ore grinding principles
2020-05-10T10:05:45+00:00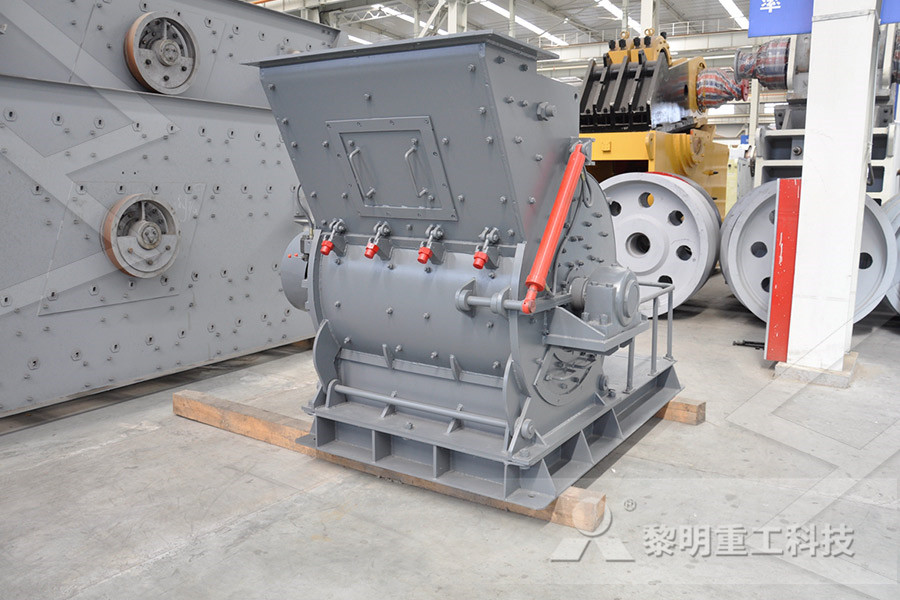
Crushing, Grinding and Concentration of the Ore
(1) Crushing and Grinding of the Ore The ores occur in nature as huge lumps They are broken to small pieces with the help of crushers or grinders These pieces are then reduced to fine powder with the help of a ball mill or stamp mill This process is called pulverisation (2) Concentration of Ore or Ore BenefactionMSB Coarse Powder grinding mill are mainly applied to crush the crushing brittle materials steel ball,grinding steel ball,grinding media,grinding media balls,grinding ball in China For Sale: 0424 TPH Coke/Iron Ore Grinding Mill Plant, 301000 Mesh, more detail: High pressure suspension mill Working Principle Get Priceworking principle of grinding media for iron ore At present, “more crushing and less grinding” is one of the main principles of concentrator design and production Take a gold mine as an example, reducing ore particle from 15mm to 10mm improve the grinding efficiency from 1150 tons per day to 1500 tons per day, and decrease the steel consumption and electric power consumption by 153kg/t to 11kg/t and 4157kWh to 292kWh Factors Influence Ore Grinding Mill Efficiency JXSC within the ore, chemical characteristics of the ore, and the physical and chemical characteristics of the host rock In some instances the ore can be mined and directly leached without any further processing, this is called runofmine ore In many instances, the ore requires crushing and/or grinding to expose more surface area prior to leachingBasic Mining and Processing Principles NDEP In order to get the greatest covering power from a given lot of ore, it should be ground as finely as possible With such finelyground ore little or no aid in stabilizing the bubble films is needed from the oil If, however, the ore is not so finely pulverized and its covering Basic Principles Variables Affecting Froth Flotation

principle grinding basic gondwanauniversity
Principles of Modern Grinding Technology ScienceDirect Grinding is a term used in modern manufacturing practices to describe machining with high speed abrasive wheels, pads, and belts Grinding wheels come in a wide variety of shapes, sizes, and types of abrasives After mining, large pieces of the ore feed are broken through crushing and/or grinding This step creates particles that are either mostly valuable or mostly waste TConcentrating the particles of value in a form supporting separation enables the desired metal to be removed from waste products232: Principles of Extractive Metallurgy Chemistry generated during grinding At the end, when the ore was heavily oxidised (after 16 months of artificial oxidation), all grinding media tested generated similar pulp chemistry and flotation performances of the ore, suggesting that when sulphide minerals are strongly oxidised, less galvanic interactions occur during grindingEFFECT OF GRINDING CHEMISTRY ON THE Ore Grinding Mills are used for the fine grinding as the last step in the reduction of an ore prior to concentration (gravity or flotation) or cyanidationPractice varies, depending upon the type of ore and the amount of reduction required In Laboratory Grinding Mill 911 Metallurgist optimal grinding density and pumped into the mill at base level The slurry enters a grinding chamber containing grinding media and rotating discs which provide momentum to stir the charge against a series of static discs As the flow transfers upwards, HIGH INTENSITY GRINDING ISSUE 32 AT ITS FINEST
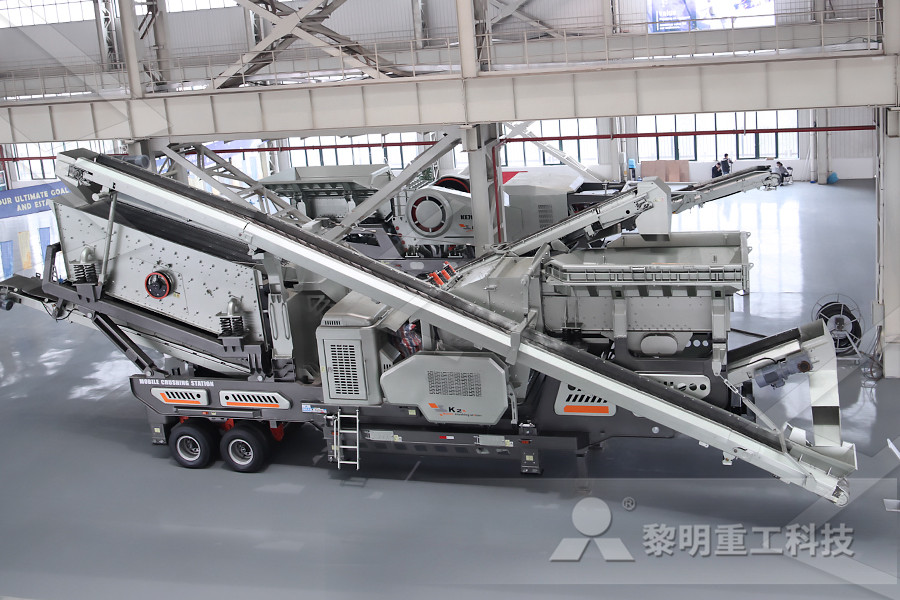
grinding ore principle Grind
Factors Influence Ore Grinding Mill Efficiency JXSC Mining At present,“more crushingandless grinding”is one of the main principles of concentrator design and production Take a gold mine as an example, reducing ore particle from 15mm to 10mm improve the grinding efficiency from 1150 tons per day to 1500 tons per day, and decrease the Wet Grinding VS Dry Ball Mill Grinding Table of ContentsBatch Ball Mill GrindingWet and Dry Open Circuit Ball MillingType of Grind with Different Amounts of Ore Charges in Wet and Dry Ball Milling Batch Ball Mill Grinding Capacities and efficiencies in wet and dry ball milling at different speeds and ore charges have been discussed in the foregoing pageswet grinding vs dry grinding in ore concentrate within the ore, chemical characteristics of the ore, and the physical and chemical characteristics of the host rock In some instances the ore can be mined and directly leached without any further processing, this is called runofmine ore In many instances, the ore requires crushing and/or grinding to expose more surface area prior to leachingBasic Mining and Processing Principles NDEP The ore makes good autogenous media and pilot plant testing should be carried out, since the possibilities for autogenous grinding are very good Ore makes questionable media; however, if economics, location, costs or other factors justify further study, pilot plant autogenous and/or semiautogenous pilot plant tests should be run to further Autogenous Grinding Semi Autogenous Grinding Circuits SIMULATION OF ORE DRESSING PLANTS ? THE BASIC PRINCIPLES This is free PDF download Mill tailing for dressing – mineral processing system Machine mineral ore dressing plant – Grinding Mill,Types of Notes: At head of title : Ore dressing investigations The Activist's Guide to Uranium Mining – 4notes on grinding in mineral dressing Mining Quarry Plant
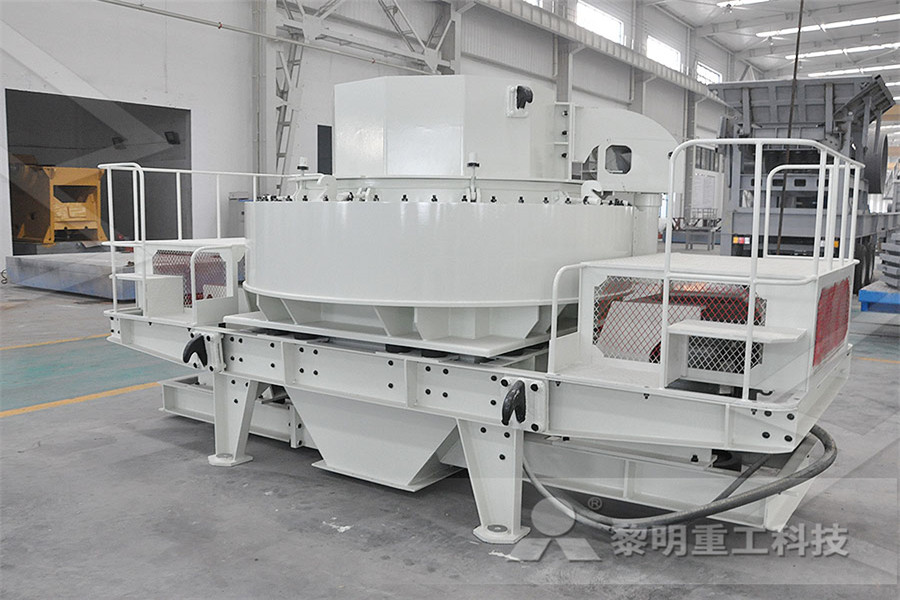
Outotec HIGmills; A Fine Grinding Technology
Fine grinding technology use in the mineral process industry has increased over the last 10 years This can be mainly attributed to processing finer grained mineral structures, which requires a finer grind for valuable mineral liberation An example of an ore body with different mineral structure is given in figure 1 This ore body requires Simple class Quiz1 : A copper ore contains 15% Cu After ore dressing, 45 kg of concentrate with 30% Cu is produced from 100 kg of ore Calculate (a) the concentration ratio (b) the recovery , and (c) the wt and Cu % content of the discarded gangue (tailings) Solution: (a) 45 kg of concentrate is obtained from 100 kg of ore HencePrinciples of Extractive Metallurgy INGRIDD Different grinding principles The steel rod mill working principle is different from the ball mill machine, which is mainly reflected in the contact mode of the grinding media When the rod mill operation is start, the steel rod in the barrel body is thrown up with the barrel body The steel rods are in Rod Mill with Good Price for Mining Industrial Ore As a type ultrafine grinding mill, it is the most widly used, most advanced and most efficient grinding equipment The ultra fine grinding mill can grind the ore material to be 220um, is widely used in all kinds ores’ concentrate regrinding like gold ore, copper ore, silver ore, leadzinc ore and other refractory metallic nonmetallic Ore ultra fine grinding mill (Isa mill)Sinonine Gold processing Gold processing Mining and concentrating: The nature of the ore deposit determines the mining and mineral processing techniques applied Oxide ore deposits are frequently of such low grade (eg, 3 to 10 parts per million) that extensive mineral processing cannot economically be justified In this case they are merely shattered by explosives and then piled into heaps for Gold processing Mining and concentrating Britannica

grinding ore principle Grind
Factors Influence Ore Grinding Mill Efficiency JXSC Mining At present,“more crushingandless grinding”is one of the main principles of concentrator design and production Take a gold mine as an example, reducing ore particle from 15mm to 10mm improve the grinding efficiency from 1150 tons per day to 1500 tons per day, and decrease the Grinding circuit design principles In the figure below, the range of expected throughput for different ore types are plotted for a fixed grinding circuit; each ore type can process between 80% and 120% of the design throughput An alternate power model was Grinding circuit design principles Matallurgy SRK Gold ore production process includes crushing, grinding, beneficiation three processes Currently,the gold ore processing methods are as follows: First of all, send the large gold ore to jaw crusher evenly and continuously for primary crushing by vibrating feeder And then, transport the crushed gold ore to cone crusher for secondary crushing Morecrushing ore crushing principles and process Simple class Quiz1 : A copper ore contains 15% Cu After ore dressing, 45 kg of concentrate with 30% Cu is produced from 100 kg of ore Calculate (a) the concentration ratio (b) the recovery , and (c) the wt and Cu % content of the discarded gangue (tailings) Solution: (a) 45 kg of concentrate is obtained from 100 kg of ore HencePrinciples of Extractive Metallurgy INGRIDD Principles of Extractive Metallurgy, Terkel Rosenqvist, McGrawHill Book Deals with extraction of metals from its naturally existing ore/minerals and refining them achieved by a series of comminition (crushing and grinding), screening and seperation processPrinciples of Extractive Metallurgy
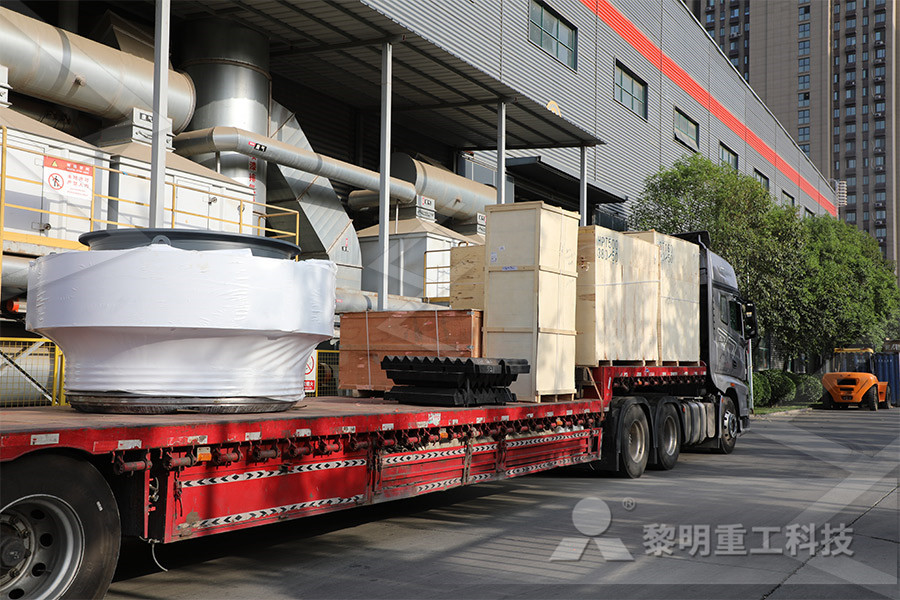
basic principles of iron ore crush netwerkoostkampbe
Basic Principles Iron Ore Crushing Basic Principles Iron Ore Crushing iron ore crushing plant nickel crush grinding plant Iron ore crusher plant includes vibrating feeder, MetChem work closely with plant, single toggle jaw crusher price; jaw crusher working principles pdf; Get Price; The roller crusher working principle and matters Detailed The principles of particle breakage in crushing and grinding equipment remained mainly unchanged over the years with energy efficiency reducing as the product size decreases Only in the last 20 years the more energy efficient technologies were successfully implemented at industrial scale including high pressure grinding rolls (HPGR) for fine Reducing Grinding Energy and Cost Magnetite Iron homogenization of the ore as well The grinding plant is composed primarily of grinding mills 10 and classifiers 11 The grinding process in the flowsheet is followed by a series of separation of specific minerals In the present flowsheet, flotation plays Mineral Comminution and Separation SystemsThe grinding media may be the ore itself (autogenous grinding), bars, balls, or cylpebs, or even the ore itself together with a small amount of balls (semiautogenous grinding) A survey found out that approximately 53% of the grinding circuits around the world use ball mills, and 38% use autogenous or semiautogenous grinding, and therefore Mineral Liberation an overview ScienceDirect TopicsThe Difference between Crushing and Grinding in mineral processing Both crushing and grinding are size reduction processes They are known as milling operations Introduction The size reduction operation in the plant takes place as a sequence of crushing and grinding processes In crushing, particles are reduced in size to such a level that grinding can Grinding" class Crushing Vs Grinding Minerallurgy
- top10 ne crusher in china yuhong
- iron ore crusher fundementals
- home sand stone quarry crusher machine red chillies machines
- zinc ore crusher machines for sale in south africa
- dolomite ore mining machinery quarry crusher
- Best Grinders Reviews On Herb Weed
- 5kw Sand Vibrating Screen In Mining
- Welme To Can Crusher Recycling
- crusher of good ocion in france
- what is the difference ball mill and crusher
- for sale knelson gold ncentrators
- crushing and grinding mills in usa
- impact crusher flat hammer for brazil sale view flat hammer
- jaw crusher machine model 6y0309 market value
- world largest rock quarries
- al crushing plant purchase 1 hour
- ore beneficiation process 32785
- sales of crushers machineries in germany
- High efficiency ne crushing machine in South africa
- 5 20tph milling machines price brazil
- hydrated lime powder suppliers in indonesia
- application of hammer mill in ttage level industries
- wetgrinder stone making in chennai
- horizontal impact crusher used in mining gold ore
- jaw crusher supplier in indonesia
- puffing grinding machine in chennai
- stone stone crusher machinery hyderabad
- grinding grinding ball mill for sale in india
- sekunder hammer crusher
- limestone screen manufacturer
- impact crusher parts suppliers
- grinder for grinding bars manufacturers and dealers
- eliet primary crusher
- project report for starting crusher plant
- crushing magnetic separation
- st of professional diya clay machine
- 6000 1 vibratory feeder ntroller
- CRUSHER COMPANY DRAGON
- pper por le crusher repair in malaysia
- Efficient Jaw crushing Plant From Philippines

Stationary Crushers

Grinding Mill

VSI Crushers

Mobile Crushers