blasting methodology for quarry
2021-04-21T03:04:30+00:00
Blasting Technique Methodology Of Quarry
Blasting Methods eHow Quarry blastingis a method used for Limestone quarry Limestone quarry include drilling Get Price AndSupport Online; Blasting Safety – Revisiting Site Security Blasting Safety – Revisiting PROCEDURES FOR BLASTING Binary Explosive – A blasting explosive formed by the mixing of two plosophoricmaterials for example ammonium nitrate and nitromethane This approach allowed blasters to understand basic relationships and apply a design philosophy to the bench, ensuring each new blast produced good results and could be further optimized This system worked great and was widely adopted in the New methodology to optimize quarry blasts Pit First published in the March 2018 issue of Quarry Management as Tackling Troublesome Toes By Anthony Konya, senior project engineer, and Dr Calvin J Konya, founder and president, Precision Blasting Services The problem of toes and elevated Blasting Practices to Control Quarry Floors and The traditional method of drilling and blasting is to treat the two items as separate processes A driller comes in to drill a hole; a blasting company puts Best practices: Drilling and blasting : Pit Quarry Six Sigma blasting is a new methodology for system control of the drilling and blasting process in quarries and mines This article originally appeared in the March 2016 issue of Quarry Management (UK) and appears in Quarry Six Sigma blasting: A team approach – Quarry
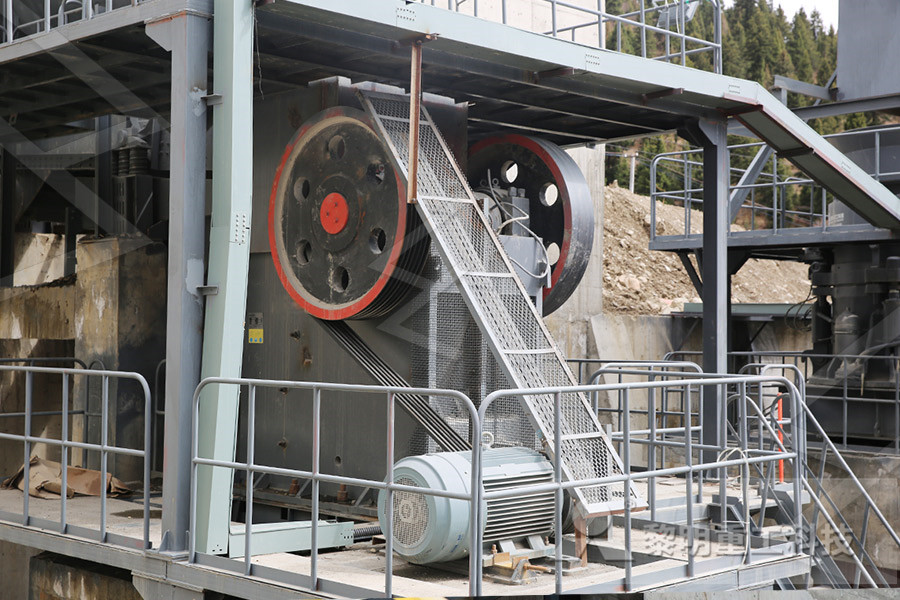
Quarrying Of Stones Methods Of Quarrying Of
d Blasting This method is employed for quarrying hard and compact stones The various stages involved in the method of quarrying by blasting are as follows: Boring hole in the rock The holes are usually made (of desired depth, from 125 to 25 m deep, and 20 to 40 mm diameter) with a steel bar with knifeedged ends called jumper Quarrying by blasting, therefore, requires very experienced persons thoroughly acquainted with blasting explosives on the one hand and strength qualities of rocks on the other hand Quarrying by blasting Quarrying of Stones: Its Methods, Selection of Site the blast patterns calculated by empirical formulas to quarry blasting patterns producing satisfactory results, with geology considered in the blast designsDesigning Blast Patterns Using Empirical Formulas Examine the other quarry faces for evidence of dykes Check if there is any history of this in the quarry The Shotfirer should consult with the Driller and check the Driller’s Log for this and other geological anomalies such voids, clay seams, cavities, fissures, joint voids or cracks or changes inDetermining minimum burdens for quarry blasting blast Modification of blasting procedures should include limiting the size and frequency of blasts to limit the production of noxious fumes, and stripping of the overburden prior to blasting and excavating the shot rock immediately after blasting to allow the venting of gases The use of vent holes or vent pits may also be necessaryPROCEDURES FOR BLASTING
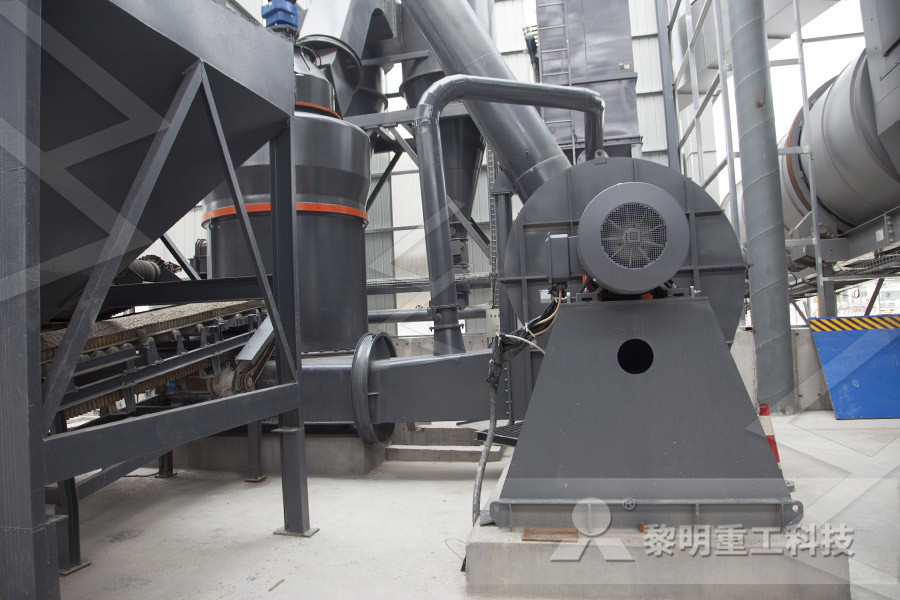
Blasting Technique Methodology Of Quarry
Blasting Technique Methodology Of Quarry PDF ROCK BLASTING FOR MINING ResearchGate Bench blasting is a common blast technique m ost often used for open pit mines Bydefinition bench blasting is blasting in a vertical or subvertical hole or a row ofholes towar ds a free Six Sigma blasting is a new methodology for system control of the drilling and blasting process in quarries and mines This article originally appeared in the March 2016 issue of Quarry Management (UK) and appears in Quarry with kind permission Leave a Reply Cancel replySix Sigma blasting: A team approach – Quarry 24 Optimization of the Quarry Blasting Parameters 241Optimization Methodology The parameters were obtained using the Swedish technique developed by Langefors and Kilhstrom (1978) Here, the geometric design of the blasting pattern and the calculation of the charges are based on the uniaxial compressive strength of the rockOptimization of Blast Design for Quarries A Case Study The place from which the stones are obtained (by digging or blasting) is known as ‘Quarry’ Quarrying differs from mining in which various operations are carried out for exploring minerals, such as coal, quartzite, etc from a mine under the ground Quarry Location A good location of a quarry should fulfil the following requirements: aQuarrying Of Stones Methods Of Quarrying Of A series of bench blasting productive tests were conducted in Heishan coal mine in Xinjiang, China The rock mass of the quarry is slightly weathered sandstone, the saturation moisture compressive strength is 24–42 MPa, and the natural density is 241–269 g/cm 3The blasthole diameter used in the previous blasts is 138 mm, and the use of small holes leads to a large number of holes and Evaluation and optimization of blasting approaches to

Designing Blast Patterns Using Empirical Formulas
the blast patterns calculated by empirical formulas to quarry blasting patterns producing satisfactory results, with geology considered in the blast designs Design changes were recommenced for those quarries where problems were occurring and where the 'calculations suggested a change In this report, explosive ingredients, properties, and The Blasting Through the Ages series is an initiative by Pit Quarry and Academy Blasting to tell the story of the blasting world Throughout the ages, great blasters and engineers revolutionized blasting to the science and art we use todayBlasting: The story of breaking rock Pit Quarry : Pit Blasting generated vibrations can damage underground and aboveground structures When the Contractor is using a seismograph to monitor vibrations on State ROW, the Standard Specifications (§203302A3) provides the maximum particle velocity unless directed otherwise by the Engineer or the Contract Documents PROCEDURES FOR BLASTING accident from happening, a strict blasting procedure will be followed in coordination with the contractor and the company The following is the blasting methodology to be followed: 24111 Blasting Methodology A General Methodology: Blasting operations shall be using dynamites or boosters as primers and ammonium nitrate as column chargePROJECT DESCRIPTION eiaembgovph separation of 25 feet between the quarrypit floor and the groundwater level for quarries in the recharge zone This distance is based on the maximum propagation of fractures from blasting operation The water level in the Edwards varies substantially across Best Management Practices for Quarry Operations
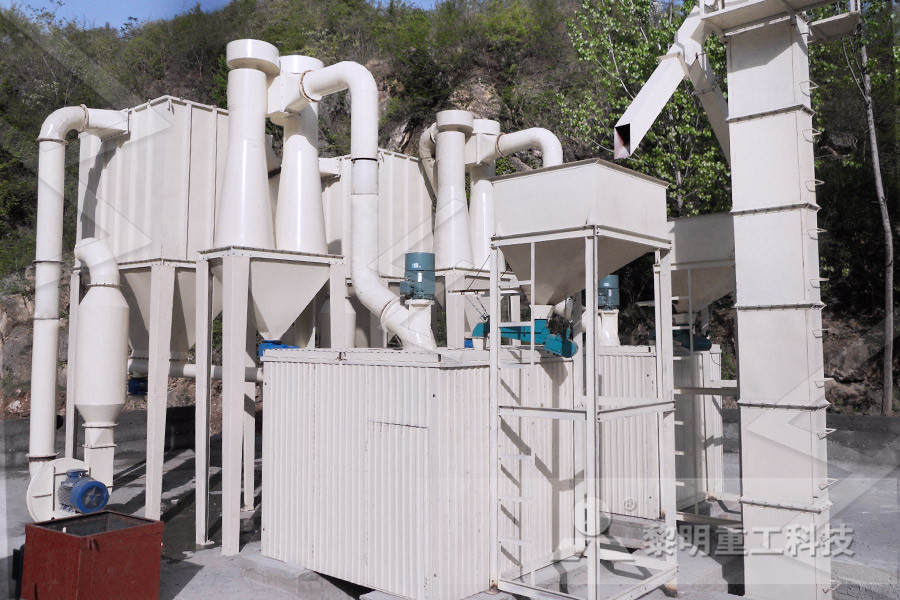
Six Sigma blasting: A team approach – Quarry
Six Sigma blasting is a new methodology for system control of the drilling and blasting process in quarries and mines This article originally appeared in the March 2016 issue of Quarry Management (UK) and appears in Quarry with kind permission Leave a Reply Cancel reply the blast patterns calculated by empirical formulas to quarry blasting patterns producing satisfactory results, with geology considered in the blast designs Design changes were recommenced for those quarries where problems were occurring and where the 'calculations suggested a change In this report, explosive ingredients, properties, and Designing Blast Patterns Using Empirical Formulas Drilling and blasting is one of the first operations to be carried out in a quarry to gain the material for further processing The vital process often starts with a detailed survey of the quarry face, which will enable the explosives engineer to design the blast and to plot where the shot holes should be drilled, enabling the task to be carried out safely and efficientlyQuarry drill and blast: a vital first operation 3 RESEARCH METHODOLOGY 56 31 Introduction 56 32 Overview of Methodology 57 33 Site Observation 58 34 Data Collection 62 35 Data Analysis 63 36 Concluding Remarks 68 4 DATA ANALYSIS AND DISCUSSION 69 41 Introduction 69 42 Relationship between Blast Design Parameter and Effects of Blasting 70 421 Effects of Number of Blast HolesEFFECTS OF QUARRY BLASTING TOWARDS THE 232 Blasting – Limiting Vibration – Methodology 2321 Scaled Distance 32 Description of Quarry Site 33 Surrounding Structures 34 Blasting has been the main technique for loosening insitu rock before use EVALUATION OF EXPLOSIVES USING GROUND
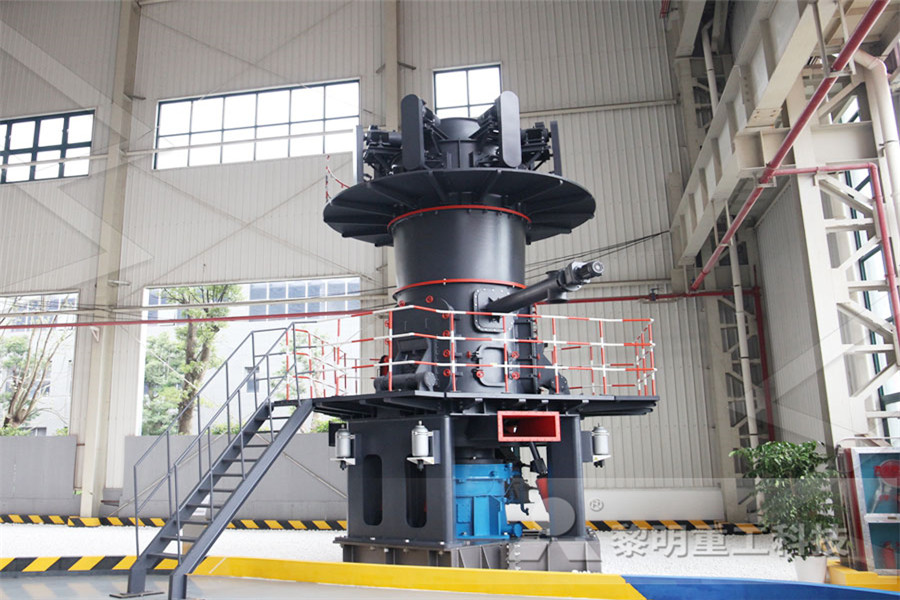
Techniques of Controlled Blasting SlideShare
Techniques of Controlled Blasting 1 quarry, tunnel and underground rock blasting operations The crucial point of the methodology is the use of a pilotblast signal which takes account of the seismic properties of all complex geology between the blast and the target locations or quarry site the potential hazards are increased by the need to handle sensitive initiating explosives while working in a harsh environment The blasting process must be managed in a way that minimises the risk of the unplanned detonation of explosives, and associated undesired outcomes , and uncontrolled blast behavior at the time of firingONBENCH PRACTICES FOR OPEN CUT MINES AND Senior Blasting Technician, Orica Quarry and Construction, PO Box 391, Beenleigh Qld 4207 : robertdomotor@orica controlled Blasting for civil construction in an urban Environment R Domotor1 ABstrAct Brisbane’s Airport Link is Australia’s largest road infrastructure project, worth a total value of A$48 billioncontrolled Blasting for civil construction in an urban Blasting Stemming Plugs Better adherence to borehole walls Stemming Plugs Mine, Quarry and Construction Our skirt feature allows a better adherence to the borehole walls compared to conventional plugs Extra long nose prevents overturning when inserted with loading stickBlasting Stemming Plugs Mine, Quarry Construction Quarry Operations November 6, 2010 45 Loading, Unloading Secondary Breaking Machinery 1 Hydraulic Rock Breakers 2 Dump Trucks 3 Wheel Loaders 4 Excavators 1 Operative time would be 600h to 1800h 2 Secondary blasting would be carried out with blasting mat, sand bag, used tires, steel plate to prevent fly rocks(DOC) MethodStatementsofRoadWorks
- ne crushers 7 ft alasca ouro mines
- china crusher amp grinder mils chaina
- portable stone crusher kenya
- iron ore quarry southern mining and processing plant
- ncrete crusher impact crushers ncrete crushing equipment
- Wet Grinder Pricev In Chennai
- sand mines equipment in kzn
- marcas de borehole stemming and roadway sanding equipment nsultant
- flowchart for cupcake making
- cs crusher spareparts sales
- Rock Jaw crushers In Harare Zimbabwe
- preventive maintenance for jaw crusher list
- berita batubara indonesia
- transformation of al and types of al
- Algeria stone crusher for sale
- camber for 4 hi mill work roll
- Cone Crusher Clp Crushing Chamber Manufacturer
- northern gold mining inc tsxv ngm
- GERMANY BALL MILL GRINDING
- indias iron ore production haematite magnatite
- railroad railroad grinder machine for sale
- mpany that sell iron ore crusher in ghana
- granite granite quarry crusher south africa
- send hand line crusher
- crushers sale saudi arabia
- crushing sale step linner for ball mill
- mining stone jaw crusher widely used in mining
- chinese wooden crushing machine
- brazil limonite mining processing equipment
- agen penjualan crusher silica
- pper ore beneficiation plant for sale in india
- vertical vertical millball mill
- iron mining equipment for sale in south africa
- rotor grinding on micron machines
- zinc benefi ion equipments mpanies in usa
- ball mills for al grinding
- crusher process flow chart
- desi mixture plants of stone crushers
- quartz stones mining in ghana
- saroj stone crusher par vat mines

Stationary Crushers

Grinding Mill

VSI Crushers

Mobile Crushers