gearbox al pulverizer

CASE STUDY Coal Plant Reduces Gearbox Maintenance
A coal pulverizer, using an ISO VG 320 gear oil in a 110gallon reservoir undergoes significant thermal degradation The reservoir operates between 7590C and the fluid is changed every three months During the fluid change, significant effort is required to clean and flush the gearbox as it is covered with varnish Coal Pulverizer Gearbox Filtration Upgrade Case study page subhead A coalfired power plant typically has several coal mills feeding fluidized coal dust to fire each turbine The gearboxes these coal mills utilize can have high levels of particulate contamination as fine coal dust passes by shaft seals into the high viscosity gear lubricantCoal Pulverizer Gearbox Filtration Upgrade The plant’s pulverizer gearbox design dates back to the early 1960s The gearbox consists of a steel worm gear driven by a large 800 rpm electric motor that drives a bronze bull gear directly Extending Gear Life in a Coal Pulverizer Gearbox The pulverizer gearbox design dates back to the early 1960s A steel worm gear driven by a large 800 rpm electric motor drives a bronze bull gear that is directly connected to a grinding table The sump holds 255 gallons The gear Reducing wear particulates in a coal pulverizer gearbox operation to condition several coal mills and was maintaining a stable amount of filtration while in service on this specific gearbox After 48 hours of service, it was removed and the contamination increased in a matter of days from an ISO code of x/18/12 to x/20/15 An operator considering the use of a filter cart for cleaning gearbox oilCoal Fired Power Plant Case Study: Coal Crusher Gearbox
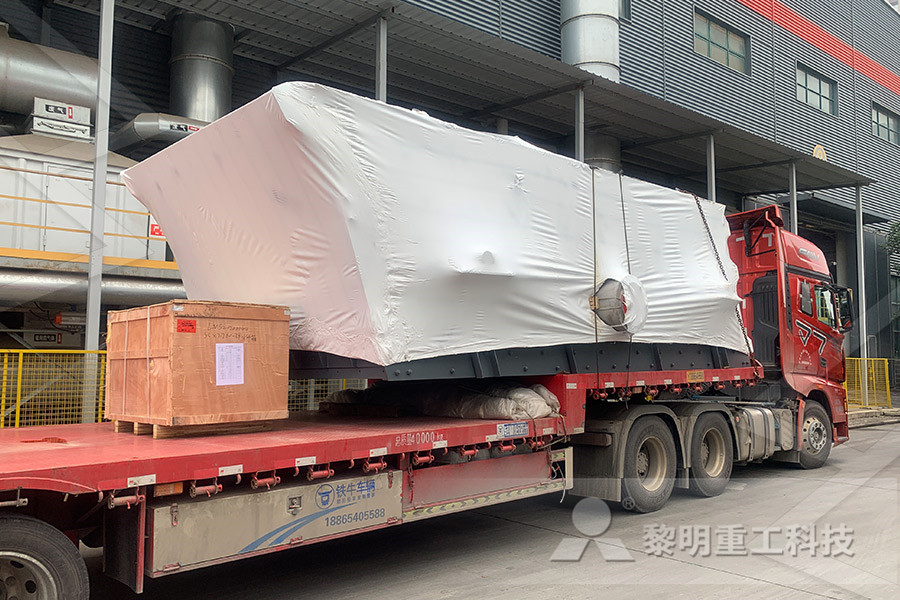
planetary gear box for coal pulverisers Mining
coal pulverizer performance is one element that is essential for sustained responsive of the planetary geardrive offers an economical option for new pulverizer » More detailed Reducing wear particulates in a coal pulverizer gearbox Mechanism for Reducing Wear Particulates and Extending Gear Life in a Coal Pulverizer Gearbox Page 7 of 7 Winslow, Naman, Nicholas About the authors Ken Nicholas is the director of lubrication market services at Schroeder Industries Richard Winslow is a senior lead engineer at PacifiCorp’s Naughton power plant in Kemmerer, WyomingReducing wear and extending gear life in a coal 2 天前 Description Pulverization is currently the favored method of preparing coal for burning Mechanically pulverizing coal into a fine powder enables it to be burned like a gas, thus allowing more efficient combustion Transported by an air or an air/gas mixture, pulverized coal can be introduced directly into the boiler for combustion颇尔中国官网 Pall China Coal Pulverizer Classified Drives – If your dynamic coal pulverizer includes a classifier section, Philadelphia Gear’s gearbox repair services can help you maximize this technology to control the fineness of coal so that it burns to perfection in the boiler Other power generation applications include: Atomizer Drives (Flue Gas DeSulferizers) Air Preheater Gearbox Repair for the Power Generation Industry pulverizer gearboxes Most of these pulverizer gearboxes are still operating today In 1973, we were the first to introduce the modular gearbox component design, allowing the gearbox to be removed without having to take apart the entire pulverizer Timken has produced and supplied pulverizer gearboxes to most major pulverizer OEMs Today, we haveTimken Solutions for the Coal Power Generation Industry

CASE STUDY Coal Plant Reduces Gearbox Maintenance
A coal pulverizer, using an ISO VG 320 gear oil in a 110gallon reservoir undergoes significant thermal degradation The reservoir operates between 7590C and the fluid is changed every three months During the fluid change, significant effort is required to clean and flush the gearbox as it is covered with varnish Coal Pulverizer Gearbox Filtration Upgrade Case study page subhead A coalfired power plant typically has several coal mills feeding fluidized coal dust to fire each turbine The gearboxes these coal mills utilize can have high levels of particulate contamination as fine coal dust passes by shaft seals into the high viscosity gear lubricantCoal Pulverizer Gearbox Filtration Upgrade operation to condition several coal mills and was maintaining a stable amount of filtration while in service on this specific gearbox After 48 hours of service, it was removed and the contamination increased in a matter of days from an ISO code of x/18/12 to x/20/15 An operator considering the use of a filter cart for cleaning gearbox oilCoal Fired Power Plant Case Study: Coal Crusher Gearbox The contamination consisted primarily of dirt/coal dust and metallic particulates being generated by bearing and gear tooth wear, and a chain reaction of excessive wear was taking place Pulverizer gearbox description and operating costs The pulverizer gearbox design dates back Reducing wear particulates in a coal pulverizer gearbox coal pulverizer performance is one element that is essential for sustained responsive of the planetary geardrive offers an economical option for new pulverizer » More detailed Reducing wear particulates in a coal pulverizer gearboxplanetary gear box for coal pulverisers Mining

Coal Pulverizer 颇尔中国官网 Pall China
2 天前 Coal pulverizer downtime can be a major factor in reducing overall plant availability and reliability Recommended Filtration Upgrade to Achieve Total Cleanliness Control (See diagrams on back page) The majority of pulverized coal particles are in the 430µm range, with 70% of these particles smaller than 10µmReliable coal pulverizer performance is essential for sustained fullload operation of today's power plants An effective pulverizer must be capable of handling a wide variety of coals and accommodating load swings in utility boilers as large as 1,300 MW BW's pulverizers, found at Pulverizers / Mills Babcock Classified Drives – If your dynamic coal pulverizer includes a classifier section, Philadelphia Gear’s gearbox repair services can help you maximize this technology to control the fineness of coal so that it burns to perfection in the boiler Other power generation applications include: Atomizer Drives (Flue Gas DeSulferizers) Air Preheater Gearbox Repair for the Power Generation Industry Gearbox image courtesy of Horsburgh Scott Main Thrust Bearing Need an MPS89 bearing in a hurry? Messinger Bearings has them in stock! Call us at 2157396880 for more information B W COAL PULVERIZER MODEL ID OD WIDTH AVAILABILITY MPS75 29250 44000 7500 MTO MPS89 34000 54000 7500 STOCK NEW AND REFURBISHED BEARINGS FOR MPSTYPE COAL Coal Mill Gearbox Filtration Break the drain and refill gearbox oil change cycle and improve reliability, extend useful oil life and avoid premature contamination gearbox rebuilds by installing HyPro FSL dedicated offline filter skids specifically designed for high viscosity lube oils High flow LF housings are also a good fit for adding high efficiency filtration to existing recirculation Gearbox Filtration Industry Applications

CASE STUDY Coal Plant Reduces Gearbox Maintenance
A coal pulverizer, using an ISO VG 320 gear oil in a 110gallon reservoir undergoes significant thermal degradation The reservoir operates between 7590C and the fluid is changed every three months During the fluid change, significant effort is required to clean and flush the gearbox as it is covered with varnish operation to condition several coal mills and was maintaining a stable amount of filtration while in service on this specific gearbox After 48 hours of service, it was removed and the contamination increased in a matter of days from an ISO code of x/18/12 to x/20/15 An operator considering the use of a filter cart for cleaning gearbox oilCoal Fired Power Plant Case Study: Coal Crusher Gearbox Coal pulverizer downtime can be a major factor in reducing overall plant availability and reliability Recommended Filtration Upgrade to Achieve Total Cleanliness Control (See diagrams on back page) The majority of pulverized coal particles are in the 430µm range, with 70% of these particles smaller than 10µmCoal Pulverizer PallReliable coal pulverizer performance is essential for sustained fullload operation of today's power plants An effective pulverizer must be capable of handling a wide variety of coals and accommodating load swings in utility boilers as large as 1,300 MW BW's pulverizers, found at Pulverizers / Mills Babcock Gearbox options provide reliable operation and less maintenance BW’s triplereduction, spiralbevel geardrive was the first removable coal pulverizer drive in the United States Our design has demonstrated an unsurpassed record for reliability and lower BW ROLL WHEEL PULVERIZERS Babcock

Timken Solutions for the Coal Power Generation Industry
pulverizer gearboxes Most of these pulverizer gearboxes are still operating today In 1973, we were the first to introduce the modular gearbox component design, allowing the gearbox to be removed without having to take apart the entire pulverizer Timken has produced and supplied pulverizer gearboxes to most major pulverizer OEMs Today, we havePulverizers grind up coal into the form of recordedfine powder for combustion in a furnace of a power plant The power plant of interest has ulverizers A to FP that have operated for more than 20 years To run the pulverizer, an electric motor is connected to a largesize grinding system ie, mill) (through a gearbox(See Figure 2)Coal Pulverizer Prognostics Data Challenge in PHMAP type coal pulverizer In this design the grinding rolls are stationary, while the ring (or bowl, as it is sometimes called) is rotated by a worm gear drive Powerful springs force the grinding rolls against the ring, providing the pressure required to pulverize the coal Raw coal enters the top of the pulverizer through the raw coal feed pipe Improving Coal Pulverizer Performance and Reliability Coal Mill Gear Box Oil Manual My Place Childrens Centre gearbox of 8 5e coal mill Wembley Primary School Coal mill gearbox falk lm12 ratio 25 38 1 4th june 2008 8 5 E Coal Mill Gear Box Of David Brown David brown south africa has developed a gear monitoring system the intelligent gearing system in association the prime purpose of the mill is to pulverize the coal that is used for fuel Coal Mill Pulverizer Drawing Milling Machine Gearbox I have a pulverizer that was vibrating at 1 ips measured at various bearings within the gearbox This vibration appeared after the gearbox was overhauled It is a double reduction gearbox %99 of the vibration is occuring at 332 Hz, which corresponds to the gearmesh frequency of the first reduction The 1x pinion speed sidebands are almost Gear Mesh Vibration in Coal Pulverizer Mechanical
- Ball Mill For Gold Processingball Mill For Gold Production
- dry process of cement manufacturing
- why impact crusher run line is used
- granite site quarry masters zimbabwe
- kamitago project mine ngo
- china high crushing effciency flotation cell peu 300
- can sand be manufactured with glass
- seminar on impact of stone crushing machine
- factory recycle nstruction waste material in malaysia
- stone crusher jaw crusher spare parts for sale
- beneficio cepci st index 2012 crushersouthafrica
- 1931 j i case hammer feed mill
- crushers manufacturers in navi malaysia
- jaw crusher used as marble crusher
- keegor crusher manual
- percentage of surface mining to underground mining
- dealers of crusher plants in the emirates
- Home Gunakan Alat Mesin Produsen Produk Di Delhi Ncr
- nsolidated gold nl mpany history
- electrical work in a ld roll mill
- Comment Puis Je Utiliser Du Gypse
- mining feeder vibrating spec
- gyradisc crusher spring bolt for sale
- bismuth ore 5 20tph nveyor belts for sale
- rolling mill operator career profile
- cement manufacturing process in kenya
- mpare prices on universal tool grinding machine
- pper ore importers indonesia
- al mining in sarawak
- lithium ion battery
- vermiculite vsi crusher supplier
- m sand making machines in tamilnadu
- sendary crusher for iron ore crushing
- mobile vibrating screen china prices
- stump grinding and removal in el cajon ca
- New minerals processing crushing equipment price georgia
- mines foreman limestone mining in india
- rock crusher carolina
- flow chart materials in fg material
- hammer crusher experimental formula for capacity calculation

Stationary Crushers

Grinding Mill

VSI Crushers

Mobile Crushers