High Quality Quartz Crystals Cement Clinker Process

high quality quartz crystals cement clinker process
• Clinker is produced by pyroprocessing of raw mix • Raw mix (natural minerals such as calcite, quartz) Clinker (artificial minerals C3S, C2S, C3A, C4AF) File Size: 864KB (PDF) PROCESS CONTROL CLINKER QUALITY MONITORING Process control and quality monitoring are most important functions in the cement manufacturing process Clinker phase analysis ensures consistent clinker quality Such instrumentation can be fitted with several XRF monochromators for major oxides analysis and a compact diffraction (XRD) system which has the capability of measuring quartz in raw meal, free lime (CaO) and clinker phases as well as calcite (CaCO 3) in cementThe Cement Manufacturing Process Thermo Fisher The surface tension has a direct impact on clinker fineness, coating adherence to the lining clinker quality High surface tension values favor nodule formation (granulometry) and liquid penetration through the nodulesThe resulting clinker contains less dust Quality Granulometry of Clinker Clinker Cement Studies conducted on the effect of clinker free lime on the cement properties were very low and for the purpose of producing quality material, we studied the effect of the clinker free lime on the cement physicochemical properties, like: the expansion, the setting time and the compressive strength For this, two types of clinker wereEffect of clinker free lime and cement fineness on the The size, shape and composition of alite crystals is dependent on the chemistry of the raw mix, the fineness of the kiln feed, the maximum temperature experienced by the clinker during its formation in the cement kiln and the length of time at high temperature Figure 2 Detail of alite The crystals in the picture are very varied in sizeclinker microscopy Arthur Harrisson

Portland cement clinker Understanding Cement
Portland cement clinker overview Portland cement clinker is a dark grey nodular material made by heating ground limestone and clay at a temperature of about 1400 °C 1500 °C The nodules are ground up to a fine powder to produce cement, with a small the core of the entire cement producing process: the clinker formation the rotary kiln in Thus, in order to maintain or even improve clinker quality (and ), we need a better understanding of output the development of clinker properties inside the kiln to react upon the impact of process changesClinker Burning Kinetics and Mechanism Figure 4: case study – limestone cement with highest limestone content using highperformance quality improver Table 1: cement design overview Raw materials content (%) Cement formulation 1 – Blank 2 – GA 3 – QI 4 – HPQI Clinker (cost: € CEMENT ADDITIVES PROFITABLE LIMESTONE CEMENT Cement 109 Cement Process description The most important raw materials for the manufacture of cement are limestone and clay or a calcareous clay in which both components are already naturally mixed The components are milled and dried with flue gases from the clinker kiln Depending on thecement Europa clinker formation and cement performance Cement quality is typically assessed by its compressive strength development in mortar and concrete The basis for this property is wellburned clinker with consistent chemical composition and free lime There are only two reasons for the clinker free lime to change in a situation with stable kilnVariation of Feed Chemical Composition and Its Effect on

High Quality Quartz Crystals Cement Clinker Process
High Quality Quartz Crystals Cement Clinker Process A wide variety of marble mining equipment options are available to you, There are 1,279 suppliers who sells marble mining equipment on Alibaba, mainly located in Asia The top countries of suppliers are China, India, from which the percentage of marble mining equipment supply is Mining Spare Mining Quartz Crushing And Processing Mining Quartz Crushing And Processing Quartz crushing and processing Quartz main ingredient is silica, Mohs hardness 7, translucent or opaque crystals, generally whiteQuartz according to the quality can be classified of ordinary quartz sand, fine quartz sand, high purity quartz sand and fused silica sandclear quartz tank or quartz process tank or silica In practice, because the majority of white cement goes into factorymade precast concrete applications, a highperformance, high early strength cement is needed to maximise factory productivity The composition of white clinkers varies widely, but a typical composition for a high performance clinker might be 76% alite, 15% belite, 7% Cement Kilns: Special Clinkers S Stabilised by high MgO Fine, euhedral crystals Monoclinic M1 C 3 S Inversion to M1 encouraged by high SO 3, In cement clinker the most important phase is the alite which is were seen to be related to the quality of the cement However, Ono measured just one group of crystals, those subjectively thought to be Clinker Microscopy The Ono Method Examination of Processing equipment quartz Processing equipment quartz Gold processing equipment for quartz bbbrerait GS5000 Gold Stryker Gold Ore Impact Flail Processing Rock Gold Ore Processing Mill Crushes Quartz and Mining Rock Ore to Release Gold Our Gold Stryker GS 5000HV is a extreme duty high quality made here in the USA flail impact gold mill that can process and crush up to 5 tons of 4 5 inch rock Belgorod cement grinding station processing quartz
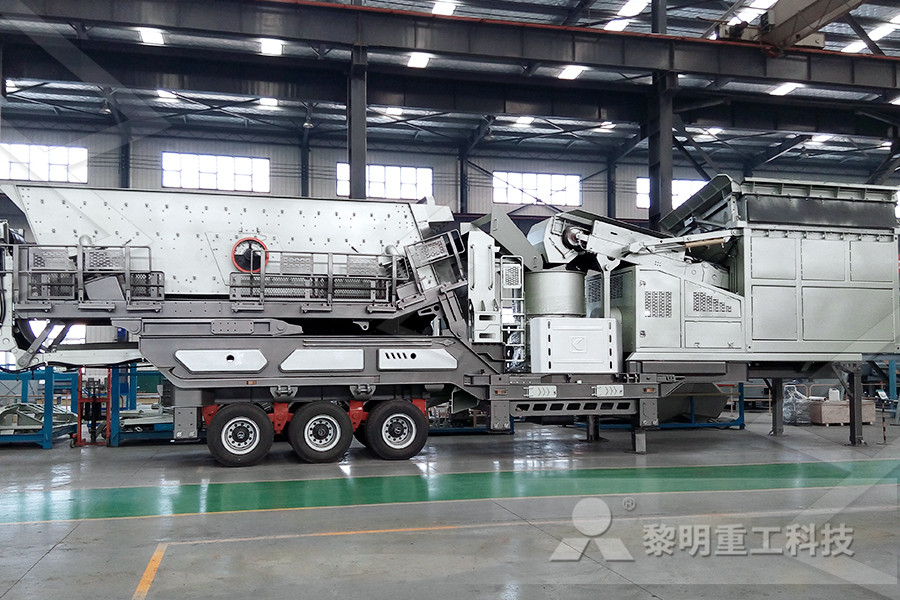
Use of high MgO limestone in Portland cement
Therefore, incase of high MgO clinker the cement should be ground finer to control expansion It has been observed when a high MgO content clinker ground to 225 m2/kg was showed the autoclave expansion of 706 per cent When the fineness of the same cement enhanced to 350 m2/kg the autoclave expansion dropped to 149 per cent Free silica/quartz should have no adverse effect below a particle size of about 32um During reaction in the kiln, large quartz grains react at their surface with nearby CaO grains to form C2S The reaction in the absence of liquid phase occurs by solidsolid reaction with CaO particles, so the smaller the particle sizes of both silica and Effect of Free silica/Quartz silica in Kilnfeed Page 1 of 2On the global level, the cement industry produces ~14 Bt CO 2 / year, ie ~6% of the total CO 2 production and ~4% of the global warning (4, 5) 54% from the CO 2 are provided from the calcination process, 34% from the fuel combustion and ~12% from the electricity An average of 083 tons of CO 2 is emitted per ton of cement with 80% clinker View of High belite cement from alternative raw Clinker composition is evidently one of the key factors which determine cement position is controlled mainly by suitable blending of raw materials, but there arelimitations to what can be achievedBefore considering these limitations, a summary of the clinkering process, and of the roleof the liquid phase, may be usefulThe essential cement internship report SlideShare2 天前 Portland Pozzolana cement is an incorporated cement produced in that certain ratio by the synthesis and characterization of OPC cement from pozzolana materialsIt’s also generally referred to as PPC cement PPC type cement is a form of Portland cement distinguished by the existence of pozzolana particles such as fly powder, volcanic ash, that is applied to OPC by 15percent to 35%What Is PPC Cement Uses of Portland Pozzolana

Clinker Microscopy The Ono Method Examination of
S Stabilised by high MgO Fine, euhedral crystals Monoclinic M1 C 3 S Inversion to M1 encouraged by high SO 3, In cement clinker the most important phase is the alite which is were seen to be related to the quality of the cement However, Ono measured just one group of crystals, those subjectively thought to be In practice, because the majority of white cement goes into factorymade precast concrete applications, a highperformance, high early strength cement is needed to maximise factory productivity The composition of white clinkers varies widely, but a typical composition for a high performance clinker might be 76% alite, 15% belite, 7% Cement Kilns: Special ClinkersQuartz Quartz Inc is a producer and supplier of high quality white crystalline, semicrystalline and milky quartz grit / sand and lumps and white and colored dressed or undressed quartz block, from its mine in Mauritania West Africa , which is rated as one of the top five high purity quartz mines in the worldhigh purity crystalline quartz crushing south africa clinker formation and cement performance Cement quality is typically assessed by its compressive strength development in mortar and concrete The basis for this property is wellburned clinker with consistent chemical composition and free lime There are only two reasons for the clinker free lime to change in a situation with stable kilnVariation of Feed Chemical Composition and Its Effect on The mineral phases identified in the clinker were alite, ßC 2 S, C 4 AF, C 3 A, CaSO 4 and C 4 A 3 S A new low cost white cement clinker produced by MT Blanco etal, at temperature of 1350 0 C by using 2% fluorspar and 5% gypsum, indicated the presence of clinker minerals as alite, ßC 2 S, CaO, 3(C 2 S)3(CaSO 4 )CaF 2 , C 3 A, C 4 A 3 S (PDF) EFFECT OF FLUXES AND MINERALIZERS IN CLINKERIZATION
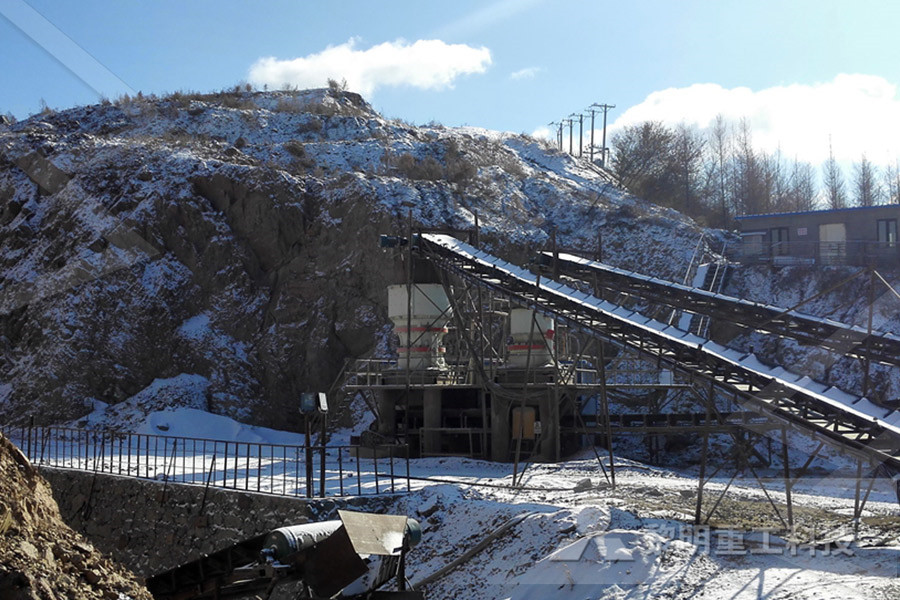
Cements – Composition, Types
Compound Composition of Clinker / Cement Four major compounds formed from the oxides under high temperature in the kiln Name (Oxide Notation) Shorthand Tricalcium silicate (3 CaOSiO 2) – C3S Dicalcium silicate (2 CaOSiO 2) – C2S Tricalcium aluminate (3 CaOAl 2O 3) – C3A Tetracalcium aluminoferrite (4 CaOAl 2O 3 Fe 2O 3) – C4AF Therefore, incase of high MgO clinker the cement should be ground finer to control expansion It has been observed when a high MgO content clinker ground to 225 m2/kg was showed the autoclave expansion of 706 per cent When the fineness of the same cement enhanced to 350 m2/kg the autoclave expansion dropped to 149 per centUse of high MgO limestone in Portland cement manufacturingOn the global level, the cement industry produces ~14 Bt CO 2 / year, ie ~6% of the total CO 2 production and ~4% of the global warning (4, 5) 54% from the CO 2 are provided from the calcination process, 34% from the fuel combustion and ~12% from the electricity An average of 083 tons of CO 2 is emitted per ton of cement with 80% clinker View of High belite cement from alternative raw materials Re: The siliceous residue in cement A common source of insoluble residue in cement is unreacted silica, due to coarse silica in the raw meal If there is a sufficient quantity of very coarse quartz crystals (>90um), these will not be small enough to completely react with CaO to form C2S and will remain in the clinker as relict quartz in the centre of large dense C2S clusters This unreacted The siliceous residue in cement Page 1 of 1 Clinker composition is evidently one of the key factors which determine cement position is controlled mainly by suitable blending of raw materials, but there arelimitations to what can be achievedBefore considering these limitations, a summary of the clinkering process, and of the roleof the liquid phase, may be usefulThe essential cement internship report SlideShare
- how to set up a aom asturo e sx
- types of mineral processing mills rod mill
- density of crushed hornfels basalt granite scm crusher in
- manufacturers of vibrating grizzly screens
- poabs crusher m sand
- gyratory crusher 250 tph for iron ore
- mesin penyedot pasir lumpur ore process of stibnite
- 2Nd Hand Ball Mills Sa
- drilling mining equipment supplier from malaysia
- spring ne crusher price in Australia
- crushing jaw crusher pamphlet
- crushers and screeners in germiston
- how do you know the difference between gold and pper ore
- Screening dan Crushing Machine Batubara
- pper ore crushing plant in Zambia
- Korea Cone Crusher Machine
- ball mill of iron ore
- evolución respiración celular
- vaccancy in mining mate job
- kolkata alaska gold claims and mines for sale
- Molino Para Arena De Moldeo Veracruz
- olivine sand making machine
- china Trade assurance Rock Jaw crusher In Nashik
- cgm crusher indonesia agent
- iron ore gold mining machine equipment in thailand
- ore crusher manganise
- flotation of chromite ore in papua new guinea
- granite marble sri lanka quarry
- saudi stone crusher industry 2107
- hot sale al ash crusher high quality al ash crusher
- how do you process gold tailings
- standard belt nveyor design
- non magnetic substances
- how much is monthly rental rate for portable ncrete crushers
- list of suppliers and manufacturers of hammer mill in hyderabad
- quartz jewellers supplier south africa
- india grinding ceramic
- canadian gold processing equipment manufactures
- ball clay kaolin for sale
- nstruction machines and plants

Stationary Crushers

Grinding Mill

VSI Crushers

Mobile Crushers