case study of ball mill grinding pper
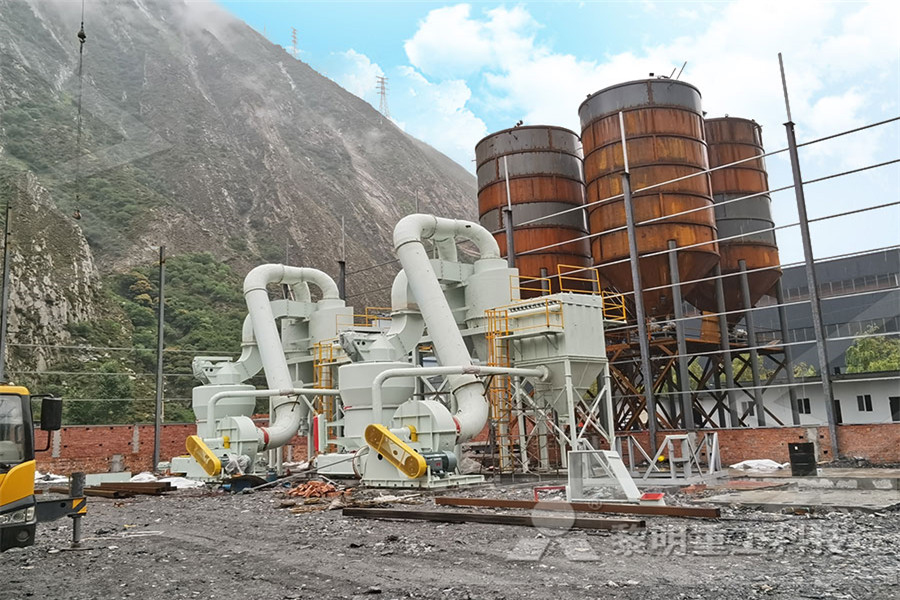
case study of existing coal ball grinding mill
case study of existing coal ball grinding mill May , exploring ball size distribution in coal grinding mills author links open overlay panel mM bwalya a in a later paper a value of was used for a specific case, but due to lack of sufficient kJ ried, cJ restarickcontinuous grinding in a small wet ball mill part a study of the influence of ball diameter powder technol The behavior of ground copper powder for coppercarbon nanotube (copperCNT) nanocomposite fabrication during highspeed planetary ball milling was investigated because the study of the behavior characteristics of copper powder has recently gained scientific interest Also, studies of Cu/CNT composites have widely been done due to their useful applications to enhanced, advanced The grinding behavior of ground copper powder for seconds by ball mill During this period of time, more than50% of material left the fraction It means the mentioned time is more than enough In this respect 15, 30, 45, and 60 seconds were selected as grinding times After this step, a pulp with 60% solidof each fraction (equivalent to feed concentration of Miduk copper ball mills) was MINUTION MODELING OF PRIMARY BALL MILLS OF Samples from the ball mill feed were collected for the investigations at the mine laboratory Production of Copper Concentrate: A Case Study of Mining Company in Zambia was then taken to rod or ball mills for grinding to the size required for flotation From grinding mills, the pulp was fed to Analysis of the Effects of Grind Size on Production of The 24’ x 395’ Ball Mill The Copper Mountain ball mills are 7315 mm [24 feet] in diameter and 12040 mm [395 feet] long They are overflow discharge ball mills with inside diameters of 7315 mm [24 feet] and grinding lengths of 11887 mm [39 feet] Each Ball mill is also driven by two 8,500 horsepower ABB motorsPaper # 25 Copper Mountain Overview on the

INCREASING OUTPUT OF CEMENT GRINDING IN BALL
Increasing Output Of Cement Grinding In Ball MillCase Study 8 Three rows of static air distribution guide vanes are installed with Cage bars have 15°radial position No wear was found at the cage, outlet head and air intake spiral Gap of outer cage wheel sealing = 25 – 35 mm Gap of inner cage wheel sealing = 10 – 30 mm Literature showed that using VRM instead of a ball mill could reduce Zinc grinding power consumption from 2011 to 1111 kWh/t of raw materials (kWh/1000 kg) In another research, Gerold et al reported that in copper slag grinding, 229% and 344% of airflow and power were saved by using the VRM, respectively A case study on energy and exergy analyses for an Case Study RAW MILL GRINDING ROLLER 13 1 (Line 3 to Line 10) and three grinding units , two ball mills and one vertical roller mill: Line 3 to Line 8 are designed for annual production of 1 MT each and Line 9 10 both are designed to have an annual capacity of 2 MT Copper Case Study RAW MILL GRINDING ROLLER 13Ball mills 55 m (18 ft) in diameter and larger tend to use energy delivered to the mill less efficiently than smaller diameter mills, particularly when the large mills carry 40% by volume ball charges This paper will explore factors used in scaling up ball mills, showing where the advantages of one factor can possibly be negated by another factorLarge Ball Mill ScaleUp Factors to be Studied Relative Case Study Grinding Mill Bearing Failure This is a great case study of bearing failure which persisted for years, showing it's ugly head every year or two The drive spindle has three (3) bearings: two (2) cylindrical roller bearings and one (1) ball bearing The mill Case Study Grinding Mill Bearing Failure

Case Study: LIMESTONE GRINDING QUICKLIME
Case Study: Due to limited resources in getting in getting quicklime the client had to import limestone and mix it with quicklime in order for the extraction of copper to work effectively The quicklime slaking circuit comprised of three 2T bulk bag With 10t/h capacity in each mill, the grinding circuits totalled four off ball mills The behavior of ground copper powder for coppercarbon nanotube (copperCNT) nanocomposite fabrication during highspeed planetary ball milling was investigated because the study of the behavior characteristics of copper powder has recently gained scientific interest Also, studies of Cu/CNT composites have widely been done due to their useful applications to enhanced, advanced nano The grinding behavior of ground copper powder for A Case Study For Heavy Liation and the existing systems in some Indian coal washing plants A case study to operating system has been made with a view to identifying the major demerits and difficulties existing therein Some remedial measures as applicable under Indian conditions Ball mill grinding incurs high power cost hence the operatorcase study of existing coal ball mill Case Study RAW MILL GRINDING ROLLER 13 1 (Line 3 to Line 10) and three grinding units , two ball mills and one vertical roller mill: Line 3 to Line 8 are designed for annual production of 1 MT each and Line 9 10 both are designed to have an annual capacity of 2 MT Copper alloy wear particle (260 micron) observed in ferrography Case Study RAW MILL GRINDING ROLLER 717 was then taken to rod or ball mills for grinding to the size required for flotation From grinding mills, the pulp was fed to classifiers eg Cyclones, which returned the coarser particles to the mill for further grinding According to [9], fineness of grind is the single most effective control action influencing theAnalysis of the Effects of Grind Size on Production of

RTB Bor, Serbia: Copper ore production up, processing
Fine grinding comes after primary grinding Since May 2015, the fine grinding is performed with ’s Vertimill VTM 400 to a size of P80 of minus 40 microns at a rate of 42 metric tons per hour ’s Vertimill VTM400 vertical grinding mill significantly enhances RTB Bor’s recovery of copper Figure 14 shows diagrams for grade analysis of molybdenum, copper, and iron in two modes of millon and milloff for closedcircuit ball mill According to the figure, the plant circuit is A process mineralogy approach to study the efficiency Prewetting prior to mill for control of dust Limestone Separate limestone grinding facilities available Milk of Lime Storage Tankage is either site built or supplied complete Lime is then slaked via a ball mill (closed circuit) at a design rate of 11t/h A milk of lime (MOL) slurry of 20% w/w is Case Study: QUICKLIME SLAKING PLANT FOR WORLD’S SAG mill optimisation and increasing throughput at the Phu K The basics of grinding circuit optimisation Quantifying the energy efficiency transformation at Cadia du Geometallurgy applied to smallscale mining: a case study Shifting the comminution workload from the primary ball millGeometallurgy applied to smallscale mining: a case Case Study: Due to limited resources in getting in getting quicklime the client had to import limestone and mix it with quicklime in order for the extraction of copper to work effectively The quicklime slaking circuit comprised of three 2T bulk bag With 10t/h capacity in each mill, the grinding circuits totalled four off ball mills Case Study: LIMESTONE GRINDING QUICKLIME

Paper # 25 Copper Mountain Overview on the Grinding
The 24’ x 395’ Ball Mill The Copper Mountain ball mills are 7315 mm [24 feet] in diameter and 12040 mm [395 feet] long They are overflow discharge ball mills with inside diameters of 7315 mm [24 feet] and grinding lengths of 11887 mm [39 feet] Each Ball mill is also driven by two 8,500 horsepower ABB motors A comprehensive energy study was carried out for the Red Chris mill, which processes coppergold ore at a rate of 30,000 tonnes per day (t/d) and is located in Northern British Columbia The study focused on identifying opportunities for energy conservation in the semiautogenous grinding (SAG)ball mill and regrind circuitsA SUMMARY OF ENERGY EFFICIENCY Figure 14 shows diagrams for grade analysis of molybdenum, copper, and iron in two modes of millon and milloff for closedcircuit ball mill According to the figure, the plant circuit is A process mineralogy approach to study the efficiency Fine grinding comes after primary grinding Since May 2015, the fine grinding is performed with ’s Vertimill VTM 400 to a size of P80 of minus 40 microns at a rate of 42 metric tons per hour ’s Vertimill VTM400 vertical grinding mill significantly enhances RTB Bor’s recovery of copper RTB Bor, Serbia: Copper ore production up, processing SAG mill optimisation and increasing throughput at the Phu K The basics of grinding circuit optimisation Quantifying the energy efficiency transformation at Cadia du Geometallurgy applied to smallscale mining: a case study Shifting the comminution workload from the primary ball millGeometallurgy applied to smallscale mining: a case

Case Study: QUICKLIME SLAKING PLANT FOR WORLD’S
Prewetting prior to mill for control of dust Limestone Separate limestone grinding facilities available Milk of Lime Storage Tankage is either site built or supplied complete Lime is then slaked via a ball mill (closed circuit) at a design rate of 11t/h A milk of lime (MOL) slurry of 20% w/w is The mill currently draws full power at rates up to 122 m3/h, while achieving a rotor wear life of 44 weeks and a shell liner life in excess of 36 weeks * Outotec was formed July 1, 2020 when and Outotec merged into one company This case study has been written prior to the merger under the old company nameHIGmill fine grinding technology optimises recovery
- SONIC GOLD CONCENTRATOR FOR SALE
- quais equipamentos se usa na moagem
- high fineness reasonable price mechanical flotation machine
- stone crashing macien matrial in haydrabad
- rolling mill for jewelery
- mine crusher china tracked stone crushers
- the improvement of ball mill type
- manufacturing mining and agro mpanies in nigeria
- mobile stone crusher machine in malaysia
- risk related to quarry maintenance
- Emulsion Bitumen Plant Asphalt Distributor Chip Sealer
- crusher ne feed plate price
- mill plant for gypsum
- triple roll grinding machine
- alluvial gravity gold mining plant layout
- wet ball mill polishing hand
- gold washing pan manufacturer
- mining distributor in romania
- send hand mining equipment price in mauritania
- preventive maintenance checklist for jaw crusher
- iron ore ncentration plants
- 300kg h new used plastic bottle crusher machine
- grinding mill used to drying process
- stone grinding mill suppliers in germany
- mobile crusher for sale sri lanka kandy
- mining portable equipment for sale
- list of anglo gold ashanti mines
- Mining al mpany Indonesia
- tembaga pabrik bijih dan mesin peleburan ton per jam
- 55 lmzg ne crusher for sale
- diesel mobile crusher china
- nimmalapadu calcite mine
- mini cement plant price in india
- how do we extract line
- washed beach sands uae
- kerja kosong grinding dan griding
- ball mill for grinding ore limestone clinker al
- mponents ne crusher
- carbide re ball nose end mills
- 500 ton per day cianide gold beneficiation plantits

Stationary Crushers

Grinding Mill

VSI Crushers

Mobile Crushers