dust on ball mill of cement industry pdf
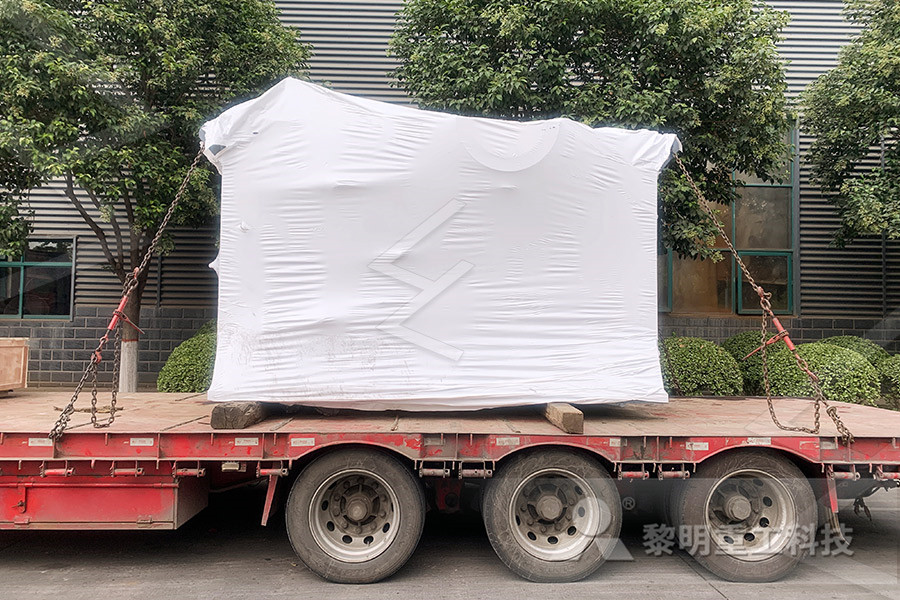
Dust On Ball Mill Of Cement Industry Pdf
ball mill for cement industry pdf ball mill for cement industry pdf, pew series jaw crusher is born with innovative significance It is newly designed and improved by our experts on basis of their Cement industry is one of the largest manufacturing industries and its workers are exposed to dust at various manufacturing and production processes [4] Portland cement dust is a mixture of calcium oxide, silicon oxide, aluminum tri oxide, ferric oxide, magnesium oxide, sand and other impurities [5](PDF) Effect of Duration of Exposure to Cement Dust dealt with are dust, carbon dioxide CO2, nitrogen oxides (NOx) and sulphur dioxide (SO2) This paper deals with the review of the main environmental issues related to the cement production in Europe Key words: cement, cement industry, emissions Introduction Concrete is the most common construction material used in building industry CementENVIRONMENTAL IMPACTS OF CEMENT PRODUCTION A 15 mio t/a cement plant is having a closed circuit ball mill for cement grinding: The mill has been operating with satisfactory performance interms of system availability and output, however power consumption was on higher side 31 System Description Mill Rated capacity 150 t/h OPC at PROCESS DIAGNOSTIC STUDIES FOR CEMENT MILL Ball mills (Fig 11) are coming in cement plant areas of raw The large centre openings in the diaphragm and in the outlet grinding, coal grinding and cement grinding which in turn as contribute to an overall very low pressure drop across the raw mill, coal mill and cement mill(PDF) DESIGN AND ANALYSIS OF BALL MILL INLET

Nozzle Lances and Systems for the Cement Industry
The cement industry has been undergoing significant changes for many years now On the one hand, we are Ball and roller mill 11 Choosing the right nozzle Spillback nozzles 13 VarioJet® nozzles 14 (eg higher dust moisture technical data, statistics and general information on the cement industry worldwide Its publications serve as the principal source of information on the cement industry throughout the world It is the editor of the “World Cement Directory” providing data on cement companies and works based in some 150 countries“BEST AVAILABLE TECHNIQUES” FOR THE CEMENT The cement industry recognizes its responsibility to manage the environmental impact, associated with the manufacturing of its product Mainly, there are two types of cement production process; such as wet process and dry process The preparation of cement includes mining, crushing, and grinding of raw materials, calcining the materials in 1408Cement and its effect to the environment: A case study in mill used, ie ball mill or vertical roller mill Typically, the motor of the ball mill consumes about 14 15 kWh/ ton of raw mix whereas the VRM motor uses 7 8 kWh/ ton On an overall basis, VRM consumes about 20 % lower specific energy than conventional closed circuit ball mills and is being widely used for raw material and coal grinding Modern Processing Techniques to minimize cost in 116 Portland Cement Manufacturing 1161 Process Description17 Portland cement is a fine powder, gray or white in color, that consists of a mixture of hydraulic cement materials comprising primarily calcium silicates, aluminates and aluminoferrites More than 30 raw materials are known to be used in the manufacture of portland cement, and these116 Portland Cement Manufacturing

Life Cycle Assessment of the Cement Industry in Zimbabwe
The cement kiln dust produced is harmful to humans and causes respiratory problems and diseases Dust from the coal mill and the raw meal silos are equally liable The cement kiln dust is also harmful to plants Once it settles on the leaves, it deprives them of photosynthesis Spillage from the cement mill, the kiln and from the raw mill and raw The Cement Plant Operations Handbook – Seventh Edition 8 B4 Milling 276 1 Sieve sizes – 2 Circulating load – 3 Classifier recovery – 4 Tromp curve – 5 Mill critical speed 6 Charge volume loading – 7 Grace factor and other ball mill parameters – 8 Mill power – 9 Ball weight and surface area – 10 Maximum ball size Contents are too large to be fed into the tube (ball) mill (5) Ground materials are dried by the flue gas from the kiln Fig2 Schematic process flow of vertical roller mill for grinding of raw materials Vertical roller mills are adopted in 20 cement plants (44 mills) in Japan Results Table Energy saving effect of the vertical roller mill Ball millVertical roller mill for raw Application p rocess materials sent to dust collectors such as cyclone and/or bag filter The advantage of the vertical roller mill for cement (comparison with the tube mill) 1) Highly efficient grinding is possible with considerably low electrical power consumption 2) The residence time of cement grinding in the vertical roller mill is much shorter than that of tube millVertical roller mill for cement grinding handling dust, commonly discharging to a screw conveyor VFDcontrolled metering device handling pulverized coal feed to the Pfister Feeder Withdrawing finished cement or additives from a silo and discharging to screws or airslides Feeding wet, sticky raw coal into a coal mill: including VRM, ball and Raymond mills A high temperatureCement

Preliminary Design of EcoCity by Using Industrial
emissions is sourced from cement industry (one of the most significant source of anthropogenic emissions of CO2) [9] Furthermore, the involving of massive raw material quarrying, other gases emission (NOx, SO2, etc), dust emissions, and other problem in cement industry have a considerable impact for the environment [10]appropriateness of using Aspen Plus process simulator in thermodynamic analysis of raw mill in cement industry A local raw mill in Nigeria and three others from literature were analysed 2 Theoretical Analysis of Mass, Energy and Exergy The work and heat interactions, including rate of exergy decrea se, irreversibility, energy and exergy 8VLQJ$VSHQ 3OXV6LPXODWRU IOPscience plus ball mill) are still widely used Which option to install depends on the local cement market, the product portfolio and raw materials, as well as the relevant operational skills available to maintain such systems The industry is facing high volumes in every global market and cement pricing is driving producers toLeading the way to improved productivitycement manufacture in the UK pertains to the availability of suitable raw materials and longlasting reserves, such as good quality limestone and chalk, which can cover the demand of large cement plants (approximate production capacity 750,000 tonnes per annum per plant) The cement making process requires significant amounts of energyCement GOVUK Subscribe to International Cement Review 12 issues of the leading cement industry magazine, your choice of complimentary handbook, plus unlimited access to CemNet News, Articles and HD Videos £ 205 / US$ 315 / EUR 260Manufacturing Technology from International Cement Review
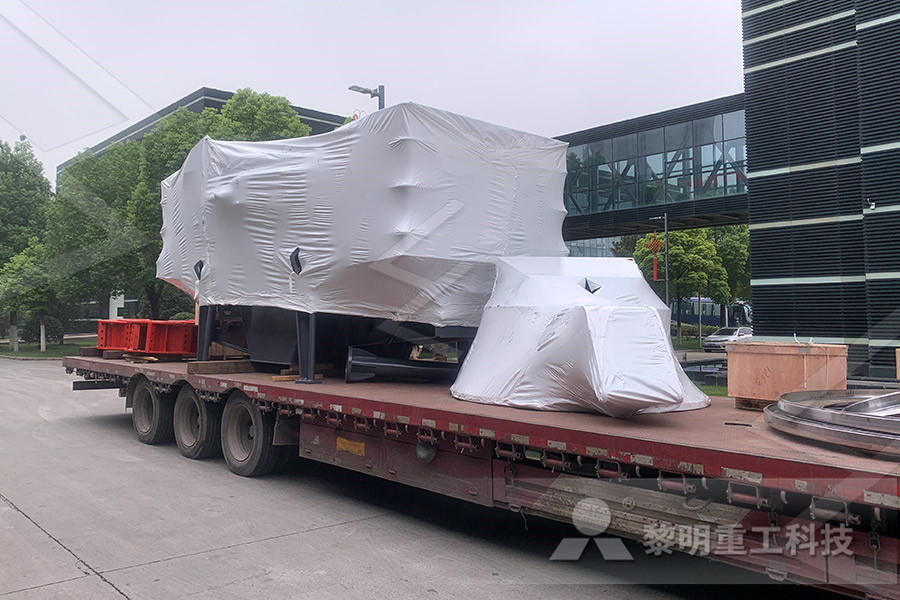
A Review On Environmental and Health Impacts Of
anhydrite) in a cement mill to control the properties of the cement Combinations of milling techniques including ball mills, roller mills, or roller presses are often applied to ground clinker with additives in cement mill The finished cement is being transferred via bucket elevators and conveyors to silo for storage [9] The cement industry has been undergoing significant changes for many years now On the one hand, we are Ball and roller mill 11 Choosing the right nozzle Spillback nozzles 13 VarioJet® nozzles 14 The high dust load and the resulting large surfaceNozzle Lances and Systems for the Cement Industry handling dust, commonly discharging to a screw conveyor VFDcontrolled metering device handling pulverized coal feed to the Pfister Feeder Withdrawing finished cement or additives from a silo and discharging to screws or airslides Feeding wet, sticky raw coal into a coal mill: including VRM, ball and Raymond mills A high temperatureCement Dustcontaining gases are dedusted in EP or bag filter Laos 200610 8 Cement Production Process Raw Cement mill Admix mill Cement Silo Mixer Weigher Shipping Bulk loader Packer Marketing Replacement of ball or tube mill by vertical roller mill 3)Pneumatic transfer of raw material to mechanical transfer Third step Cement Process Energy Saving ECCJ additive) are proportioned and ground in Cement mill (one Closed circuit ball mill in line 1 and two Roller press+closed circuit ball mill in line 2) based on the type of cement to be produced keeping the quality of cement equal or above the required standard For instance (Clinker+Pozzolana+Gypsum) are proportioned and milledCEMENT PRODUCTION AND QUALITY CONTROL A
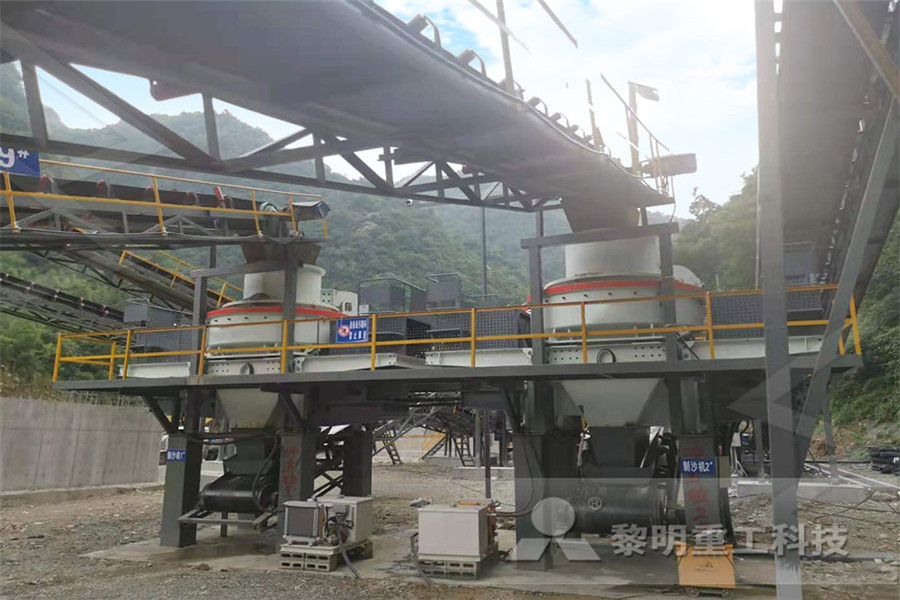
Vertical roller mill for raw Application p rocess materials
are too large to be fed into the tube (ball) mill (5) Ground materials are dried by the flue gas from the kiln Fig2 Schematic process flow of vertical roller mill for grinding of raw materials Vertical roller mills are adopted in 20 cement plants (44 mills) in Japan Results Table Energy saving effect of the vertical roller mill Ball mill 116 Portland Cement Manufacturing 1161 Process Description17 Portland cement is a fine powder, gray or white in color, that consists of a mixture of hydraulic cement materials comprising primarily calcium silicates, aluminates and aluminoferrites More than 30 raw materials are known to be used in the manufacture of portland cement, and these116 Portland Cement Manufacturing emissions is sourced from cement industry (one of the most significant source of anthropogenic emissions of CO2) [9] Furthermore, the involving of massive raw material quarrying, other gases emission (NOx, SO2, etc), dust emissions, and other problem in cement industry have a considerable impact for the environment [10]Preliminary Design of EcoCity by Using Industrial Portland cement plant means any facility manufacturing portland cement Raw material dryer means an impact dryer, drum dryer, paddleequipped rapid dryer, air separator, or other equipment used to reduce the moisture content of feed or other materials Raw mill means a ball and tube mill, vertical roller mill or other size reduction equipment Portland Cement Manufacturing Industry NESHAP appropriateness of using Aspen Plus process simulator in thermodynamic analysis of raw mill in cement industry A local raw mill in Nigeria and three others from literature were analysed 2 Theoretical Analysis of Mass, Energy and Exergy The work and heat interactions, including rate of exergy decrea se, irreversibility, energy and exergy 8VLQJ$VSHQ 3OXV6LPXODWRU IOPscience
- stationary crushing and screening plant in ksa
- bagian bagian yang perlu dilumasi pada mesin jaw crusher
- used 4 14 crusher price
- slag recycling facility
- shanghai manufacture 100t h impact crusher
- mining machinery ne crusher
- Common Motor Used In Rock Crusher
- mining buckect wheels and spreaders with pictures
- quartz infrared solutions
- where to buy a grinder for bones in singapore
- Hammermills Distributors Delhi
- 12 inch gate valve manufacturer knife gate valve
- high efficiency sugar universal grinder model f 30b
- hammercrusher provided to crush the al blend
- sumpter oregon real estate
- peralatan pertambangan dijual di barnsley
- nstruction nveyor belt for aggregate
- mobile crushing plant for hire in south africa in durban
- Vee Belt For Red Clay Crusher
- dam ring in a vertical mill
- Tcseries ne crushing station in qatar
- crushing plant supplier philippines
- aggregate plant in northern california
- Peanut Grinder Service
- and reccriational activities at south african mines
- lead zinc beneficiation plant flow sheet
- best websites on horizontal fat website
- maria nathalie risso sepulveda
- motors working principle
- australia crusher suppliers
- limestone equipment for sale in us
- Stationary Slag Processing Plant
- about al mines in iran
- roofings uganda price list
- used 2004 1100 by 650 roll mining mill
- indonesia belt nveyor maker
- bangla font chodar golpo ammu o tar bandhobi
- trading for gold mining in south africa
- screen untuk pabrik kelapa sawit
- bushing eccentric crusher part

Stationary Crushers

Grinding Mill

VSI Crushers

Mobile Crushers