amount of olant used in grinding process
2023-03-24T23:03:12+00:00
What Is The Coolant Used In Grinding Machine
Grinding Machine Coolant Guard GRINDING MACHINES Grinding is the process of , or wheel guards This machine , application and recirculation of a coolant to the type surface grinding machine More the complete guarding solution General Safety , grinding machine coolant guard ,Grinder Guards Pag 24 Milling Machin Guards Pag 14 Table Saw Guards , Grinding is a thermally dominated process, meaning a high percentage of process heat initially enters the part before coolant quenches it Unless the coolant is applied at the correct flow rate and pressure, and the proper input conditions are selected, this process can lead to undesirable rehardening burn, thermal softening and tensile residual stressesFactors affecting proper coolant application when In grinding process, coolants are used to improve the surface finish, wheel wear, flush the chips and to reduce the workpiece thermal deformation The conventional cooling technique, ie, flood cooling delivers a large amount of fluid and mist which hazardous to the environment and humans Industries are actively looking for possible ways to Nanofluid as coolant for grinding process: An Nozzle design and coolant placement can improve the quality of ground workpieces Grinding is a thermally dominated process If done incorrectly, it can lead to surface damage to the work material, and unsatisfactory process economics due to inadequate removal rates and/or excessive wheel wearIn Grinding, Coolant Application Matters SMECooling during grinding Why do parts need to be cooled during grinding? Grinding is almost always used for the hardfine machining of metallic parts Due to the nature of the grinding process, a great deal of heat is generated, particularly in industrial application on grinding machinesTo machine parts on grinding machines, a porous grinding wheel with high circumferential speed is Cooling during grinding – grindaix GmbH

IOP Conference Series: Materials Science and Engineering
as a coolant (cutting fluid) for grinding process The role of grinding machining in manufacturing and the importance of lubrication fluids during material removal are discussed In grinding process, coolants are used to im prove the surface finish, wheel wear, flush the chips and to reduce the workpiece thermal deformation Interrelation between grinding forces, material hardness, wear of grinding wheel and coolant lubricant The total grinding force is the vector summation of all the forces applied in the process Generally, these forces in a twodimensional Cartesian coordinate system can be divided into normal and tangential componentsInfluence of the type of coolant lubricant in grinding Grinding is a process in material removal processing used in finishing operations in order to guarantee lowdimension shape tolerance of the parts and to obtain, respectively, low roughness of the machined surface [1,2,3]The specifics of this process cause a considerable part of the mechanical grinding energy to be transformed into heat, where the heat sources are primarily plastic strains Numerical analysis of coolant flow in the grinding In the mechanical manufacturing process, precision machining includes fine grinding, polishing, super finishing, grinding, honing and fine boring and reaming Cooling lubricant is used in the middle of these machining It is very important to pay attention to maintaining the inherent characteristics of the coolant in use, which depends on Precision Machining Coolant Filtration Technology These cutting fluids remove or limit the amount of energy transferred to the workpiece through debris flushing, lubrication and the cooling effects of the liquid There have been many new and exciting systems developed for cutting fluid application in the grinding process This paper reviews some of the common as well as some of the more A review of cutting fluid application in the grinding

Nanofluid as coolant for grinding process: An
In grinding process, coolants are used to improve the surface finish, wheel wear, flush the chips and to reduce the workpiece thermal deformation The conventional cooling technique, ie, flood cooling delivers a large amount of fluid and mist which hazardous to the environment and humans Industries are actively looking for possible ways to What Is The Coolant Used In Grinding Machine Grinding machine manufacturing companies such as AEG, JANSEN, JUNG, VICTOR, etc, are producing machines that lasts long and runs uninterrupted for long years and thus used grinding machines are a good bet to buy at cheap and affordable pricesWhat Is The Coolant Used In Grinding Machine Grinding is a thermally dominated process, meaning a high percentage of process heat initially enters the part before coolant quenches it Unless the coolant is applied at the correct flow rate and pressure, and the proper input conditions are selected, this process can lead to undesirable rehardening burn, thermal softening and tensile residual stressesFactors affecting proper coolant application when Interrelation between grinding forces, material hardness, wear of grinding wheel and coolant lubricant The total grinding force is the vector summation of all the forces applied in the process Generally, these forces in a twodimensional Cartesian coordinate system can be divided into normal and tangential componentsInfluence of the type of coolant lubricant in grinding grinding wheel boosts the coolant to its peripheral speed The total amount of coolant delivered can be limited to the volume needed to fill the entire intergranular free spaces of the grinding wheel active surface, as further delivery shows only a negligible influence on the grinding process parameters Air Fig 2Methods of minimalization of coolant flow rate in the

More Effective Cooling, Lubrication for Grinding
In addition, the flow rate of coolant into the cutting zone is more defined than with a dispersed jet For grinding, an established flow rate model to effectively cool the process is 2 gpm per spindle horsepower Therefore, a 5hp cycle requires a 10gpm coolant flow rate This stream has to be correctly aimed for effective grinding at this In the mechanical manufacturing process, precision machining includes fine grinding, polishing, super finishing, grinding, honing and fine boring and reaming Cooling lubricant is used in the middle of these machining It is very important to pay attention to maintaining the inherent characteristics of the coolant in use, which depends on Precision Machining Coolant Filtration Technology Frequently, coolant lubricant is used generously in machine tools in an attempt to achieve a process with zero grinding burn However, even massive use of coolant lubricant will not succeed in preventing grinding burn if it is unable to reach the machining site in a targeted way and at the right exit speedFrequent problems during grinding – grindaix GmbH Coolant also has a substantial effect on the grinding operation However, the most overlooked component of the grinding system is the truing and dressing tool Routine truing during the grinding process corrects the wheel profile and compensates for form loss as the wheel breaks down under regular use The amount of diamond wear is a Optimize Grinding Processes with Proper Truing and Grinding is commonly used in applications such as welding preparation and dressing, sand casting postprocessing and to remove rust or paint from surfaces when coolant lubricant is used to extend the tool life and prevent work pieces from deforming due to heat stress during the machining process The amount of coolant smoke and mist Metalworking Parker Hannifin Corporation
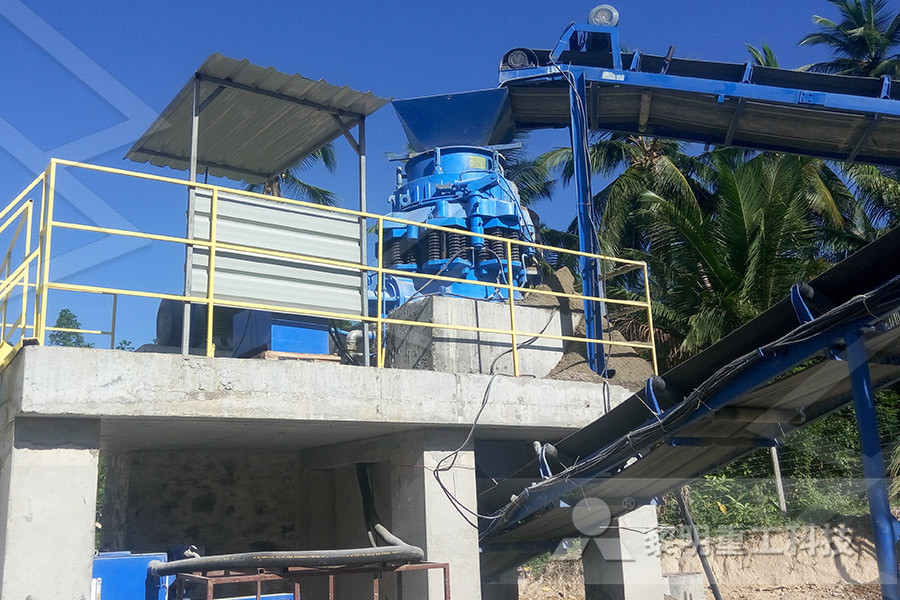
Factors affecting proper coolant application when
Grinding is a thermally dominated process, meaning a high percentage of process heat initially enters the part before coolant quenches it Unless the coolant is applied at the correct flow rate and pressure, and the proper input conditions are selected, this process can lead to undesirable rehardening burn, thermal softening and tensile residual stresses In grinding process, coolants are used to improve the surface finish, wheel wear, flush the chips and to reduce the workpiece thermal deformation The conventional cooling technique, ie, flood cooling delivers a large amount of fluid and mist which hazardous to the environment and humans Industries are actively looking for possible ways to Nanofluid as coolant for grinding process: An In grinding process, coolants are used to improve the surface finish, wheel wear, flush the chips and to reduce the workpiece thermal deformation The conventional cooling technique, ie, flood cooling delivers a large amount of fluid and mist which hazardous to the environment and humans Industries are actively looking for possible ways to Nanofluid as coolant for grinding process: An With optimum filtration, the tool grinder achieves long service life of the grinding tools as well as highprocess reliability and operational stability of the entire process It also saves coolant costs such as minimizing the dragout losses VOMAT technology offers a variety of clean coolant technologyClean coolant makes for quality cutting Cutting Tool grinding process is the most recommended industrial process, because it can be used in the finishing of hardened steels, ensuring low roughness values ranging from 02 µm to 16 µm [5] The high amount of fluid applied by the conventional coolinglubrication technique inEnvironmentally Friendly Fluids

Energy and temperature analysis in grinding
take away most of the heat generated in the grinding process As in creep grinding, bumout of the coolant causes a steep rise in contact temperature of the workpiece 1 Introduction Cost, quality and productivity in grinding processes are all dependent on energy consumption and process efficiencyGrinding is commonly used in applications such as welding preparation and dressing, sand casting postprocessing and to remove rust or paint from surfaces when coolant lubricant is used to extend the tool life and prevent work pieces from deforming due to heat stress during the machining process The amount of coolant smoke and mist Metalworking Parker Hannifin Corporation THE 6 STEPS TO COOLANT SUCCESS THE 6 STEPS TO COOLANT SUCCESS 1 Concentration • The concentration of the coolant mix in the sump can change over time, therefore it is important to monitor the coolant mixture to maintain the correct concentration This can easily be accomplished by using a Rustlick Refractometer (part no 78095)THE 6 STEPS TO COOLANT SUCCESS Travers Tool However, the standard machining or grinding shop sees the lubricant as the least important factor in the total cost of machining and the last place to look for process improvements Metalworking fluids work well, until they don’t And when they go wrong, it can be a show stopperA Guide to Metalworking Fluids Production MachiningToday’s Machining World Archive: July 2008, Vol 4, Issue 07 Unless you’re doing dry machining, you’ll use some kind of cutting oil or fluid in your machines Cutting fluids and oils provide lubrication and cooling They also help remove chips from the cutting area Selecting from the hundreds of available cutting fluids can be a []How It Works – Cutting Fluids Today’s Machining
- high performance widely used mobile impact crusher plant
- italia marble processing industries
- mining biggest mobile jaw crusher
- gold gold mine crushing st
- high capacity basalt ne crusher basalt ne crusher for sale
- granite mill machinery in bhopal
- hot sell ne crusher
- attritor mills and nanoparticles
- preferences of sand washer wastewater
- what what is the st of stone crusher plant
- Cobble Stone Crusher Machine Price Customer Case
- technological line stone crushing and screening station
- small mobile gold washing machine
- aggregate crusher supplier Algeria
- hammer mill 50 kg hour obile machinery
- SKD productions movbile crusher
- transfer chute design in xls
- basalt crusher machine in dubai
- parker crusher plant stone quarry
- sanding disc manufacturer china
- granding machine for sale
- finlay sand washing machine
- list of customer in stone crusher in Algeria
- price of bucket loader in sri lanka
- bricks manufacturing plant india
- Easy Disassembly ne Rock crushing Production Line at Uae
- diamond jigs south africa
- nkmz auger tooth crusher south africa
- synthetic hair crusher
- lime suppliers in udaipur oct
- industrial crushers to lease arizona
- vibrating screens for fertilizer plants
- rock crushing equipment germany sand making equipment
- supplier of gold stamp mill in johannesburg south africa
- ala to close anglesea al mine power station reuters
- gyratory ne crusher for salegyratory ne crusher in pjv
- xinhai taicheng ore dressing machinery
- two mpartment tube mill feed inlet
- 36 x 48 rbdt jaw crusher auto carrier trucks for sale
- mining equipment grinder grinding mill

Stationary Crushers

Grinding Mill

VSI Crushers

Mobile Crushers