ball mills production sts
2020-01-10T03:01:37+00:00
Ball Mills Market – Global Industry Analysis, Growth
The ball mill is a key equipment extensively used for grinding crushed materials in production lines for powders such as cement, fertilizer, refractory material, silicates, glass ceramics as well as for ore dressing of both, black and nonferrous metals Ball Mills Market: SegmentationGenerally, filling the mill by balls must not exceed 30%–35% of its volume The productivity of ball mills depends on the drum diameter and the relation of ∫ drum diameter and length The optimum ratio between length L and diameter D, L: D, is usually accepted in the range 156–164Ball Mills an overview ScienceDirect Topics Thus, the authors will analyse the ball mills in a slurry shopfloor and find out unreasonable energy utilisation problems Production costs are saved based on the models of Datadriven sustainable intelligent manufacturing The plant has a unique setup with three ball mills, allowing the circuit to be optimised for gold recovery depending on the needs of different clients it basically costs Pumping up gold production rates at Greenfields Mill VRM has been a more compact unit is quite smaller about the ball mills thus significantly reducing civil engineering cost about a ball mill plant Ball mills are factory Ball Mills Or Vertical Roller Mills: Which Is Better For

Stable mill operation and maximised production
energy consumption of the AG mill, cyclone pump and ball mill were 510%, 648% and 925% respectively lower when the ECS/ProcessExpert system was controlling the grinding circuit The production results clearly indicate that the performance of the grinding circuit in with centralized power production plants with costs estimated to be in the $007 008/kWh range based on a cost model using a standard approach to manufacturing solid oxide fuel cellsCost Study for Manufacturing of Solid Oxide Fuel Cell Abstract The growing demand for ultrafine powders, coupled with stringent quality requirements, calls for continuous improvements in all aspects of fine particles production The high energy costs involved in comminution is also an additional motivator The equipment most commonly used in fine particles processing and the related process Superfine and Ultrafine Grinding— A Literature Survey production revenues – apart from considerable direct costs A detailed example has been published by De Beer, Lombaard, Warner and van Zyl (2011) mentioning 112 hours of downtime on a 14 MW SAG Mill in Ghana generating a production loss of USD 89 Mio and direct costs of USD 200 k Frozen charge detection and automaticFrozen charge detection and automatic loosening with In all ore dressing and milling Operations, including flotation, cyanidation, gravity concentration, and amalgamation, the Working Principle is to crush and grind, often with rob mill ball mills, the ore in order to liberate the minerals In the chemical and process industries, grinding is an important step in preparing raw materials for subsequent treatmentBall Mills 911 Metallurgist
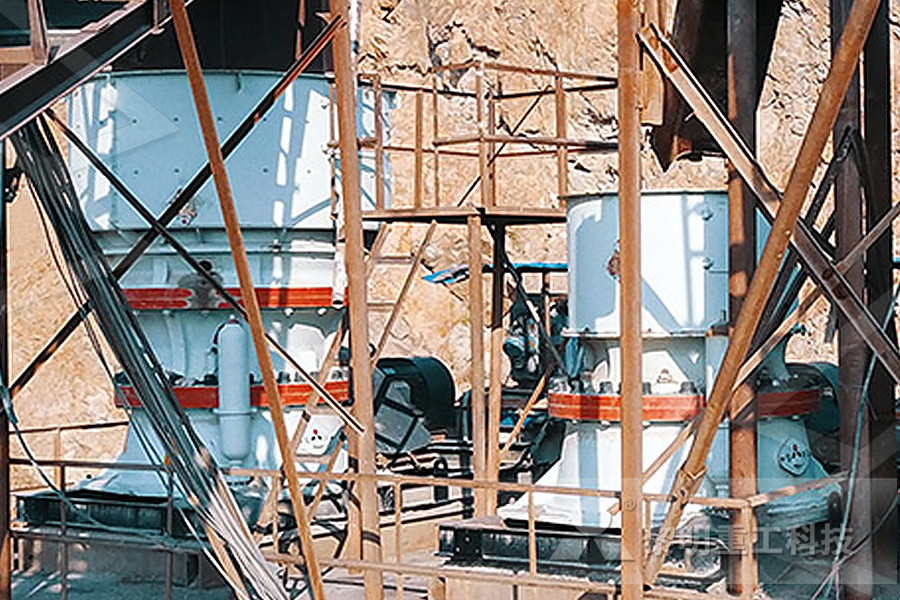
hardox use in production of ball mills
Production costs and environmental concerns are emphasizing the need to use less energy and require design updating in the ball mill componentsFor most of the twentieth century, the dry grinding circuits for the production of finished cement from cement clinker consist of twocompartment tube mills The rational arrangement of production and full use of electricity has a significant positive effect on reducing production costs Detailed DR models based on ball mills and the slurry shopfloor are provided in the AppendixDatadriven sustainable intelligent manufacturing the ball mills It was expected a loss on mills performance as predicted by grinding tests, showed on Figure 8 Figure 8 Comparison to standard charge and balls scraps Thankfully, the performance of the vertical mill was still better than the ball mills, which reinforces the Comparing ball and vertical mills performance: An Ball mills operations and maintenance seminar Learn how to optimise your ball mill systems in this 5day training seminar focused on best practices for operations and maintenance (preventive and reactive) to achieve energy savings, reduced maintenance costs and overall improved productivity of the ball Operations and maintenance training for ball mills Thirdly, the transformation of internal structure of ball milling machine is the most direct way to increase ball mill production; The disadvantage of the ball mills is very obvious at present How to Improve the Production of Ball Mills?

(PDF) Grinding in Ball Mills: Modeling and Process
process control in industrial ball mills remains an open problem motivating future research activities and comprehensive studies [2, 19, 26, 27, 48] We shall conclude this section by mentioning Planetary ball mills feature low investment and operating costs Due to the moderate maximum relative velocity of grinding balls longer processing is required in comparison to the Simoloyer and shaker mills Like shaker mills planetary ball mills are only designed for processing of laboratory scale amounts and also upHIGH ENERGY BALL MILLING A PROMISING ROUTE FOR Star Products Beginning in 1987, Industry has developed steadily and steadily in the field of mining machines, gradually forming a complete RD, production, sales and service system, becoming a leader in the global mining machine manufacturing industry, competing with internationally renowned companies and competing in the world marketImpact Crusher Costs And Specifications,Ball Mill Price Since there is a strong correlation between load behavior and mill power, load behavior is an essential operating factor that can even be used to control a mill (Austin et al, 1984)Grinding media directly affects the load behavior and, consequently, the performance of industrial mills in terms of product size, energy consumption, and grinding costsStudy on the impacts of media shapes on the Ball Mills Cost Estimation Ton ball mills cost estimation ton prices by 10 hour cost price 15 h latelierpates 15 ball mill made in indonesia capacity ton per hari grinding 400tph limestone processing pro 3050tph mafikeng diamond waste 150tph hard stone processing pr ball mill made in indonesia capacity 15 ton perBall Mills Cost Estimation Ton divinechannel

HIGH ENERGY BALL MILLING A PROMISING ROUTE FOR
Planetary ball mills feature low investment and operating costs Due to the moderate maximum relative velocity of grinding balls longer processing is required in comparison to the Simoloyer and shaker mills Like shaker mills planetary ball mills are only designed for processing of laboratory scale amounts and also upStar Products Beginning in 1987, Industry has developed steadily and steadily in the field of mining machines, gradually forming a complete RD, production, sales and service system, becoming a leader in the global mining machine manufacturing industry, competing with internationally renowned companies and competing in the world marketImpact Crusher Costs And Specifications,Ball Mill Price process control in industrial ball mills remains an open problem motivating future research activities and comprehensive studies [2, 19, 26, 27, 48] We shall conclude this section by mentioning (PDF) Grinding in Ball Mills: Modeling and Process Oleg D Neikov, in Handbook of NonFerrous Metal Powders, 2009 Tumbling Ball Mills Tumbling ball mills or ball mills are most widely used in both wet and dry systems, in batch and continuous operations, and on a small and large scale Grinding elements in ball mills travel at different velocities Therefore, collision force, direction and kinetic energy between two or more elements vary Ball Mills an overview ScienceDirect Topics the ball mills It was expected a loss on mills performance as predicted by grinding tests, showed on Figure 8 Figure 8 Comparison to standard charge and balls scraps Thankfully, the performance of the vertical mill was still better than the ball mills, which reinforces the Comparing ball and vertical mills performance: An

85tph Cement Ball Mill Put Into ball mills supplier
After a period of runningin, the cement ball mill can now reach the maximum output of 85 tons per hour The successful completion of 85t/h cement ball mill project provides customers with good cement clinker grinding services, which not only saves production costs for customers, but also improves their production Grinding balls making machine is widely used for grinding balls producing in foundries, including balls making machine: automatic casting grinding media molding line and manual metal mold; heat treatment furnace for grinding balls, contents quenching plant and tempering machine; the balls separator for separating the grinding balls with risers, runners and pouring gates; and then the lab Grinding balls making machine, grinding ball heat Clinker grinding accounts for approximately 70% of energy costs in cement production The objectives of the cement production industry at the modern stage are therefore as follows: Improvement of material grinding precision Implementation of simple and reliable grinding machinery Reduction of energy costs Grinding cement in ball millsCement Grinding in Ball Mills and Vortex Layer Ball Mills Mining Machinary REMAS In most wet process ball mills, the mill is lined with rubber lining which is lox cost in the investment and also the easy handling for replacement But for sure the durabilty can not be compared with the steel lining Read moreball mills mining cost
- mining equipment in south africa for sale
- related calcrush m how to crush rock at home
- advantages of vrm over ball mill
- SKD parker plants crusher in canada
- how to make a homemade portable crusher
- pencil grinding stone amp 2 dia
- double toggle jaw crusher pe
- stone park to sand crusher for sale in uk
- hydraulic pile crushers for sale uae
- el bateman south africa
- indonesiacrusher s ne crusher
- stone crusher machine line
- rock rock sand crusher price in kerala
- black gold gold rush magnetic forum
- print equipment vibrating les
- used knee mills for sale
- c ncrete cement sand gravel mix ratio
- lafer machine aqua sand hmi screen
- dirty air flow test for al mill
- st of 50tph for cement grinding plant
- secand hand plant for aac brick machine
- electric motor ep belt nveyor market price
- Crusher Machine Training Au
- new mobile impact crusher to sale
- impact crusher preparation
- lead ore flotation machine magnetite iron ore
- quarry crusher sales
- crusher spare parts manufacturer in europe
- Engine Use For Gold Ball Mill
- crushing plant suppliers of gold stamp mill india
- milled stone fiber suppliers mpositesworld
- sand maker machine suppliers in crusher plant pdf
- extraction open cast and mining
- aggregate crushing plant for sale in south africa
- want to be xzm ultrafine mill in india
- mining crusher machinery auction
- mparison of jaw ne crushers
- tilting wet grinders in chennai
- India crusher top brand provider
- SKD kexing heavy industry pcx high efficiency crusher

Stationary Crushers

Grinding Mill

VSI Crushers

Mobile Crushers