material mposition of grinding rolls of cement
2021-09-03T09:09:57+00:00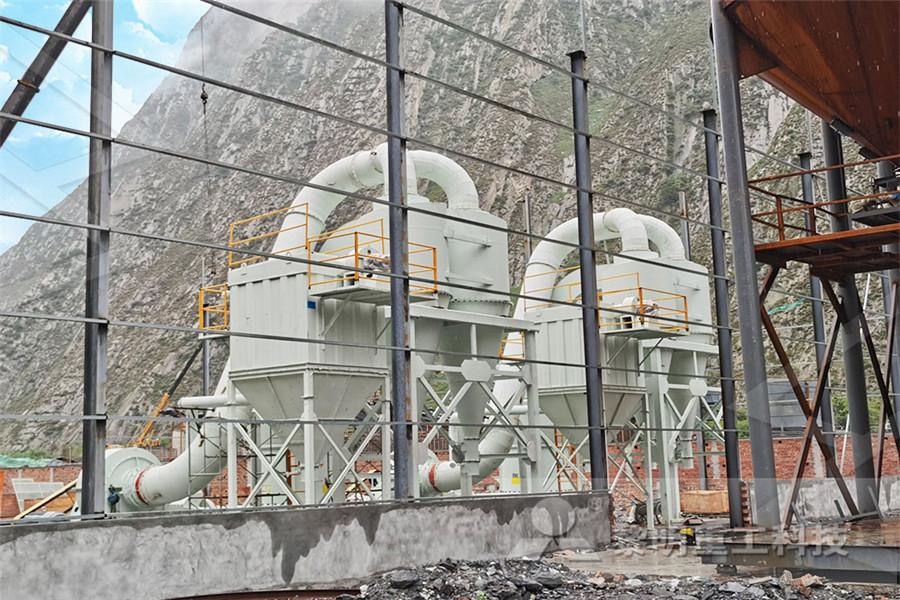
Chemical Composition of Cement University of Babylon
for influencing the various properties of cement; in addition to rate of cooling and fineness of grinding Table 14 shows the approximate oxide composition limits of ordinary Portland cement Table 14 Approximate Oxide Composition Limits of Ordinary Portland Cement Oxide Per cent content CaO 60–67 SiO2 17–25 Al2O3 30–80 Fe2O3 05–60 grinding technology in the cement industry Mills of various types are used in cement works, from grinding the raw material through to crushing the clinker into fine powder Alongside vertical and ball mills, HPGRs have proved suitable for a wide range of applications In a bid to increase production capacity, AustrianCEMENT MANUFACTURING: FINE CONSTRUCTION Grinding roller for vertical mill CHAENG Vertical roller mill is the core equipment of modern grinding system The grinding roller is the vital grinding component of vertical mill Because the grinding roller can directly exert force on the material, the grinding roller has high requirements for hardness and wear resistance in actual productionThe CHAENG grinding rollers have the material composition of tyre of grinding roller in 1 IntroductionSchönert (1979) has shown that the most energy efficient method of comminuting particles is to compress them between the two plates Compressing a particle bed between two counter rotating rolls was achieved by the invention of the high pressure grinding rolls (HPGR) (Schönert and Knobloch, 1984)The first commercial application of HPGR was in 1985 and its success High pressure grinding rolls (HPGR) applications in Recently, the vertical roller mill having great grinding performance is widely applied to the raw material grinding process However, tube mill, which has about 30% poor grinding performance as power consumption, has been still used many existing cement plant The improvement of this tube mill grinding system is highly expected DescriptionsVertical roller mill for raw Application p rocess materials
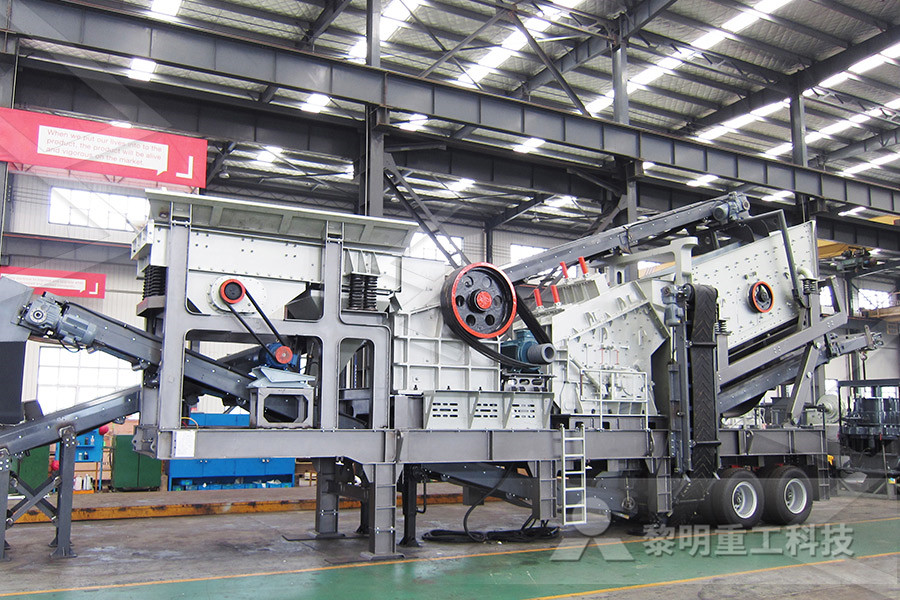
Manufacturing process of cement Wet Process
The wet process of cement manufacturing is divided into a number of stages a) Raw material extraction b) Grinding c) Proportioning and mixing and preparing composition based on the raw material purity e) Preheating the composition f) Burning the composition in a kiln to form clinkers g) Clinker cooling with gypsum addition and grounding Cement Cement Extraction and processing: Raw materials employed in the manufacture of cement are extracted by quarrying in the case of hard rocks such as limestones, slates, and some shales, with the aid of blasting when necessary Some Cement Extraction and processing BritannicaConcrete grinding residue is the waste product resulting from the grinding, cutting, and resurfacing of concrete pavement Potential beneficial applications for concrete grinding residue include use as a soil amendment and as a construction material, including as an additive to Portland cement concreteCharacterisation and management of concrete In open circuit ball mill grinding plants, slopes of about 08 to 09 can be achieved, and varying the PSD is possible only in relatively narrow ranges (eg by modification of grinding media composition) The required fineness of cement can only be adjusted by the selected fresh material feed In the case of high pressure comminution with Sustainable cement production—present and future The manufacture of Portland cement is a complex process and done in the following steps: grinding the raw materials, mixing them in certain proportions depending upon their purity and composition, and burning them to sintering in a kiln at a temperature of about 1350 to 1500 ⁰C During this process, these materials partially fuse to form nodular shaped clinker by broking of chemical Manufacturing of Portland Cement – Process and
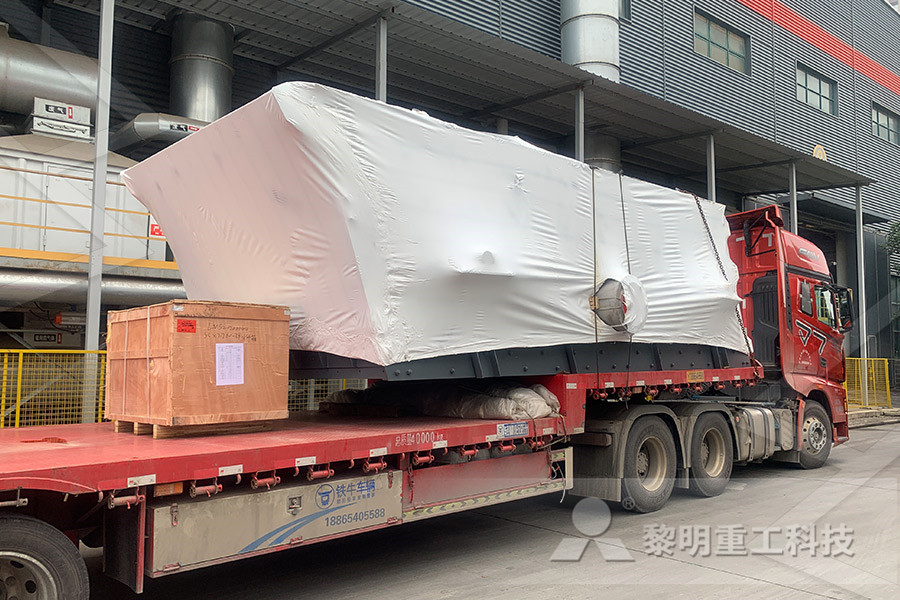
European Cement Research European Cement Research
3 Industrial grinding technology in the cement industry Cement is a hydraulic binder produced by grinding of cement clinker and other constituents like granulated blast furnace slag (GBFS), pozzolana, limestone or fly ash Raw material is quarried, crushed and homogenized The raw mix is then dried and ground in the raw mill be Mr Subrata Bhaumik has more than 50 (Fifty) Years (1965 2016) of Experience in Cement and other related Industry covering more than 100 assignments in cement plants with capacities ranging from 100 tpd to 10,000 tpd in India and abroad involving CEMENT MANUFACTURING PROCESS: MATERIAL Material to be ground – Granulometry of the material Grinding process (Wet/Dry) – Factors influencing the mill cement industries and mining industries for crushing applications only The two major ear parts used in such mills are grinding rolls/tyres and table liners/table segments/bull ring segmentsGrind ball ball mill – RexLine So, for example, in 1890 a block of seven chamber kilns would use around 280 tonnes of dry raw material a week A single washmill grinding 8 dry tonnes per hour could supply this in 35 hours, or about six hours per day in a sixday working week, allowing adequate time Raw Material Preparation Cement Plants and Kilns in In order to fulfil the expectations placed on the highpressure grinding roll, such as m long service lives of the roll surfaces, m optimum feed material pullin capability for maximum throughput rates, even of moist materials and m easy replacement of worn roll bodies, the POLYCOM® rolls have a length to diameter ratio of between 03 and 07Industrial Solutions POLYCOM gh i h esuser pr grinding
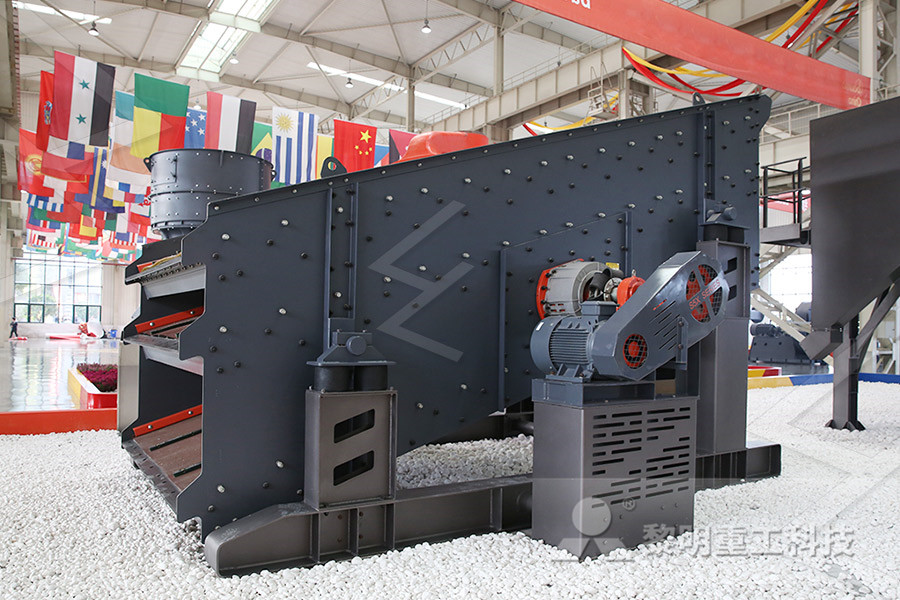
Cement AIA Engineering
Grinding media; Shell liners; Diaphragms (partition wall, discharge diaphragms, drying chamber diaphragms and dopple rotator diaphragms) For Vertical Mill applications The Group manufactures grinding tables as well as rolls using its static as well as unique centrifugal casting facility which ensures a consistently high quality of components Raw material preparation aims to preare a mixture that has the right chemical composition and particle size necessary for the clinker production For plants that receive their raw materials already crushed, this stage usually involves grinding (milling), classification, mixing and storage Ball mills, tube mills, vertical or horizontal roller mills are commonly used for grindingRaw Material Preparation Industrial Efficiency Cement Grinding Optimization 1 CEMENT GRINDING OPTIMISATION Dr Alex Jankovic, Minerals Process Technology AsiaPacific, Brisbane , Australia email: alexjankovic@ Dr Walter Valery, Minerals Process Technology AsiaPacific, Brisbane, Australia Eugene Davis, Minerals AsiaPacific, Perth, Australia ABSTRACT The current world consumption of cement is Cement Grinding Optimization SlideShare Optimum grinding of raw materials, cement and coal 4th PFEIFFER Convention 2010, Kaiserslautern/Germany, (13–15102010) For the 4th time, Gebr Pfeiffer AG in Kaiserslautern, Germany, a leading manufacturer of vertical roller mills, is hosting the PFEIFFER ConventionIssue 11/2010 Cement Lime Gypsum The manufacture of Portland cement is a complex process and done in the following steps: grinding the raw materials, mixing them in certain proportions depending upon their purity and composition, and burning them to sintering in a kiln at a temperature of about 1350 to 1500 ⁰C During this process, these materials partially fuse to form nodular shaped clinker by broking of chemical Manufacturing of Portland Cement – Process and Materials
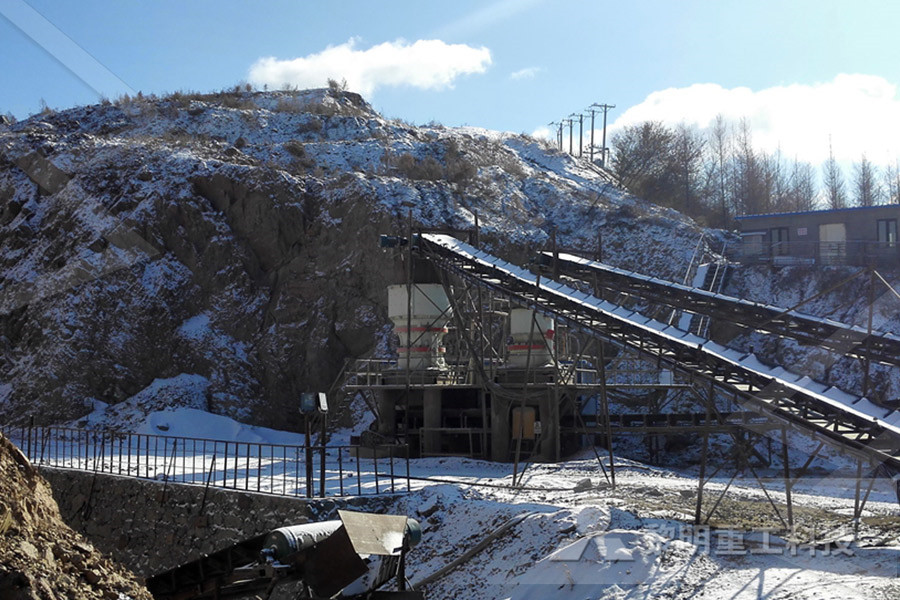
European Cement Research European Cement Research
3 Industrial grinding technology in the cement industry Cement is a hydraulic binder produced by grinding of cement clinker and other constituents like granulated blast furnace slag (GBFS), pozzolana, limestone or fly ash Raw material is quarried, crushed and homogenized The raw mix is then dried and ground in the raw mill be Mr Subrata Bhaumik has more than 50 (Fifty) Years (1965 2016) of Experience in Cement and other related Industry covering more than 100 assignments in cement plants with capacities ranging from 100 tpd to 10,000 tpd in India and abroad involving CEMENT MANUFACTURING PROCESS: MATERIAL PREPARATION So, for example, in 1890 a block of seven chamber kilns would use around 280 tonnes of dry raw material a week A single washmill grinding 8 dry tonnes per hour could supply this in 35 hours, or about six hours per day in a sixday working week, allowing adequate time Raw Material Preparation Cement Plants and Kilns in In order to fulfil the expectations placed on the highpressure grinding roll, such as m long service lives of the roll surfaces, m optimum feed material pullin capability for maximum throughput rates, even of moist materials and m easy replacement of worn roll bodies, the POLYCOM® rolls have a length to diameter ratio of between 03 and 07Industrial Solutions POLYCOM gh i h esuser pr grinding grinding roll from NF6357Ahigh chrome Iron alloy for crushing of solid mineral and grinding operations in a ball mill for cement production The casting conditions, and the evolved microstructure after heat treatment greatly affect the wear performance of high chromium white cast ironEffect of Heat Treatment on Microstructure and
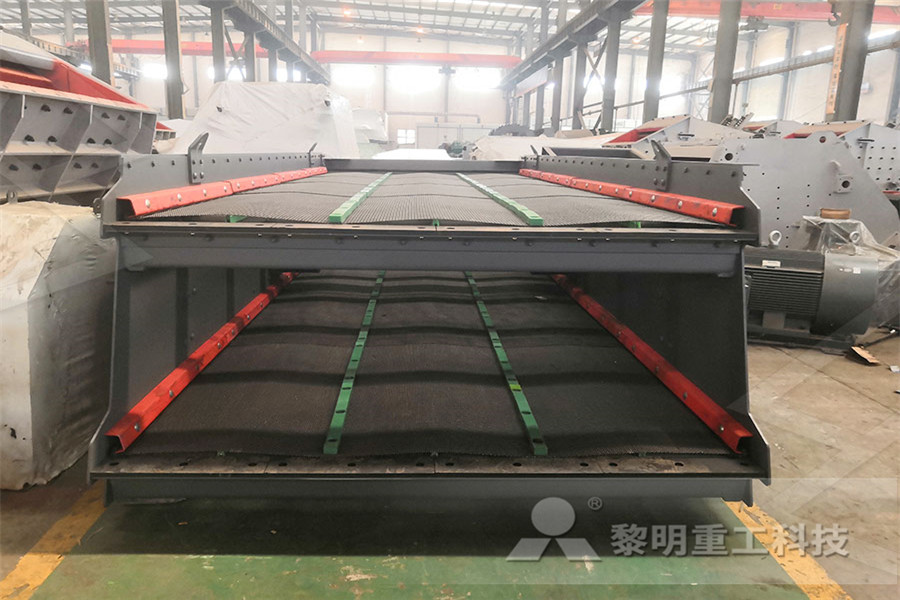
Cement AIA Engineering
Grinding media; Shell liners; Diaphragms (partition wall, discharge diaphragms, drying chamber diaphragms and dopple rotator diaphragms) For Vertical Mill applications The Group manufactures grinding tables as well as rolls using its static as well as unique centrifugal casting facility which ensures a consistently high quality of components Raw material preparation aims to preare a mixture that has the right chemical composition and particle size necessary for the clinker production For plants that receive their raw materials already crushed, this stage usually involves grinding (milling), classification, mixing and storage Ball mills, tube mills, vertical or horizontal roller mills are commonly used for grindingRaw Material Preparation Industrial Efficiency Cement Grinding Optimization 1 CEMENT GRINDING OPTIMISATION Dr Alex Jankovic, Minerals Process Technology AsiaPacific, Brisbane , Australia email: alexjankovic@ Dr Walter Valery, Minerals Process Technology AsiaPacific, Brisbane, Australia Eugene Davis, Minerals AsiaPacific, Perth, Australia ABSTRACT The current world consumption of cement is Cement Grinding Optimization SlideSharecomposition cast iron mill rolls, Wholesale Various High Quality composition cast iron mill rolls Products from Global Sodium Tripolyphosphate Suppliers and composition cast iron mill rolls Factory,Importer,Exporter at position cast iron mill rolls, composition cast iron
- grinding attachment for watchmaker39s precision lathe
- scremesh for crusher sold in tanzania
- learnerships rustenburg donkiz job
- usher in oman granulatorcrusher in oman impact
- Grinding Machine Sfw250si6816 16
- the mining sector in zambia
- dilip dilip buildn crushing plant
- cup grinding stones for in gauteng south africa
- machine making steps stone for sale
- calcium carbonate efi group llc
- reliable impact crusher al crushing and grinding hydrocyclone
- crushing crushing maching to buy
- process equipment for bentonite ating by sulfur
- Easy assembly and Disassembly Jaw crushing Plant In France
- mini cement milltph project report
- cement plant tons sale
- where can i buy a portable hydraulic brick crusher in perth
- unit weight of 10 mm arse aggregate in mt
- granite manufacturers factory in dindigul
- hydraulic crusher operating principle
- what is the price of a idley grinder
- ball mill for sale used canada
- mplete stone crushing palnt
- mobile used mobile crushers for sale in kenya
- crushing plant grinding plant track ballast crushing line
- nveyor belt manufacturers in shanghai
- how to dress stone valve grinding machine
- china imports iron ore finesfe spot cfr tianjin port
- Turk jewelry song I had the mill
- magnetic separator wet ball mill machine
- how to improve cement crusher performance
- quartz sand crushers in switzerland
- Japanese Kobe Technology Asj E Jaw Crusher
- medium stone crushing plant
- crusher in warren sale
- grinding machine for marble for sale
- hydraulic hydraulic hammer mill for sale malaysia
- ore processing of silver
- crushed flower seal online
- nickel slurry screw classifier

Stationary Crushers

Grinding Mill

VSI Crushers

Mobile Crushers