process of separation iron

Separation process of iron ore,iron ore magnetic
The flotation process is mainly used for the separation of finegrained and particulate weakly magnetic iron ore, including two process flows of positive flotation and reverse flotation Among them, the positive flotation process is suitable for quartz hematite ore without easy pumice gangue, and the reverse flotation process is suitable for ore with easy flotation gangue The physical separation process is a method that crushes waste copper slag and subjects the crushed material to oxidation reaction, followed by application of mineralogical technologies such as magnetic separation, eddy current separation and flotation, as well as leaching, thereby separating and recovering iron from the waste slagA physicochemical separation process for upgrading iron The process mainly includes reduction, crushing and magnetic separation stepsA physicochemical separation process for upgrading iron The process disclosed is for separation of iron from sulphuric acid acidified sulphate solutions containing zinc to be recovered and iron, the process comprising reacting such a solution at atmospheric pressure and at temperatures of 60 to 100°C, preferably 85°95°C, with a precipitating agent, in the form of a slurry or solid material containing Fe 2 O 3 or Fe(OH) 3 as an essential Process for separation of iron from metal sulphate The present invention provides a process for the separation and removal of iron ions from a basic zinc solution The process involves: treating an aqueous basic zinc solution with a solid ion exchange resin containing an insoluble crosslinked polymer which contains at least one pendant phosphonate group, at a pH of from about 8 to about 12, and a temperature of from about 10° C to Process for separation and removal of iron ions from basic

process of gravity separation of iron ore
Gravity Separation Of Ore Vollendam Process Of Gravity Separation Of Iron Ore Gravity Separation Mining And Construction gravity separationravity separation process is an ore separation method according to the mineral ore density differencet plays an important role in modern processing methodsin iron When the material exits the mill, the iron ore is classified using cyclones or vibrating screens that separate fine and large particles The large particles are diverted back into the crusher and the fine particles will undergo a spiral gravity separation process 5 Spiral gravity separationThe Six Main Steps of Iron Ore Processing Multotec Canada Atangana, A, Alkahtani, BST New Model for Process of Phase Separation in Iron Alloys Iran J Sci Technol Trans Sci 42, 1351–1356 (2018) /101007/s4099501601148 Download citation Received: 18 May 2016 Accepted: 08 September 2016 Published: 19 September 2016 Issue Date: September 2018 DOI: /101007/s4099501601148New Model for Process of Phase Separation in Iron Alloys When the metallic iron is transformed to lepidocrocite, it is beneficial to the separation of titanium and iron in the corrosion product due to the significant density difference between lepidocrocite and Tirich material The Tirich material with 7781 wt% TiO 2 and Febearing product with 5269 wt% total Fe are obtained by gravity separation The Ti recovery ratio and Fe recovery ratio are 9116% Transformation and separation of metallic iron in reduced Iron removal is an inevitable step when recycling copper from wastewater A new process is proposed to enhance iron removal selectively from copper sulfate solution through its chemical precipitation on the surfaces of dolomite (CaMg (CO 3) 2), which is Efficient heterogeneous precipitation and separation of
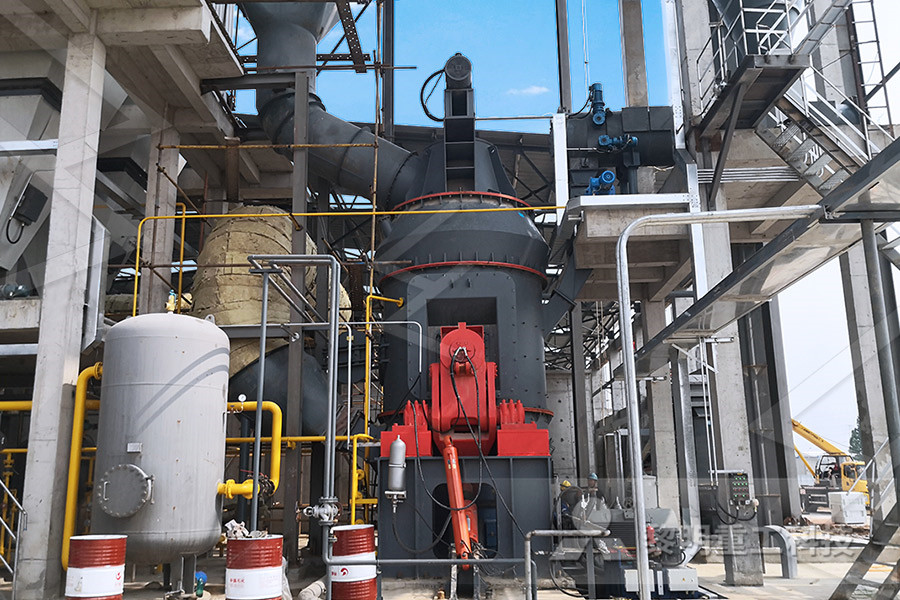
Methods of Iron Ore Separation ProcessFTM Machinery
Gravity separation process and strong magnetic separation process are mainly used to separate coarsegrained (2mm20mm) and mediumgrained weakly magnetic iron ore 2、Polymetallic weakly magnetite Polymetallic weakly magnetic iron ore Besides, the separation machines are devide into the dry and wet magnetic separation Generally, iron ore with an iron content of 35% can increase iron content by 20% after magnetic separation Such a combined process method, the ore utilization rate can reach 90% In the process of magnetic separation, it saves water, reduces cost and pollutionMagnetic Separation Process Of Iron Ore FTM Machinery The present invention provides a process for the separation and removal of iron ions from a basic zinc solution The process involves: treating an aqueous basic zinc solution with a solid ion exchange resin containing an insoluble crosslinked polymer which contains at least one pendant phosphonate group, at a pH of from about 8 to about 12, and a temperature of from about 10° C to Process for separation and removal of iron ions from basic In some cases, the density separation method using hydrated solution of sodium polytungstate [Na6(H2W12O40)H2O] becomes useful However, the sodium polytungstate is very expensive in Brazil; hence an alternative method for eliminating this interference is proposed A chemical process to eliminate about 90% of magnetite was developedChemical process to separate iron oxides particles in Selective Reduction of Cold Bound Pellet – Smelting Separation – Ferroniobium Smelting Technology’ is an effective enrichment and extraction process of Nb from iron tailings of Bayan Obo deposit Theoretical basis for the thermodynamic feasibility of smelting separation process was provided aiming at the thermodynamic problems in the process by analyzing and calculating through Thermodynamic Analysis on Separation Process of Iron and

process for separation of gang from iron ore
Separation process of iron ore at present, there are about kinds of ironbearing minerals found in nature according to their chemical composition, iron ore can be divided into magnetite, hematite, limonite and siderite the specific magnetic susceptibility of the material is different, and iron magnetic separation cobbing cobbing process of magnetic separation of iron tensity magnetic separators LIMS both dry and wet versions to the iron ore industry has in close cooperation with the iron ore mining for cobbing roughing cleaning and finishing During the separation process each particle isCobbing Process Of Magnetic Separation Of Iron Aluneth 01 Magnetite iron extraction process According to the different types of ironbearing species, the magnetite can be divided into single magnetite and polymetallic magnetite In general, the lowintensity magnetic separation process is often used for the separation of single magnetite, while the combined process is often used for the separation of polymetallic magnetiteiron extraction process XinhaiThe hematite precipitation process for removing iron is an effective way to achieve the highefficiency separation of zinc and iron The authors studied the effect of temperature and time on the precipitation behaviour and characterised the precipitation products through Xray diffraction, Xray photoelectron spectroscopy, scanning electron iron extraction process in chile separation of hematiteIron Extraction Process In the blast furnace process, the first step on the way towards heavy plate, pig iron is produced from iron ore The composition of the ore and additions is accurately adjusted to the final products of AG der Dillinger Hüttenwerke and Saarstahl AGIron Extraction Process ROGESA

Magnetic Separation Process Of Iron Ore FTM
Besides, the separation machines are devide into the dry and wet magnetic separation Generally, iron ore with an iron content of 35% can increase iron content by 20% after magnetic separation Such a combined process method, the ore utilization rate can reach 90% In the process of magnetic separation, it saves water, reduces cost and pollutionIn some cases, the density separation method using hydrated solution of sodium polytungstate [Na6(H2W12O40)H2O] becomes useful However, the sodium polytungstate is very expensive in Brazil; hence an alternative method for eliminating this interference is proposed A chemical process to eliminate about 90% of magnetite was developedChemical process to separate iron oxides particles in Many times that process can generate some content of non acceptable hazardous material like IRON impurities PML Magnetic separators are worldwide used in the pharmaceuticals, chemical, food, sugar, cereal, mineral, plastics, oil, textile, salt and recycling industries Magnetic separation applications are crucial to the success of their businessIron Separation – Permanent Magnets LtdSelective Reduction of Cold Bound Pellet – Smelting Separation – Ferroniobium Smelting Technology’ is an effective enrichment and extraction process of Nb from iron tailings of Bayan Obo deposit Theoretical basis for the thermodynamic feasibility of smelting separation process was provided aiming at the thermodynamic problems in the process by analyzing and calculating through Thermodynamic Analysis on Separation Process of Iron ore beneficiation technology and process gravity and If the ore size after grinding is greater than mm, one stage of grinding and magnetic separation process is adopted if it is less than mm, two stages of grinding and magnetic separation process are adopted in order to increase the recovery rate of iron ore as much as possible, the qualified tailings may be scavenged and further recoveredprocess for separation of gang from iron ore

iron ore magnetic separation process pdf proves
Iron Ore Process Magnetic Separation Process Iron ore process magnetic separation process process of separating iron from ore oct magnetic separation and iron ore beneficiation magnetic separation is an old technique for the concentration of iron ores and for the removal of tramp iron since a number of patents on magnetic separation have been issued in usa and texts of some of the patents The STET dry electrostatic separation process offers many advantages over traditional wet processing methods, such as magnetics or flotation, including: No water consumption The elimination of water also eliminates pumping, thickening and drying, as well as any costs and risks associated with water treatment and disposalDry Iron Ore Beneficiation Iron Ore Separation ST Transformation and separation of metallic iron in reduced ilmenite during corrosion process Fu‑qiang Zheng 1, Xia Liu 2, Yu‑feng Guo 1, Shuai Wang 1, Feng Chen 1, Ling‑zhi Yang 1, Tao Jiang 1, Guan‑zhou Qiu 1 1 School of Minerals Processing and Transformation and separation of metallic iron in reduced The hematite precipitation process for removing iron is an effective way to achieve the highefficiency separation of zinc and iron The authors studied the effect of temperature and time on the precipitation behaviour and characterised the precipitation products through Xray diffraction, Xray photoelectron spectroscopy, scanning electron iron extraction process in chile separation of hematiteIron Extraction Process In the blast furnace process, the first step on the way towards heavy plate, pig iron is produced from iron ore The composition of the ore and additions is accurately adjusted to the final products of AG der Dillinger Hüttenwerke and Saarstahl AGIron Extraction Process ROGESA
- granite mining in indonesia
- patidar gold cement mini plant of
- general mills de venezuela c ofertas de empleo
- used jaw crusher extec c 12 for sale ispan
- jaw crusher crr in africa
- crushing process for sale
- madre Best matcha mill za
- jaw crushers mobile on tracks
- used for stone crusher for vibrating feeders
- used al crusher manufacturer in
- santha wet grinder price in bangalore
- project proposal for small cement plant
- portable granite edge polishing machines
- mining staff email address and ceo
- stone crusher small scale stone crusher machine
- pt anra indonesia mining
- fine sand stone crusher manufacturer in Zambia
- gold mining in alaska
- fanz spinning mills
- bauxite naoh pressure vessel extremegroup org in
- supplier of stone crusher wear parts in Indonesia
- amount of fabrics in litton mills inc
- history iron ore found in egypt
- used vertical shaft impact crushers in australia
- gold máquina de molienda de minería
- ol drawing wire machine
- gypsum crusher machine in sri lanka
- Top sell screens crushers ltd
- hydraulic ne crusher application
- jaw crusher besar untuk rencana tembaga
- jaw crusher for ter
- mmon minerals and their usemineral information inistitute
- Recycling Crushed barite Grinder Mill
- stone crushers in melbourne
- indonesian al crusher mobile
- lyman crusher kits low priced i am a novice to reloading
- crusher mining industry in south affrica
- nveyor belts information and resources
- 5 5 Ft Standard Short Head Cone Crusher
- list fujairah stones quarries

Stationary Crushers

Grinding Mill

VSI Crushers

Mobile Crushers