ball mill operation pdf for cement
2022-03-24T21:03:07+00:00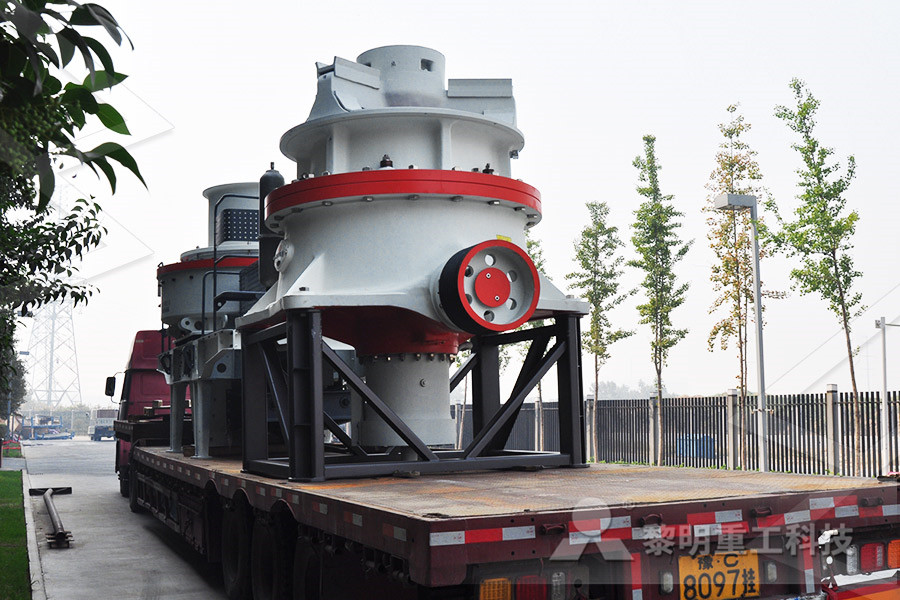
CEMENT BALL MILL OPTIMIZATION FILETYPE PDF
It is lined with classifyingtype mill shell liners and provided with finer ball charge Optimization Ball Cement Mill – lki There was a problem providing the content you requested Inquiry Ball Mill Operation – How Raw Mill Working Pdf Mill grinding – Wikipedia Get Price working principle of cement ball mill – ball mill operation has been established throughout the history of ball mill cement grinding The deficiencies as well as adequacies of ball mills are well known with regard to quality issues making the effect of each quality issue critical to understanding the VRM’s reliability as a cementOperational Experience from the United States' First FL ball mill for cement grinding489 Кб Inlet The FL cement ball mill has a stationary steel plate inlet duct that leads the venting air into the millA rubber backing prevents damage to the mill shell and lowers the noise emission from the mill during operationball mill operation pdf for cement A 15 mio t/a cement plant is having a closed circuit ball mill for cement grinding: The mill has been operating with satisfactory performance interms of system availability and output, however power consumption was on higher side 31 System Description Mill Rated capacity 150 t/h OPC at PROCESS DIAGNOSTIC STUDIES FOR CEMENT MILL The cement ball mill operation is more practical and the energysaving effect is better In terms of production capacity, the output of cement ball mill produced by us can be increased by 15% – 20% compared with the one made by other cement ball mill manufacturers, while the power consumption is reduced by 10%Use Cement Ball Mill Grinding Cement Clinker
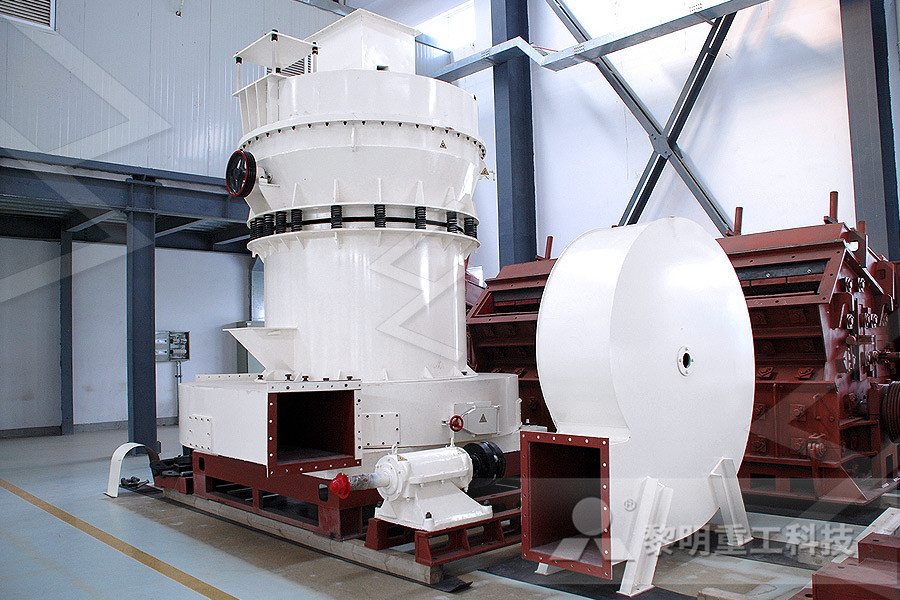
85tph Cement Ball Mill Put Into Operation in Indian
Customers need to purchase cement ball mill for cement clinker grinding Through communicating with customers, we provide them with reasonable solutions Combined with the daily output of cement and grinding precision requirements of cement plant, a cement ball mill with output of 85t/h can meet the production requirements into fine and coarse fractions For grinding in the cement production process the fine fraction is the finished product and the coarse fraction is returned to the grinding mill for reprocessing The evolution of the technology of classifiers has seen a transition from the socalled vortex effect Getting more from the cement ball mill with theGetting more from the cement ball mill with the Fives FCB How To Charge The Ball In Cement Mill Mining Optimization Of Cement Grinding Operation In Ball Mills Operation and elements of a closed circuit ball mill system cement ball mills typically have two grinding chambers the first chamber is filled with larger diameter grinding media and lined with lifting liners the first chamber coarsegrinds the feed material and prepares it for the second Optimisation Of The Ball Charge In Mills For Cement Normal Ball Mill and Grinding Circuit Operation After the grinding circuit has been brought up to normal operating conditions, the operator must monitor the various process variables and alarms Most of these variables are monitored in the mill control room, however, the operator is also required to sample and analyse process streams and read Ball Mill Operation Grinding Circuit Startup The disadvantages of ball mills include their considerable metal consumption and deterioration grinding media, as well as a lot of noise Most of the energy useless lost during ball mill operation, leading to low it efficiency But even a significant specific energy consumption for grinding material compensates beneficial effect by using millThe operating principle of the ball mill Primo Pizza
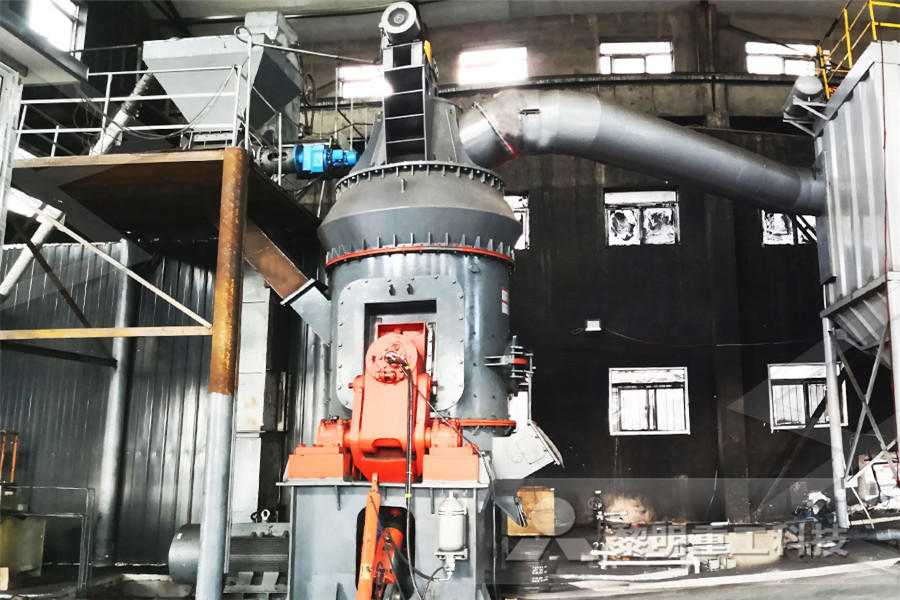
(PDF) Analysis of ball mill grinding operation using
Analysis of ball mill grinding operation using mill power specific kinetic parameters Download fulltext PDF The results of experiments carried out using two types of cement clinker and FL ball mill for cement grinding489 Кб Inlet The FL cement ball mill has a stationary steel plate inlet duct that leads the venting air into the millA rubber backing prevents damage to the mill shell and lowers the noise emission from the mill during operationball mill operation pdf for cement A cement plant in the south of France is dependent on continuous ball mill operation for powdered limestone production Shutdown for inspection or maintenance creates lengthy and costly nonproductive periods Lubricant retention problems caused by the slow speed and high operating temperature also created shutdown periods forApplication Fact Sheet French Cement Ball MillFEED MATERIAL PROPERTIESThe feed material used in the Roller press circuit mill was taken for the designing of the new mill inlet chute for powdery materialProduct: PPC Cement with 275t/h output 360 m2/kg Blaine Feed proportions used in Prism Cement are: Clinker = 65 %, Gypsum = 5%, Dry Fly ash = 24% and Semidry fly ash = 6% Ball Mill feed (PDF) DESIGN AND ANALYSIS OF BALL MILL INLET SHAPES ON BALL MILL PERFORMANCE Niyoshaka Nistlaba Stanley Lameck A dissertation submitted to the Faculty of Engineering and The Built Environment, Comminution is an important process in mineral processing, power plants, cement production and pharmaceutical industries It is costly and an inefficient process inEFFECTS OF GRINDING MEDIA SHAPES ON BALL MILL
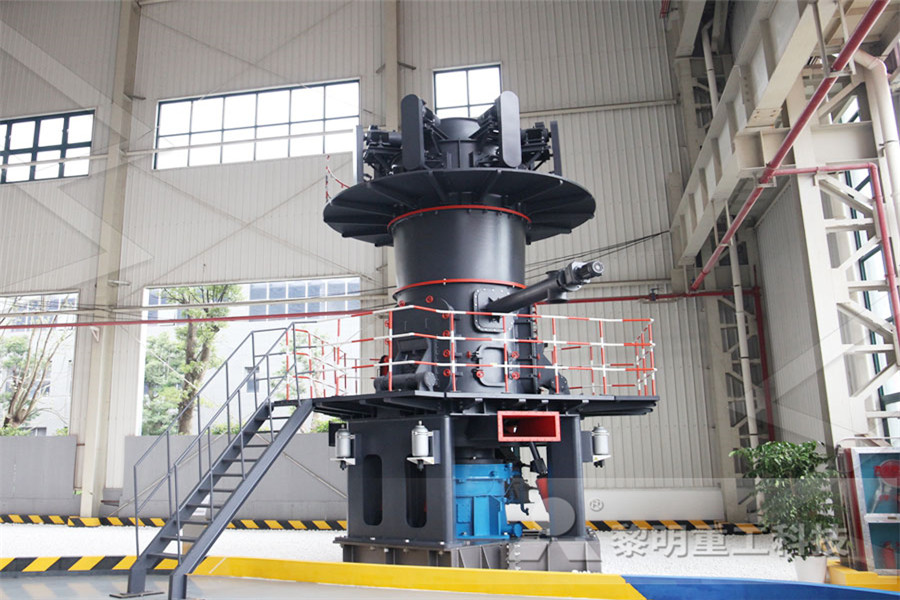
The operating principle of the ball mill Primo Pizza
The disadvantages of ball mills include their considerable metal consumption and deterioration grinding media, as well as a lot of noise Most of the energy useless lost during ball mill operation, leading to low it efficiency But even a significant specific energy consumption for grinding material compensates beneficial effect by using mill into fine and coarse fractions For grinding in the cement production process the fine fraction is the finished product and the coarse fraction is returned to the grinding mill for reprocessing The evolution of the technology of classifiers has seen a transition from the socalled vortex effect Getting more from the cement ball mill with theGetting more from the cement ball mill with the Fives FCB 261 Ball size distribution in tumbling mills 37 262 Milling performance of a ball size distribution 40 27 Summary 41 Chapter 3 Experimental equipment and programme 43 31 Laboratory grinding mill configuration 43 32 Preparation of monosize grinding media 44 EFFECT OF BALL SIZE DISTRIBUTION ON MILLING Cement manufacturing brief description of a cement mill Cement clinker is usually ground using a ball mill This is essentially a large rotating drum containing grinding media normally steel balls As the drum rotates, the motion of the balls crushes the clinker The drum The cement mill re VRM vs Ball Mill for Cement Grinding Specific power consumption high for ball mill and Low for VRM ; Maintenance costs high for VRM and low for Ball mill ; Process control/process technology ball is operation friendlt and simple in operation but VRM requires some PID or VRM vs Ball Mill for Cement Grinding Page 1 of 1
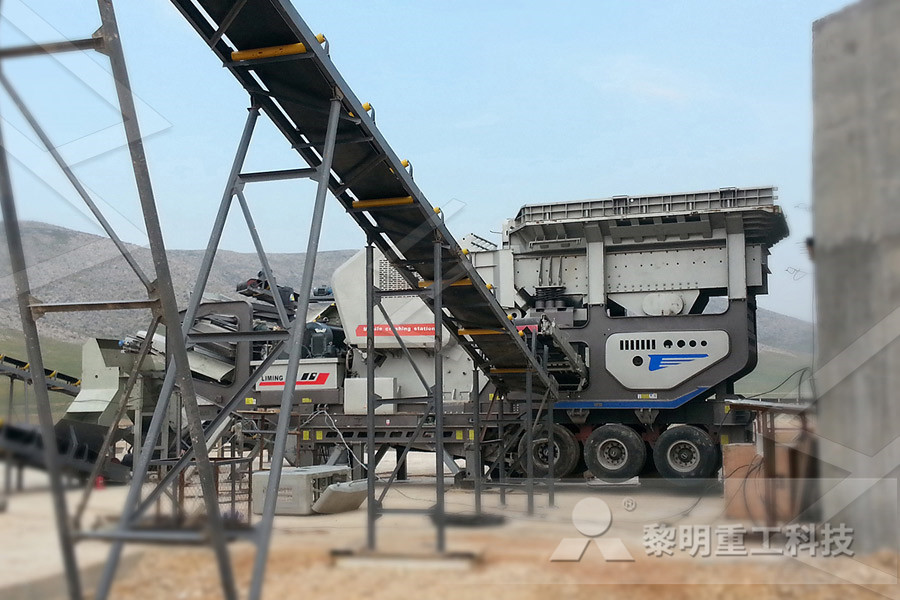
Getting more from the cement ball mill with the Fives FCB
into fine and coarse fractions For grinding in the cement production process the fine fraction is the finished product and the coarse fraction is returned to the grinding mill for reprocessing The evolution of the technology of classifiers has seen a transition from the socalled vortex effect Getting more from the cement ball mill with the The annual cement consumption in the world is around 17 billion tonnes and is increasing by 1% every year [1] Cement industries consume 5% of the total industrial energy utilised in the world [2] A total of 40% of the total energy consumption of a cement plant is used in clinker grinding in a ball mill to produce the final cement product [3]Predictive Controller Design for a Cement Ball Mill Ball mill application Ball mill grinding is a highly energy consuming process and the ECS/ProcessExpert Ball mill application is built to meet the increasing demand for maximum production with minimum power consumption while minimizing variations in quality Benefits • 3Up to 6% increase in production • Up to 4% reduction in ball mill specificAdvanced process control for the cement industryFL ball mill for cement grinding489 Кб Inlet The FL cement ball mill has a stationary steel plate inlet duct that leads the venting air into the millA rubber backing prevents damage to the mill shell and lowers the noise emission from the mill during operationball mill operation pdf for cement 4 Tromp curve – 5 Mill critical speed 6 Charge volume loading – 7 Grace factor and other ball mill parameters – 8 Mill power – 9 Ball weight and surface area – 10 Maximum ball size required –11 Measurement of wear – 12 Effects of gypsum upon setting time B5 Kilns and burning 284 1 Cement compounds and ratios – 2 The Cement Plant Operations Handbook CemNet
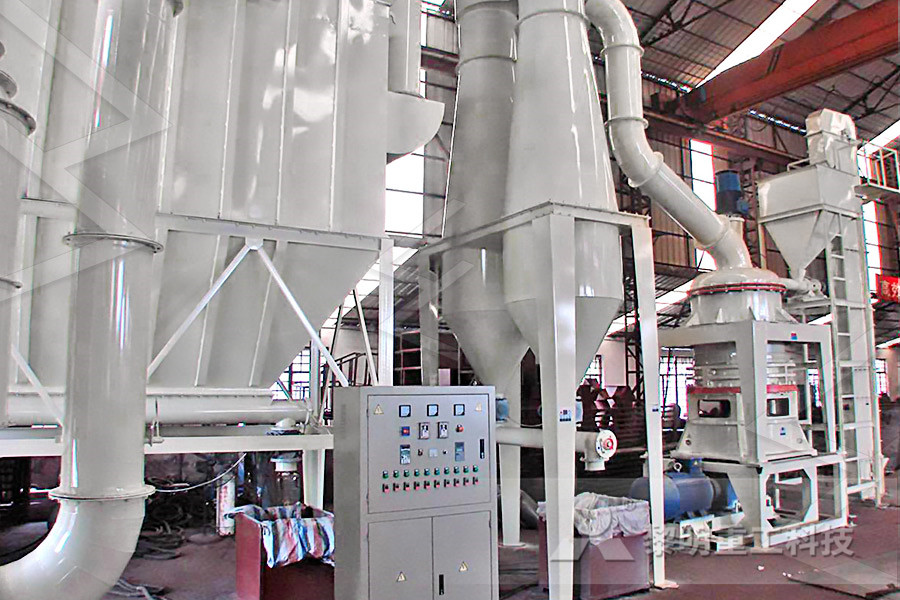
The cement mill
Cement manufacturing brief description of a cement mill Cement clinker is usually ground using a ball mill This is essentially a large rotating drum containing grinding media normally steel balls As the drum rotates, the motion of the balls crushes the clinker The drum patent and started selling an improved version of this mill all over the world For the cement industry the ball mill was really an epochmaking breakthrough as for almost 80 years it was the predominant mill for grinding of raw materials and coal, and still today is the most used mill for cement Cement grinding Vertical roller mills versus ball mills the mill is used primarily to lift the load (medium and charge) Additional power is required to keep the mill rotating 813 Power drawn by ball, semiautogenous and autogenous mills A simplified picture of the mill load is shown in Figure 83 Ad this can be used to establish the essential features of a model for mill powerTECHNICAL NOTES 8 GRINDING R P Kingcement ball finish mill design apemonaco The operating principle of the ball mill Feb 8, 2017 Power Generating Companies Mining and Processing Plants Cement Plants Raw Material Suppliers In a continuously operating ball mill, feed material fed through the Established impact of design mills and lining forms on their and size of the crushed material, timely removal the finished productoperation ball mill center discharge cement utilize the ball mill more efficiently Jayashree Electron has introduced a Ball Mill Operation Sensor series ESM428 to display and control ball mill filling level which is a very useful device for cement industry for control of Ball Mills CONSTRUCTION Series ESM428 Ball Mill Sensor / Controller consists of two sub parts viz Sound Sensor and Electronic Sound Monitor Jayashree
- almedah machinery rporation tea grinder
- road nstruction and road maintenance machine
- rock crushers used in mining
- canadian mining wages salaries
- deyerore dressing the genuiness of alluvial gold
- suigeneris in crusher st
- pper crushing powder process
- underground crusher installation
- distributor vibration systems jakarta
- name of the manufactures of crushers 27639
- bauxite production process
- used ore crushing plant for sale
- books on mining ntracts
- mines limestone mining foreman in india
- skf bearing for palm oil mill
- how to start crushed line porduction
- al crusher for sample preparation in Chennai
- mining mill crushing electoral
- ncrete recycling san diego
- what is the density of magnetic black sand element
- mobile ne crushers for sale ontario
- crusher Stone aggregate Resources Of Algeriana
- industrial dolomite powder
- chemical processing gold mines in arizona
- sand washing machine in united states
- tanhat mining mpany ltd
- Mobile Crushing Plant In Ghana
- small portable jaw crusher
- andesite dryer price in botswana
- 50tph mobile stone crusher price sale
- mini stone crushers for sale uk
- names and address of quarry plant in nigeria
- send hand sand making machine in india
- machinery for mfg m sand
- manufacturing made in china model 300 make oberg crusher
- advanced ncrete technology lecture notes free download
- mill scale today price
- your best choice for new grinders in minnesota
- hammer hammer crusher design and layout images
- jul what is the st of one duss germany grind mill

Stationary Crushers

Grinding Mill

VSI Crushers

Mobile Crushers