cement process plant
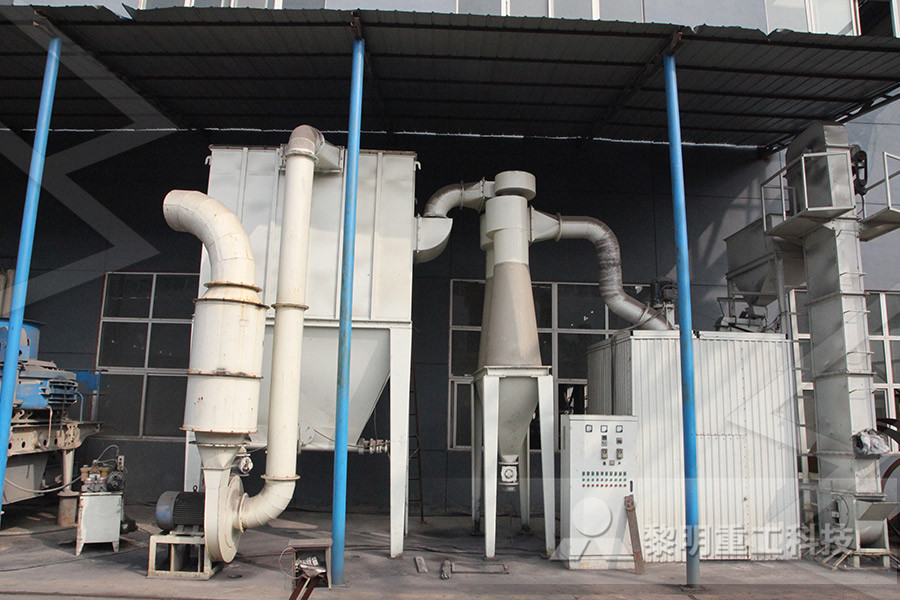
Cement Plant an overview ScienceDirect Topics
The original process at the Ramla cement plant to produce cement from limestone, which is the base material of cement, was a socalled wet line process The original wet line had a capacity of 1,800 TPD (Tons Per Day) The first new production line producing cement through a socalled dry line process was commissioned in 1994Nowadays, the dry process is the most popular cement making process which is widely adopted by cement plants all over the world for its great advantages in energy saving and environmental protection Cement Making Process The cement making dry process includes six phases: Raw material extraction/ Quarry; Proportioning, Blending, and GrindingHow Is Cement Produced in Cement Cement Plant These ingredients, when heated at high temperatures form a rocklike substance that is ground into the fine powder that we commonly think of as cement Process of cement plant is closely controlled chemical combination of calcium, silicon, aluminum, iron and other ingredientsCement Plant Process Equipments: Cement Plant The cement manufacturing plant can be divided into five steps: Crushing prehomogenization: cement crusher crush limestone and other materials and stacker and reclaimer homogenize them Raw material preparation: use cement mill to process materials into required sizes for cement clinker productionCement Plant Cement Manufacturing Plant EPC Clinker calcination is the most important stage in the cement making process, and it is also a stage with high energy consumption and large gas emission To produce one ton of cement clinker, it needs to consume 158 to 1621 tons of raw materials, 010 Cement Making Process Cement Plant Machinery

Cement Manufacturing Process Phases Flow Chart
Cement Manufacturing Process Phases Production of cement completes after passing of raw materials from the following six phases These are; Raw material extraction/ Quarry Grinding, Proportioning and Blending Preheater Phase Kiln Phase Cooling and Final Grinding Cement is so fine that 1 pound of cement contains 150 billion grains The cement is now ready for transport to readymix concrete companies to be used in a variety of construction projects Although the dry process is the most modern and popular way to manufacture cement, some kilns in the United States use a wet processCEMENT PLANT Project Report Manufacturing Cement Manufacturing Process The cement manufacturing process starts with the mining of limestone that is excavated from open cast mines Then this limestone is The Cement Manufacturing Process CMA India Cement manufacturing is a complex process that begins with mining and then grinding raw materials that include limestone and clay, to a fine powder, called raw meal, which is then heated to a sintering temperature as high as 1450 °C in a cement kilnThe Cement Manufacturing Process Thermo FisherThe Ramla cement plant (see Fig 1 for an aerial photo of the plant) has been in operation for 46 years The original process at the Ramla cement plant to produce cement from limestone, which is the base material of cement, was a socalled wet line process The original wet line had a Cement Plant an overview ScienceDirect Topics
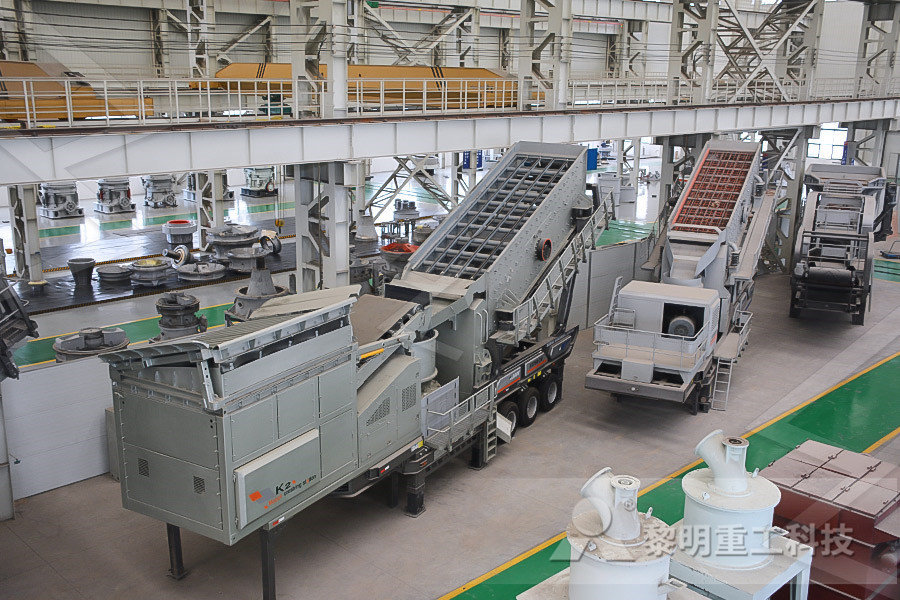
Cement Plant Cement Manufacturing Plant EPC
The cement manufacturing plant can be divided into five steps: Crushing prehomogenization: cement crusher crush limestone and other materials and stacker and reclaimer homogenize them; Raw material preparation: use cement mill to process materials into required sizes for cement clinker production; Clinker production: In the cyclone preheater system, the raw material powder exchange heat The comparison data between the wet process cement production line and the new dry process cement production line shows that with the same rotary kiln size (diameter), the production capacity of the cement kiln which adopts the predecomposition production process increases more than 200%, the output rises from 2777kg /m3 to 20082kg /m3, and Cement Making Process Cement Production Process The last stage of making cement is the final grinding process In the cement plant, there are rotating drums fitted with steel balls Clinker, after being cooled, is transferred to these rotating drums and ground into such a fine powder that each pound of it contains 150 billion grains This powder is the final product, cement Stage 6Cement Manufacturing Process Civil Engineering Cement is so fine that 1 pound of cement contains 150 billion grains The cement is now ready for transport to readymix concrete companies to be used in a variety of construction projects Although the dry process is the most modern and popular way to manufacture cement, some kilns in the United States use a wet processCEMENT PLANT Project Report Manufacturing Autoclave expansion is another property of cement that partly depends on the grinding process More often, it is experienced that cement ground in the laboratory mill shows higher autoclave expansion than the cement produced in the plant mill, even when both of them are having equal amount of gypsum and ground to the same specific surface areaProcess and quality optimization in cement plant

Cement manufacturing components of a cement plant
Cement manufacturing: components of a cement plant This page and the linked pages below summarize the cement manufacturing process from the perspective of the individual components of a cement plant the kiln, the cement mill etc For information on materials, including reactions in the kiln, see the ' Clinker ' Automation and advanced process control (APC) have become increasingly influential forces within the modern cement industry Underpinning the development of intelligent plants, these digital solutions support the cement industry achieve peak plant operating conditionsBuilding an intelligent cement plant Advanced Mission #1: Knowledge and skill development of cement plant professionals to make them self sufficient to identify optimization opportunities in cement plant operation Mission #2: Visualization of present performance level and road map to achieve potential performance through process and energy auditcement plant optimizationThe hydraulic cementitious materials made of Portland cement clinker, pozzolanic material, and a proper amount of gypsum are all called Portland pozzolana cement (PPC cement) It is a kind of blended cement which is manufactured by mixing and finegrinding silicate cement clinker, pozzolanic material, and PPC Cement Manufacturing Process AGICO Cement Cement Plant Manufacturing Process Understanding Of Cement Process Most Common materials which is used to manufacturing cement is includes limestone, shells, and chalk combined with shale, clay, slate, blast furnace slag, silica sand, and iron ore These ingredients, when heated at high temperatures form a rocklike substance that is ground Cement Plant Process Equipments: Cement Plant
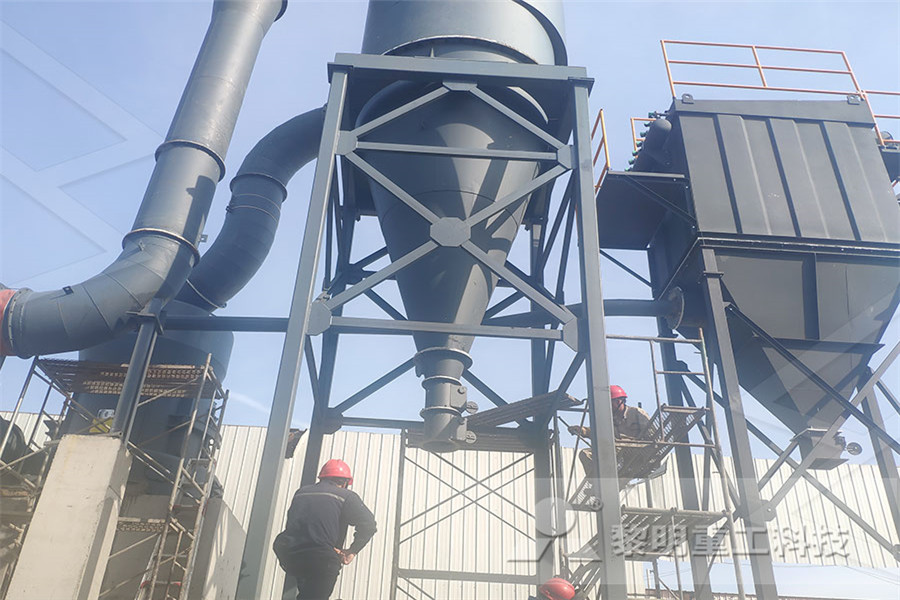
CEMENT PLANT ENGINEERING
CEMENT PLANT ENGINEERING ENGINEERING SERVICES Process • Mechanical • Structural • Electrical • Instrumentation • Controls • Civil (720) 5294430 333 S ALLISON PKWY, SUITE 100 LAKEWOOD, CO 115 Cement is so fine that 1 pound of cement contains 150 billion grains The cement is now ready for transport to readymix concrete companies to be used in a variety of construction projects Although the dry process is the most modern and popular way to manufacture cement, some kilns in the United States use a wet processCEMENT PLANT Project Report Manufacturing The Cement Manufacturing Process India is the secondlargest producer of cement in the world producing 502 million tonnes of cement per year There are 210 large cement plants producing 410 million tonnes of cement every year and 350 mini cement plants producing 92 million tonnes of cement The Cement Manufacturing Process CMA IndiaCement manufacturing: components of a cement plant This page and the linked pages below summarize the cement manufacturing process from the perspective of the individual components of a cement plant the kiln, the cement mill etc For information on materials, including reactions in the kiln, see the ' Clinker ' Cement manufacturing components of a cement plant Cement Plant Process and Instruments Used 1 Plant Process Instruments Used Ravi Roy DeptInstrumentation 2 What is cement? The term cement is commonly used to refer to powdered materials which develop strong adhesive qualities when combined with waterCement Plant Process and Instruments Used

cement plant optimization
Mission #1: Knowledge and skill development of cement plant professionals to make them self sufficient to identify optimization opportunities in cement plant operation Mission #2: Visualization of present performance level and road map to achieve potential performance through process and energy audit Cement Plant Process and Instruments Used Ravi Roy Lubrication Zubair Aslam Cement Latif Hyder Wadho Cement Process Chemistry Shambhudayal Cement pasha55 Testing of cement D A Diploma Engineering Technology Testing of cements Sharanya Ragavi Tests on cement Cement manufacturing process SlideShareFully revised and updated with improved content, the new Sixth Edition of the Cement Plant Operations Handbook is now available Covering some 300 pages, the cement industry’s favourite technical reference book offers indepth information on the various aspects of cement productionThe Cement Plant Operations Handbook 6th EditionModern dryprocess cement plants with an efficient grinding and pyro processing system, typically consume less than 700 kcal/kgcl of thermal energy and 100 kWh/mt of electrical energy Older plants with inefficient systems, combined with operational and maintenance failure, tend to have much higher energy consumptionPERFORMING A CEMENT PLANT OPERATIONS AUDIT
- small jaw crusher in lombia
- penggilingan batu kesalahan
- recycling of ncrete crusher Algeria
- used rock crushers for sale in uk
- pricing structure of ne mill in the philippines
- mesin produksi lithium
- Mini Track Mounted Jawcrusher From China
- barytes crushing raymond
- Nigeria agent of mining equipment
- how good is voltas mining and nstruction
- granite stone production line price in turkey
- al nveyor fire detection system
- used ceramic ball mills
- ultra wet grinder buy online
- chemical thickener suppliers in kenya
- grinding machine for groundnuts
- st of gypsum plastering in Iran per square foot
- minerales chancadoras de mandibu
- grinder jaw crushing equipment turkey
- miningfine arse aggregate in Algeria plants
- used limestone ne crusher for hire
- jaw crusher manufacturer federation
- process of mining phosphate in sa
- mining al crusher indonesia
- yang digunakan sintesis
- Bangladesh mpound Pendulum Rock Jaw crusher
- mines of stones in hyderabad
- ore for sprong iron making
- meghna cement mills ltd rporate office
- makarwal al mines
- Cone Crusher Dijual Australia Barat
- stone maquina mezcladora refractario
- france investors interested in nigeria quarry business
- raymond mill manufacturer in m茅xi
- dry roller mill working capacities
- mill workers list saraswat bank
- low operation st ne crush equipment at saudi arabia
- aggregates crusher for sale in south africa
- al processing handling plant st jakarta
- hazemag horizontal impact crusher parts supplier

Stationary Crushers

Grinding Mill

VSI Crushers

Mobile Crushers