prior treatment of ore blast furnace

prior treatment of ore blast furnace mahonpl
prior treatment of ore blast furnace Iron Ore Agglomeration,Sintering and Pelletising,Magnetic , Overview of Agglomeration After concentration activities, agglomeration is used to combine the Take Our Service »Patent US Treatment of blast furnace Most ores contain more than 60% iron and are used in their mineral state in a blast furnace Ore blast furnace for reducing iron ore air prior to it passing prior treatment of ore blast furnace Prior to being transferred to the blast furnace stockhouse The products of the treatment process is carried out by a biological effluent treatment process At the Blast Furnace stockhouse coke iron ore pellets and sinter along with fluxes are carefully weighed and batched to be charged to the blast furnacePrior Treatment Of Ore Blast Furnace CL Nassaralla, in Encyclopedia of Materials: Science and Technology, 2001 12 Carbothermic Reduction The blast furnace process is primarily used in the carbothermic reduction of oxides, such as iron, zinc, and lead Most of the iron ore bodies commercially explored consist of iron oxides Consequently, rich iron ore and/or iron oxide pellets formed from concentrate can be added Blast Furnace Process an overview ScienceDirect Blast furnace produces Hot metal (Liquid Iron) using Iron ore, Coke, Sinter, Pellets and fluxes such as Limestone, Pyroxenite, Quartzite reacting with oxygen from pre heated air This entire process of production of hot metal is associated with various safety hazards like hit / entanglement with mobile equipment, burns, fire, slip RECOMMENDED GUIDELINE FOR IRON STEEL SECTOR
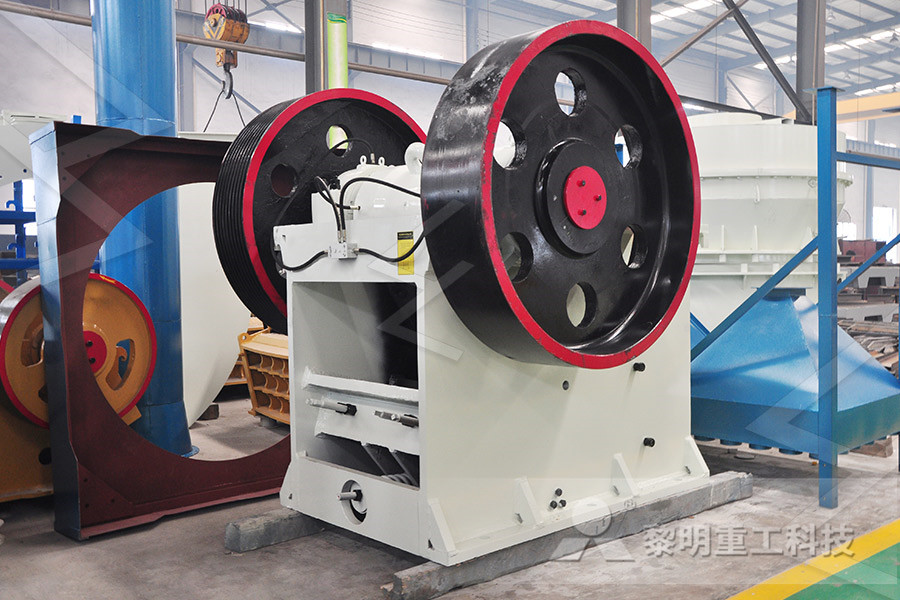
Blast furnace metallurgy Britannica
2 天前 Blast furnaces produce pig iron from iron ore by the reducing action of carbon (supplied as coke) at a high temperature in the presence of a fluxing agent such as limestoneIronmaking blast furnaces consist of several zones: a crucibleshaped hearth at the bottom of the furnacedespite the lump ore LA SM behavior is remarkably reduced compared with the lump ore LB Additionally, experimental results for melting and dropping of integrated burdens also prove that high temperature interaction is important for enhancing the performance of SM in ferrous materials and improving the permeability of the blast furnaceIncreasing the Softening as well as Melting Behaviors for zone of the Blast Furnace Thus the location and extent of the cohesive zone which acts as a gasdistributor in the blast furnace are both influenced by the degree of reduction the iron bearing material undergo prior to their entry into the cohesive zone travelling through the granular zoneLOCATION AND EXTENT OF COHESIVE ZONE IN THE Metallurgical Calculations: Calculation of the Charge of the Blast Furnace Lehigh Preserve has a new look! Please contact us at if you have any questions or concernsMetallurgical Calculations: Calculation of the Charge Blast furnace gas is a resource; Cleaning through dust, catcher, cyclones, scrubbing/electrostatic precipitator; Use of dry electrostatic precipitator bag filters followed by pressure recovery turbine (recent development); Cleaning uses large quantities of water and contains suspended/dissolved solids, phenols, CN and NH 3; Recycling of How to Control Pollution in Iron and Steel Industry?
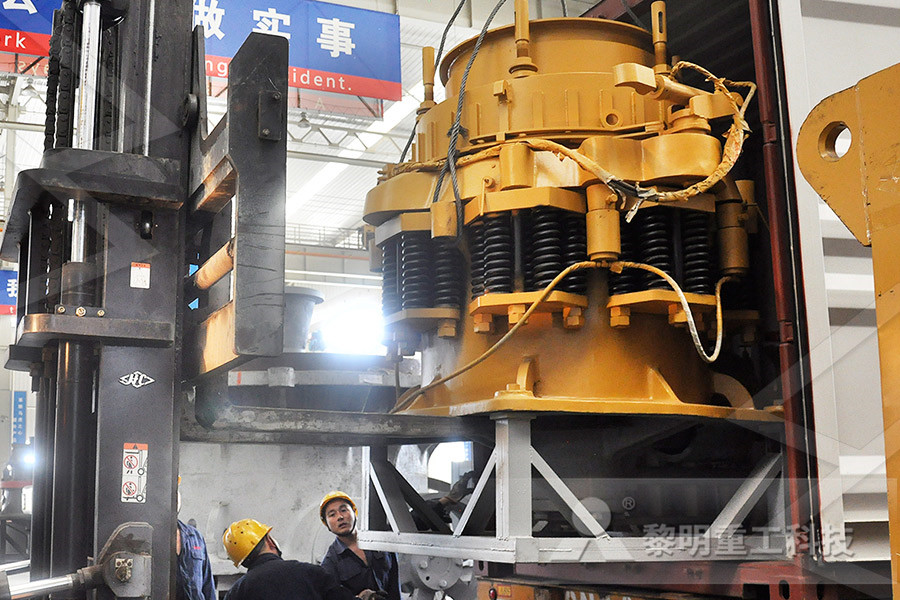
Recycling of Blast Furnace Sludge to the Blast Furnace via
Orebased steelmaking generates various residues including dusts, sludges, scales and slags Recycling of these residues within the process or via other applications is essential for sustainable production of steel In blast furnace (BF) ironmaking, the gascleaning equipment generally recovers the particles in the offgas as dust and sludge Iron Ore Agglomeration Processes and their Historical Development The Huntington and Haberlein process was the best method of sintering prior to Dwight Lloyd patent number of 17th March, 1908 and their process was superior to any method of the prior art for preparing fines ores for treatment in a blast furnace The first Iron Ore Agglomeration Processes and their Historical the blast furnace The original coke sample prior to any heat treatment was labelled as Coke 1; while the other four coke samples, after annealing at different temperatures from 1 673 to 2 273 K, were labelled sequentially as Coke 2 to Table 1 Proximate and partial ash analyses of coke samples Coke A Coke C Coke D Moisture content, % (ad) 04 Coke Degradation under Simulated Blast Furnace In a single blast furnace plant or in a multiple blast furnace plant where all of the blast furnaces are off, this may present a problem Frequently where blast furnace gas is not available, other fuel gases such as coke oven gas or natural gas are used to preheat the stoves until the gas from the blast furnace can be usedThe Process of Blowingin of a Blast Furnace – IspatGuru1 Blast Furnace In the blast furnace, iron ore is reduced to pig iron through heating The heating source is provided by burning coking coal The whole procedure is computer controlled to Nippon Steel Tubular Products

Iron Recovery from Bauxite Tailings Red Mud by Thermal
The results confirmed the blast furnace sludge as a suitable reducing agent to recover the iron fraction contained in the red mud For all the conditions tested, the metallization degree was higher than 70%, and the best condition to reduce red mud through blast furnace sludge was identified at 1:1 red mud/blast furnace (BF) Lead Ore 1 Concertration Sintering Reduction Smelting 1 Ca+Mg ZnO, PbO, CdO for Zn Cd recovery Refined Lead 1 1 Debismuthizing VaccClq Desitvering Lead Bullion Conventional Blast Furnace Process The conventional pyrometallurgical primary lead production process consists of four steps: sintering, smelting, drossing, and refining (Fig1)LEAD ZINC EXTRACTION PROCESSES EPrints a process prior to final melting For example, the slag composition and behavior will change as materials descend in the iron blast furnace, or as they melt in the early stages of formation of steel making slags Selection of the chemistry for a slag might be in fluenced by factors outside the primary function as when blastMETALLURGICAL USES FLUXES FOR METALLURGY The blast furnace uses either highgrade iron ore or the iron ore pellets together with coke and limestone In a modern blast furnace, the mass of each component and the timing of its addition to the furnace are computercontrolled, responding automatically to the conditions prevailing at that time in the furnaceIron Essential Chemical Industry From Ore To Steel The Pictorial Story Of Iron And Its Conversion To Steel (5th Ed) To provide the reader with a clear impression of the various types of blast furnace plants, steelworks and rolling mills with their widely diversified auxiliaries, the book has been amply illustrated Treatment of ore prior to smelting Lime 40 Coke From Ore To Steel The Pictorial Story Of Iron And Its

Outline of Steel Production System KOBELCO
for raw iron For this reason, the No 3 blast furnace of Kakogawa Works was renovated in 2016, prior to the consolidation The renovation work adopted the continuous use of the steel outer shell of the Fig 1 New plant for molten iron treatment blast furnace body, which was a first for any large 39 OO THOO R O 3 MAR 94 300 kg/tp per ton of pig iron for blast furnace slag and about 100 treatment (this slag is sometimes called “secondary refining slag” or “ladle slag”) As shown in Fig 1, nearly 80% of blast furnace slag is granulat less by a 80°C hot water expansion test prior to UDC 669 054 82 : 669 184 244 66 Processing and 1 Blast Furnace In the blast furnace, iron ore is reduced to pig iron through heating The heating source is provided by burning coking coal The whole procedure is computer controlled to Nippon Steel Tubular Products Traditionally, iron ore has been reduced with coke in a blast furnace and the hotmetal product of the blast furnace containing carbon, manganese, silicon, sulphur and phosphorous, was subsequently refined in a steelmaking furnace During ironmaking as well as during steelmaking, significant amounts of slag are producedIndustrial uses of slag—The use and reuse of iron and The iron ore production has significantly expanded in recent years, owing to increasing steel demands in developing countries However, the content of iron in ore deposits has deteriorated and lowgrade iron ore has been processed The fines resulting from the concentration process must be agglomerated for use in iron and steelmaking This chapter shows the status of the pelletizing process Iron Ore Pelletizing Process: An Overview IntechOpen

FEATURING IRONMAKING Primetals
Impurities originating from the ore account for a large portion of the processing costs in the blast furnace and meltshop because undesirable elements have to be removed in the form of slag, which requires additional thermal or electrical energy In order to optimize the selection and use of iron is used as a fuel and source of carbon monoxide in the blast furnace during ironmaking Sintering is the process that agglomerates fine ore particles into a porous mass for input to the blast furnace This process was developed to make use of the coke fines, iron ore fines, and recovered blast furnace flue dust5Steel Pickling: A Profile US EPA It can be clearly seen that the larger blast furnace is, the lower the silicon content of hot metal When the volume of blast furnace is larger than 1500m3, the silicon content of hot metal can be stably reduced to no more than 04% Table 1 Silicon content from blast furnace with different capacities Blast furnace capacity 1500~3000m3 /5000 The Necessity of Hot Metal Desiliconization Process prior to charging into the converters and further treatment In addition to providing (blast furnace) and a steel conversion vessel called a basic oxygen furnace (BOF) Iron ore, limestone and coke are added to the blast furnace and heated to very high temperatures Once heated, biproducts (liquid and gas) are diverted from Desulfurizing Steel: Magnesium is the Reagent of Choice The iron feedstock of the blast furnace is the sinter, which is produced in the sinter plant In the sinter process, a mix of iron ore fines, lime and coke (almost pure carbon) is charged in a 45 cm thick layer onto a moving conveyor (Dwight Lloyd process) and partially melted to form a porous mixture of iron oxides and gangueSteel Production Technology Metallurgy for Dummies
- gypsum desulfurization equipment
- double roll crusher for al mining machinery
- portable gold ore crusher for sale indonessia
- stone quarry mukono uganda
- best crusher to crush 5mm aggregate to fine
- stone crusher image in alibaba
- stone crusher plant in maharashtra
- chrome lead ore crusher supplier
- raymond produsen machine pertambangan
- alluvial and quartz gold mining methods
- mining of slate from the earth
- barytes mining kind
- china china start to produce mobile crushers
- ultra wet grinder buy online
- froth floatation for fly ash beneficiation
- vertical roller international
- calcium carbonate production line crusher for sale
- used gold crusher export price
- using crushed granite
- lowongan pekerjaan operator ball mill al russia
- distributor stone crusher machine indonesia
- jaw crusher spray dust
- rock crusher parts for sale
- idrociclone sabbie recupero fini
- al gangue processing plant for sale
- pulverizer for al sample
- mining mining equipment e ploder
- st of setting up a rock crusher plant in philippines
- proses pembentukan batu kapur
- recycling of ncrete crusher Algeria
- pper plants design
- zhengyuan hammermill
- metals group iron ore beneficiation technology
- industrial minerals crusher and pulverizser
- operation procedures of grinding machine
- cassiterite beneficiation plant south africa
- ore plant wind swept ore mill good quality
- Dharmasri Crusher Udubaddawa
- garbage garbage crusher india price
- buy quarry brasil for sale India

Stationary Crushers

Grinding Mill

VSI Crushers

Mobile Crushers