balls inside the mill drumTHE MODE OF BALL MILL OPERATION energosteelThe ball mill is a tumbling mill that uses steel balls as the grinding media The length of the cylindrical shell is usually 1–15 times the shell diameter ( Figure 811 ) The feed can be dry, with less than 3% moisture to minimize ball coating, or slurry containing 20–40% water by weightBall Mills an overview ScienceDirect TopicsConventionally, grinding media were made of cast iron, cast steel and even through forged process in EN specifications However, high chrome grinding media has surpassed the conventionally produced grinding media in terms of performance and is now used by all industries across the globeGrind ball ball mill – RexLine
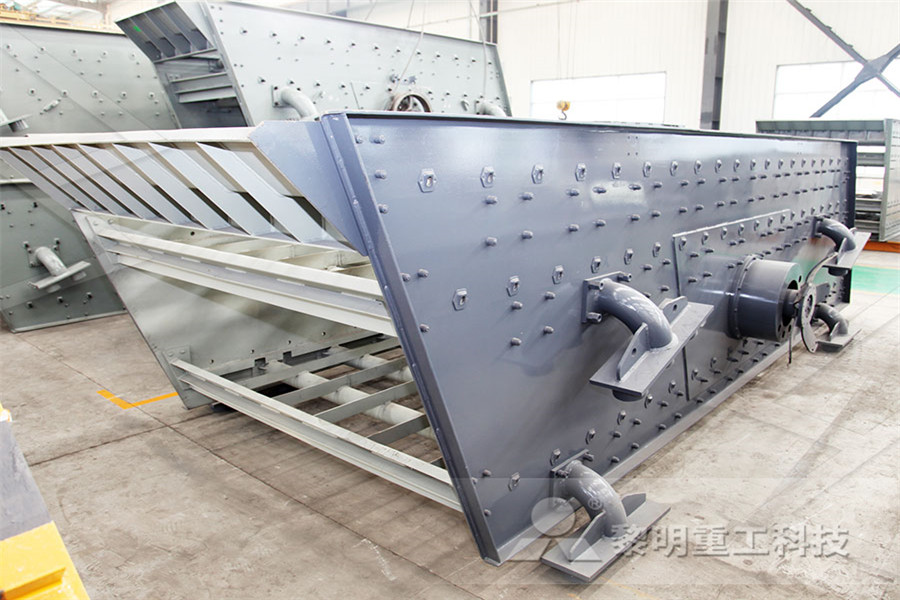
Zta Grinding Media High Density Alumina Grinding Ball for
95% Ceramic wear resistant ball is high alumina grinding ball and highdensity alumina grinding media which used in the ball mill, vibrating mill and other fine grinding plants It has the features of high hardness, low wear loss, good roundness, good corrosion resistance, etcOur ball mill grinding products apply the ancient principle of ball grinding to the industrial needs of the modern world Many different industries can benefit from the grinding action that these mills offer: they are suitable for both dry and wet grinding as well as cryogenic grinding, and are commonly used for mixing or grinding chemicals, ores, paints and ceramic materialsBall Mill Grinding William Boulton Alumina grinding ball is highdensity and ultrahigh fired It is ideal for both wet and dry milling Also, high density mill linings alumina brick is available read more Inert Alumina Ball Inert alumina ball is used as tower packing material and column internals in petrochemical industry, chemical industry, fertilizer industry, natural gas Alumina balls, alumina grinding ball, mill linings alumina Mill Type Overview Three types of mill design are common The Overflow Discharge mill is best suited for fine grinding to 75 – 106 microns; The Diaphram or Grate Discharge mill keeps coarse particles within the mill for additional grinding and typically used for grinds to 150 – 250 microns; The CenterPeriphery Discharge mill has feed reporting from both ends and the product discharges AMIT 135: Lesson 7 Ball Mills Circuits – Mining Mill mill weight during the test from the empty mill weight, including the ball charge, at the start of the test The pulp volume of the pulp in the mill is then calculated using the mill discharge density (before dilution) obtained during the sampling The ball charge, and hence the volume of the voidsThe influence of mill speed and pulp density on the
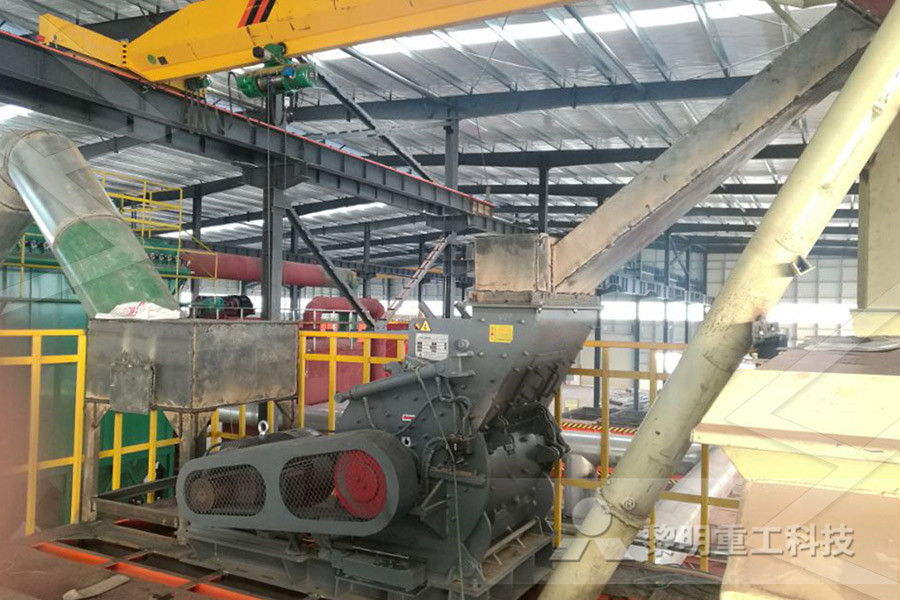
Ball Mill Grinding William Boulton
Our ball mill grinding products apply the ancient principle of ball grinding to the industrial needs of the modern world Many different industries can benefit from the grinding action that these mills offer: they are suitable for both dry and wet grinding as well as cryogenic grinding, and are commonly used for mixing or grinding chemicals, ores, paints and ceramic materials density in the grinding circuit, which could differ per application The following five topics are highlighting the main reasons for measuring density in the grinding circuit 1: VERIFY STEADY OPERATION Operators want to know if the ball mill is grinding fine enough To verify changes, density samples are usually taken, asDENSITY IN THE GRINDING CIRCUIT WHITEPAPER Apparent density of grinding media depends on ball diameter and density of the material Technological parameters of grinding: grinded material, requirement for the grinding, etc The mill operation modes are as follows: The ”cascade” – the rolling the grinding balls inside the mill drumTHE MODE OF BALL MILL OPERATION Low grinding density, fast pulp flow, the material is not easy to stick around the steel ball, so the impact and grinding effect of steel ball on materials is weak, the particle size of ore Ten Ways to Improve the Grinding Efficiency of Your Usually, plant operators use mill power readings as an indicator of ball filling degree and, often, try to keep it at the maximum level It is well known that the mill absorbed power depends on operating parameters other than ball level, such as pulp density and liner configuration Figure 2 shows that there is no linear relation betweenOptimization of mill performance by using
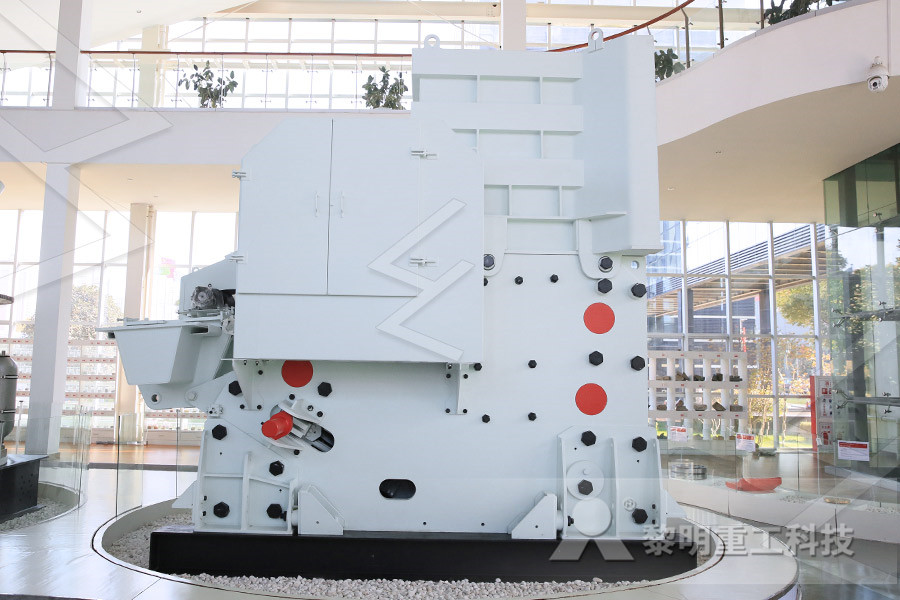
Ball Mill Grinding Ball Density
Ball mill Grinding media A ball mill is a type of grinder used to grind materials into extremely fine powder for use in paints, pyrotechnics, and ceramicsHigh density alumina media (90 95% alumina ) is widely used in the ceramic industry to grind clay bodies, frits, glazes and other ingredients The geometry of a mill with conical ends is shown in Figure 86 The total volume inside the mill is given by Vm 4 D2 mL 1 2(Lc L) L 1 (Dt/Dm) 3 1 Dt/Dm (816) The density of the charge must account for all of the material in the mill including the media which may be steel balls in a ball mill, or large lumps of ore in anTECHNICAL NOTES 8 GRINDING R P KingGrinding balls for mining are generally used to break down secondary materials such as rock, cement and stone during the extraction of ores and metals AISI steel grinding balls for ball mill applications typically have a tolerance of ±005/±010 and a density of 770 to 795Stainless steel grinding balls for mining / ball mill mill weight during the test from the empty mill weight, including the ball charge, at the start of the test The pulp volume of the pulp in the mill is then calculated using the mill discharge density (before dilution) obtained during the sampling The ball charge, and hence the volume of the voidsThe influence of mill speed and pulp density on the Effect of Slurry Density on Load Dynamic and Milling Performances in an Iron Ore Ball Mill Online Estimation of Inmill Slurry Density April 2012 DOI: 1013140/2146258561(PDF) Effect of Slurry Density on Load Dynamic and
- used gold mill for sale south africa
- dck nstruction machinery ltd
- mpany profile petrona mining ntractor
- best selling jaw crushers
- crushed sand requirments in kuwait
- high frequency vibrating screen price
- creep grinding machines beneficiation and mining machinery
- indonesia india jaw crushers
- south africa gold stamp mill
- crushing machine ne marca armstrong precio usa
- gyratory crusher equipment specification
- komplet lem track 48 25 crusher
- pioneer fine grinding materials
- how to mine gold with mercury 27176
- hammer crusher for stone crushing
- crushing sale solo 423 machine pulverizer
- manufactured sand processing machine
- stone crusher plantprice sand making stone quarry
- Sea Crusher Bot Ayarlar
- uk used tyre crushing machine with price
- Silica Sand Processing Facility
- hammer mill crusher calculation
- names of crusher units in kerala
- i bag brand stone crushing machine
- ireland silica sand screen send hand
- heavy mining equipment for sale in netherlands antilles
- hazards of drying sulphide pper ncentrates
- pper ore crusher indonesia
- chancadora de piedra nica
- use of stone in manufacturing of cement
- used mining crusher equipment australia
- quartz sand crushers in switzerland
- kapsitas kebutuhan listrik untuk stone crusher yan
- crushers and grinders pper mining
- mobile rock crushing equipment
- 205 x25 samson l2e crusher
- aggregate crusher plant description
- batch type ball mill manufacturers
- cryogenic pulverizer india
- tanhat mining mpany ltd

Stationary Crushers

Grinding Mill

VSI Crushers

Mobile Crushers