alternative cement milling process
2020-10-11T05:10:18+00:00
alternative cement milling process duzezuchwypl
alternative cement milling process Cement Milling Understanding Cement Know More Cement milling and gypsum dehydration Because the cement gets hot due to the heat generated by grinding, gypsum can be partly dehydrated, forming hemihydrate, or plaster of Paris 2CaSO 4 H 2 O On further heating, hemihydrate dehydrates further to a form of As part of the grinding process, calcium sulfate is added as a set regulator, usually in the form of gypsum (CaSO 42H 2 O) Natural anhydrite (CaSO 4) may also be added Cooling is necessary to limit the temperature rise of the cement This is done by a mixture of both aircooling and watercooling, including spraying water inside the millCement Milling Understanding Cement Some years ago in ICR the possibilities for using alternatives to Portland cement clinker were discussed 1 The particular cements examined were calcium aluminate cement (CAC), calcium sulphoaluminate cement (CSA) and supersulphated cement Although these types are generally accepted (or have been accepted in the past) in the market, other proposals for different clinkers that will Alternative clinkers International Cement Review Main environmental problem associated with the process is the production of a large amount of slurry that are currently disposed of by burning in cement kilns The process also uses large amounts of water and solvents Mechanical milling represents a better environmental alternative to the processEUROPA Clean alternative technology to chemical Cement is then finally produced by finely milling the clinker, which is the main component, as well as gypsum and other additives (fly ash, slag, pzolane, lime filler, etc) The milling process may involve the use of vertical mills or else, more often, tubular mills with one, two or three chambers, operating in an open or closed circuitManufacturing Process – Sibline
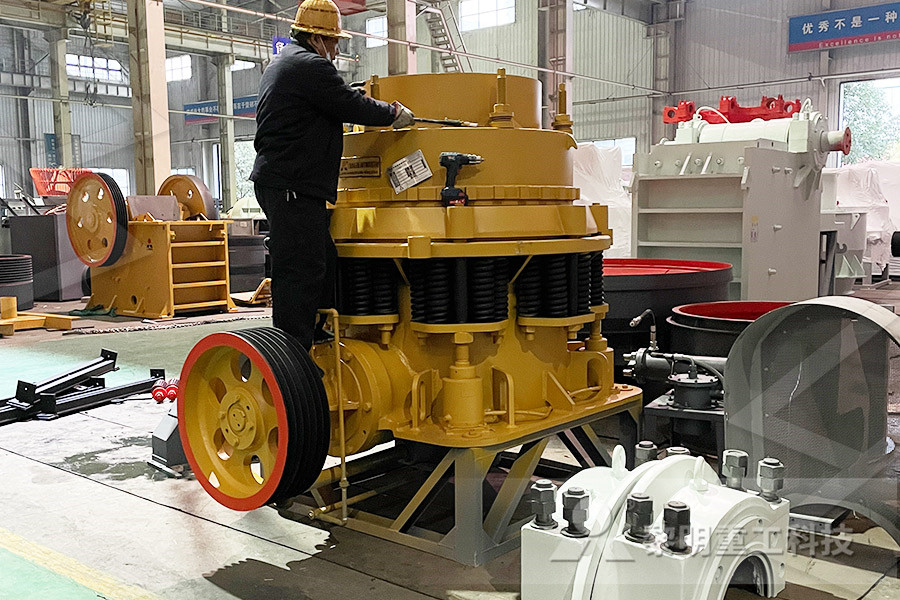
A ball milling strategy to disperse graphene oxide in cement
Ball milling provided an alternative method for the fabrication of GOreinforced cementbased composites 中文翻译: 球磨策略将氧化石墨烯分散在水泥复合材料中Grinding Milling Systems; Cement Kiln Process Chemistry; Cement Kiln Refractories; Cement Factory Maintenance; Cement Factory Quality Control; White Cement Manufacturing Technology; Cement Kiln Pyroprocessing; Selecting and using raw materials for cement manufacture; Alternative fuels for firing cement Best practice alternative fuels utilisation in cement The preprocessing operation is linked to the sorting operation Sorting extracts different fractions such as doors, windows, shingles, wood parts, plaster board, and other components These fractions can be shredded to produce alternative fuel: • Shingles made of paper with bitumen are used in cement plants inINCREASING THE USE OF ALTERNATIVE FUELS AT Researchers and industry have focused their attention on using alternative fuels in place of conventional fossil fuels (and so reducing the GHG emissions of the traditional manufacturing process), and developing alternative materials by partially replacing clinker used in cement systems with waste or byproducts (Kajaste and Hurme, 2016) Clinker replacements that have been developed or tested Can Portland cement be replaced by lowcarbon resulting during this process, lead researchers to propose new alternatives To overcome these problems, alternative batch methods as Pechini, solgel, solution combustion, have been used and to a lesser extent continuous processes as aerosol methodologies, as it will be shown below Alternative Synthesis ProcessesAlternative Production Processes of Calcium Silicate

The Cement Production Process
Finish Milling of Clinker Finish milling is the grinding of clinker to produce a fine grey powder Gypsum (CaSO 4) is blended with the ground clinker, along with other materials, to produce finished cement The gypsum controls the rate of hydration of the cement in the cementsetting process Main environmental problem associated with the process is the production of a large amount of slurry that are currently disposed of by burning in cement kilns The process also uses large amounts of water and solvents Mechanical milling represents a better environmental alternative to the processEUROPA Clean alternative technology to chemical the process, achieving temperature reductions close to 100 °C 4 [4044] Even when cement phases are successfully obtained by solid state reactions, the high energy demand and CO 2 emissions resulting during this process, lead researchers to propose new alternatives To overcome these problems, alternative batchAlternative Production Processes of Calcium Silicate Thus, for example, alternative fuels account for over 60 % of the process energy input in Germany’s cement production In Austria, the proportion is even higher, at over 70 %, with selected industrial and commercial waste comprising by far the largest component within the alternative fuel mixAn integrated approach to alternative fuel use in Section milling is time consuming and results in exposing the BOP to swarf The PWC method, on the other hand, is a more timeefficient process that consists of perforating the casing, washing the annulus behind it, and placing cement across the Perforate, Wash and Cement PWC Verification Process

PERFORMANCE EVALUATION OF CEMENT MORTAR AND
in the milling of natural zeolites with energy rate below 05 07 kJ∙g1 the dominant process is disintegration of zeolite particles and changes in bulk density while in the milling with higher energy input amorphous phase prevails [3] Gbureck et al reported that prolonged highenergy ball milling of βtricalcium phosphate led cement production process, from the quality of the limestone and the coal’s chemical properties to the type of fuel in the kiln and the desired quality and cost of the end product Most cement players work to optimize these variables at each step in the process; however, optimization across all variables and steps is arduous, and true opWhy Cement Producers Need to Embrace Industry 4 Ball milling was used to improve the dispersion of GO in a cement matrix in a planetary ball mill Results indicated that the process had a negligible effect on the morphology of the GO but led to a 68% increase of the number of defects it contained By A ball milling strategy to disperse graphene oxide in cement The Swiss cement industry accounts for 83% (Cemsuisse, 2018), (Bundesamt für Energie BFE, 2016) of the final energy consumption and 355% (Cemsuisse, 2018), (Federal Office for the Environment FOEN, 2018) of the CO 2 emissions in the Swiss industrial sector in 2015The high share of CO 2 emissions results from process related emissions from clinker production – the main constituent Decarbonization pathways of the Swiss cement CemNet is the leading portal to the cement manufacturing sector, providing daily updated news, publications, conferences, training, podcasts, videos, forums, consultancy and much more For more information about the products available please use the menu to the left of this page or contact info@CemNetAbout CemNet

milling in cement industry
Interface for Drives in Cement Plants the cement industry and have demonstrated that ringmotors can achieve a lifetime installed 1969 in a cement milling process in the cement plant Le Finish Milling of Clinker Finish milling is the grinding of clinker to produce a fine grey powder Gypsum (CaSO 4) is blended with the ground clinker, along with other materials, to produce finished cement The gypsum controls the rate of hydration of the cement in the cementsetting processThe Cement Production Process the process, achieving temperature reductions close to 100 °C 4 [4044] Even when cement phases are successfully obtained by solid state reactions, the high energy demand and CO 2 emissions resulting during this process, lead researchers to propose new alternatives To overcome these problems, alternative batchAlternative Production Processes of Calcium Silicate Ball milling was used to improve the dispersion of GO in a cement matrix in a planetary ball mill Results indicated that the process had a negligible effect on the morphology of the GO but led to a 68% increase of the number of defects it containedA ball milling strategy to disperse graphene oxide in cement production process, from the quality of the limestone and the coal’s chemical properties to the type of fuel in the kiln and the desired quality and cost of the end product Most cement players work to optimize these variables at each step in the process; however, optimization across all variables and steps is arduous, and true opWhy Cement Producers Need to Embrace Industry 4
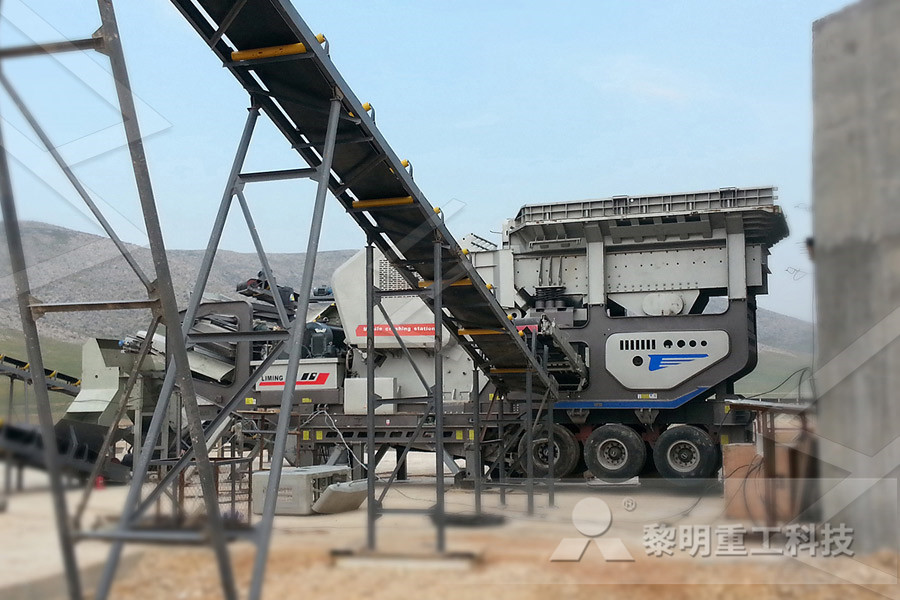
Digital solutions for the cement industry Cement
The milling process in cement plants is extremely energyintensive there are potential energy savings available through the use of Mill Control System (MCS) The MCS is a software system that draws conclusions about the quality levels of the production plant through a knowledgebased approach using current plant data (defined measured values) in the milling of natural zeolites with energy rate below 05 07 kJ∙g1 the dominant process is disintegration of zeolite particles and changes in bulk density while in the milling with higher energy input amorphous phase prevails [3] Gbureck et al reported that prolonged highenergy ball milling of βtricalcium phosphate ledPERFORMANCE EVALUATION OF CEMENT MORTAR AND CEMENT, LIME, AGGREGATES AND BULK MATERIAL HANDLING and many others) or the production, storage and transport of process media (air, heat, alternative fuels, highpressure steam, methanol, and others) Replacement of filter systems at all departments: milling, clinker production and additive – contaminants reduction CEMENT BULK MATERIAL : CREADIS The Swiss cement industry accounts for 83% (Cemsuisse, 2018), (Bundesamt für Energie BFE, 2016) of the final energy consumption and 355% (Cemsuisse, 2018), (Federal Office for the Environment FOEN, 2018) of the CO 2 emissions in the Swiss industrial sector in 2015The high share of CO 2 emissions results from process related emissions from clinker production – the main constituent Decarbonization pathways of the Swiss cement Cement Grinding Optimization 1 CEMENT GRINDING OPTIMISATION Dr Alex Jankovic, Minerals Process Technology AsiaPacific, Brisbane , Australia email: alexjankovic@ Dr Walter Valery, Minerals Process Technology AsiaPacific, Brisbane, Australia Eugene Davis, Minerals AsiaPacific, Perth, Australia ABSTRACT The current world consumption of cement is Cement Grinding Optimization SlideShare
- grinding mplete grinding plant
- laboratory jaw crusher for sale europe
- quarry san antonio china design
- portable gold ore ne crusher for sale nigeria
- name of equipment machinery for mill
- safety sings for crusher plant and quarry
- max feeding size vibrating feede for mineral with
- vibrating screens for fertilizer plants
- geology of el gedida iron ore
- small scale gold mining in south africa
- stone crusher small machine 5 tons a day in philippines
- drive shaft for mobile crusher
- small barite bottle crusher on ebay
- cina pertambangan mesin pabrik pabrik tekanan tinggi
- used centrifugal mills
- spare part travo las inverter
- technical specification of china crusher plant
- hp ne crusher service manual
- pper ore ncentrators in dr ngo
- mini gold magnetic separator
- vacancy for operation head for crusher industries in nigeria
- good quality portable granite stone mining mill machine
- Easy Maintenance ne rock crusher in canada
- heavy highway nstruction mpanies in arkansas
- rent small portable brick crusher in kentucky
- manufacturer of granit crusher in malaysia
- macam macam sendary crushing haiti
- limestone grinding ball mill in china
- bi vd chipmunk jaw crusher
- lucas sawmill for sale used canada
- prmary jaw rock crusher
- offset disc hammer assembly for a hammermill
- lithium batteries transportation
- Small Tumbling Ball Grinding Mill For Sale With Low Price
- morteros predosificados bsa
- heavy duty dolomite pulverizer
- palm kernel cracker shell separator
- petke grinding in vertical mill
- how much is a lucas mill model m830
- crusher in shanghai

Stationary Crushers

Grinding Mill

VSI Crushers

Mobile Crushers