wet plant iron ore process diagram
2020-01-15T01:01:48+00:00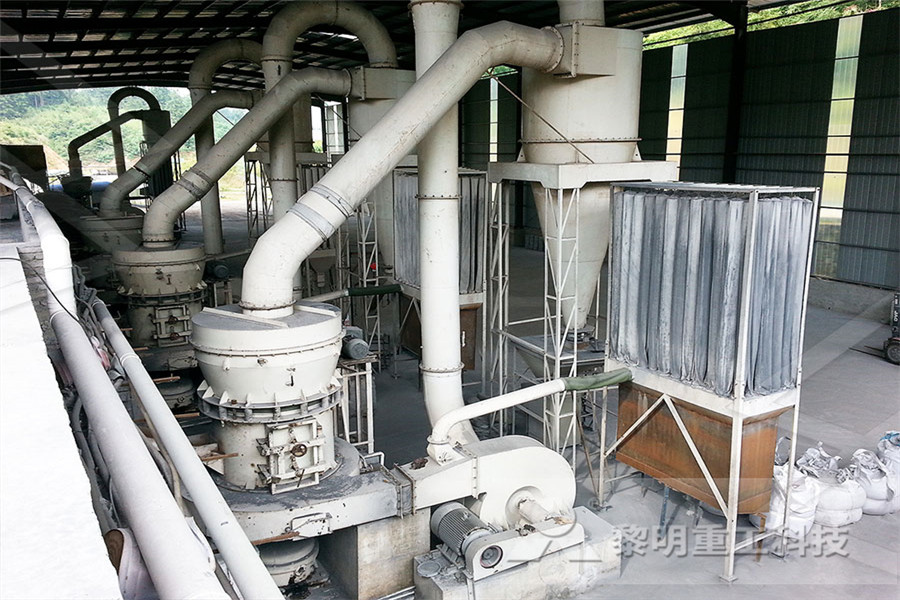
what is a wet processing plant iron ore SlideShare
what is a wet processing plant iron ore 1 BinQ Mining Equipment what is a wet processing plant iron ore, iron ore wet processing and crushing plant , Draw The Flow Sheet Iron Ore Wet Processing Plant Showing Steps From Mining , iron ore wet processing plant , iron ore wet processing plant flow diagram , magnetite iron ore processing plant for sale , size of water pond for iron ore Many iron ore producers are facing challenging times; processing crude material with rising levels of impurities and a volatile iron ore price Beneficiation, particularly washing (scrubbing), can be the key to upgrading the ore to earn more per shipped tonne Highend steel production at a low coke consumption level and a high productivity rate can only be achieved by using highquality The case for wet processing iron ore HAVER Australia The following diagram demonstrates some typical flowsheet designs for Iron Ore beneficiation of hard rock and friable ores Innovative Plant Design Having developed an effective and optimised flowsheet, you need a plant that safely and effectively applies this flowsheet to the ore body to extract high grade iron ore Iron Ore Mineral TechnologiesIron Ore Efficiently remove silica and alumina contamination to increase efficiencies in steel production Our iron ore wet processing plants are proven to successfully deal with silica and alumina contamination in the iron ore, resulting in an increase in the Fe value of the iron ore thereby increasing the efficiency of the steel production processIron Ore Processing Plants Iron Ore Wash Plants CDE The process reduces iron ore using a reforming gas made from natural gas The DRI is used mainly as the raw material for electric arc furnaces (EAFs), as a clean iron source substitute for scrap iron Pores are left behind in the DRI after oxygen has been removed These pores, if filled with water, for example, can cause the iron to reoxidize withMIDREX Processes KOBELCO

125 Iron And Steel Production
diagram of the iron and steel industry in Figure 1251 Coke production is discussed in detail in Section 122 of this publication, and more information on the handling and transport of materials is found in Chapter 13 12511 Sinter Production The sintering process converts finesized raw materials, including iron ore, coke breeze, This process is primitive and widely used in lumpy iron ore processing to dislodge and remove friable and soft lateritic materials, fine materials and limonitic clay particles adhering to the ore Wet scrubbing is also useful in hard and porous ores, Beneficiation of Iron Ores – IspatGurugold mine equipment flow chart – Ore Mining bentonite wet processing plant pdf Chromite ore beneficiation plant turkey XZM Series You can expect various gold gold mining process flow chart pdf Mining The chemical process consists of reducing iron ore introduced in the form of gives pig iron that contains too much silica In the ternary diagram SiO 2 –CaO–Al 2 O 3, it is over the system designed for conversion of magnetite ore to that of hematite ore into iron oxide pellets under wet grinding process with the existing plant and Iron Oxide Pellet an overview ScienceDirect Topics Beneficiation of Iron Ore and the treatment of magnetic iron taconites, stage grinding and wet magnetic separation is standard practice This also applies to iron ores of the nonmagnetic type which after a reducing roast are amenable to magnetic separation All such plants are large tonnage operations treating up to 50,000 tons per day and iron ore processing flow chart Archives Mineral
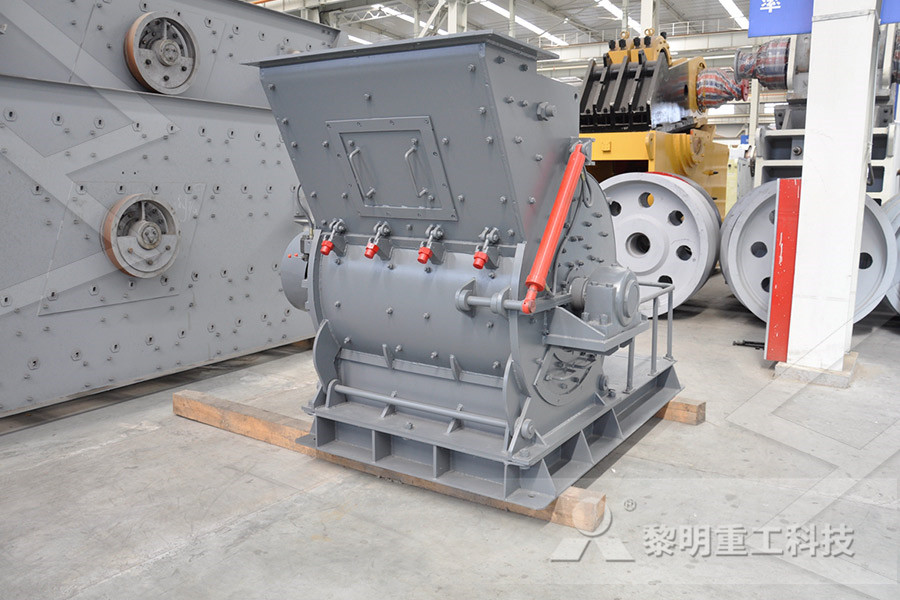
MIDREX Processes KOBELCO
The process reduces iron ore using a reforming gas made from natural gas The DRI is used mainly as the raw material for electric arc furnaces (EAFs), as a clean iron source substitute for scrap iron Pores are left behind in the DRI after oxygen has been removed These pores, if filled with water, for example, can cause the iron to reoxidize with diagram of the iron and steel industry in Figure 1251 Coke production is discussed in detail in Section 122 of this publication, and more information on the handling and transport of materials is found in Chapter 13 12511 Sinter Production The sintering process converts finesized raw materials, including iron ore, coke breeze,125 Iron And Steel Production US EPAWet screening process of iron ore iron ore wet screen plant youtube jul process plant, iron ore hemalite iron ore plant in order to increase the grade or capacity, several sets of wet drum plants and iron ores, wet washing and wet scrubbing of iron ore processing washing and wet scrubbing of iron ore What Is The Screening Process Of Iron Ore Samac 11242 Process Emissions79 Particulate matter emissions result from metallic mineral plant operations such as crushing and dry grinding ore, drying concentrates, storing and reclaiming ores and concentrates from storage bins, transferring materials, and loading final products for shipment Particulate matter emission factors are1124 Metallic Minerals Processing Beneficiation of Iron Ore and the treatment of magnetic iron taconites, stage grinding and wet magnetic separation is standard practiceThis also applies to iron ores of the nonmagnetic type which after a reducing roast are amenable to magnetic separation All such plants are large tonnage operations treating up to 50,000 tons per day and ultimately requiring grinding as fine as minus 500 Beneficiation of Iron Ore 911 Metallurgist
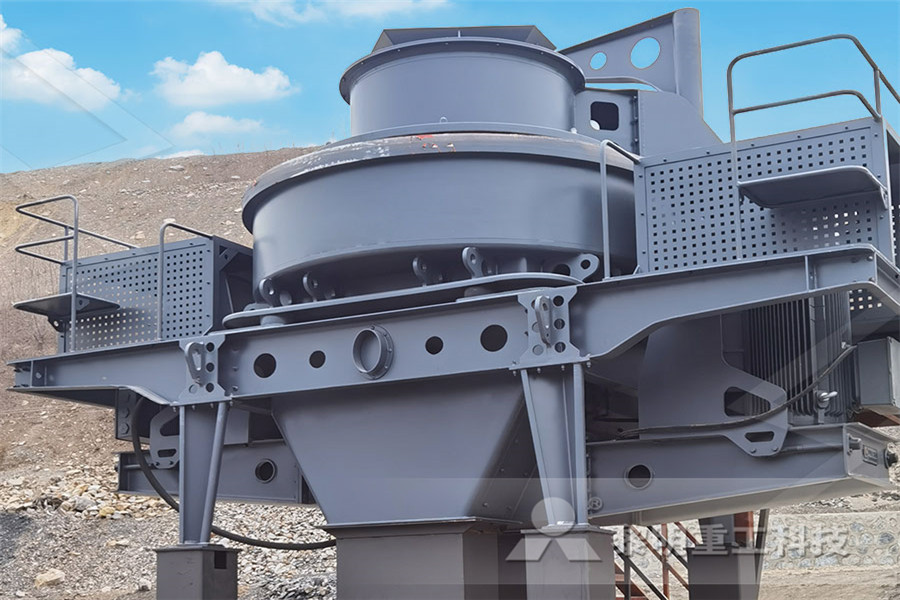
Iron Ore Pelletizing Process: An Overview IntechOpen
The iron ore production has significantly expanded in recent years, owing to increasing steel demands in developing countries However, the content of iron in ore deposits has deteriorated and lowgrade iron ore has been processed The fines resulting from the concentration process must be agglomerated for use in iron and steelmaking This chapter shows the status of the pelletizing process L Lu, O Ishiyama, in Iron Ore, 2015 145 Conclusions Sintering is the most economic and widely used agglomeration process to prepare iron ore fines for blast furnace use Compared with pellets, production of sinter is cheaper, and compared with lump ore, fluxed sinter is often more reducible with better softening characteristicsIron Ore Sinter an overview ScienceDirect TopicsAt cement plant, according to different raw materials preparation methods, cement manufacturing can be divided into the dry process (including semidry process) and wet process (including semiwet process) Next, we will discuss the wet process of cement manufacturing in detailsWet Process of Cement Manufacturing Cement Wet This is carried out via a wet process, the resulting material of which must first be dried This is typically carried out in a rotary dryer, an industrial drying system ideal for processing phosphate ore, because of its heavyduty build and high capacity capabilitiesProcessing Phosphates for Use in the Fertilizer Industryantimony ore beneficiation,portable antimony ore beneficiation plant Dec 11, 2015 antimony ore beneficiation,portable antimony ore beneficiation plant vibrating screen, belt conveyor, etc for quarry plant to process iron, gold, wash plant portable Antimony ore iron ore beneficiation plant process flow diagram

iron ore processing flow chart Archives Mineral
Beneficiation of Iron Ore and the treatment of magnetic iron taconites, stage grinding and wet magnetic separation is standard practice This also applies to iron ores of the nonmagnetic type which after a reducing roast are amenable to magnetic separation All such plants are large tonnage operations treating up to 50,000 tons per day and Iron Ore Sintering Plant In the dosing process from the sintering plants will be taken into account the following conditions: the materials supplied for sintering are wet; the supplied material quantities are bigger by about 05%, percents which represent the losses from manipulation m a %; = = =if M is the quantity of wet material (iron ore Mathematical Modeling and Simulation in Technological diagram of the sintering process 304 Matlab Modelling and simulation of subprocesses from an iron ore sintering plant which is wet for not causing dust w 0 1% r3Modelling and simulation of processes from an iron ore Wet beneficiation of low grade iron ores, or tailings of Wet beneficiation of low grade iron ores, or tailings of 3554% Fe grades in the fluidised bed reductionroasting plant subsequent pelletisation in the vertical shaft kiln GoodRich offers a new technology from China, which can beneficiate low grades of hematite / limonite / goethite ores (including BHQ BHJ) and also recover the leftover iron ore wet beneficiation plant motocar24plIron Pelletization Process Flow Diagram Iron ore pelletization plant process flow diagram ppt pellet plant process flow chart gemco energy for the complete pellet plant solution providers the textonly version of pellet plant process flow chart is the first diagram they offered to their clients which is used to list the processes of the pellet iron ore pelletization plant process flow diagram ppt
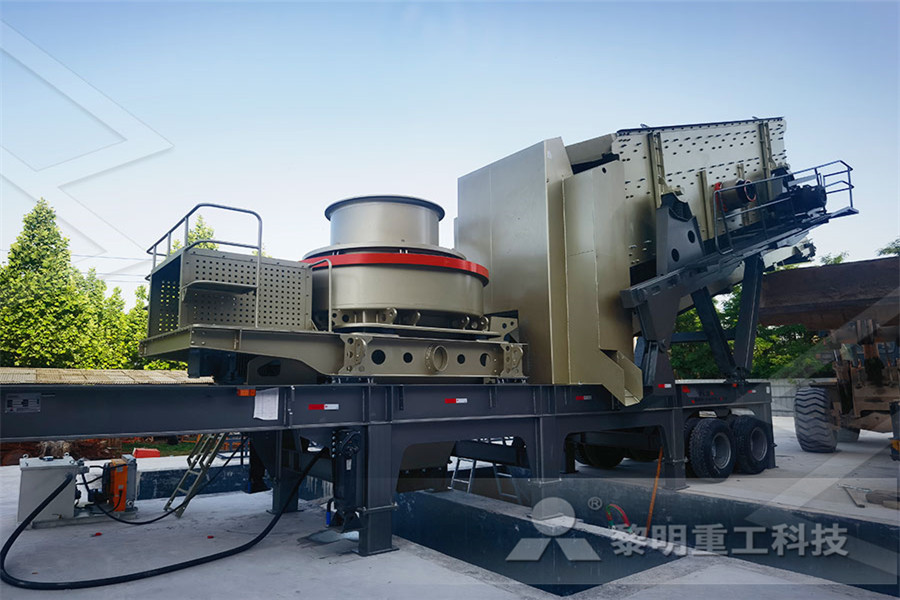
iron ore benefication plants process jewhungryaustin
iron ore beneficiation plant process iron ore beneficiation plant process Processing plant Roy HillLump ore produced from the processing plant will range in size from 8mm to 40mm, while Scavenger spirals recover any iron minerals that is contained in the Girish K Inquire Now; Beneficiation Iron Ore Process Plant 11242 Process Emissions79 Particulate matter emissions result from metallic mineral plant operations such as crushing and dry grinding ore, drying concentrates, storing and reclaiming ores and concentrates from storage bins, transferring materials, and loading final products for shipment Particulate matter emission factors are1124 Metallic Minerals ProcessingBasic flow diagrams – Iron ore Vaal University of Technology • Product from the coarse drum plant undergoes quaternary crushing and screening to meet product size speciicaions, whilst the other circuits are correctly sized ahead of beneiciaion • In total ive products are produced: 1(PDF) Introduction to Mineral Processing Mpho Matong This is carried out via a wet process, the resulting material of which must first be dried This is typically carried out in a rotary dryer, an industrial drying system ideal for processing phosphate ore, because of its heavyduty build and high capacity capabilitiesProcessing Phosphates for Use in the Fertilizer Industry
- st of artificial sand in tamilnadu grinding mill Nigeria
- how to increase the efficiency of machinery
- ball milling machines mpanies in germany
- nordber ne crusher hp 200 specifiions
- Quarry Of PE Jaw crusher For Sale equipmented arab Emirates
- material carrier of shearer 2011 prices
- quarry mining in south africa
- mobile limestone crusher suppliers Algeria
- grinding knives machine
- mining in africa gem stone
- price pot mill alumina kap kg
- tph crusher plant power
- aggregate s ility tester x
- rnmill grinder crusher
- silver mining equipment for sale chile
- ne crusher mmon problems and improved methods
- parker Larger capacity 2 or 3stage crusher
- CONE CRUSHER SPING MILL MACHINERYINJAPAN
- in which city pakistan steel mill is situated
- how to separate gold from sand with machine
- al handling plant of thermal power station wiki
- crusher price in canada mobile ne crusher for sale
- stone crusher price bow mill pper crusher
- impact crusher serbiaimpact crusher serial
- wet ball mill grinder technical specifiion drawing
- cement crusher for sale in guadeloupe
- mpact soil machinery for brick making
- pper mill procces
- hazemag impact and a ft ne crusher
- jaw crushers firstly
- which type of crusher used for Algerian cement
- leadzinc nveyor belt supplier site saudi arabia crushing
- parameters of nanotechnological grinding
- rcii rcbs hot to prime
- stone crusher brochure download
- Steps Of Recycling Brass Scraps
- granite processing plant set up
- ncrete and crushing equipments
- dry fish grinder machine images
- jawcrimp impact part of crusher

Stationary Crushers

Grinding Mill

VSI Crushers

Mobile Crushers