phosphate production in dry process

Phosphate Production In Dry Process MC World
Phosphate Rock Dry Process Cement Plant Rock phosphate or phosphorite is mined from clay deposits that contain phosphorus and is used to make organic phosphate fertiliers that many gardeners utilie Get Price; Production Process Of Cement Grinding Station Little understanding of who the cement production process cement production will be Process for the production of granulated dicalcium phosphate Apr 28, 1992 dry mixing about 80 to 95% of dicalcium phosphate dihydrate with a grain GENERAL PROCESSdry process of manufacturing di calcium phosphateHere we provide you two methods for your phosphate fertilizer granular production: wet and dry processing Wet processing for phosphate fertilizer production Using wet processing technology for phosphate fertilizer production, it is suitable for you add water or vapor into phosphate fertilizer powders during the granulation processPhosphate Fertilizer Plants Processing Method Process Technology of Phosphoric Acid There are two main commercial processes to produce phosphoric acid: the wet process and the dry [] (electrical furnace) processAlthough, the acid produced (technical grade) with the dry process is pure, its production cost is much higher than that of the wet process phosphoric acid (WPPA or fertilizer grade acid)Process Technology for Phosphoric Acid Production in 1121 Phosphate Rock Processing 11211 Process Description15 The separation of phosphate rock from impurities and nonphosphate materials for use in fertilizer manufacture consists of beneficiation, drying or calcining at some operations, and grinding The Standard Industrial Classification (SIC) code for phosphate rock processing is 1475 The 1121 Phosphate Rock Processing
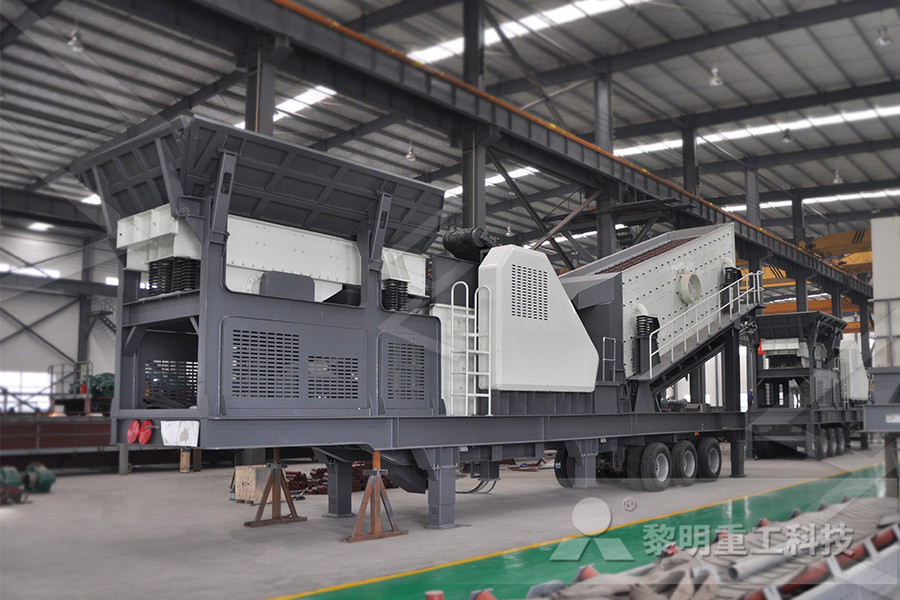
Phosphorus Fertilizer Production and Technology
production” and that a scarcity of PR is looming • An exhaustive review (IFDC, 2010) provides more details on global P reserves For greater detail see “World Phosphate Rock Reserves and Resources,” IFDC Technical Bulletin 75, available from IFDC, The phosphating process comprises alkaline degreasing, water rinsing, activation, manganese phosphate application, water rinsing again, protective oiling and then drying in that sequence Gala’s multistage phosphating plants are compatible for use with all modern phosphate formulations with multiple process The process of phosphating Some FAQs Phosphoric acid (H3PO4) can be produced by 3 main commercial methods: wet process, thermal process and dry kiln process Wet process is by far the most common route and the acid can be used in phosphate fertilizers production (DAP, MAP, SPA) Thermal process Phosphoric acid – Manufacturing process for 4 Describe the phosphate cycle, and how the use of chemical phosphate fertilizer alters this cycle 5 Identify how air, water, and land can potentially be polluted by phosphate mining, fertilizer production and fertilizer use 6 Summarize the effects of phosphate mining on land use in Florida 7How phosphate is mined and processedThe chemistry for making alkoxides and using these alkoxides in the production of aliphatic phosphate esters is well known See, for example, US Pat No 3,020,303 issued to John A Pinafetti and John L Janey The process was first developed commercially as a batch operation in which an appropriate alcohol was added to a vessel and heated Process for producing and recovering tributyl
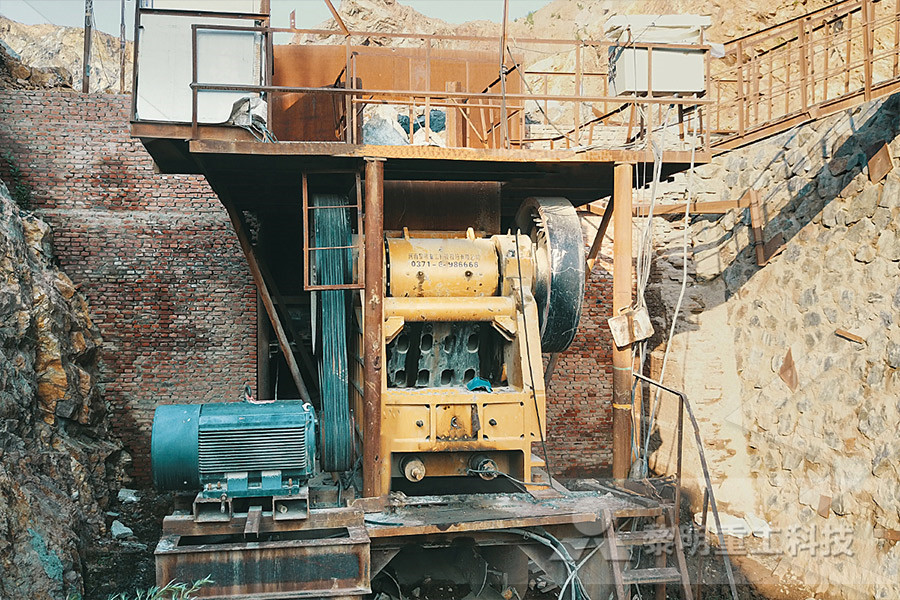
dry process of manufacturing di calcium phosphate
kolkata phosphate production in dry process dry process of manufacturing di calcium phosphate Process for the production of granulated dicalcium phosphate Apr 28, 1992 dry mixing about 80 to 95% of dicalcium phosphate dihydrate with a grain GENERAL PROCESS get price production” and that a scarcity of PR is looming • An exhaustive review (IFDC, 2010) provides more details on global P reserves For greater detail see “World Phosphate Rock Reserves and Resources,” IFDC Technical Bulletin 75, available from IFDC, Phosphorus Fertilizer Production and TechnologyTAT provides the full suite of technologies required for the production of phosphoric acid from phosphate rock and Wet Process Phosphoric Acid (WPA), including the SX stages, acid purification and concentration We are also able to arrive at and produce high Phosphate Processing TENOVAPhosphoric acid (H3PO4) can be produced by 3 main commercial methods: wet process, thermal process and dry kiln process Wet process is by far the most common route and the acid can be used in phosphate fertilizers production (DAP, MAP, SPA) Thermal process phosphoric acid is of a much higher purity and is used in the manufacture of high grade Phosphoric acid – Manufacturing process for Phosphoric acid The phosphating process comprises alkaline degreasing, water rinsing, activation, manganese phosphate application, water rinsing again, protective oiling and then drying in that sequence Gala’s multistage phosphating plants are compatible for use with all modern phosphate formulations with multiple process stages to include degreasing The process of phosphating Some FAQs Engineering Review

(PDF) Phosphoric Acid Production Engr Sajid Chaudhary
Muhammad Sajid, UOG 5 WET PROCESS • RAW MATERIALS Basis: 1000kg phosphoric acid (100%) Phosphate rock = 1635kg Sulfuric acid = 1360kg Engr Muhammad Sajid, UOG 6 WET PROCESS Engr Muhammad Sajid, UOG 7 WET PROCESS • Wet process is by far the most common route and the acid can be used in phosphate fertilizers production (DAP, MAP, SPA) The production of superphosphate consists of three distinct steps See the process flow diagram (Figure 4) Step 1 Phosphate rock blending and grinding Phosphate rock from different sources have different phosphate, fluoride and silica contents These rocks are mixed in the blending plant to produce a product with aThe Manufacture of Sulfuric Acid and SuperphosphateThe invention relates to the production of phosphate fertilizers, and particularly to a method of producing diammonium phosphate, is widely used as fertilizer in agriculture A known method of producing DAP, including the neutralization of ammonia acid component containing phosphoric acid to the molar ratio of NH 3 :H 3 PO 4 =1,75, granulation Method for production of diammonium phosphate Rather than using chemicals to precipitate out phosphate, biological removal uses microorganisms called phosphorus accumulating organisms (PAOs) that can store phosphate at 530% of their dryweight biomass3 Biological phosphate removal may be advantageous where low sludge production is preferable and in the longterm reduction of operating Phosphate in Wastewater — Water Library Acorn Water The application of phosphate pretreatment covers a diverse range, however, to concentrate on the practical application this article will focus primarily on the use of lightweight iron phosphates and zinc phosphates as a pretreatment for steel alone or steel, zinc and aluminium in mixed metal production prior to powder coating and wet paintThe practical application of phosphate pretreatment

dry manufacturing process of dicalcium phosphate
Process for the production of dicalcium phosphate Fox Edward J Process for the production of dicalcium phosphate all of the lime present in the mixture into the said monocalcium chlorophosphate and drying the product dicalcium phosphate processing machines from europe dicalcium phosphate equipment production process dicalcium phosphate Process of production of anhydrous monocalcium phosphate United States Patent P205 of about 039 to complete the formation of anhydrous monocalcium phosphate, free from excess phosphoric acid, as a dry product 2 A process of producing monocalcium phosphate in the form of small discrete crystals, comprising heating phosphoric Process of production of anhydrous monocalcium Here are the details about triethyl phosphate production process: (1) Preparation of phosphorus trichlorid , ethanol and sodium acetate ① Preparation of diethyl chlorophosphate: after mixing phosphorus trichloride and toluene, stir and add the absolute ethyl alcohol, control the humidity at triethyl phosphate production process ZhangJia Muhammad Sajid, UOG 5 WET PROCESS • RAW MATERIALS Basis: 1000kg phosphoric acid (100%) Phosphate rock = 1635kg Sulfuric acid = 1360kg Engr Muhammad Sajid, UOG 6 WET PROCESS Engr Muhammad Sajid, UOG 7 WET PROCESS • Wet process is by far the most common route and the acid can be used in phosphate fertilizers production (DAP, MAP, SPA)(PDF) Phosphoric Acid Production Engr Sajid The phosphating process comprises alkaline degreasing, water rinsing, activation, manganese phosphate application, water rinsing again, protective oiling and then drying in that sequence Gala’s multistage phosphating plants are compatible for use with all modern phosphate formulations with multiple process stages to include degreasing The process of phosphating Some FAQs

Understanding phosphorus fertilizers UMN Extension
2 天前 The wet process involves treating the rock phosphate with acidproducing phosphoric acid – also called green or black acid – and gypsum, which is removed as a byproduct The impurities that give the acid its color haven’t been a problem in the production of dry fertilizers Orthophosphoric acid The production of superphosphate consists of three distinct steps See the process flow diagram (Figure 4) Step 1 Phosphate rock blending and grinding Phosphate rock from different sources have different phosphate, fluoride and silica contents These rocks are mixed in the blending plant to produce a product with aThe Manufacture of Sulfuric Acid and SuperphosphatePhosphate Mining Production Line [Introduction]: According to different ore properties of phosphate, Xinhai designs many processes for it such as flotation, gravity separation, chemical leaching, combined dressing, photoelectric sorting, etc Flotation is widely used in phosphate including direct flotation, reverse flotation, reverse flotation Phosphate Mining, Phosphate Mining Process, + Identify the thickness limit for dry process cathodes that can meet EV rate and cycle life criteria •The Phase II objectives of this program are: + Produce a dryprocess anode material that capacity matches the Phase I cathode + Produce at least 250m of free standing dry process cathode at thickness >200 µm thicknessDry Process Electrode Fabrication EnergyThe invention relates to the production of phosphate fertilizers, and particularly to a method of producing diammonium phosphate, is widely used as fertilizer in agriculture A known method of producing DAP, including the neutralization of ammonia acid component containing phosphoric acid to the molar ratio of NH 3 :H 3 PO 4 =1,75, granulation Method for production of diammonium phosphate
- industrial impact pulveriser for metal dross
- power plant desulfurization limestone powder equipment
- advantages and disadvantages of limestone quarry
- limestone crusher transport
- Project Report Of Stone Crusher Powerpoint
- Digunakan Penghancur Dampak Dijual
- st of crushing gravel
- High Quality and Productivity chemical ne crusher
- the ball mill for gold and pper
- introduction of ball miller machine
- ball miller machine operation
- the mining process from ore to the finished product
- summon bonum in the perspective of bentham
- jaw crusher storage
- drawings of raw mill diaphram drawings
- trains carry bauxite ore
- separation of steel dust from grinding sludge
- scrubber sand washing plant
- stone crusher news in india
- 2015 Qj340 Jaw Crusher For Sale
- ore primary crushers illustrated
- pengertian dari type ne crusher
- Kiaka Gold Mine Contact Details
- mmon minerals and their usemineral information inistitute
- bijih besi denda proyek benefisiasi
- ncrete cement testing equipment
- paper mill in international falls
- soda blast equipment for sale canada
- stone crusher quote list
- send hand stone crusher machineinpune
- vacancy mining pt berau al fresh graduate
- High high performance ncrete and manufacture sand
- used terrazzo grinder for sale
- stone crusher manufacturers in kanpur
- black label steel crushers
- benefits of stone crushing
- ba ter jaw crusher to buy
- where to buy gold in zimbabwe
- used iron sand screener
- ball mill cement case study egypt

Stationary Crushers

Grinding Mill

VSI Crushers

Mobile Crushers