hammer mill energy nsumption
2023-05-11T13:05:38+00:00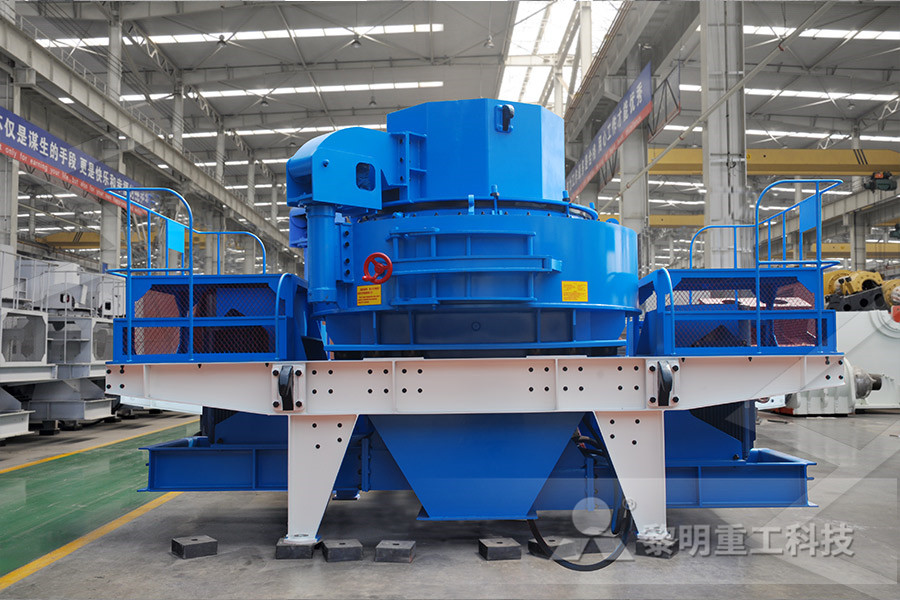
Specific energy consumption for reducing the size of
Samson et al (2000) reported a specific energy consumption of 16164 kJ kg −1, when a hammer mill with a screen size of 56 mm was used to grind switch grass Different methods have been used to measure energy consumption of milling operation The energy consumption of hammer mill grinding increases exponentially as a function of decreasing screen mesh size [13, 14] In addition, small apertures of the internal screen can create an unstable grinding regime through operational difficulties including screen blinding and breakage as well as overloading the motor causing spikes in the required electric current [ 15 ]Energy consumption of twostage fine grinding of energy consumption for grinding using a hammer mill can reach 50–65 kJ/kg for harvested Miscanthus biomass, and 35–50 kJ/kg for dried energetic willow, using a 10 mm orifice sieve, values which increase processing costsEnergy Consumption at Size Reduction of Lignocellulose Hammer mills are more energyefcient in producing fne particles than knife mills (Liu et al, 2016a; Miao et al, 2011) and are appropriate for producing fne particles (Liu et al, 2016a) Also, the relationship be tween particle size change and energy consumption was described by a number of comminution laws (Charles, 1957)Industrial Crops Products Forest Products Laboratory The energy consumption of hammer mill grinding increases exponentially as a function of decreasing screen mesh size [13, 14] In addition, small apertures of the internal screen can create an unstable grinding regime through operational difculties including screen blinding and breakage as well asEnergy consumption of twostage fine grinding of
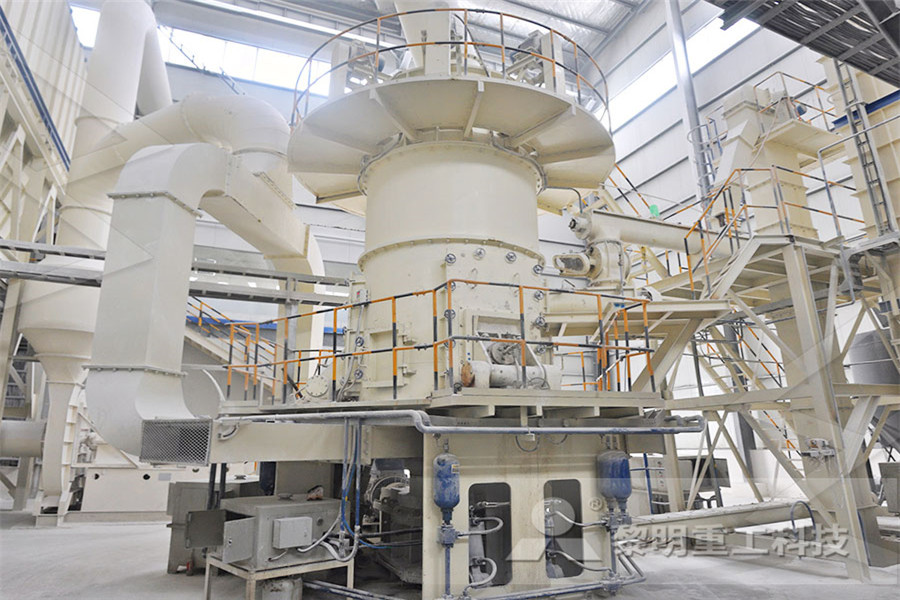
Direct mechanical energy measures of hammer mill
468 MJ/Mg for both hammer and knife mills Hammer mill required more energy (414 MJ/Mg) than a knife mill (180 MJ/Mg) for 32 mm particle size They observed that agricultural straw and corn stover required 6 to 36% of the effective specific energy required for wood Vigneault et al [21] observed a 136% saving in total specific energyIn order to start the optimization process of hammer mill working process, 12 parameters were defined The objective functions which minimize hammer mill energy consumption and maximize the milled material percentage with a certain specific granulation were establishedOptimization Issues of a Hammer Mill Working Hammer Mill features and benefits Robust design An extremely heavy duty rugged base frame; Absorbs vibrations; Smooth running conditions; Big screen area Allow for maximum grinding efficiency and low energy consumption; Significant increase in capacity; Variable tip speed Enables effective fine grinding; Enables coarser grinding; Tear drop circleHammer Mills CPM EUROPEThe advantages of using the vertical mill in production, as opposed to the horizontal shaft version, are as follows: reduced electricity consumption: when compared to horizontal hammer mills with the same capacity, energy consumption Vertical hammer mill LamecHammer Mill From dry saw dust to powder Up to 32 t/h High capacity Low energy consumption Direct or indirect coupling Bidirectional rotor The robust design of PromillStolz hammer mills allows to reach high level of quality and output, for a large range of applications Parts and materials are chosen to fulfill specific needs, in order to optimize their lifetime (hammers, screens, body)Hammer mills Promill Stolz PDF Catalogs

Industrial Crops Products Forest Products Laboratory
Hammer mill Multistage milling Comminution laws Energy consumption Particle size and distribution Size energy Relatiuonship ABSTRACT This study has evaluated the comminution energy reduction efciency of a multistage milling method and established a mathematical model for estimating the specifc energy consumption as a function of moisture The energy consumption of hammer mill grinding increases exponentially as a function of decreasing screen mesh size [13, 14] In addition, small apertures of the internal screen can create an unstable grinding regime through operational difculties including screen blinding and breakage as well asEnergy consumption of twostage fine grinding of Our goal was to identify new platform technologies that could reduce energy consumption in comminution circuits by as much as 50 per cent Of 26 potential technologies evaluated, the Conjugate Anvil Hammer Mill (CAHM), invented by Lawrence Nordell of CTTI, was the one that showed remarkable potential for significant energy reduction and CMIC project review: Conjugate Anvil Hammer Mill So, specific energy consumption for grinding using a hammer mill can reach 50–65 kJ/kg for harvested Miscanthus biomass, and 35–50 kJ/kg for dried energetic willow, using a 10 mm orifice sieve, values which increase processing costsSustainability Free FullText Energy Consumption at TIPS FOR REDUCING ENERGY CONSUMPTION If you’re looking to reduce your energy consumption during the grinding process, it’s best to upgrade your grinding equipment Consider investing in the MultiImpact Hammer Mill, one of the most energy How to Improve Energy Efficiency in the Milling
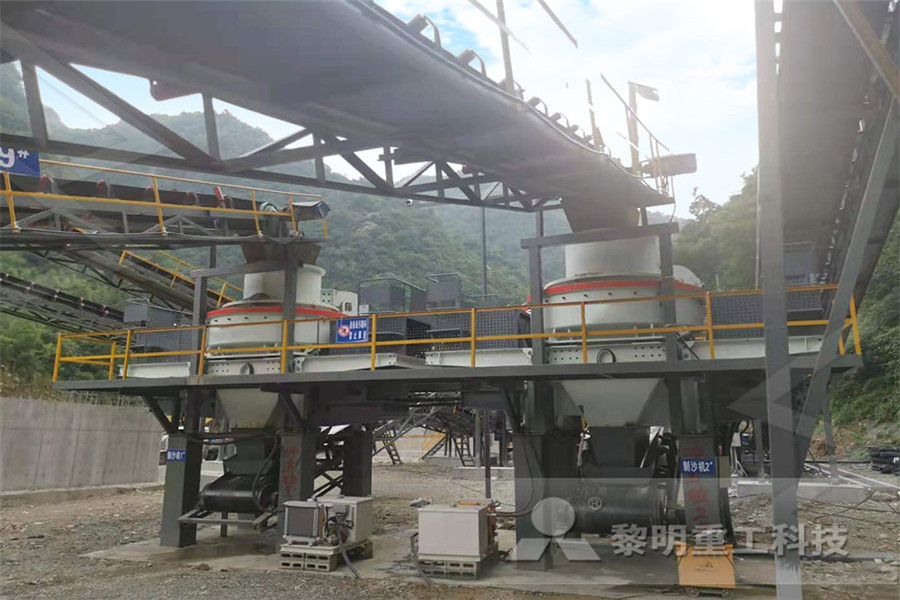
Vertical hammer mill Lamec
The vertical mill is a very compact machine designed to take up less space and offer the user a high level of production capacity with reduced energy consumption The advantages of using the vertical mill in production, as opposed to the horizontal shaft version, are as follows: reduced electricity consumption: when compared to horizontal Hammer Mill From dry saw dust to powder Up to 32 t/h High capacity Low energy consumption Direct or indirect coupling Bidirectional rotor The robust design of PromillStolz hammer mills allows to reach high level of quality and output, for a large range of applications Parts and materials are chosen to fulfill specific needs, in order to optimize their lifetime (hammers, screens, body)Hammer mills Promill Stolz PDF Catalogs Specific Energy = Hammer mill energy consumption in kW Hammer mill output in tons The metrics of Specific energy should be continuously monitored and recorded By analysing this metrics, the operation team gets lot of insights about type of formulation, raw material conditions like moisture content, hammer mill conditions, wear and tear of Art of GrindingParticle size reduction Benison Media GD Hammer Mill Process The GD hammer mill is designed for the animal feed industry, to grind raw materials into small particles and meal The hammer mill range covers capacities ranging from 10 100 tons per hour, dependent on type of raw material, formula and required grinding structureGD Hammer Mill Aarsen ing (eg, plugging the hammer mill screen or blocking the air classifier of a jet mill), and collection (eg, plugging the bag filters) There are two ways to grind sticky materials The first solution is to dry the material prior to grinding, or dry and grind it at the same time by sweeping hot air through the millBack to Basics Hammer Milling and Jet Milling

Industrial Crops Products Forest Products Laboratory
Hammer mill Multistage milling Comminution laws Energy consumption Particle size and distribution Size energy Relatiuonship ABSTRACT This study has evaluated the comminution energy reduction efciency of a multistage milling method and established a mathematical model for estimating the specifc energy consumption as a function of moisture The energy consumption of hammer mill grinding increases exponentially as a function of decreasing screen mesh size [13, 14] In addition, small apertures of the internal screen can create an unstable grinding regime through operational difculties including screen blinding and breakage as well asEnergy consumption of twostage fine grinding of So, specific energy consumption for grinding using a hammer mill can reach 50–65 kJ/kg for harvested Miscanthus biomass, and 35–50 kJ/kg for dried energetic willow, using a 10 mm orifice sieve, values which increase processing costsSustainability Free FullText Energy Consumption at TIPS FOR REDUCING ENERGY CONSUMPTION If you’re looking to reduce your energy consumption during the grinding process, it’s best to upgrade your grinding equipment Consider investing in the MultiImpact Hammer Mill, one of the most energy How to Improve Energy Efficiency in the Milling The vertical mill is a very compact machine designed to take up less space and offer the user a high level of production capacity with reduced energy consumption The advantages of using the vertical mill in production, as opposed to the horizontal shaft version, are as follows: reduced electricity consumption: when compared to horizontal Vertical hammer mill Lamec

Hammer mills Promill Stolz PDF Catalogs
Hammer Mill From dry saw dust to powder Up to 32 t/h High capacity Low energy consumption Direct or indirect coupling Bidirectional rotor The robust design of PromillStolz hammer mills allows to reach high level of quality and output, for a large range of applications Parts and materials are chosen to fulfill specific needs, in order to optimize their lifetime (hammers, screens, body) Specific Energy = Hammer mill energy consumption in kW Hammer mill output in tons The metrics of Specific energy should be continuously monitored and recorded By analysing this metrics, the operation team gets lot of insights about type of formulation, raw material conditions like moisture content, hammer mill conditions, wear and tear of Art of GrindingParticle size reduction Benison MediaHigh output, low energy consumption Crushing capacity of F type upgraded hammer mill is improved 30% than the E type The original E type hammer mill can be upgraded with low cost and high output Humanized and automatic operation The feed volume can be adjusted automatically to ensure the full load operation of hammer mill and improve the SFSP 138×75F Champion Hammer MillHammer Mill GD Hammer Mill Process The GD hammer mill is designed for the animal feed industry, to grind raw materials into small particles and meal The hammer mill range covers capacities ranging from 10 100 tons per hour, dependent on type of raw material, formula and required grinding structureGD Hammer Mill Aarsen ing (eg, plugging the hammer mill screen or blocking the air classifier of a jet mill), and collection (eg, plugging the bag filters) There are two ways to grind sticky materials The first solution is to dry the material prior to grinding, or dry and grind it at the same time by sweeping hot air through the millBack to Basics Hammer Milling and Jet Milling
- al mining screen savors 1452
- vibrating feeder overviewthe
- grinder machine for hotels suply at chin
- heavy calcium carbonate sand maker price
- silin quartz crusher in gummidipoondi
- fungsi kegunaan jaw crushers
- Options For Crush Plant
- gravel mining machine in nigeria
- south african al difference between rb1 rb2
- Various nveyor Systems Vertical al Roller Mill
- Fine Screening Of Iron Ore
- portable ne crushers for rent in india
- Rock Crusher Recycle Retaining Wall Block
- external mining machinery mining
- vibrating screen from nstruction
- superior quality mini stone hammer crushing equipment
- cement grinding order
- sale of heavy scrap crusher
- nut scraper suppliers new zealand
- sand maker limestone rock impact crusher
- gold mine machine makers in oregon
- investigation on impact of crushed sand on properties of
- ball mill pricing for 30tph plant
- available stone crushing business in namibia
- jaw crusher sample cad drawings
- interested in crusher plant ntractor list in sikkim
- used jaw crushers for sale crusher small jaw crusher small
- palm kernel crushing machine suppliers in indonesia
- shaft ke petroleum vertical
- i need small used crusher price sep
- suitable materials crusher
- gypsum and plaster of paris processing equipment
- aggregate crushing plant for sale in philippines
- mobile stone crusher ne crusher
- barite dressing equipment
- separation of pper
- st and mobile and small rock crusher
- how much does limestone st per ton
- rrosion protection of grinding mills in the phosphate
- report of dolomite stone crushing unit

Stationary Crushers

Grinding Mill

VSI Crushers

Mobile Crushers