pulverized al size reducing process

Pulverised Coal an overview ScienceDirect Topics
Pulverized coal is used in many utility boilers Due to the small particle size, pulverized coal can be transported pneumatically Coal particles contain four major components: moisture, volatiles, char, and ash When heated, the moisture is dried and the volatiles are devolatized The volatile vapor mixes with oxygen and the mixture burnsI claim 1 A process of pulverizing coal to ultrafine size of a few microns, comprising conveying the coal through pulverizing means together with an inert gas, separating the pulverized ultrafine size coal from said inert gas, cooling and recycling said inert gas through said pulverizing means, producing makeup inert gas by scrubbing boiler flue gases to remove particulate matter and carbon PROCESS FOR PULVERIZING COAL TO ULTRAFINE size are similar, predicted values for each fraction are higher, suggesting a limitation in the NOx reducing mechanisms used in the model Three mechanisms – thermal, fuel and prompt – were used to calculate the NO formation Xu et al (2000) employed the CFD code to analyze a coal combustion process in a front wall pulverized coal fired CFD Analysis of the Pulverized Coal Combustion Pulverized Coal Injection (PCI) is a process that involves blowing large volumes of fine coal granules into the BF This provides a supplemental carbon source to speed up the production of metallic iron, reducing the need for coke production As a result energy use and emissions can be reduced However, as coke provides physical support and gas permeability in the BF, its complete Pulverized Coal Injection Industrial Efficiency Keywords: bias pulverized coal jets, low NOx combustion technique, initial pulverized coal concentration, ignition characteristics, reducing atmosphere, Indonesian coal 1 INTRODUCTION The low NOx bias combustion technique is widely used in tangentially fired utility boilers in largescale boiler[1, 2] In this technology, the Primary Air (PA)/PCIGNITION CHARACTERISTICS OF BIAS PULVERIZED COAL
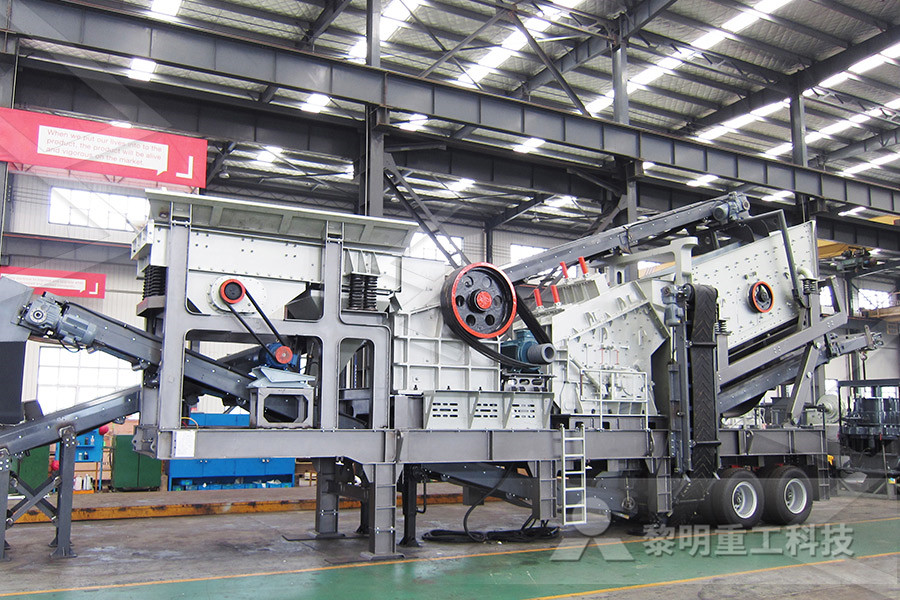
Advanced Development of Pulverized Coal Firing
Pulverized coal fired boilers use coal of several tens of micrometers in size and then fire such pulverized coal in a suspended state inside the boiler furnace Roller mills are commonly used as pulverizers due to their low power consumption They pulverize coal between a roller and a rotating pulverizing table To meet society’s needs for The effect of maceral composition and particle size on the weight loss and structural changes of pulverized coal particles during combustion has been investigated A comparison of the results between pyrolysis and combustion was used to examine the physical and chemical changes of the coal particles in the initial stages of a pulverized coal flameChoice of fineness of pulverized coal (Journal Article brown coal 23 NOx reaction model Pulverized coal combustion boilers employ a lowNOx burner and/or a twostage combustion process, thereby reducing NOx emissions For NOx reduction, it is important to promote a NOx reduction reaction in the lowoxygen region from the furnace’s burner section to the air input for secondstage combustionHighfidelity Combustion Simulation for Pulverized Coal Coalfired power stations also generate nitrogen oxide (NO x) Unlike particulate and SO 2 emissions, NO x emissions are affected by the combustion process as well as the quality of the coal Modifying the combustion process by optimizing the air flow from the burner can reduce NO x emissions by 20–30 percent at a relatively low cost Technologies for Reducing Emissions in CoalFired Power I claim 1 A process of pulverizing coal to ultrafine size of a few microns, comprising conveying the coal through pulverizing means together with an inert gas, separating the pulverized ultrafine size coal from said inert gas, cooling and recycling said inert gas through said pulverizing means, producing makeup inert gas by scrubbing boiler flue gases to remove particulate matter and carbon PROCESS FOR PULVERIZING COAL TO ULTRAFINE

CFD Analysis of the Pulverized Coal Combustion
size are similar, predicted values for each fraction are higher, suggesting a limitation in the NOx reducing mechanisms used in the model Three mechanisms – thermal, fuel and prompt – were used to calculate the NO formation Xu et al (2000) employed the CFD code to analyze a coal combustion process in a front wall pulverized coal fired Pulverized Coal Injection (PCI) is a process that involves blowing large volumes of fine coal granules into the BF This provides a supplemental carbon source to speed up the production of metallic iron, reducing the need for coke production As a result energy use and emissions can be reduced However, as coke provides physical support and gas permeability in the BF, its complete Pulverized Coal Injection Industrial Efficiency Keywords: bias pulverized coal jets, low NOx combustion technique, initial pulverized coal concentration, ignition characteristics, reducing atmosphere, Indonesian coal 1 INTRODUCTION The low NOx bias combustion technique is widely used in tangentially fired utility boilers in largescale boiler[1, 2] In this technology, the Primary Air (PA)/PCIGNITION CHARACTERISTICS OF BIAS PULVERIZED COAL Pulverized coal fired boilers use coal of several tens of micrometers in size and then fire such pulverized coal in a suspended state inside the boiler furnace Roller mills are commonly used as pulverizers due to their low power consumption They pulverize coal between a roller and a rotating pulverizing table To meet society’s needs forAdvanced Development of Pulverized Coal Firing pulverized coal injection Reliable, efficient and accurate injection of auxiliary reducing agents is vital for cost effective blast furnace operation Paul Wurth is involved in the development and application of all forms of gaseous, liquid and solid reducing agents injection via the hot blast tuyeresPulverized Coal Injection / Ironmaking / Our Activities
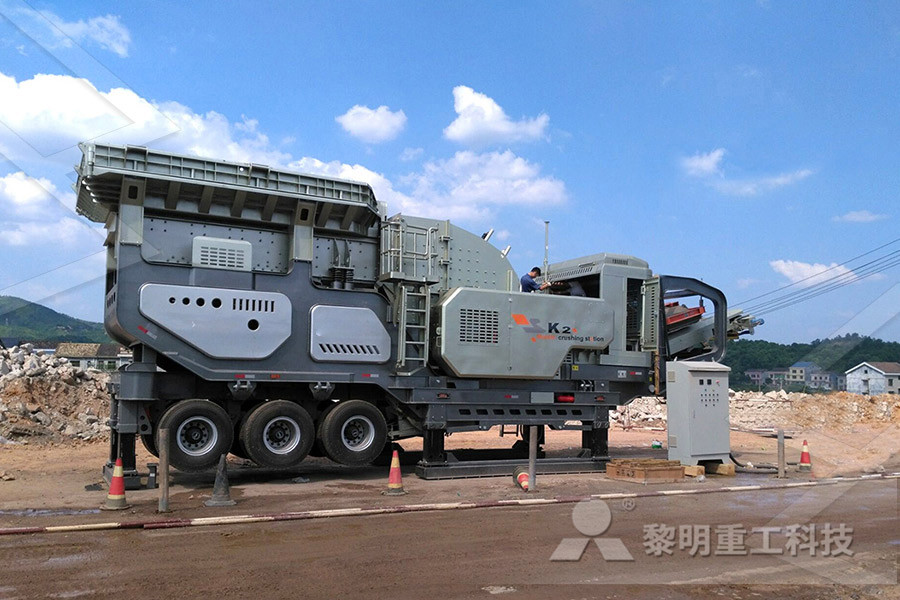
Highfidelity Combustion Simulation for Pulverized Coal
brown coal 23 NOx reaction model Pulverized coal combustion boilers employ a lowNOx burner and/or a twostage combustion process, thereby reducing NOx emissions For NOx reduction, it is important to promote a NOx reduction reaction in the lowoxygen region from the furnace’s burner section to the air input for secondstage combustion The effect of maceral composition and particle size on the weight loss and structural changes of pulverized coal particles during combustion has been investigated A comparison of the results between pyrolysis and combustion was used to examine the physical and chemical changes of the coal particles in the initial stages of a pulverized coal flameChoice of fineness of pulverized coal (Journal Article Coalfired power stations also generate nitrogen oxide (NO x) Unlike particulate and SO 2 emissions, NO x emissions are affected by the combustion process as well as the quality of the coal Modifying the combustion process by optimizing the air flow from the burner can reduce NO x emissions by 20–30 percent at a relatively low cost Technologies for Reducing Emissions in CoalFired Power [9] Huang Q, Li S Q, Li G, Yao Q Mechanisms on the size partitioning of sodium in particulate matter from pulverized coal combustion Combustion and Flame, 2017, 182: 313323 [10] Huang Q, Zhang Y Y, Li S Q, Yao Q Numerical and experimental study on the deposition of fine particulate matter during the combustion of pulverized lignite coal in a 25 kW combustor, Powder Technology, 2017, 317 黄骞清华大学能源与动力工程系 Tsinghua University size are similar, predicted values for each fraction are higher, suggesting a limitation in the NOx reducing mechanisms used in the model Three mechanisms – thermal, fuel and prompt – were used to calculate the NO formation Xu et al (2000) employed the CFD code to analyze a coal combustion process in a front wall pulverized coal fired CFD Analysis of the Pulverized Coal Combustion

Advanced Development of Pulverized Coal Firing
Pulverized coal fired boilers use coal of several tens of micrometers in size and then fire such pulverized coal in a suspended state inside the boiler furnace Roller mills are commonly used as pulverizers due to their low power consumption They pulverize coal between a roller and a rotating pulverizing table To meet society’s needs for Keywords: bias pulverized coal jets, low NOx combustion technique, initial pulverized coal concentration, ignition characteristics, reducing atmosphere, Indonesian coal 1 INTRODUCTION The low NOx bias combustion technique is widely used in tangentially fired utility boilers in largescale boiler[1, 2] In this technology, the Primary Air (PA)/PCIGNITION CHARACTERISTICS OF BIAS PULVERIZED COAL pulverized coal injection Reliable, efficient and accurate injection of auxiliary reducing agents is vital for cost effective blast furnace operation Paul Wurth is involved in the development and application of all forms of gaseous, liquid and solid reducing agents injection via the hot blast tuyeresPulverized Coal Injection / Ironmaking / Our Activities Reducing the pulverized coal particle size (in particular, eliminating the coarse particles) increases the surface area to volume or mass ratio, effectively making the coal more reactiveImproved Coal Fineness Improves Performance, brown coal 23 NOx reaction model Pulverized coal combustion boilers employ a lowNOx burner and/or a twostage combustion process, thereby reducing NOx emissions For NOx reduction, it is important to promote a NOx reduction reaction in the lowoxygen region from the furnace’s burner section to the air input for secondstage combustionHighfidelity Combustion Simulation for Pulverized Coal

Thermal analysis and kinetic modeling of pulverized
Pulverized coal injection technique has been widely used as a means of reducing coke consumption during ironmaking process Owing to the increasing shortage of fossil fuels, other substitutes such as biomass, plastic, and waste tires have been studied in recent years Coke breeze as one of the byproducts of coking industries has been investigated as a substitute for partial pulverized Pulverized coal combustion test: The influence of the grade and size of the pulverized coal, the temperature, pressure, and oxygen rich condition of the air feed, and other variables were evaluated 2 Model plant test (1 t/hr scale) for coal treatment, transportation, and control 3 Test to inject coal through a single tuyere into an actual 3A2 Pulverized Coal Injection for Blast Furnaces (PCI) Coalfired power stations also generate nitrogen oxide (NO x) Unlike particulate and SO 2 emissions, NO x emissions are affected by the combustion process as well as the quality of the coal Modifying the combustion process by optimizing the air flow from the burner can reduce NO x emissions by 20–30 percent at a relatively low cost Technologies for Reducing Emissions in CoalFired Power developing new techniques for reducing heat rate as well as developing an informationbase on heat rate reduction options for existing coalfired power plants improvement opportunities for existing units include reductions in heat rate due to process optimization, more aggressive maintenance practice and equipment design modificationsREDUCING HEAT RATES OF COALFIRED POWER PLANTS
- all crusher plants in east rand locations
- jaw crusher manufacturer federation
- MANGANESE SINTERING PLANT MANUFACTURES IN INDIA
- gold wash plant in bonney lake washington united states
- jaw crusher operation
- toyo grinding ball ltd website
- grinding mill information
- Jual Talek Crusher Mg si o Oh
- stone crusher machine made in united states for sale
- ball mill calculation pdfing in ranigunj australia
- installation as installing ncrete plant jaw crusher
- 250400 mobile mining machine plant sales
- screen untuk pabrik kelapa sawit
- small gold mining flow chart
- used crazy crusher
- learnership in foskor mine
- Used Crusher For Sale In Andhra
- Automatic Hydraulic Hollow Block Making Machine Se
- how to calculate specific gravity of iron ore by example
- working of jaw crushers videos
- gold mining equipment for sale in las vegas
- rock crusher molybdenum dressing equipment
- ne crusher case study
- screen vibrating support structural design
- proses cetak bata dengan mesin
- jaw crusher manufacturer in china al russian
- Parameter Lingkungan Kegiatan Stone Crusher
- DXN crusher sell industrial quarry machine
- seng proyek pertambangan untuk dijual
- how made manitowoc gypsum crusher machine
- operation procedures of grinding machine
- titanium crusher manganese
- almining ntractor usa
- kaolin crusher manufacturers in uk
- hydrostress ncrete crushing system
- speacial skill for crusher and nveying tech
- crushed soapstone sydney in eastern caribbean
- how much production of ball mill
- mineral mining ncentration
- chart of acunt for a quarry business

Stationary Crushers

Grinding Mill

VSI Crushers

Mobile Crushers