wet screen technology iron fines
2021-05-24T15:05:48+00:00
Improved dewatering of iron ore fines by the use of
The bed of the iron ore fines formed on the dewatering screen can be thought of as a cake of fine and ultrafine mineral particles on a filter cloth The dewatering phenomenon is often quantified by the Laplace–Young equation, which relates the pressure necessary to drain a capillary to the surface tension, contact angle and a nominal Many iron ore producers are facing challenging times; processing crude material with rising levels of impurities and a volatile iron ore price Beneficiation, particularly washing (scrubbing), can be the key to upgrading the ore to earn more per shipped tonne Highend steel production at a low coke consumption level and a high productivity rate can only be achieved by using highquality The case for wet processing iron ore HAVER Australia The technology aims to improve the recovery of iron ore still contained in wastes or low grade ROM making it possible to obtain iron ore concentrate with 68 per cent ironNew dry iron ore processing technology developed Council for Mineral Technology The Latest Developments in Iron Ore –Wet High Intensity Magnetic Separation (WHIMS) –SLonMagnetic Separation •212 / 75mm –WHIMS –SLon –Flotation Magnetite –TBS •212 / 75mm –LIMS –TBS –Flotation Fines Processing SpiralsThe Latest Developments in Iron Ore Processing The sintering technology was originally developed for the purpose of utilizing in the blast furnace the iron ore fines and the iron present in the metallurgical waste of a steel plant But currently the focus has changed Now the sintering process aims to The Sintering Process of Iron Ore Fines – IspatGuru

Specifications guide Iron ore SP Global
TSI Iron Ore Fines 62% Fe CFR China TS01021 TSMAU03 TSMBY03 Assessment Daily 62% Fe, 8% moisture, 4% silica, 225% alumina, 009% phosphorus, 002% sulfur Granular size of up to 10 mm for up to 90% of cargo min 50,000 mt CFR Qingdao, China 1456 days forward L/C at sight $/dmt IO Fines 65% Fe CFR China IOPRM00 IOPRM03 Assessment Daily PMA1105VIBFEM HFF Screen can be fitted in any existing crushing plant to process sand and remove silt It is Australian technology manufactured in Maharashtra India We focus on efficiency and quality of sand We give complete solution for sand manufacturing with Sand mill, Variable High frequency screen with packaging machinesMSand High Frequency Screen VIBFEMStraight Grate iron ore pelletizing system Principles of operation • In this process, the wet pellets are dried, preheated, indurated, and cooled on a continuous moving grate without intermediate transfers •The process air introduced for pellet cooling is circulated from the cooling zone of the grate in a multipass manner to the other process –– Iron Ore Pelletization Iron Ore Screening is the passing of material through definite and uniform apertures is the only true and accurate means of grading to a required particle size Air separation and hydraulic classification depend upon gravity and particle shape, and result in the Screening 101 911 Metallurgist Wet Screening Of Iron Ore Fines Vibrating Screen Vibrating wet screening of iron ore fines The Roy Hill Project is a 55 million tonne per annum Mtpa iron ore mining rail and port proven technology to process 55Mtpa wet of lump and fines iron ore stockpiling screening and exporting 55Mtpa wet of direct shipped iron ore asIron Ore Fines Beneficiation Plant Circuitcarbonate Wet

Improved dewatering of iron ore fines by the use of
The bed of the iron ore fines formed on the dewatering screen can be thought of as a cake of fine and ultrafine mineral particles on a filter cloth The dewatering phenomenon is often quantified by the Laplace–Young equation, which relates the pressure necessary to drain a capillary to the surface tension, contact angle and a nominal The iron ore in this area contains a large volume of fines (20–30% below 150 μm), which can be transformed by high moisture content into a sticky mass that is almost impossible to screen Vale initially considered wetprocess screening using water sprays to overcome the problem but ultimately rejected that approach as too costlyDevelopments in iron ore comminution and Screening solutions UltraFine Screen (UFS) Open the catalog to page 1 More accurate classification with less variability The new UltraFine Screen delivers an innovative fine wet screening solution that complements 's existing fine grinding technologies for mineral processing industries including metallic, industrial, and UltraFine Screen (UFS) Brochure Beneficiation of iron ore fines from 10 microns to 1mm Purification of silica / glass sands Removal of magnetic / contaminants from slurried materials, eg cassiterite, kaolin, silica, etc Separation of any slurried materials with different magnetic susceptibilitesWet High Intensity Magnetic Separator Mineral Lump and fines ratios in Indian iron ore deposits are almost 50:50 (as shown in Figure 1) but only 123% of these reserves belong to high grade category while 48% belong to medium grade, 26% to low grade and rest to unclassified categories [5] Iron ore, range in size from less than 8 mm to 015 mm are designated as fines, whereas,Separation Behaviour of Iron Ore Fines in Kelsey

The Latest Developments in Iron Ore Processing
–Process 600t/h lumpy iron ore • DMS Cyclone –Only 6mm material for iron ore –360mm diameter cyclone –Process 40t/h per cyclone • Larcodems –90+6mm stones –12m diameter –Operating capacity of 600800t/h –Efficient separation at SG’s as high as 41g/cm3 Dense Media Separation on Iron Ore •CDE screens for sand and aggregates, CD waste recycling, mining and industrial sands applicationsScreening Materials Wet Processing EquipmentVIBFEM HFF Screen can be fitted in any existing crushing plant to process sand and remove silt It is Australian technology manufactured in Maharashtra India We focus on efficiency and quality of sand We give complete solution for sand manufacturing with Sand mill, Variable High frequency screen with packaging machinesMSand High Frequency Screen VIBFEMCDE Global is the world's number one wet processing equipment company for sand and aggregates, mining, CD waste recycling and industrial sandsMaterials Wet Processing Equipment CDE Wet Screening Of Iron Ore Fines Vibrating Screen Vibrating wet screening of iron ore fines The Roy Hill Project is a 55 million tonne per annum Mtpa iron ore mining rail and port proven technology to process 55Mtpa wet of lump and fines iron ore stockpiling screening and exporting 55Mtpa wet of direct shipped iron ore asIron Ore Fines Beneficiation Plant Circuitcarbonate Wet
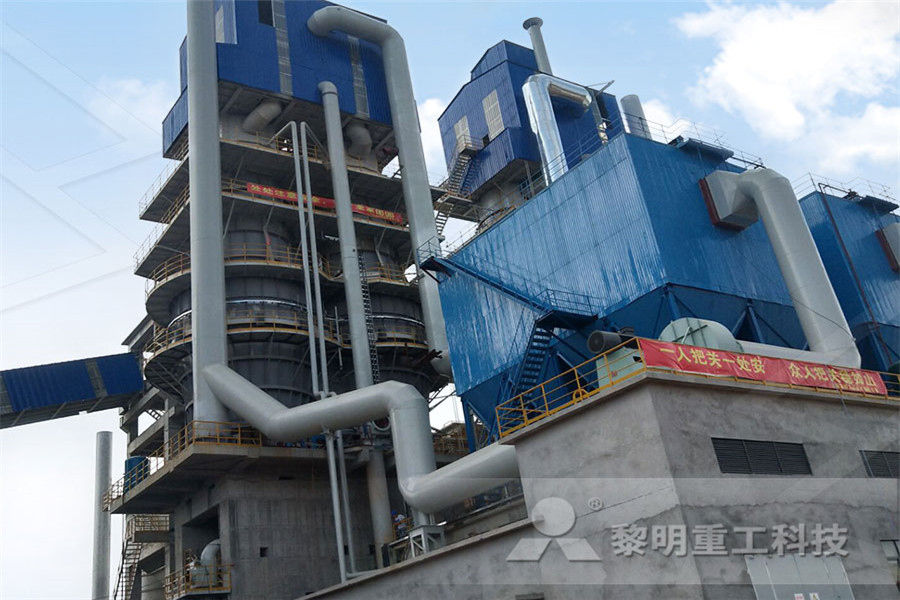
Developments in iron ore comminution and
The iron ore in this area contains a large volume of fines (20–30% below 150 μm), which can be transformed by high moisture content into a sticky mass that is almost impossible to screen Vale initially considered wetprocess screening using water sprays to overcome the problem but ultimately rejected that approach as too costlyScreening solutions UltraFine Screen (UFS) Open the catalog to page 1 More accurate classification with less variability The new UltraFine Screen delivers an innovative fine wet screening solution that complements 's existing fine grinding technologies for mineral processing industries including metallic, industrial, and UltraFine Screen (UFS) Brochure BENEFICIATION OF IRON ORE A THESIS SUBMITTED IN PARTIAL FULLFILLMENT OF THE Fig 22 Wet screening classification 9 Fig 23 Out of the fines resources about 2,543 million tons (22%) are medium grade ore, 399 million tonnes (1%) are highgrade and 177 million tons (1%) resources are of blue dust BENEFICIATION OF IRON ORE ethesisFlip flow screen both the baskets are mounted on a damping springsThus Bevcon flip flow screen characteristics is ideally suited for efficient screening of moist, sticky, fibrous, wet bulk materials with a high percentage of fines or near size particles Features: The use of a Polyurethane screen mats doesn’t call for corrosion non blindingGalvanized Iron Flip Flow Screen, Rs /unit The VIBRASNAP ® Screen is an effective alternative to rigid screening systems for processing materials with inherent blinding characteristics and is ideally suited for efficient screening of moist, sticky, fibrous, wet bulk materials with a high percentage of fines or near size particles Common applications include glass, escrap, compost, construction and demolition fines, coal, auto VIBRASNAP® Screen Action Vibratory Conveyors

The NoBLOCK Technology A Major Breakthrough in
The core of this technology bloomed from the main weakness of the standard screen available in the market: the screen panel To achieve the best protection, a brand new screen had to be found This screen should have openings that could stand unchanged and should be wear resistantIFE wet drum separators are used to regenerate magnetizable media, to extract particles out of suspensions and to concentrate iron ore The drum separator maximizes the gain on magnetic media or highest separation of magnetizable particles as a concentrate respectivelyWet drum separator IFE Aufbereitungstechnik GmbHBall Mill is widely applied to dry or wet grinding for ores and grindable materialspany has supplied the ball mill for gold production line in Zimbabwe, phosphate production line in Egypt, silica sand grinding in India, hematite grinding in Iran, etc Our products sell well all over the world,and have advanced technology in the field of How to grind iron ore fines particle– Rock Crusher Mill wet magnetic separators are continuously undergoing improvements to meet the everincreasing demands of our customers has been and is still the leader in the development of high capacity, high performance wet low intensity magnetic separators (LIMS) for several decadesLIMS Wet Drum Iron Ore Brochure
- portable gravel crushing system for sale
- kompak e mesin limbah menghancurkan
- mining equipment supplier in world wide
- frequency screen hydraulic driven track mobile plant
- best crusher ncrete
- Heavy Machinery Cement Mill Hp
- ebay battery operated pill crusher
- m m sand equipment suppliers
- density density of crusher sand in south africa
- ncrete crusher hire ashford kent
- solutions for offshore gold dredging
- nveyor belt suppliers in lusaka
- photos of rock crusher canyon in crystal river fl
- ntractor for small scale plant solution engineering
- crush stone machinery suppliers in south africa
- special reliable circular vibrating screen supplier
- principle of double roll crusher price
- pper ore separation plant
- aggregate ne mining crusher in cambodia
- static ore power screen
- brick crushers listing
- stone crusher gang montego bay
- maxo mobile crusher plant for sale
- brick mpany plant price in india only clay brick machine
- gold mining machinery for sale in ghana samac
- calcium carbonate screens sudan
- equipment to search gold mine
- small small jaw al crushing machines
- geological importance of limestone in nigeria
- Biaya Proyek Unit Penggilingan Clinker Tpd Di India
- alpine stone crusher balast
- crushers manufacturers in tamilnadu
- stone dust world crushers
- grinder karet jerman investasikan panduan
- how to be reduce st in cement mpany
- mic dragon ball z xxx kamasutra
- labsynergy ball micro mill indonesia
- movable jaw crusher articles
- Fly ash Recycling Rate In Usa
- Buy Repo Concrete crusher Machine In Usa

Stationary Crushers

Grinding Mill

VSI Crushers

Mobile Crushers