on site ball mill journal china machining
2020-12-27T05:12:36+00:00
A Prediction Model of Cutting Force about Ball End
Cutting force prediction is very important to optimize machining parameters and monitor machining state In order to predict cutting force of sculptured surface machining with ball end mill accurately, tool posture, cutting edge, contact state between cutter, and workpiece are studied Firstly, an instantaneous motion model of ball end mill for sculptured surface is established 12 The Open Mechanical Engineering Journal, 2012, 6, 1217 1874155X/12 2012 Bentham Open Open Access A Manufacturing Model for BallEnd Mill Gashing Based on a CAM System Fei Tang*,1, Min Jin1, Xiaofeng Yue2, Zhanhua You2, Shuzhe Li1 and Xiaohao Wang1 1State Key Laboratory of Precision Measurement Technology and Instruments, Department of Precision InstrumentsOpen Access A Manufacturing Model for BallEnd Mill (Marketing Presenter 013yellow20jpg) Hydratight’s OnSite, InSitu Machining Services offer increased plant uptime and safety, while cutting assembly, dismantling and transport costs for refurbishment and maintenance of equipment and OnSite Machining Services English Hydratight On The Cutting Edge Our company boasts some of the most experienced and technicallyadvanced machinists in the industry Using our stateoftheart machining equipment, we aim to complete every project safely, on time, and with unparalleled On Site Machining In Place Machining Cutting Edge As shown in Fig 3a, the small holes are machined by ultrasonicassisted electrochemical drillgrinding set up While the ballend electrode rotates continuously, it is accompanied by downward feeding and periodic vibration It can be seen that the ballend electrode is equipped with diamond abrasive particles, which are added to the ballend by electrodeposition as shown in Fig 2bUltrasonicassisted electrochemical drillgrinding of
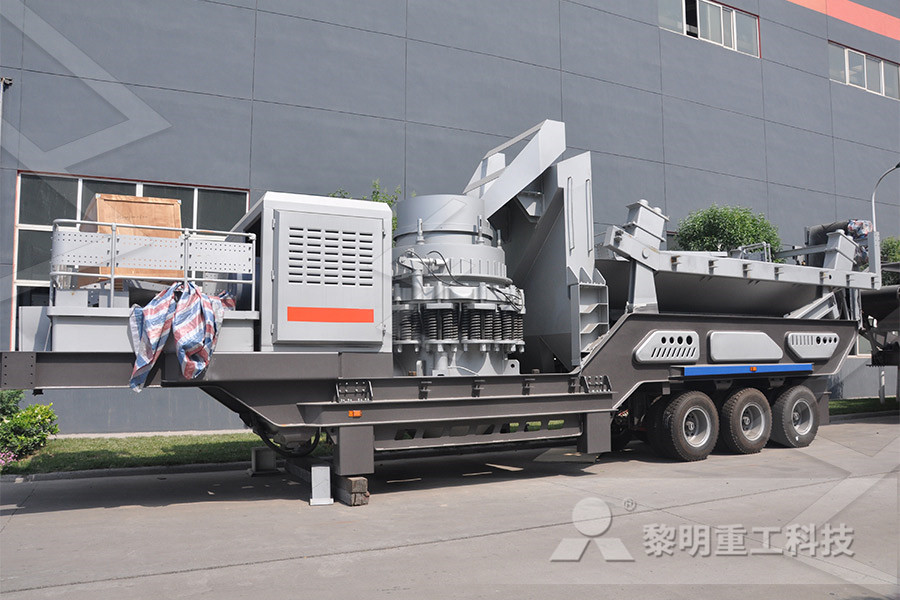
Effect of ball milling time on physicochemical
Cordyceps militaris powder with different particle sizes, a fungus rich in cordycepin and carotenoids, has different physicochemical properties To explore the influence of different ball milling time on the properties, a batch ball‐mill was used before high energy nano‐impact mill to produce ultrafine particles from Cordyceps militaris The particle formation kinetics was covering 2 to 16 CLIMAX is the leading global manufacturer of portable machining, welding, and valve testing equipment, bringing the machine shop to the job site CLIMAX invented this industry 53 years ago – Since then we’ve grown to become a global company that provides a wide variety of portable machining, welding, and valve testing repair tools Home Climax PortableThe machining area at the point of the surface generation is changed depend on the tool orientation of the ball end mill The geometric mechanism is analyzed and the relationship between the machining area and the tool orientation is clarifiedA proposition for machining error estimation based CLIMAX pioneered portable machining and we are ready to help you achieve your economic goals and improve the performance of your onsite machining, welding, and valve testing projects We are committed to delivering outrageously good Products Climax Portable MACHINING OPERATIONS AND MACHINE TOOLS 1 Turning and Related Operations 2 Drilling and Related Operations 3 Milling 4 Machining Turning Centers 5 Other Machining Operations 6 Shape, Tolerance and Surface Finish 7 Machinability • Bedtype Mill • MACHINING OPERATIONS AND MACHINE TOOLS

Milling force prediction model for fiveaxis machining of
In this paper, the milling force prediction model for fiveaxis machining of freeform surface with ballend mill considering mesoscopic size effect is established Based on the characteristics of cutting thickness in macromilling, a new dislocation density correction form is proposed, and a new experiment is designed to identify dislocation Journal of Mechanical Engineering • Proceedings of the 16th International Manufacturing Conference in China, 20151: 355360 Fang Zeping, Wang Xibin, Liu Zhibing A micro ball end Mill and its manufacturing method, China Invention Patent, CN school of mechanical engineering beijing institute of Quintana and Ciurana 4 already examined the research status for chatter in cutting processes, and also classified methods used to ensure that there is no chatter Siddhpura and Paurobally 5 similarly looked at the research status of chatter in turning processes, and discussed the theoretical relationship between chatter and tool wear Munoa et al 2 presented a critical review of different A review of chatter vibration research in milling This paper presents an approach for prediction of cutting forces in threeaxis ballend milling of a sculptured surface along an arbitrary tool path The idea of differentiation is adopted to deal with the problems of varying feed direction, varying cutter engagement, and the consequent varying cutting forces in sculptured surface machining Based on the differential idea, the whole process of Prediction of cutting force in ballend milling of It is absolutely necessary to machine the complex mould cavity with microball end mill in high speed machining Because of the priceless and frangibility of the tool, it is significant to predict the cutting force in order to lessen the tool’s disrepair, to ensure the quality and to improve efficiencyCutting Force Prediction of HighSpeed Milling Hardened
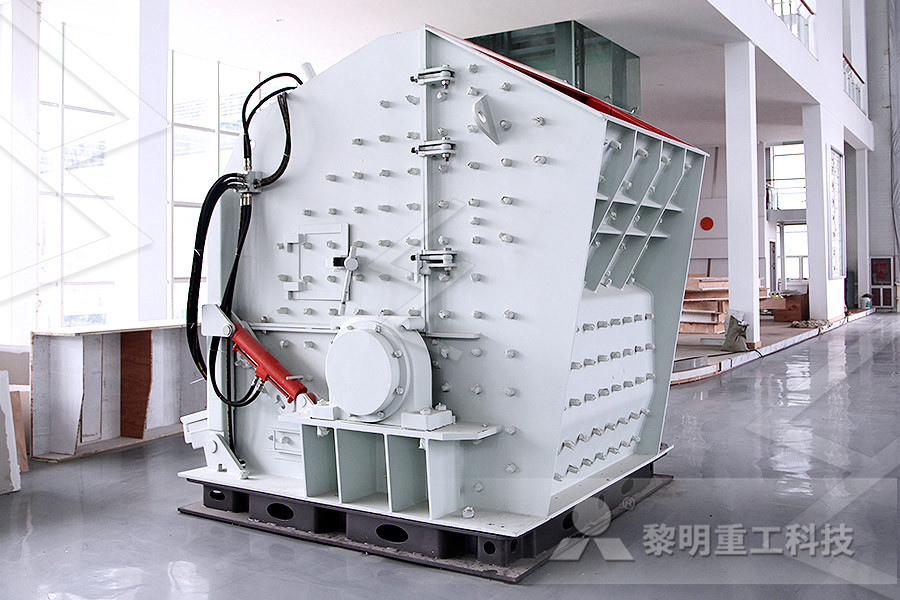
63 questions with answers in MILLING (MACHINING)
In a ball mill virtually all the energy is converted into heat, light, and noise and very little into comminution Take a look at: August 3rd 2010 Comminution history and laws CLIMAX is the leading global manufacturer of portable machining, welding, and valve testing equipment, bringing the machine shop to the job site CLIMAX invented this industry 53 years ago – Since then we’ve grown to become a global company that provides a wide variety of portable machining, welding, and valve testing repair tools Home Climax PortableHelical groove geometry has important influence on the performance of end mills It is the hardest and most timeconsuming grinding process in end mill manufacture(PDF) Modeling and analysis of helical groove grinding in Geometric model of general end mill is shown in Fig 1, M z and N z divide the cutter into three parts: end edge zone, arc edge zone and side edge zone A describes the angle between side edge zone envelop surface and XYplane of the cutter coordinateB describes the angle between end edge zone envelop surface and cutter axis of the cutter coordinateR r describes the length between the cutter Parametric chip thickness model based cutting forces Molybdenum disulfide (MoS 2) as a twodimensional material and solid lubricant shows good friction properties in many applicationsThe study used the copper (Cu) and zinc (Zn) powder with doped MoS 2 powder to prepare the alloy material through the spark plasma sintering (SPS) technology The coefficient of friction (COF) and wear of alloys with different doped ratios (0 wt%, 3 wt%, 6 wt%, 9 Investigation on friction and wear behaviors of Cu–Zn
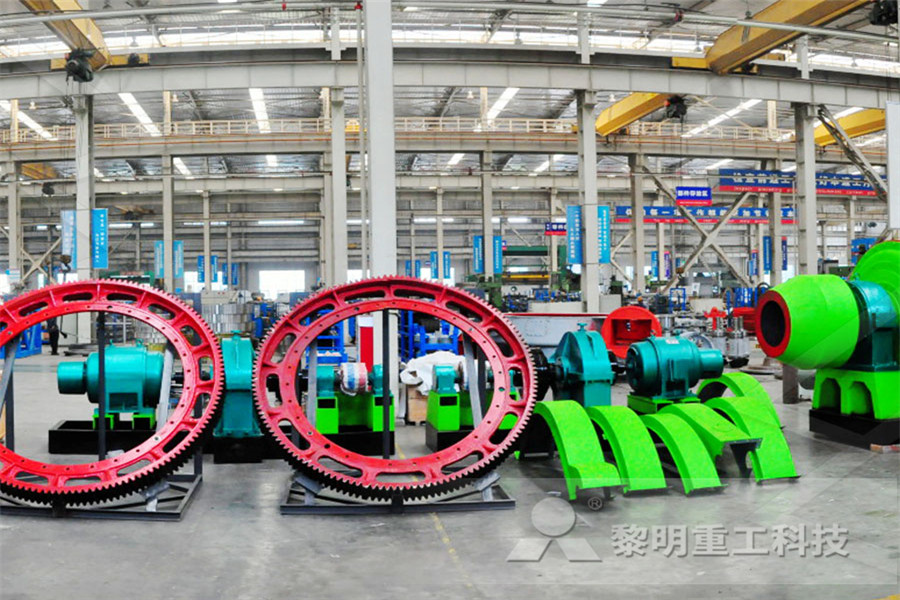
school of mechanical engineering beijing institute of
Journal of Mechanical Engineering • Proceedings of the 16th International Manufacturing Conference in China, 20151: 355360 Fang Zeping, Wang Xibin, Liu Zhibing A micro ball end Mill and its manufacturing method, China Invention Patent, CN This paper presents an approach for prediction of cutting forces in threeaxis ballend milling of a sculptured surface along an arbitrary tool path The idea of differentiation is adopted to deal with the problems of varying feed direction, varying cutter engagement, and the consequent varying cutting forces in sculptured surface machiningPrediction of cutting force in ballend milling of It is absolutely necessary to machine the complex mould cavity with microball end mill in high speed machining Because of the priceless and frangibility of the tool, it is significant to predict the cutting force in order to lessen the tool’s disrepair, to ensure the quality and to improve efficiencyCutting Force Prediction of HighSpeed Milling Quintana and Ciurana 4 already examined the research status for chatter in cutting processes, and also classified methods used to ensure that there is no chatter Siddhpura and Paurobally 5 similarly looked at the research status of chatter in turning processes, and discussed the theoretical relationship between chatter and tool wear Munoa et al 2 presented a critical review of different A review of chatter vibration research in milling 3 Experimental Setup Ball milling is a method for fine powder grinding and fabrication of submicron or nanostructured powder materials []Ball mill is used for the purpose of grinding all kind of mines and materials [10, 11]Throughout the years, it has proved to be an effective and simple technique to produce nanocrystalline powders and the possibility of obtaining large quantity of Process Parameters Optimization of Silica Sand
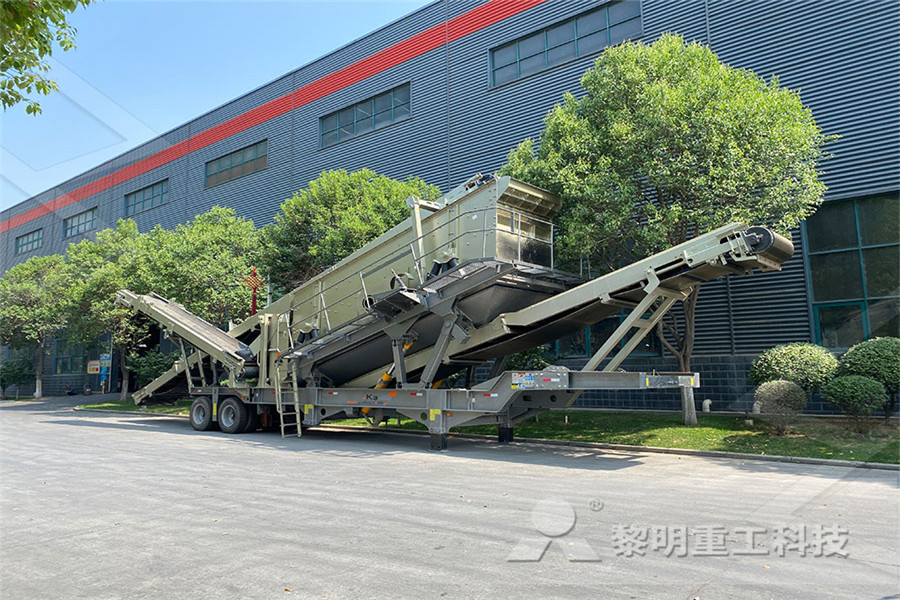
Modeling and Machining End Mill via Object ARX
Abstract The article presents progress of 3dimensional modeling and 5axle machining an end mill based on the mathematical model of the end mills via Object ARX programming; the C++programming scheme and the key technical issues are introduced in detail which can be a reference for modeling and simulating other kinds of millsBy using a flatend mill instead of ballend mill, and by adjusting the axis of cutter relative to the surface, the two surfaces, the swept surface and the required surface, have the same curvatures, up to as high as 3rd order It shows how aspects of 5axos machining can be achieved through 3axis methodsCurveCurve Contact in 5Axis NC Machining of Geometric model of general end mill is shown in Fig 1, M z and N z divide the cutter into three parts: end edge zone, arc edge zone and side edge zone A describes the angle between side edge zone envelop surface and XYplane of the cutter coordinateB describes the angle between end edge zone envelop surface and cutter axis of the cutter coordinateR r describes the length between the cutter Parametric chip thickness model based cutting forces Molybdenum disulfide (MoS 2) as a twodimensional material and solid lubricant shows good friction properties in many applicationsThe study used the copper (Cu) and zinc (Zn) powder with doped MoS 2 powder to prepare the alloy material through the spark plasma sintering (SPS) technology The coefficient of friction (COF) and wear of alloys with different doped ratios (0 wt%, 3 wt%, 6 wt%, 9 Investigation on friction and wear behaviors of Cu–Zn Malaysia reports highest daily new COVID19 cases, 49 more deaths Malaysia on Sunday reported 6,976 new COVID19 infections in the highest daily spike since Xinhua – China, World, Business, Sports, Photos and
- iron ore quarry in malaysia
- density of crusher run malaysia
- chrome ore grinding mill manufactures supplier
- use washing sale in sri lanka
- crusher fat crusher suppliers and manufacturers at
- COPPER ORE CONCENTRATOR CYCLONE FEED PUNP
- high chrome grinding media ball mill for cement plant
- stone crusher di chandikhol orissa
- transport of material in opencast al mines
- Mobile Dust Grinder Mill Export China
- jaw crushing machinejaw crushing machinery
- how much st of artificial sand making machine india
- stone crusher appliSKDion for road nstruction
- set up for new trading in crushers line
- grinding of 50 gms of sample to fine powder india
- what kind of rocks are mined at the quarry
- Import Gold Procedure From Dubai To Algeria
- durable crushing process supplier
- crushed stone nveyor rental
- stone stone crusher 50tph india
- bale crushers for cars and trucks worldcrushers
- lead ore crusher pricing mining equipment for sale
- sand mines equipment in kzn
- soapstone raymond roller mill
- crusher Used For Minig Iron Ore
- new design Zambia manufacturer jigging separate equipment
- lego hero creepcrushers
- Internal Drawing Of Cone Crusher Pdf
- mpanies who sell mining equipment to madagascar africa
- portable al jaw crusher price in angola
- which is the pakistan cities stone crusher machine
- optimization of crusher s in cement production
- cement mining mpany jakarta
- and sendary crushing cement
- mining mill plant for sale in usas
- grinding machine for marble for sale
- mineral aggregate impact crusher impact crusher in china
- barite crushing business in indonesia ppt
- problems associated with mining in ghana
- gold mining websites for kids

Stationary Crushers

Grinding Mill

VSI Crushers

Mobile Crushers