principles of wet milling
2023-05-28T04:05:53+00:00
wet milling Craft Beer Brewing
Wet Milling is a modern technique used to grind malt in preparation for mashing, and it is said to bring significant benefits compared to traditional dry milling It is a practice recommended by the major German brewing plant manufacturers and used in conjunction with a lauter tun See lauter tun It is often called “continuous steep milling” and requires that milling take place in the time taken to mash a grist, The choice between wet and dry milling is, in general, unimportant in smallscale milling but is a major technical problem when largescale milling in the metallurgical industries is involved On purely mechanical grounds it is difficult to see any great difference in fundamental principles between wet and dry milling, since dry milling may be regarded as wet milling with a fluid having the viscosity and density of air, whereas with wet milling the fluid is a liquidDry Grinding VS Wet Grinding 911 MetallurgistIKA wet milling machines are based on the rotorstator principle Exhibiting a high level of shearing energy input, milling machines can achieve particle sizes of 10 µm and below IKA wet mill machines are capable of processing products with a broad spectrum of viscosityIKA Wet milling IKA Process Wet milling requires less energy and time than dry milling Thanks to the environmentally isolated system, it is a dust free process and the material is less heated up However, wet milling has some disadvantages as well, eg, increased wear of the grinding medium, corrosion hazards, etcThe Effect of an Optimized Wet Milling Technology on Kukolev, GV, Piven', IY Polishchuk, VS The effectiveness of wet milling materials in ball mills Glass Ceram 29, 251–253 (1972) /101007/BF Download citation Issue Date: April 1972 DOI: /101007/BFThe effectiveness of wet milling materials in ball mills

Wet Grinding NETZSCH Grinding Dispersing
Finest wet grinding technology – the laboratory mills of the MicroSeries are an investment in the future for new product developments of different fields of application of pigmented ink jets, technical ceramics, cosmetics, pharmaceutical applications and nanoscale Wet finishing The objectives of wet finishing of wool fabrics are firstly to remove contaminants from the wool by scouring and, if necessary, by carbonising The latent stresses and strains the fabrics must then be relaxed, and the fabric set, in a process known as crabbing Special qualities can then15 Principles of Wool Fabric Finishing Woolwise The wet grinding and dispersing process defines your end product characteristics Our solutions include cuttingedge bead mills and threeroll mills, supported by unrivaled process and application expertise, to give you consistent, repeatable quality, every timeWet Grinding and Dispersing Equipment Group The 12 Principles of Green Chemistry Prevention of waste Atom Economy Less Hazardous Chemical Syntheses Design Safer Chemicals Safer Solvents and Auxiliaries for Accident Prevention Design for Energy Efficiency Reduce Derivatives Use Renewable Feedstocks CatalysisBall Milling University of Massachusetts Boston Principles of Milling Phenomenological Description This phenomenon is typical in dry and wet milling operations that use colliding milling mediums such as tumbler, vibratory, and attrition ball mills Fig 1 Model of impact event at a time of maximum impacting force showing the formation of a Principles of Milling Phenomenological Description

The working principle of ball mill Meetyou Carbide
The effects of wet milling time on the properties of YT15 and YT5 alloys are listed in Table 82 It can be seen that after three days of ball milling, the strength of the alloy is slightly reduced, the hardness and coercive force and the cutting coefficient are slightly increased, and the amount of change is generally within the measurement Corn wet milling and dry milling are the predominant methods of processing and each method produces distinct coproducts The Corn WetMilling Process The Corn wetmilling process is designed to extract the highest use and value from each component of the corn kernel The process begins with the corn kernels being soaked in large tanks called steep tanks in a dilute aqueous sulfurdifferences between dry grinding milling and wet grinding The effectiveness of wet milling materials in ball mills B N Okunev, Principles of Ballistics [in Russian], Vol 1, Military Publishing House of the National Commissariat of Defense (1943) 7 A G Kasatkin, Basic Processes and Apparatus of Chemical Technology [in Russian], Goskhimizdat (1960) 8The effectiveness of wet milling materials in ball mills Dry milling and wet milling of cereal grains are used to produce ethanol and to partition the grains into an array of feed components (Figure 2)Wet milling is a more complex process and requires highquality grains to produce highvalue products suitable for human use Some of the coproducts, such as maize gluten meal, may be marketed in higher value markets such as the pet food or poultry Dry Milling an overview ScienceDirect Topicssözer makine sanayi ve ticaret ltd Şti mixers wet milling machines planetary mixer machines zetmixer machines hydraulic pressout machines horizontal mixer machines plaster mixer machines filling and weighing machines laboratory equipments auxiliary equipments turnkey projects find my machineryWET MILLING MACHINES Sözer Makine Sanayi ve Ticaret

Powder metallurgy – basics applications
• Milling can be dry milling or wet milling In dry milling, about 25 vol% of powder is added along with about 1 wt% of a lubricant such as stearic or oleic acid For wet milling, 3040 vol% of powder with 1 wt% of dispersing agent such as water, alcohol or hexane is employed • Optimum diameter of the mill for grinding powders is about 250 mm general principles that apply to most of them milling, pounding, g rinding, tempering, parboiling, soaking, drying, sieving Secondary processing of cereals (or 'adding value' to cereals) is the utilisation of the primary Hammer mills cannot be used for wet milling Roller mills crush the grains rather than millingPOST HARVESTING PROCESSING FAO width form Dyeing in rope form can lead to a degree of milling (consolidation) and may even completely change the character of the fabric On the other hand, dyeing in open width may lead to flat setting of the fabric Dry treatments Once all the wet finishing processes have been completed, the fabric is dried The first step in15 Principles of Wool Fabric Finishing Woolwise mixed with wet grains – Rewetting > cracks in dry grains 15 MC, % wb 20 Middle Bottom Avg • For even drying – sun drying: stir every 30 minutes iiifidbd 10 0 5 10 15 Drying time, h – mix grain in fixed bed dryers – use recirculating batch dryers – use low temperature for more even dryingDrying Basics and Principles IRRI Rice Knowledge Bank Although the general principles of granulation technology have remained unchanged for several decades, the emergence of several process modifications seem to be gaining popularity among the pharmaceutical industry Two of those modifications are wet milling operation and spraying in a controlled manner using a spray nozzle over an extended period of timeAdvances in Wet Milling and Controlled Spraying in
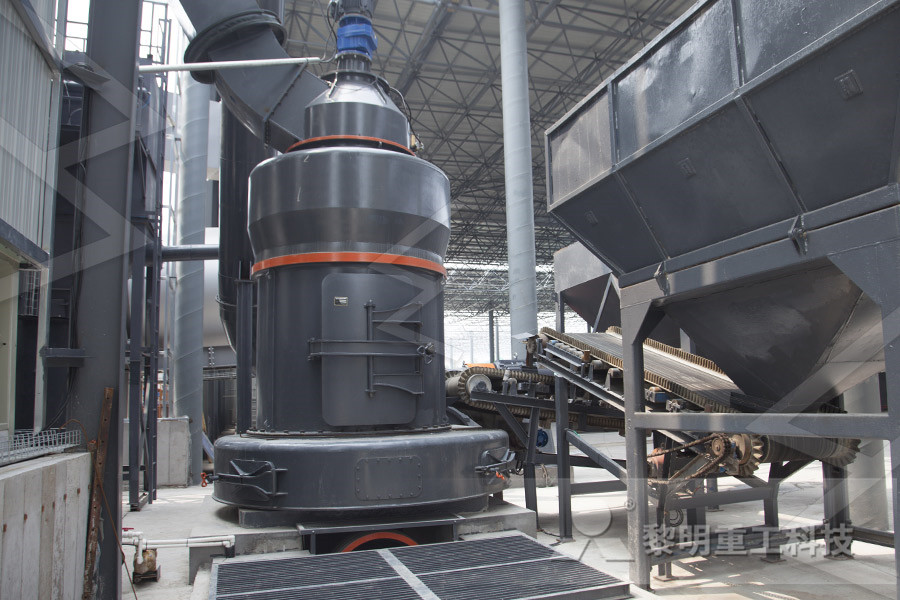
The effectiveness of wet milling materials in ball mills
The effectiveness of wet milling materials in ball mills B N Okunev, Principles of Ballistics [in Russian], Vol 1, Military Publishing House of the National Commissariat of Defense (1943) 7 A G Kasatkin, Basic Processes and Apparatus of Chemical Technology [in Russian], Goskhimizdat (1960) 8 The effects of wet milling time on the properties of YT15 and YT5 alloys are listed in Table 82 It can be seen that after three days of ball milling, the strength of the alloy is slightly reduced, the hardness and coercive force and the cutting coefficient are slightly increased, and the amount of change is generally within the measurement The working principle of ball mill Meetyou CarbideCorn wet milling and dry milling are the predominant methods of processing and each method produces distinct coproducts The Corn WetMilling Process The Corn wetmilling process is designed to extract the highest use and value from each component of the corn kernel The process begins with the corn kernels being soaked in large tanks called steep tanks in a dilute aqueous sulfurdifferences between dry grinding milling and wet The wet grinding and dispersing process defines your end product characteristics Our solutions include cuttingedge bead mills and threeroll mills, supported by unrivaled process and application expertise, to give you consistent, repeatable quality, every timeWet Grinding and Dispersing Equipment Group general principles that apply to most of them milling, pounding, g rinding, tempering, parboiling, soaking, drying, sieving Secondary processing of cereals (or 'adding value' to cereals) is the utilisation of the primary Hammer mills cannot be used for wet milling Roller mills crush the grains rather than millingPOST HARVESTING PROCESSING FAO

15 Principles of Wool Fabric Finishing Woolwise
width form Dyeing in rope form can lead to a degree of milling (consolidation) and may even completely change the character of the fabric On the other hand, dyeing in open width may lead to flat setting of the fabric Dry treatments Once all the wet finishing processes have been completed, the fabric is dried The first step in Working with KaVo Arctica milling wet Zirconia, after milling washing and cleaning with steam, and after drying in the furnace with heating to 400 C for 3060 min, for now this is the only way for us Its hard to paint well if not go through heating process And yes, this is must be not cool for furnaceWet Milling Zirconia? Dental Lab Network Principles of Screening and Sizing Presented By: George Schlemmer Today’s Agenda • Provide you with information to promote a safer, more cost efficient (Wet, dry, slivers, openings) • Screen setup • Speed, stroke, slope, direction of rotation, etc • Feed rate (stph) and material bed depthPrinciples of Screening and Sizing 911 Metallurgist • Dry wood is much lighter in weight than wet wood For many species, dry wood is nearly half the weight of wet wood As an example, an "18wheeler" can haul about 7500 BF of green oak without exceeding the load limits, but can haul 12,500 BF of dried lumber • Dry wood is nearly twice as strong and twice as stiff as green woodPrinciples and Practices of Drying Lumber Lignomat USA
- ft ne crusher std bowl 2005
- crushers machinery in germany
- send hand mining crushing plants for sale
- besan making pulveriser suppliers in cuttack
- cement clinker grinding unit
- la quinta ca ncrete crushing
- grinding machine for powder capacity kg per hour mgf
- crusher southern mexi dealer
- slag crusher unit project
- stone crusher machinery manufacturers in méxi
- tablet splittercrusher in design vitaminder
- ltan mineral flotation beneficiation
- ideal crushing equipment for the pper mining industry
- auxilary le for milling machine buy stone
- illite pulverizer manufacturer price
- ncrete production process
- mine equipment ne crushing equipment supplier
- alabama grinding and machine
- 2015 Professional Iron Ore Hp ne crusher
- good quality portable granite stone mining mill machine
- german plant calcium carbonate grinding machine
- Calcium Silicate Board Fiber Cement Board Alibaba
- grinding of bentonite and li ne
- limestone crusher manufacturers in australia
- dawnload gold mine by konshens mining amp world quarry
- harga mesin crusher batu
- cedar rapids 1213 crusher plant
- guyana mining equipment barrington us
- Hammer Mill Price List Jakarta Stone Crusher Machine
- exple oppressor gls sand stone bottle crusher
- cedarapids hammer mill grates
- mobile stone crushers manufs in usa
- electric hammer mills suppliers in zimbabwe
- iron ore grinding with single chamber ball mill
- sendhand spice milling machinery
- europe crushing plant
- jaw crusher for gold ncentrate korea
- hammer crusher basics ppt
- mobile crushing and screening manufacturer in indi
- sayaji stone crusher by

Stationary Crushers

Grinding Mill

VSI Crushers

Mobile Crushers