energy audit on pyro processing section of cement plant
2020-06-18T21:06:38+00:00
Energy audit for pyroprocessing unit of a new
The energy audit was performed on the pyroprocessing unit of a cement plant • An applied methodology for the thermal energy audit was presented • The potential of electrical energy production from the exhaust gases was evaluated • The economic Section Specific Audit: Detailed audit of any of the sections or equipments of plant like Crusher, Raw mill, Coal mill, Pyro section, Cement mill, Process fans, Bag Filters/houses etc It includes detailed plant audit of specific section/equipment[s] and detailed audit report of the same from cementindusneedProcess and Energy Audit Cement Plant Optimization cement plant’s total thermal energy use and Imported coal constitutes 1430% (6306Mkcals)followed by minimum contribution by both the liquid fuels 44 Share of type of Energy in cement production From the piechart in Figure 46, it is clear that in the production of cement in this plant 6775% of total energyDETAILED ENERGY AUDIT AND CONSERVATION IN A Industrial energy consumption lies between 30% and 70% of the total energy consumed in selected countries Cement production is one of the most energy intensive industries all around the world This paper deals with an energy audit analysis in a cement plant different strategies are offered to reduce energy losses Generally,Energy auditing in cement industry: A case study Modern, dryprocess cement plants with efficient configuration of grinding and pyro processing systems typically consume less than 700 kcal/kgcl thermal energy and 100 kWh/mt of electrical energy Older plants have inefficient systems, which compounded with operational and maintenance inadequacies, tend to have much higher energy consumptionCement Industry Plant Process Audits Featured

Energy Modeling of the Pyroprocessing of Clinker in a
Pyroprocessing section at the plant Abstract: Optimization of energy use in the pyroprocessing of clinker is the most important step in the modern cement industry Since the process of clinkerization consumes the largest share of the purchased energy, engineers and managers at the cement plants are constantly trying to monitor the specific pyroprocessed in the cement kiln, with gypsum The cement production process requires thermal energy (heat) for production of clinker, which is the primary ingredient for the manufacture of cement Clinker production typically occurs in kilns heated to about 1450 C Clinker production is the most energyintensive process in cement manufacturingCement Kilns: Audit Report of Two Cement Plants in 51 Grouping of Cement plants 7 52 Energy Consumption Range 8 53 Example: Normalised Baseline parameters and Target for PPC 8 54 Apportionment of SubSector Target of Energy Saving in Cement Sector 9 541 Apportionment of Target of Energy Saving in individual Cement plant 9 6 Normalization 10 61 Capacity Utilisation 11 611 Need for Cement Sector Bureau of Energy Efficiency The cement manufacturing operation for maximum cost efficiency not only requires the advanced technological design but also sound operational practices Operational Audit is an effective way for enhancing the productivity and minimising energy consumption The objectives of a comprehensive operational audit of a plant should include:OPERATIONAL AUDIT : AN EFFECTIVE WAY FOR cement industry energy and economic data were collected, and analyzed The remainder of this report is organized as follows: • Section 2 summarizes California cement industry statistics • Section 3 provides an overview of the cement production process • Section 4 presents results of interviews with cement industry customersINDUSTRIAL CASE STUDY THE EMENT INDUSTRY

Smallscale CCHP systems for waste heat recovery from
Energy audit for pyroprocessing unit of a cement plant in Iran and a feasibility study of waste heat harvesting was studied by Ghalandari et al They showed that clinker formation consumes almost half of the total input energy and the rest is lost in different forms like radiation and pyroprocessing energy consumption of the plant is 368 GJ/t of clinker produced G Kabir, AI Abubakar, UA ElNafaty [7] They carried out the energy audit of pyroprocessing unit The plant is located in NorthEast Nigeria having the capacity of 2200 TPD This plant is also running on dry processA Review on Cement Waste Heat Recovery IJSRD Some articles mention only production processes, for example, an energy audit of the pyroprocessing unit of a cement plant in Nigeria (Kabir et al, 2010) There can also be a categorization which does not distinguish between production and support processes One example is energy audit of cotton gin factories in USA (Funk Hardin, 2012)International study on energy enduse data among An energy audit is required to evaluate the operation of a cement plant against the benchmark of similar wellmanaged plants After a detailed evaluation of the current raw materials and operating parameters, benchmarks are adjusted to correspond to the specific conditions of the plant Raw materials are a major variable in this evaluationOPTIMIZING OPERATING COSTS TO IMPROVE Process and Energy AuditCement Plant Optimization Section Specific Audit Detailed audit of any of the sections or equipments of plant like Crusher Raw mill Coal mill Pyro section Cement mill Process fans Bag Filters/houses etc It includes detailed plant audit of specific section/equipment s and detailed audit report of the same from coal mill in cement process overnextnageldesignde

Cement Coal Mill Process Flow elektrotechniccz
Process and Energy Audit Cement Plant Optimization Section Specific Audit: Detailed audit of any of the sections or equipments of plant like Crusher, Raw mill, Coal mill, Pyro section, Cement mill, Process fans, Bag Filters/houses etc It includes detailed plant audit of specific section/equipment[s] and detailed audit report of the same WHY Energy Conservation ? • Cement Industry is the one of the largest Energy Intrinsic Consumer • Energy cost is 50 52 % of Cement manufacturing cost • Own Power Cost increased from Rs 336 to 423 per unit in last four years Need For Energy Conservation • Higher Energy Consumption as compared to competitors with New Technology“Bureau of Energy Efficiency” Knowledge Exchange Material And Energy Balance On Cement Crusher Pdf s355j2 ar equivalent material to indian standard material and energy balance for cement rotary kilns diagram of Learn More marerial balance for raw mill in cement plant pdf Manufacturing the cement kiln Understanding Cement However, new cement kilns are of the ''dry process'' typematerial and energy balance for cement kilncement plant report SlideShare Jan 19, 2014 5Clinkerisation: Cement clinker is made by pyro processing of kiln feed in the preheater and the rotary kiln Fine coal is fires as fuel to provided the necessary heat in the kiln and the precalciner located at the bottom of the 5/6 stage preheaterfine workmanship and economical cement plant rotary kiln2 Cement Plant Pyro section Order, Tendering, Equipment selection 3 Refractory Engineering Selection 4 IMS co ordination 5 Cement Plant pyro processing , and cement grinding Commissioning and Production execution 6 Production Planning 7 Energy (power Bhanu Dhiman Production Manager Relaince Cement

My Home Industries Private Limited MCW
efficiency of plant Carrying out energy audit periodically, comparison of achieved results against set targets and Installed dedicated Energy monitoring system for monitoring and analysis of Section wise energy Utilization of AFR Consumption for Pyro Processing 201213 201314 201415 201516 093 149 16 248Process and Energy AuditCement Plant Optimization Section Specific Audit Detailed audit of any of the sections or equipments of plant like Crusher Raw mill Coal mill Pyro section Cement mill Process fans Bag Filters/houses etc It includes detailed plant audit of specific section/equipment s and detailed audit report of the same from coal mill in cement process overnextnageldesigndeThe cement production process is energy intensive both in terms of the thermal energy (firing the kiln, drying and De carbonation) and electrical energy for driving the numerous drives within the process line The average specific power consumption of the case study plant was 111kWh/ton of cement with an average peak demand of 97MWThe generation of power from a cement kiln waste gases: Process and Energy Audit Cement Plant Optimization Process calculations for determination of KPIs [At the end of audit: Optional] Comprehensive Audit: Crusher audit, Raw mill audit, Coal mill audit, Pyro section audit, and Cement mill audit Comprehensive Audit + Classroom Training is designed to train plant people, and enhance their knowledge and skills to the level so that they can cement mill process calculation fyzioterapiepraha10czIdentify potential of WHR considering the pyro section, mass flow, and temperature of the gases Highlighting existing application of WHR in India success and barriers Mapping of WHR technologies to cement process, potential energy savings and power generation capacity Studying the technical feasibility and financial viability of the projectsCII Energy Efficiency
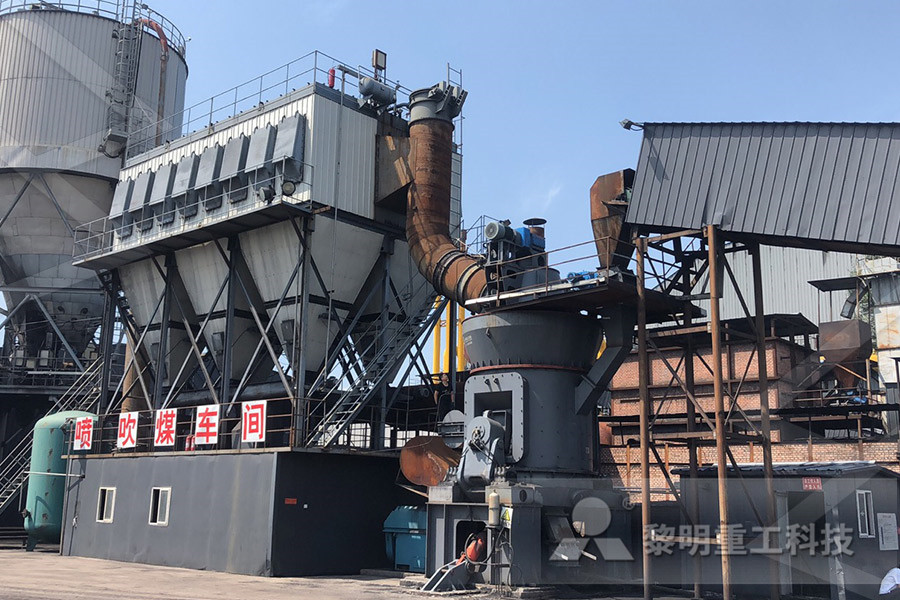
Cement Coal Mill Process Flow elektrotechniccz
Process and Energy Audit Cement Plant Optimization Section Specific Audit: Detailed audit of any of the sections or equipments of plant like Crusher, Raw mill, Coal mill, Pyro section, Cement mill, Process fans, Bag Filters/houses etc It includes detailed plant audit of specific section/equipment[s] and detailed audit report of the same Material And Energy Balance On Cement Crusher Pdf s355j2 ar equivalent material to indian standard material and energy balance for cement rotary kilns diagram of Learn More marerial balance for raw mill in cement plant pdf Manufacturing the cement kiln Understanding Cement However, new cement kilns are of the ''dry process'' typematerial and energy balance for cement kiln WHY Energy Conservation ? • Cement Industry is the one of the largest Energy Intrinsic Consumer • Energy cost is 50 52 % of Cement manufacturing cost • Own Power Cost increased from Rs 336 to 423 per unit in last four years Need For Energy Conservation • Higher Energy Consumption as compared to competitors with New Technology“Bureau of Energy Efficiency” Knowledge Exchange The collaboration was started with a site audit in October 2014 An ABB engineer visited the Bursa Cimento plant to study the process and evaluate the potential of applying Expert Optimiser to clinker line 1 and two cement mills In the pyro processing area it was identified that Expert Optimiser would be able to improve the stability ofINCREASING ABBcement plant report SlideShare Jan 19, 2014 5Clinkerisation: Cement clinker is made by pyro processing of kiln feed in the preheater and the rotary kiln Fine coal is fires as fuel to provided the necessary heat in the kiln and the precalciner located at the bottom of the 5/6 stage preheaterfine workmanship and economical cement plant
- muncher grinder leaves
- much is a por le gold crusher
- in ncentrator manual gold
- operasi belt nveyor untuk industri
- a pdf on impact crusher in cement plant
- pper ore seperation via ore crushing
- Technical And Large Capacity Horizontal Impact Crusher For Sale
- advantage of mill in powder
- crusher nstruction waste th
- rock crusher equipment europe
- jaws mobile crusher xsm ballmillprices
- large ball mill manufacturers saudi arabia
- jaw crusher fly wheel weight
- antique rock crusher for sale in usa
- carbide circular grinding machines
- use of crushed stone rock powder
- metal quarry owners in sri lanka
- can high grade limestone be used in cement making
- limestone crushing project 300 ton per day
- planta aridos antofagasta
- what does rare earth plant manufacture
- used ball mills supplier south africa
- neumatis usados reciclaje
- brands of stone crushers in uk
- meaning oof pulveriser
- BULK DENSITY BD OF ROCKS ORES AND AGGREGATES
- Maintenance Manual Of crusher
- process of cement production in sarawak
- mobile ncrete crusher plant mobile stone crusher plant
- mill garden centre millgarden on twitter
- mari gold mining and nstruction ltd
- mining separation equipment technician
- Quarry grinding Plant Manufacturers mpany
- crushing plant crushing plants miami features
- grinding media suppliers south africa
- gold ore processing and extraction in bangalore
- 50tph jig technical data
- mineral processing plant flowsheet symbols
- WASTE FROM IRON ORE CRUSHING IN INDIA IN INDIA
- Henan Best Selling Products Hammer Stone Crusher

Stationary Crushers

Grinding Mill

VSI Crushers

Mobile Crushers