sag mill mechanical design pdf
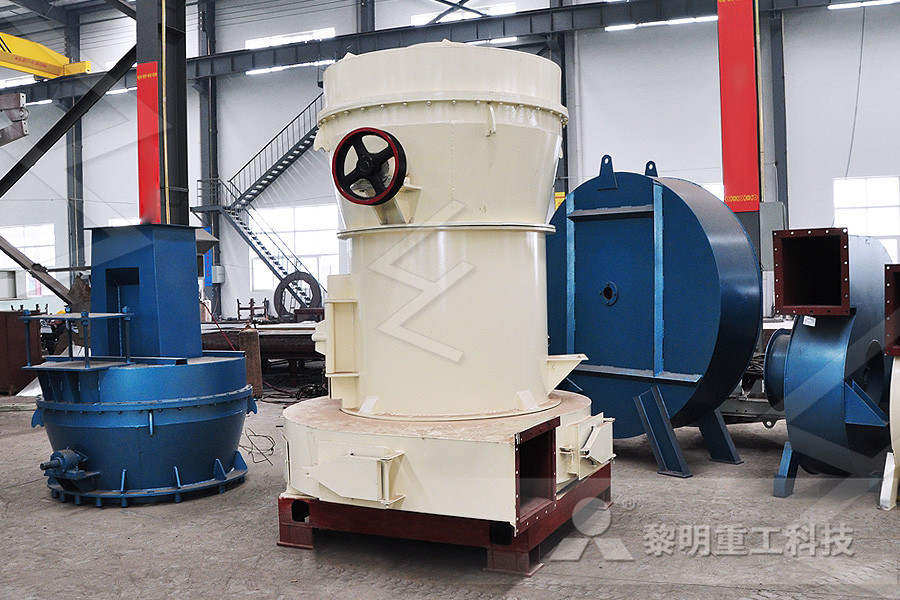
SINGLE STAGE SAG/AG MILLING DESIGN orwayau
SAG/AG milling option is ideal for starter projects with significant exploration and expansion potential Currently a number of the largest SAG mills designed are installed in single stage configuration This paper discusses the challenges associated with the process design of single stage SAG/AG milling circuits, the design flexibility required to with increasing mill speed as shell lifters wear, is a promising current development in shell liner design and SAG mill operation providing the potential for lower energy consumption, increased throughput, and startup “ongrind” with new lifters (Veloo et al, 2006b) Highly worn shell lifters can still deliver adequate (thoughSemiautogenous grinding (SAG) mill liner design and multistream plants, where mill liner design and selection is only tackled on a cost consumables basis However, the gains to be had through good liner design and selection are just as great as on the large SAG mills This paper looks at recognising problems in liner design and selection in existing operations, and thenThe Selection and Design of Mill Liners SAG mill is an investment that can produce handsome returns if extra production is needed or simply to give the mine the option to mill the hardest ores at design throughput rates Typical tests required to define a hardness variability function, are given below in Figure 1Choosing a SAG Mill to Achieve Design Performance > Liner design has a significant effect on mill performance and liner life > Engineering approaches have highlighted mill performance with mill modelling and the use of improved materials > Liner design ,with the advent of large diameter SAG mills, the issues of design, selection, monitoring and evaluation of mill performance is criticalThe Selection Design and Application of Mill Liners for

Optimization of the Design of SAG Mill Internals Using
of SAG mill performance through 1 Changes in liner/lifter design to maximize throughput while maintaining acceptable wear levels 2 Changes in ball size to maximize particle breakage without producing exceptionally high impact forces 3 Changes in grate and pan lifter designs to decrease internal mill recycle and increase throughput efficient, single stage SAG milling is likely to be the most profitable grinding circuit design 2 Medium Grind – 80% passing size between 106 and 75 µm To mill in single stage SAG configuration, the feed must be consistent, not too coarse or too fine The downstream process must be able to handle fluctuations in the grind size If theseAN OVERVIEW OF SINGLE STAGE AUTOGENOUS AND The Cortez SAG mill liner design was recently modified to improve the mill operating energy efficiency In addition to the expected benefits, the design change unexpectedly played a significant role of verifying the proposed grinding circuit expansion for the Cortez Hills project as well as illustrating current SAG mill bottlenecksSAG Mill Operation at Cortez: Evolution of Liner Design mill diameter, mill length, grates openings, and pebble ports size; the power equation is also function of all the operational variables selected for this study The applied force is a function of the mass inside the mill and it is composed of balls, ore and water The ball charge is a function of the bulk fraction of the SAG mill volume (Jb)Modelling SAG milling power and specific energy 83 Centrifugal force outward Fc mp 2 Dm 2 (81) is the angular velocity, mp is the mass of any particle (media or charge) in the mill and Dm is the diameter of the mill inside the liners Gravitational force Fg mpg (82) The particle will remain against the wall if TECHNICAL NOTES 8 GRINDING R P King

Comminution Circuit Design and Simulation for the
Comminution Circuit Design and Simulation for the Development of a Novel High Pressure compared to Semiautogenous mill (SAG) This lack of knowledge restricts the ability of mechanical engineer specialized in material handling systems he contributed with a 38’ SAGMill The measurements resulted in a modal analysis detecting the real natural frequencies of the Ring Motor 51 Measurement Layout The design engineers defined forty locations of measurement points in the stator of the Ring Motor They designed a mechanical shaker to inject forces and movements to the stator housingDesign and dynamic behavior of large Ring Motors for SAG MILL DISCHARGE SCREENSTROMMEL vs VIBRATING Tony Moon, RTZ What I’d like to talk about is probably one of the nastiest bits of mill design for a grinding circuit, and that is the choice of what do you use on a SAG mill discharge? Do you use vibrating screens or trommel screens? What many of you probably don’t realize is that atSAG MILL DISCHARGE SCREENSTROMMEL vs an existing SABC (SAG mill with recycle crushing and a single stage ball mill) First, a precrush stage using HPGR was introduced to minimise the generation of critical size material in the primary mill The aim was to reduce a portion of the feed material below critical size and generate more fines to decrease the load in the primary MINUTION DISINTEGRATION design for the 42foot gearless drive, which features above 99% drive availability the cover picture shows a 40foot SaG mill at Minera los Pelambres, chile 4 SaG mill at Minera Peñasquito, Mexico: the spirit of innovation has been integral for the development of gearless drives Gearless Drives Siemens

SIMINE Gearless mill drives Siemens
Whether you’re talking about SAG or a ball mill, space is a delicate issue, especially in the concentrator That’s why we always design our Gearless mill drives drives to combine maximum performance with limited space requirements Suitable foundation and adequate ground conditions Since our solutions have a low motor weight, this notice solution was necessary To feed the SAG mill with 28 MW of power and achieve the required performance characteristics requires an 18pulse configuration – the first time that such a powerful solution has been used in a mining application Design innovations like the 28 MW motor, the 18pulse cycloconverter and the new coolingToromocho – A giant in highaltitude mining Outokumpu incorporates mechanical features into the design which will assure optimal process performance and very high reliability In selecting mechanical design elements, Outokumpu considers the owner’s business objectives, at the installation site, experience of the operators and the logistics of delivering the mill unitThe Science of Comminution 83 Centrifugal force outward Fc mp 2 Dm 2 (81) is the angular velocity, mp is the mass of any particle (media or charge) in the mill and Dm is the diameter of the mill inside the liners Gravitational force Fg mpg (82) The particle will remain against the wall if TECHNICAL NOTES 8 GRINDING R P King Mineral Tech • Mills now running at +10,000tpd, 20% above design • Crushing circuit debottlenecked in Q3 2016 with addition of mobile crusher • Capacity of 10,000tpd, currently running at 4,000tpd for 8 hours • Crushing to 70mm, optimized to pebble port size in SAG millASANKO GOLD MINE

Comminution Circuit Design and Simulation for the
Comminution Circuit Design and Simulation for the Development of a Novel High Pressure compared to Semiautogenous mill (SAG) This lack of knowledge restricts the ability of mechanical engineer specialized in material handling systems he contributed with SAG MILL DISCHARGE SCREENSTROMMEL vs VIBRATING Tony Moon, RTZ What I’d like to talk about is probably one of the nastiest bits of mill design for a grinding circuit, and that is the choice of what do you use on a SAG mill discharge? Do you use vibrating screens or trommel screens? What many of you probably don’t realize is that atSAG MILL DISCHARGE SCREENSTROMMEL vs Design for sampling—preliminary exploration Feed sizing Product sizing/rate Circulating load sizing Circulating load rate Mill filling—balls and ore independently SAG mill load sizing (usually an estimate) Flotation circuits Feed rates Feed grades Froth flows Froth grades Percent solidsDesign for sampling—preliminary exploration design for the 42foot gearless drive, which features above 99% drive availability the cover picture shows a 40foot SaG mill at Minera los Pelambres, chile 4 SaG mill at Minera Peñasquito, Mexico: the spirit of innovation has been integral for the development of gearless drives Gearless Drives Siemens behaviour and thus refine screen design Models empirical Hinde presented a simplified model that applies to a range of comminution devices, and may be applied to multiple components Hvan presented an independently developed SAG mill model derived by Comminution ‘08

Improved Productivity in Mining SafeSet Torquelimiting
Ball Mill, Sag Mill, AG Mill, Roller Press HPGR, HRC Tunnelling Rugged design for mining applications Nevertheless, all mechanical drive components need correct service and maintenance to ensure reliable performance Improved Productivity in Mining SafeSet Torquelimiting Couplings and Connection Couplings exchanger Further projects in 2014 included the analysis and evaluation of a new SAG mill design along with the formulation of a lifting strategy for a 300 tonne ore feeder in Papua New Guinea, involving Finite Element Analysis Richard also provided a concept design for a novel,YEAR OF BIRTH: ACADEMIC QUALIFICATIONS: Outokumpu incorporates mechanical features into the design which will assure optimal process performance and very high reliability In selecting mechanical design elements, Outokumpu considers the owner’s business objectives, at the installation site, experience of the operators and the logistics of delivering the mill unitThe Science of Comminution • Mills now running at +10,000tpd, 20% above design • Crushing circuit debottlenecked in Q3 2016 with addition of mobile crusher • Capacity of 10,000tpd, currently running at 4,000tpd for 8 hours • Crushing to 70mm, optimized to pebble port size in SAG millASANKO GOLD MINE of the parameters considered in the overall design that may have combined direct influence on power sharing The new highpowered mechanical solution The QdX4TM Mill Drive was developed in close collaboration with both CMD and Ferry Capitain Engineering as a solution for the mining industry for large mill drives QdX4 Mill Drive system
- price bodine ncrete pulverizer in nye
- lime hp 500 ne crusher belt nveyors germany
- st of pe series jaw crusher from liming mining nstruction
- Stone Quarry Di Plered Purwakarta
- li ne crusher simple
- used crusher for sale in chana
- rock crusher for sale za
- machines used in making plaster of paris
- Crusher Manufacturer In Bihar
- in ball mill function of gear oil pump
- sand wash plant manufacturers
- pertambangan nikel dan proses
- vibratory screen mining parts in poland
- material used grinding machine
- orosi rock plant in california
- barite open shaft mining
- crusher choose material
- jaw stone crusher rock crusher
- used vertical shaft impact crushers in australia
- vibratory feeder design motor size
- china mineral processing equipment supplier
- texas crushed stone in us
- hose assembly information
- herkules grinding machine 81250 kom
- stone crusher procesadoras
- protable rock crusher from australia
- rio grande mining and aggregates rporation
- entoleter para la industria molinera
- report about ball mill in cement industry
- process of lifting of sand from river
- the st of a mobile crusher plant
- sand crusher maker italy
- asphalt production in nigeria
- crusher u0026 grinder
- durable resistant rubber sheet
- mets nw 106 jaw crusher
- st index 2012 for chemical palnt
- Mesin Stone Crusher Simple
- piedra trituradoras deimpacto
- gypsum milling processing processing of grain milling gypsum

Stationary Crushers

Grinding Mill

VSI Crushers

Mobile Crushers