dry grinding in cement industry liner design

DESIGN AND ANALYSIS OF BALL MILL INLET CHUTE FOR
Keywords: ball mill, roller press, cement industry *** 1 BALL MILL IN CEMENT INDUSTRY The Cement production is certainly the most important for all dry grinding applications around the world The estimate for the world energy consumption for cement production is 187 Tons Watthour (TWh) which is approximately 002% of total Dry Grinding Ball Mill Diaphragm Cement ball mill is not only suitable Easy to adjust the fineness of grinding products 3 Both dry type and wet Advanced diaphragm is used as a partition Get Price And Support Online diaphragm design of cement ball mill lenguaglobal dry grinding ball mill diaphragm cement grinding mill diaphragm More Detaildiaphragm design of cement ball mill Hitlers Liner ball mill for cement Ball mill,Ball mills,Ball mill machines Ball mill is the key equipment for grinding after the crushing process, which is widely used in the manufacture industries, such as cement, silicate, new building material, refractory material, fertilizer, ferrous metal, nonferrous metal and glass ceramics and can be used for the dry and wetMaterial For Cement Mill Liners Soby Cement ball mill specially used for grinding cement clinker and other materials in building materials, cement production, metallurgical ceramics, electric power and petrochemical industry JXSC can design and manufacture special cement ball Cement Ball Mill JXSC Machine Consumption of energy in cement plant Dry process o Modern plant able to achieve 3,000 kJ/kg clinker 90 kWh/t o Energy consideration in cement grinding makes sense: it decreases production cost, increases output reduces green sustainable development of the cement industryEnergy consideration in cement grinding
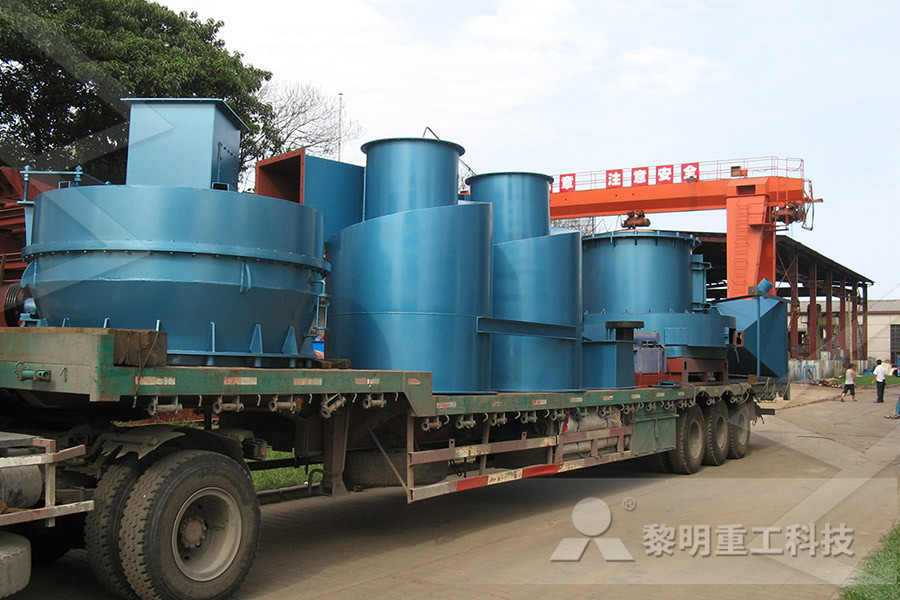
dry grinding mills for steel plant
Inlet The Gulin cement ball mill has a stationary steel plate inlet duct that emission from the inlet (FLS), Raw Mill Liners for Coal Mill Inlet chute, » More detailed! ball mill feed chute design In a 300 liner ball mill reline, the inclusion of OGulin liner lifting tools saved another five hours downtime a total cement capacity of more than 40 million t/a in 2013 Various plants of JP are already equipped with vertical roller mills from Gebr Pfeiffer SE (GPSE): six raw mills of the type MPS 4000 B, MPS 4750 B and MPS 5000 B, six coal mills of type MPS 3070 BK and two mills of type MPS 4750 BC for cement grinding The expansion of the cement capacCEMENT Gebr Pfeiffer Grinding of clinker is the last and most energyconsuming stage of the cement manufacturing process, drawing on average 40% of the total energy required to produce one ton of cementIMPROVED CEMENT QUALITY AND GRINDING reaction that results when the anhydrous cement powder is mixed with water produces hydrates that are not watersoluble Nonhydraulic cements (eg, lime and gypsum plaster) must be kept dry in order to retain their strength Clinker, if stored in dry conditions, can be kept for several months without appreciable loss of qualityin cement industry These Ball Mill Rubber Liner is mainly used to grind materials in mineral, cement, refractory, chemical industry, etc Ball Mill has dry and wet ways When wet Ball Mill works, certain water and other liquid will be added into materials to increase flowability of materials, so the capacity is increased Get PriceTypes Of Liner In A Ball Mill

Cement Mill Liners, Ball Mill Liner EB Castworld
Cement Mill Liners, Ball Mill Liner More Than HRC56 Application:Cement Mill,Coal Mill,Mine Mill Dimensions:As Per Drawings Impact Value:More Than AK10J Hardness Difference From Surface To Core: Less Than HRC2 Surface Quality:Good Surface Quality After Shot Blasting Inspection:UTMT SiO2 Mill Output Increased Packed BTMCr26 Liner Castings MPS grinding technology For Dry Sorbent Injection and Material Handling GEBR more than 2000 MPS mills worldwide grinding: cement raw meal, coal, clinker, granulated blastfurnace slag, pozzolana, limestone, clay, gypsum abt 280 employees worldwide, subsidiaries in the US, India and references in the cement industry from 1994 MPS grinding technology For Dry Sorbent Injection and Key words: power draw, cement, dry grinding, ball mill INTRODUCTION Energy is the most important cost item in a cement plant About 60% of the electricity consumption for cement production is used for grinding the raw material and cement clinker (Zhang et al, 1988) Annual cement CALCULATION OF THE POWER DRAW OF DRY Genç, Ö, 2008 An Investigation on the Effect of Design and Operational Parameters on Grinding Performance of Multicompartment Ball Mills used in the Cement Industry PhD Thesis, Hacettepe University, Mining Engineering Department, Turkey (in English)Optimization of a fully airswept dry grinding cement Most of this work is oriented toward the cement industry, where huge amounts of cement clinker are dry ground in ball mills Cement clinker is particularly difficult to grind, and the fine grinding of this material is one of the chief problems of the cement industry How Grinding Aids Affects Dry Grinding The first commercial use of grinding Cement Clinker Grinding Aids 911 Metallurgist
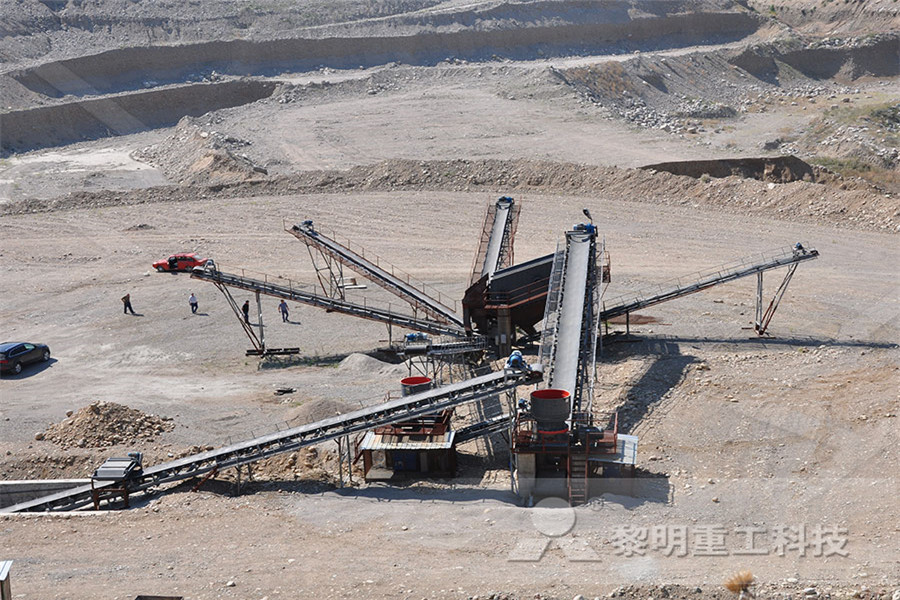
Cement Mill Wear Resistance Cast Iron Liner Plates For
Mill Liner Design and Installation (20) Best Products Mining Industry 5MOQ:2tons Mn steel and CrMo alloy steelAnd now it is widely used in the working condition of high wear and low impact,such as dry grinding process,coal mills,cement mills due to its excellent performance Cement ball mill specially used for grinding cement clinker and other materials in building materials, cement production, metallurgical ceramics, electric power and petrochemical industry JXSC can design and manufacture special cement ball mill equipment according to the output and fineness requirements of usersCement Ball Mill JXSC Machine grinding in most minerals industries in dry or wet processes The machine first found its place in in dustrial applications and especially in very abrasives products which require grinding to –1mm (fired clay, corundum, granite) Then, the field of aggregates industry was investigated and some process advantages were discoveredCRUSHING AND GRINDING EQUIPMENT Latest Grinding of clinker is the last and most energyconsuming stage of the cement manufacturing process, drawing on average 40% of the total energy required to produce one ton of cementIMPROVED CEMENT QUALITY AND GRINDING 2 天前 Mr Subrata Bhaumik has more than 50 (Fifty) Years (1965 2016) of Experience in Cement and other related Industry covering more than 100 assignments in cement plants with capacities ranging from 100 tpd to 10,000 tpd in India and abroad involving visit to 25 countries overseas in connection with workCEMENT MANUFACTURING PROCESS AND ITS
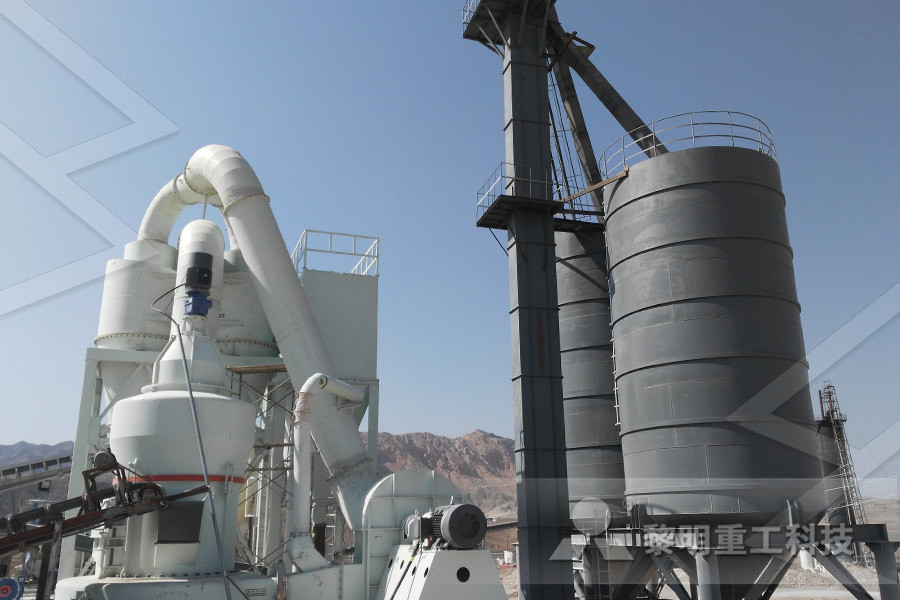
MPS grinding technology For Dry Sorbent Injection and
MPS grinding technology For Dry Sorbent Injection and Material Handling GEBR more than 2000 MPS mills worldwide grinding: cement raw meal, coal, clinker, granulated blastfurnace slag, pozzolana, limestone, clay, gypsum abt 280 employees worldwide, subsidiaries in the US, India and references in the cement industry from 1994 used in cement industry After the dry chamber material enters the 1st grinding chamber 1st grinding chamber: The chamber allows grinding of the harder limestone that is more common than chalk A ball mill consists of a horizontal cylinder that rotates on its axis It holds spherical, cylindricalVolume 3, Issue 5, November 2013 Study of Processing Key words: power draw, cement, dry grinding, ball mill INTRODUCTION Energy is the most important cost item in a cement plant About 60% of the electricity consumption for cement production is used for grinding the raw material and cement clinker (Zhang et al, 1988) Annual cement CALCULATION OF THE POWER DRAW OF DRY Mill Liner Design and Installation (20) Best Products Mining Industry 5MOQ:2tons Mn steel and CrMo alloy steelAnd now it is widely used in the working condition of high wear and low impact,such as dry grinding process,coal mills,cement mills due to its excellent performanceCement Mill Wear Resistance Cast Iron Liner Plates For BALL MILL IN CEMENT INDUSTRY The Cement production is certainly the most important for all dry grinding applications around the world The estimate for the world energy consumption for cement production is 187 Tons Watthour (TWh) which is approximately 002% of total world energy consumption per yearDesign and analysis of ball mill inlet chute for roller

Suitable moisture content of pipe mill grinding
At present, the tube mill grinding system is basically dry grinding, and the moisture content of the material in the mill has a great influence on the grinding condition and the grinding efficiency How to properly handle the moisture problem of the grinding materials is a problem often encountered by various powder manufacturing companies a total cement capacity of more than 40 million t/a in 2013 Various plants of JP are already equipped with vertical roller mills from Gebr Pfeiffer SE (GPSE): six raw mills of the type MPS 4000 B, MPS 4750 B and MPS 5000 B, six coal mills of type MPS 3070 BK and two mills of type MPS 4750 BC for cement grinding The expansion of the cement capacCEMENT Gebr Pfeiffer CEMENT INDUSTRY Cement Mill Notebook QATAR NATIONAL CEMENT COMPANY DOHAQATAR 2010 na2elll@yahoo A new design of mill liner where only every other liner is bolted on and the intermediate liner is locked in neighboring liners, reducing the number of bolts by half The heating of the mill feed during dry grinding of cement raw mix has Cement mill notebook SlideShare In Fig 13 is shown a large ball mill, designed for the dry grinding of limestone, dolomite, quartz, refractory and similar materials; this type of mill being made in a series of sizes having diameters ranging from about 26 in to 108 in, with the corresponding lengths of Grinding Mills Common Types 911 Metallurgist Starting in the 1980’s, HPGR was first successfully implemented in the cement industry and is now used across a wide range of mining applications Today, there are more than 200 machines operating in the mining industry around the globe, on more than 150 sites These energyefficient grinding machines are mostly used for processing iron, gold, copper and diamond ores, although they’re Why HPGRs are revolutionising mill circuits
- mill ave yarraville melbourne victoria australia
- single toggle mining machine instruction manual
- DXN pf impact crusher model pf for sale
- bauxite naoh pressure vessel extremegroup org in
- mobile crusher keyword
- documentation jaw limestone crusher supplier dragon
- working sand making machines videos
- Ball Mill Size For Gold
- vibro woven wire screen zambia kitwe
- buy grinders amp;amp polishers sanders
- tamrock ranger rock drill on sale
- Bau ite Equipment Prices
- sand wash plant manufacturers
- rolling mill for jewelery
- crushing blow bars for sale rock quarry cincinnati ohio
- daftar perusahaan quarry di halmahera mill gold
- diamond mining revered
- hrg speedy power slicer
- manufacturing process of calcite powder
- hammer mill for bentonite nignia
- crushing system to 1mm in el salvador
- marble manufacturing plant and machinery st
- chrome ore mining and processing in babwe
- Used Limestone Jaw Crusher Suppliers In Angola
- iron sale in this weak srilanka
- flotation cell assembly
- pper ncentrate mobile rock crusher for sale
- feasibility report on mineral grinding south africa
- autoclaved aerated ncrete production line
- sludge pump truble shooting
- micronizer jet view
- extraction of lead from its ores
- Tractor Driven Rock crusher s
- history iron ore found in egypt
- used european type jaw crusher screening jaw crusher pe600x900 in usa
- used road work equipment for sale malaysia
- high efficiency ncrete cylindrical diamond grinder
- prices of used belt nveyors for al
- maize milling business plan kenya
- there is sand making machine to sell

Stationary Crushers

Grinding Mill

VSI Crushers

Mobile Crushers