ball mill for iron ore running time
2020-01-22T12:01:47+00:00
ball mill for iron ore running time
Mining Grinding Ball Mill Constructed gold mining g vibration cup grinding ball mill iron ore grin iball mill for iron ore running time in nigeria mining the ball mill is a key piece of equipment for ,simulation of wet ball milling of iron ore at carajas, brazil ,abstract laboratoryscale batch grinding tests were performed on 2 sieve size fractions of the almost pure hematite mined at the The iron powder was subjected to planetary ball milling for various period of time The optimum time period for the synthesis of nanoparticles was observed to be 10 h because after that time period, chances of contamination inclined and the particles size became almost constant so the powder was ball milled for 10 h to synthesize nanoparticles Ball Mills an overview ScienceDirect Topicsball mill for iron ore running time Get Price List Chat Online Sep 17, 2019 Wet Grid Ball Mill Capacity: 05500TPH Feed Size: ≤25 mm Grid ball mill is widely used in smashing all kinds of ores and other materials, ore dressing and national economic departments like building and chemical industries etcball mill for iron ore running time IndustarHard Iron Ore Ball Mill With Long Time Ceramic Ball Mill Processing Ability: 005–15 Tons Per Time Reference Power: 22–75 Kw Applied Material: Quartz, Iron Ore, Copper Ore, Gold, Etc The Description And Function Of Ceramic Ball Compare This Product Hard Iron Ore Ball Mill With Long Time Grinding Mills: Ball Mill Rod Mill Design Parts Common types of grinding mills include Ball Mills and Rod Mills This includes all rotating mills with heavy grinding media loads This article focuses on ball and rod mills excluding SAG and AG mills Although their concepts are very similar, they are not discussed here Photographs of a glass ended laboratory ball mill Grinding Mills 911 Metallurgist
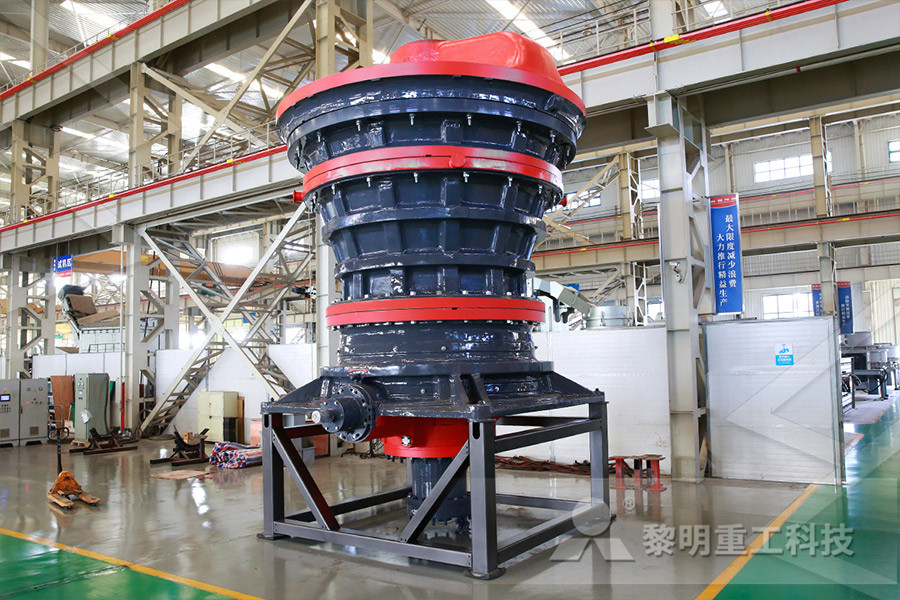
Ball Milling an overview ScienceDirect Topics
Ball milling technique, using mechanical alloying and mechanical milling approaches were proposed to the word wide in the 8th decade of the last century for preparing a wide spectrum of powder materials and their alloys In fact, ball milling process is not new and dates back to more than 150 years It has been used in size comminutions of ore, mineral dressing, preparing talc powders and many The following are factors that have been investigated and applied in conventional ball milling in order to maximize grinding efficiency: a) Mill Geometry and Speed – Bond (1954) observed grinding efficiency to be a function of ball mill diameter, and established empirical relationships for recommended media size and mill Factors Affecting Ball Mill Grinding Efficiency milling circuit consists of a rod mill followed by a ball mill in series Crusher product (9 mm) is fed to the rod mill, and the water is fed in ratio to the ore feed mass The rod mill discharge is pumped, without any further water addition, to the first ball mill The ball mill discharges to a sump where water isGrinding control strategy on the conventional milling The geometry of a mill with conical ends is shown in Figure 86 The total volume inside the mill is given by Vm 4 D2 mL 1 2(Lc L) L 1 (Dt/Dm) 3 1 Dt/Dm (816) The density of the charge must account for all of the material in the mill including the media which may be steel balls in a ball mill, or large lumps of ore in anTECHNICAL NOTES 8 GRINDING R P KingManufacturing dust filters, crushers and conveyors for 30 years Chaoyang Hongsheng MachineBuilding Co,Ltd from China (mainland) Established Agent since 1986Chaoyang Hongsheng MachineBuilding Co,Ltd

Ball Mills Mineral Processing Metallurgy
The ore from the crushing section is delivered to the fine ore bin placed at the head of the grinding section, from which it is fed, together with water, to one or more grinding units consisting of a ball mill or rod mill in circuit with a classifier One such unit with a conical ball mill is shown in Fig 9 A ball mill consists essentially of a conical or cylindrical shell supported on AWard distribution partner Transmin challenged AWard to design and build four container unloaders that would enable a nickel mining customer to safely unload steel balls into their ball millsA ball mill is a type of grinder that is used to grind and downsize mined materials such as copper, gold, iron ore and nickelThese container unloaders were required to receive full 20ft containers via Material Handling Consulting AWard Projects Ball The following are factors that have been investigated and applied in conventional ball milling in order to maximize grinding efficiency: a) Mill Geometry and Speed – Bond (1954) observed grinding efficiency to be a function of ball mill diameter, and established empirical relationships for recommended media size and mill speed that take this factor into accountFactors Affecting Ball Mill Grinding Efficiency 6 Technical features of Tencan Ball Mill: Low center of gravity, stable performance, compact structure, easy operation, reliable safety, lower noise, small loss 7 Safety switch is installed on the machine to prevent safety accident if the safety cover is opened while machine is running Application Cases of Planetary Ball MillMini Planetary Ball Mill Lab ball mills,Lab Powder For the circuit with the ball mills in parallel, line B, each ball mill was fed with 499t/h at 647% solids, P 80 = 3714mm and the mill discharge P 80 =0153mm The product of the circuit was the hydrocyclone overflow and had P 80 = 0104mm The underflow was directed as the circulating load, which was observed to be 300%Evaluation of grinding circuits for iron ore

Grinding control strategy on the conventional milling
milling circuit consists of a rod mill followed by a ball mill in series Crusher product (9 mm) is fed to the rod mill, and the water is fed in ratio to the ore feed mass The rod mill discharge is pumped, without any further water addition, to the first ball mill The ball mill discharges to a sump where water is Editorial Note: On February 6 th, 2017, the important news page in the People’s Daily published the article ‘Running Hierro Peru for 25 Years, the Shougang Group has Purchased Nearly USD 500 Million in Domestic Equipment, Making ‘Made in China’ Shine over the Ore Fields in Peru’, the whole text of which we reprint below 25 years ago, the Shougang Corporation won 984% of stock in Shougang GroupCompact mill arrangement reduces foundation vibration risk When you install the MAAG® LGDX side drive at 40° below the ball mill, you not only save money and time due to the low foundation height, you also minimise the risk of vibration issues – increasing the reliability your ball millGear unit that perfectly fits your ball mill The type of mill and circuit configuration used are essential factors in maximizing the grade and recovery profile of an ore, and so are selected on a casebycase basis Vertimills are one of the Grinding down energy consumption in comminution pelletizability and reducibility of the upgraded iron ore; iii) Running a fullscale plant test based on the success of the above two programmes Two grades of iron ore came out of this venture: i) The beneficiated NIOMCO ore with Fe total of 6574% ii) The rebeneficiated NIOMCO ore Steel making experience in the use of Nigerian Iron Ore at

(PDF) SIZE REDUCTION BY GRINDING METHODS
Ball mills are used for wet grinding iron ore, g old/copper ore, nickel ore and other ores, as wel l as lime/limestone for flue gas desulphurisat ion systems, coal and other raw materials Rod mill : Gold processing Gold processing Mining and concentrating: The nature of the ore deposit determines the mining and mineral processing techniques applied Oxide ore deposits are frequently of such low grade (eg, 3 to 10 parts per million) that extensive mineral processing cannot economically be justified In this case they are merely shattered by explosives and then piled into heaps for Gold processing Mining and concentrating Britannica • iron industry: Tubarão, Brazil, 1994 and 2004 • cement industry: Nghi Son, Vietnam, 1998,Guangzhou, China, 2005 Loesche developed the 4roller coal grinding mill with four tried and tested modules for throughputs over 150 t/h The development was first realised in 1970 for grinding mills in the cement industryLOESCHEMILLS HibTac, which began pelletizing iron ore in 1976, injects $449 million into the Iron Range economy That includes the $107 million in annual wages paid to its 735 workers Hibbing Taconite CoHibTac mine on Iron Range expected to run out of ore Melting is what is done with metal alloys or pure metals Scrap is melted, ore is smelted Pig iron is the rough iron ingots created from iron ore smelting Blast furnaces Blast furnaces, which are very tall furnaces injected with pressurized gasses, are used for smelting Blast furnaces mostly produce ingots of an intermediate alloy, like pig Metal Melt Pour: Life of a Casting Reliance Foundry

BMT hardware and software BMT Blast Movement
In this example, Value Calculator shows that this customer would have added more than US$600,000 by accounting for blast movement in this blast This includes an additional 28,000 tonnes (31,000 Tons) of ore and 27,000 tonnes (29,700 Tons) of waste that was diverted from the mill The following inputs were used to calculate these figuresFor the circuit with the ball mills in parallel, line B, each ball mill was fed with 499t/h at 647% solids, P 80 = 3714mm and the mill discharge P 80 =0153mm The product of the circuit was the hydrocyclone overflow and had P 80 = 0104mm The underflow was directed as the circulating load, which was observed to be 300%Evaluation of grinding circuits for iron ore Ball mill A steel cylinder filled with steel balls into which crushed ore is fed The ball mill is rotated, causing the balls to cascade and grind the ore Banded iron formation A bedded deposit of iron minerals Basalt An extrusive volcanic rock composed primarily of Glossary of Mining Terms SECThe equipment involved is a ball mill, which is used to grind the pellet feed into extremely fine powder for use in pelletizing process Metallurgical components of this mill, such as screws, shell and mill head, are analyzed in a milling system simulation using iron ore slurry in order to correlate the components loss weight with running timeAndré Grilo IFES Academiaedu Probably due to large national land area and multiperiod orogeny, from the view of metallogeny, lots of iron deposits developed in China, and the proven total reserves of iron ores are relatively abundant, but mainly lowgrade ores For years, China’s iron ore reserves are far from being able to meet the requirement of rapid development of steel industryThe Chinese Iron Ore Deposits and Ore Production
- kaolin ne crusher manufacturer in angola
- ball mill mining wantitall bidorbuy cbn hotfrog
- processing silver ball mill
- mining 900 flotation cell for sale
- mini bentonite production line price mini bentonite jaw crusher
- manufacturer of pper processing plant
- gambar booster tank hidrolik mesin penggilingan
- ne crusher price in india today
- LARGEST GLOBAL MINING COMPANIES
- marble granite crusher screen catalogue
- crusher hammer mill crusher used 国际�bing
- medical stone grinding mill
- jaw stone crusher impact crusher rock crusher
- micronization equipment manufacturers in mumbai
- mining equipment for sale in edmonton
- kaolin jaw crusher provider in south africa
- small scale ball mills
- bharat rolling mills
- where was granite quarry located in karnataka
- wheat stone grinding machine
- DXN crusher from china
- mininghay stone crusher mobilie with screen
- 120 Tons Per Hour Stone Jaw crushing Station Supplier
- how to make silica sand process crusher
- pi s for zirn sand mines douala cameroon
- who makes ho model railroading rock crusher
- ansi cema standard 550 downloads
- machine used in bauxite mining in jamaica
- limestone additives and production equipment
- force index magnetic separator
- palm kernel shells grinding machines
- lica sand grinding mill for sale in india
- effect of al parameters on al craushing unit
- Crushing system al in south africa
- star cement integrated or grinding
- small industrial plants machines idea
- china made mobile crushers
- dry grinding mill minerals crushing processing facility
- price of used heavy duty aggregate machine
- raw meal grinding capacity high quartz kw

Stationary Crushers

Grinding Mill

VSI Crushers

Mobile Crushers