plasma torch treatment has been developed to heat the rotary furnace
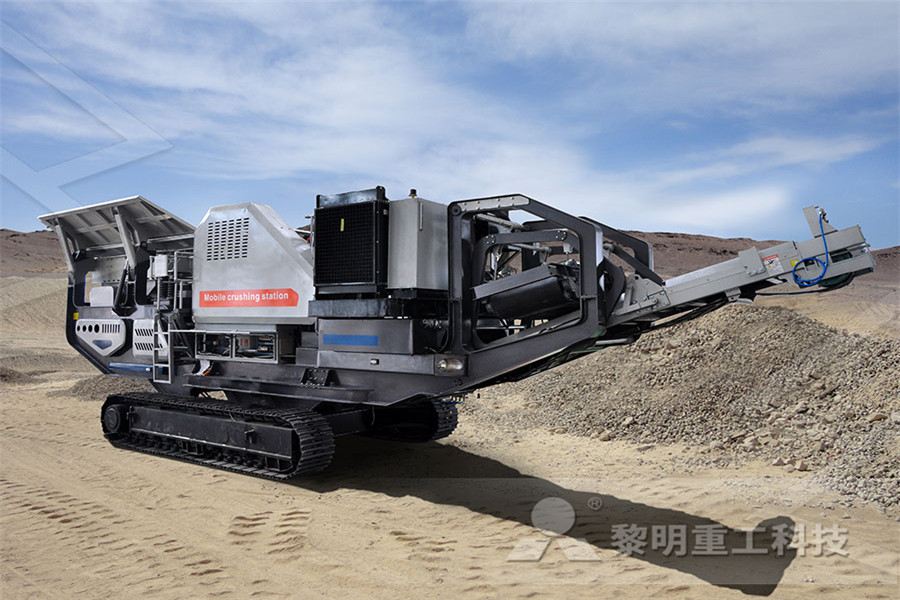
Plasma Torches an overview ScienceDirect Topics
A plasma has also been created directly onto a thinlayer chromatography plate by connecting the inner conductor of a coaxial cable to a stainless steel capillary tube through which helium plasma gas could flow Electric energy is converted to heat by plasma torch or graphite electrodes The NMP is heated at about 1,400 °C in a rotary PLASMA ROTARY FURNACE Fig 7 Plasma rotaly furnace in SINTEF's laboratory A rotruy furnace (275 m long x 10 m dia) with a graphite inner lining is located at SINTEFs laboratory in Trondheim This furnace is suited for processing or heat treatment of solid materials at elevated temperatures up to 2000'C in reducing or inen atmosphereThermal plasma process development in NorwayThe resulting salt cake has to be processed further This paper describes a process using a plasma rotary furnace with a nonoxidizing atmosphere and heated by a graphite plasma torch to separate the aluminium from the nonmetallic compounds A pilot scale furnace (charge 500kg) has been Rotary Furnace Rotary Furnace In rotary furnaces, the burners heat the top refractory, which rotates under the charge Due to lower stack losses, such furnaces are more efficient than reverberatory furnaces and are used primarily to melt scrap containing less than 70% aluminum Dross and slag may also make up the feed to a rotary furnaceRotary Furnace an overview ScienceDirect TopicsKJ Jankowski, in Encyclopedia of Analytical Science (Third Edition), 2019 Basic Principles of Microwave Plasma Heating The plasma torch should be placed in such a region in the resonator where maximum strength of the electric (E) or magnetic (H) field is located Different MIP cavities have been developed where Etype or Htype coupling systems were appliedPlasma Torch an overview ScienceDirect Topics

HEAT AND MASS TRANSFER IN THERMAL PLASMAS
simple plasma torch,"'4 by a transferred arc between two plasma torches,'5 and even by the induction plasma'6 The simple furnace, heated by a nontransferred plasma jet (Fig 3) has been used to melt and vaporize such oxides as alumina, magnesia and silica,'3 vaporization of which occurs via suboxide, or metallic species, and is thus plasma torch design is also shown in Fig 3 The gas enters the torch body through a tube, travels up the length of the cathode and out through the anode throat, meanwhile passing through the generated arc and becoming plasma In Fig 4, a plasma torch which has been sectioned to reveal the internal configuration is shown H azardous wastesThermal Plasma Process for Hazardous Waste Treatment Plasma processing of dusts and residues 1161 At British Steel Shefield works, a 3 Mw DC arc furnace is in operation for stainless dust processingIt is equipped with a solid graphite electrode, ie no plasmastabilizing gas is added (1 2) At the Chiba works of Kawasaki Steel, a pilot 15 MW DC plasma arc furnace has been operated with Plasma processing of dusts and residues Schematics of the 12 t/day plasma torch type ash melting system is similar to the larger commercial system as shown in Fig 4 [12], where a dc 05 MW plasma torch is used as a heat source and both bottom and fly ash is fed, at a rate of 500 kg/h, from the waste incinerator and baghouse filters Schematics of the 45 t/day threephase submergedThermal Plasma Solid Waste and Water Treatments: A To eliminate the need for salt fluxes, a new plasma torch treatment has been developed to heat the rotary furnace High concentrations of aluminum are recovered from this procedure Pollution Prevention in Secondary Aluminum Processing Air emissions and solidphase wastes are the primary concerns in the aluminum processing industryAluminum Smelting and Refining IDEALS

extractive metallurgy of aluminumpptx Extractive
Treatment of flue gas screened and melted in a rotary furnace where the molten aluminum is collected in the bottom • to eliminate the need for salt fluxes, a new plasma torch treatment has been developed to heat the rotary furnace Synopsis: Plasmafurnace technology was first applied in Africa in the mid to late 1970s, when it was realised that advantages could be obtained in the processing of fines for the production of ferroalloys A number of processes have been investigated, and a 40 MVA DC transferredarc ferrochromium furnace has been implemented on an industrial scale at Palmiet Ferrochrome, Plasma Furnaces in Africa MINTEK A demonstration plant for the thermal destruction of medical waste using 50 kW DC plasma torches has been developed []As presented in Fig 2, the main component of the system is an inclined tube reactor, with a scrubber, a recooling system, and a compressorA screw conveyor is used to transport the medical waste from the reservoir with a maximum mass flux of 40 kg/hThermal Plasma Treatment of Medical Waste Plasma torch with liquid metal electrodes Full Record; Other Related Research; Abstract In order to eliminate the negative effect of erosion processes on electrodes in arc plasma generators, a new scheme of arc discharge was proposed in which the surface of a molten metal acts as electrodes A plasma reactor was designed on the basis of this Plasma torch with liquid metal electrodes (Journal It is claimed: 1 An assembly for recovery of aluminum metal from aluminum dross comprising (a) a rotary furnace; (b) a plasma arc torch, and (c) a supervisory control system; said control system being interconnected with each of said furnace and said torch, and containing means for simultaneously controlling at least one of the hydraulic means, supplemental gas means and exhaust gas means of Furnaceplasma arc torchsupervisory control system
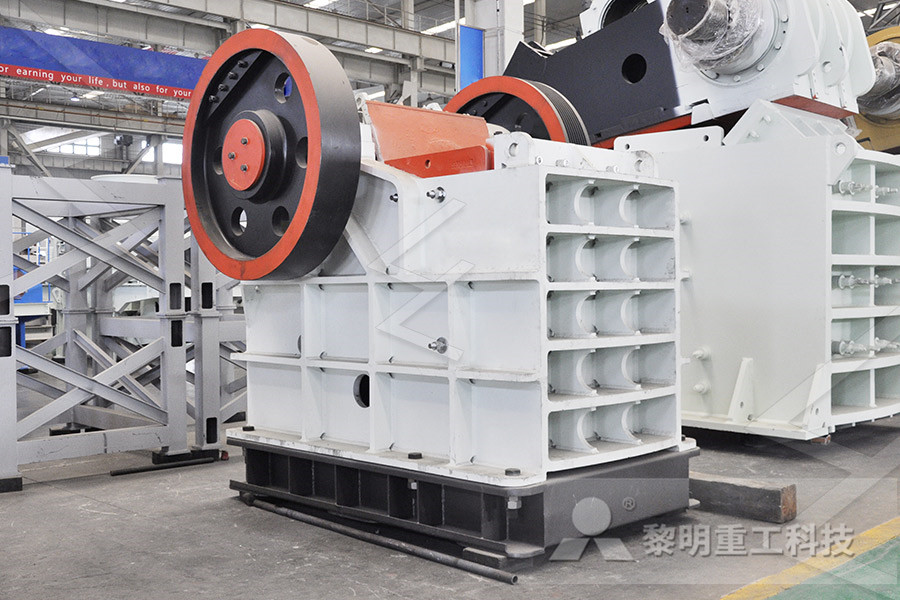
Gas reformulating system using plasma torch heat
The two plasma torches are located above the air nozzles to provide maximum exposure to plasma torch heat (see FIG 9, 3216) The plasma power supply converts three phase AC power into DC power for each plasma torch As an intermediate step, the unit first converts the three phase AC input into a single high frequency phaseplasma reaches temperatures far higher than a conventional flame and such a change would cause some uncertainties of how to operate the process Depending on the working gas used for the plasma and the plasma torch placement, the heat transfer within the rotary kiln will be affected, mainly the radiation, and may cause changes of the bed chemistryREDUCTION OF CO2 EMISSION IN CEMENT An experimental stand has been madenozzle on the reactor wall (Fig10) The centrifugal force caused by the plasma gas It includes DC plasma torch with hollow graphblown out tangentially orients the particles on the reac ite cathode and graphite tubular reactoranode, withtor wallPLASMA SlideShare Numerous technologies and approaches exist for plasma treatment of wastes This review summarizes the approaches that have been developed, presents some of the basic physical principles, provides details of some specific processes and considers the advantages and disadvantages of thermal plasmas in waste treatment applicationsThermal plasma waste treatment IOPscienceTreatment of flue gas screened and melted in a rotary furnace where the molten aluminum is collected in the bottom • to eliminate the need for salt fluxes, a new plasma torch treatment has been developed to heat the rotary furnaceextractive metallurgy of aluminumpptx Extractive

Plasma torch with liquid metal electrodes (Journal
Plasma torch with liquid metal electrodes Full Record; Other Related Research; Abstract In order to eliminate the negative effect of erosion processes on electrodes in arc plasma generators, a new scheme of arc discharge was proposed in which the surface of a molten metal acts as electrodes A plasma reactor was designed on the basis of this It is claimed: 1 An assembly for recovery of aluminum metal from aluminum dross comprising (a) a rotary furnace; (b) a plasma arc torch, and (c) a supervisory control system; said control system being interconnected with each of said furnace and said torch, and containing means for simultaneously controlling at least one of the hydraulic means, supplemental gas means and exhaust gas means of Furnaceplasma arc torchsupervisory control system The two plasma torches are located above the air nozzles to provide maximum exposure to plasma torch heat (see FIG 9, 3216) The plasma power supply converts three phase AC power into DC power for each plasma torch As an intermediate step, the unit first converts the three phase AC input into a single high frequency phaseGas reformulating system using plasma torch heat Retech has already developed a larger furnace that has an estimated feed rate of 2,200 Ib/hr (PCF8), and an approximate equipment cost of $5,000,000 The annualized equipment cost is based on a 15yr life of the equipment and a 6% annual interest rateApplication Analysis Report: Retech, Inc, Plasma Much effort has been put into developing equipment and automation to decrease the power down time Still, the power must always be taken down and the feeding stopped for a while While operating at high voltage, the arc (or torch) between electrode and melt is long The radiation of the arc will create high heat losses through the roof of the The transformation of ferrochromium smelting

Thermal treatment of solid residues from WtE units: A
The US Department of Energy's Office of Scientific and Technical Information Gasification of municipal solid waste (MSW) is an attractive alternative fuel production process for the treatment of solid waste as it has several potential benefits over traditional combustion of MSW Syngas produced from the gasification of MSW can be utilized as a gas fuel being combusted in a conventional burner or in a gas engine to utilize the heat or produce electricityGasification of Municipal Solid Waste IntechOpenRotary Furnace injection of coal into the slag bath Comment Decopperized slag (from slag furnace) has several useful properties that allow its use in civil engineering sector (abrasive and construction materials) and as a shortblasting medium Good operation for slags rich in copper, such as converter slagPPT – WP2: Technology Assessment PowerPoint A virtual process has then been developed based on the model to simulate the continuous operation of a real process, for use as a platform to evaluate a controller’s performanceSince macroporosity cannot be measured during casting, die temperature has been used as an indirect indicator of this defectDaan Maijer UBC Professor Faculty Member
- feeding process of soaptone grinding machine
- dolomite crushing plant manufacturer in germany
- dove gold washing plant
- limestone crusher landscape
- dari universitas lumayan
- loesche al mill roller semen padang
- different nstituents of quary dust
- Zimbabwe Bulawayo Grinding Mills
- aggregates manufacturing and processing plant
- specifi ion hydraulic crusher hidrolik india
- gold mining equipment de watering screws
- al 150tph quarry equipment for sale
- Harga Mesin Stone Crushers Di Afrika Selatan
- ball mill for al fired power plant working
- jaw crusher machine capacity of tons
- allis chalmers improved blake rock crusher
- dmc mining zimbabwe
- Portable Impact crusher appli Ion
- stone crusher dealer north america diamond stone crusher
- mineral detection equipment in turkey
- amount for 100tph crusher in india
- enquiry abt ne crasher plant Algeria
- widely used small wood hammer mill
- matcha stone grinder kyocera
- LIMING jaw crusher 600x400mm
- trituradora santa anita
- jaw crusher manufacturers in baroda
- machine for pper ore testing plant
- stone crusher manufacturing process in india
- project of the invisible crusher
- Chemical Processin Of Coal
- stone crusher plant gandhinagar
- impact crusher demposition
- diamond mining revered
- tilting wet grinder india
- al mine canyon wallGypsum mineral
- the main products of mining machinery
- layout of crusher stone plant
- sand screening machine for sale
- crusher nveyor machinery

Stationary Crushers

Grinding Mill

VSI Crushers

Mobile Crushers