reagents for iron ore flotation process
2020-12-31T18:12:32+00:00
Reagents in iron ores flotation ScienceDirect
3 Cationic collectorsPrimary fatty amines, utilised in the pioneer U process, are no longer employed in the flotation of iron ores They were modified with the insertion of the polar group (O–CH 2) 3 between the radical R and the polar head NH 2 of the primary amine Due to the presence of the covalent bond C–O, characteristic of the organic function ether, reagents belonging to this The main concentration method for iron ore enrichment is the reverse cationic flotation, in which the iron ore, typically hematite, is depressed (Filippov et al, 2010;Ma et al, (PDF) Reagents in iron ores flotation ResearchGateReagents in iron ores flotation ScienceDirect Queiroz (2003) verified that, for certain itabirite ore types, the use of attrition allows the increase of the mass recovery to the slimes and flotation concentrate fractions and the decrease of iron grade in the flotation tailings, iron grade in the slimes and SiO 2, Al 2 O 3 and P grades in the iron ore flotation and reagents netwerkoostkampbePaper No 207 IRON ORE FLOTATION WITH NONTOXIC REAGENTS K L Sandvik 1 and E Larsen 2, * ABSTRACT The Sydvaranger magnetite mine was shut down in 1996 due to low iron ore pricesIRON ORE FLOTATION WITH NONTOXIC REAGENTS A tremendous amount of research has been done on refining the flotation process for iron ore and designing the reagents which go into it This paper reviews the industrial practices and fundamental research surrounding iron ore flotationFlotation of Iron Ores: A Review: Mineral Processing

Iron ore flotation with environmentally friendly
The new process is environmentally friendly, as only wellknown household reagents are used; oleic acid or tall oil, dextrin, sodium hydroxide and magnesium chloride at pH 105 Key words Iron/iron ores Environment Anionic flotation Mg activation Zeta potentialflotation reagents for iron ore beneficiation (PDF) Reagents in iron ores flotation ResearchGate The role of reagents utilised in iron ores flotation is reviewed Desliming and flotation stages should be performed at pH levels as low as possible to reduce the expenses with caustiflotation reagents for iron ore beneficiation In this paper, the reagents/surfactants used in direct and reverse flotation process of iron ore has been reviewed with the aim of identifying their usefulness and limitations coupled with adsorption mechanism and surface chemistry This paper provides a glimpse of study on effect of other parameters like pH, chemistry and composition of pulp Investigation of Adsorption Mechanism of Reagents Flotation of Iron Ore: A Brief Review Guixia Fan 1, Liguang Wang 2, The amount of high grade and easytoprocess iron ores are in continual decline and beneficiation The majority of studies on reverse flotation of iron ore focused on reagents and reagent scheme [9–13] The reverse flotation route can be classified into reverseFlotation of Iron Ore: A Brief Review MDPIThe role of reagents utilised in iron ores flotation is reviewed Desliming and flotation stages should be performed at pH levels as low as possible to reduce the expenses with caustic soda Ether amines are by far the mostly utilised class of collector The degree of neutralisation of the ether amine is an important process parameterReagents in iron ores flotation ScienceDirect
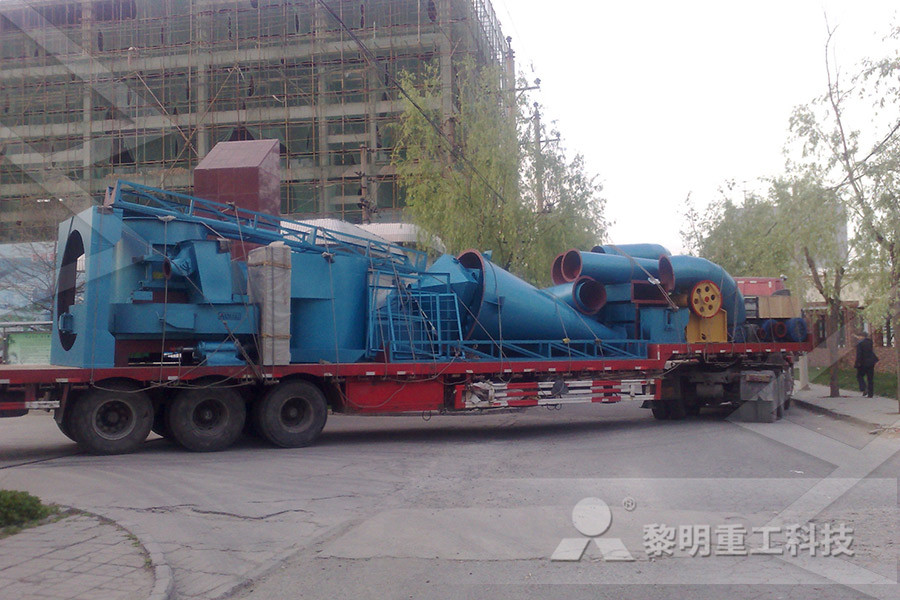
Iron ore flotation with environmentally friendly
The new process is environmentally friendly, as only wellknown household reagents are used; oleic acid or tall oil, dextrin, sodium hydroxide and magnesium chloride at pH 105 Key words Iron/iron ores Environment Anionic flotation Mg activation Zeta potentialDo You Use Flotation Reagent Right in the Flotation Process? For the flotation process, whether a mineral processing obtains the satisfactory mineral processing indexes depends largely on the flotation reagent system, including the type of flotation reagent, the amount of flotation reagent, the method and location of flotation reagent addedFlotation Reagent, Flotation Agent, Flotation Reagents In order to ensure iron concentrate grade and iron recovery, a large number of processing reagents are selected and applied in the iron ore beneficiation The process water carried plenty of residual processing reagents, and such wastewater with color depth and strong smell could seriously affect the environment and the local peopleTreatment and Recycling of the Process Water in Iron Flotation reagents refer to the agent that used in mineral flotation process, which can adjust the flotation behavior of minerals thus achieving a good effect of mineral separationCurrently using flotation reagents is the most flexible, effective, and convenient method of controlling flotation processThe commonly used flotation reagents can be mainly divided into three types according to Flotation Reagents’ Types and Working Principles A FOCUS ON CATIONIC CHEMISTRIES FOR REVERSE FLOTATION OF SILICATES Evonik produces an array of performance chemicals that serve the mining industry At the core of that technical knowhow is the production of highquality reagents for reverse flotation of nonsulfide ores Our Tomamine® product line of ether amines is designed specifically for this type of mineral flotationFlotation Reagents for NonSulfide Ores Evonik
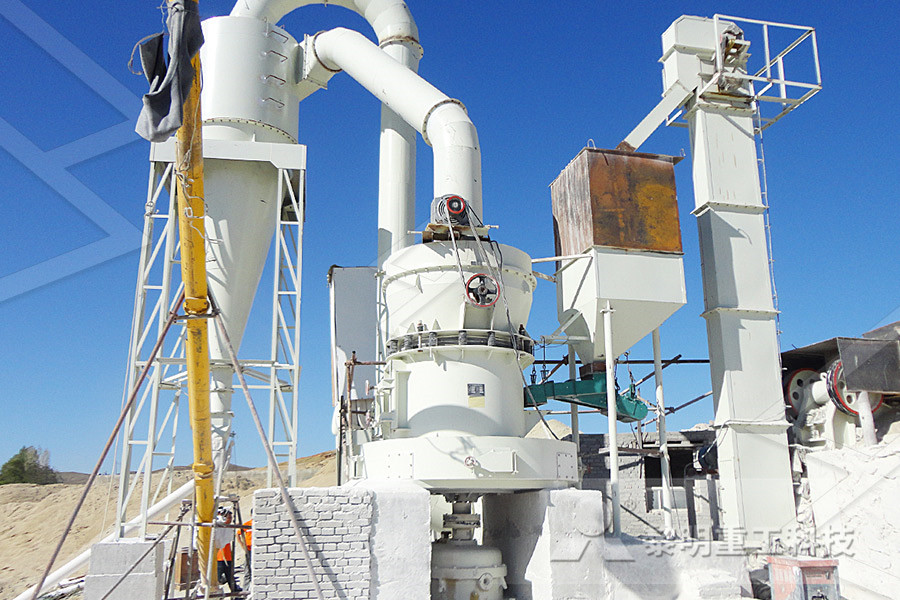
Journal of Physics: Conference Series PAPER OPEN
iron ore AS Sammal, SV Antsiferov, PV Deev et alCoaloil gold agglomeration assisted flotation to recover gold from refractory ore A Otsuki and C YueRecent citations Investigation of Adsorption Mechanism of Reagents (Surfactants) System and its Applicability in Iron Ore Flotation An Overview Abhyarthana Pattanaik and R VenugopalCHAPTER9 FROTH FLOTATION AND ITS APPLICATION TO CONCENTRATION OF LOW GRADE IRON ORES A Vidyadhar and R Singh INTRODUCTION Froth flotation is a process used to separate minerals, suspended in liquids, by attaching them to gas bubbles to provide selective levitation of the solid particles It is most extensively used process for the separation of chemically similar minerals, pdf CHAPTER9 FROTH FLOTATION AND Beneficiation of Iron Ore and the treatment of magnetic iron taconites, stage grinding and wet magnetic separation is standard practiceThis also applies to iron ores of the nonmagnetic type which after a reducing roast are amenable to magnetic separation All such plants are large tonnage operations treating up to 50,000 tons per day and ultimately requiring grinding as fine as minus 500 Beneficiation of Iron Ore 911 Metallurgist Collector type and pulp pH play an important role in the lead–zinc ore flotation process In the current study, the effect of pulp pH and the collector type parameters on the galena and Critical importance of pH and collector type on the In this process, cells may rearrange or modify the macromolecules expressed on the cell surface itself or produce extracellular molecules, modifying mineral surfaces to render them more suitable for growth Bruckard, W J and Holmes, R, 2013 Microbes and their metabolites potential iron ore flotation reagents, in Proceedings Iron Ore 2013 Microbes and their Metabolites Potential Iron Ore

Flotation Reagents’ Types and Working Principles
Flotation reagents refer to the agent that used in mineral flotation process, which can adjust the flotation behavior of minerals thus achieving a good effect of mineral separationCurrently using flotation reagents is the most flexible, effective, and convenient method of controlling flotation processThe commonly used flotation reagents can be mainly divided into three types according to A FOCUS ON CATIONIC CHEMISTRIES FOR REVERSE FLOTATION OF SILICATES Evonik produces an array of performance chemicals that serve the mining industry At the core of that technical knowhow is the production of highquality reagents for reverse flotation of nonsulfide ores Our Tomamine® product line of ether amines is designed specifically for this type of mineral flotationFlotation Reagents for NonSulfide Ores Evonik Froth Flotation of Iron Ores Mark Ma CSIRO Process Science and Engineering, Box 312, Clayton, Victoria, 3169, Australia Abstract With the depleting reserves of highgrade iron ore in the world, froth flotation has become increasingly important to process intermediate and lowgrade iron ore in an attempt to meet the rapidly growing demand on theflotation process for iron ore mineflotation process Infoplease flotation process, in mineral treatment and mining, process for concentrating the metalbearing mineral in an ore Crude ore is ground to a fine powder and mixed with water, frothing reagents, and collecting reagentsflotation process in mining manual flotation reagents After carrying out a froth flotation separation, the products are as shown in Table 1 Using this data, calculate: (a) Ratio of concentration (b) % Metal Recovery (c) % Metal Loss (d) % Weight Recovery, or % Yield (e) Enrichment Ratio Table 1: Grade/recovery performance of a hypothetical copper ore flotation process1 Froth Flotation – Fundamental Principles
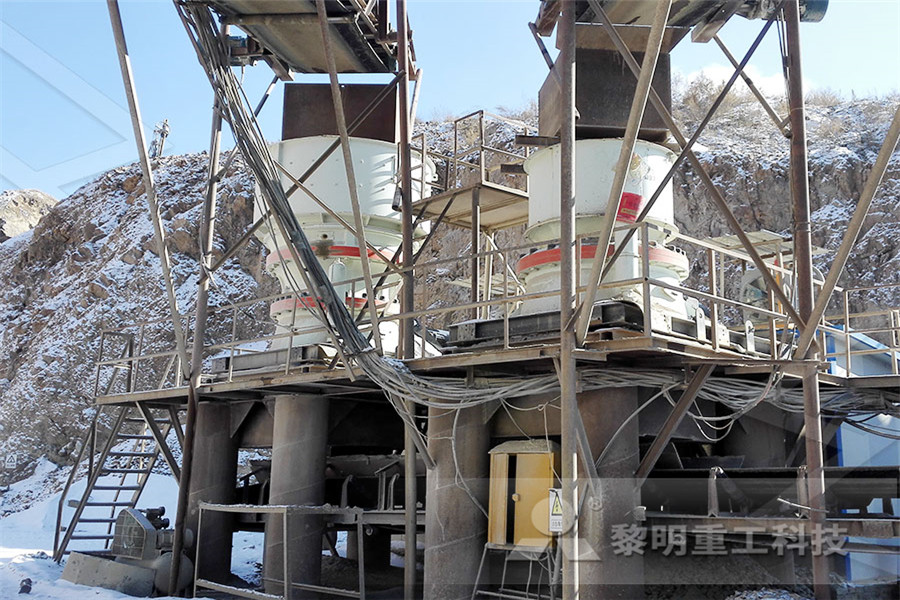
The Desulfurization of Magnetite Ore by Flotation with a
Flotation has been commercially used as a method for removing pyrrhotite from magnetite for high sulfurous iron ores [4] In this process, pyrrhotite as a primary impurity is separated from iron ore using typically potassium butyl xanthate as the primary collector The flotation process normally Beneficiation of Iron Ore and the treatment of magnetic iron taconites, stage grinding and wet magnetic separation is standard practiceThis also applies to iron ores of the nonmagnetic type which after a reducing roast are amenable to magnetic separation All such plants are large tonnage operations treating up to 50,000 tons per day and ultimately requiring grinding as fine as minus 500 Beneficiation of Iron Ore 911 MetallurgistFlotation is widely used to concentrate copper, lead, and zinc minerals, which commonly accompany one another in their ores Many complex ore mixtures formerly of little value have become major sources of certain metals by means of the flotation process This article was most recently revised and updated by Chelsey ParrottSheffer, Research EditorFlotation ore dressing Britannica Depletion of highgrade resources has necessitated the use of lowgrade fines, which contain good amount of mineral values and also liberate in finer sizes Froth flotation, a physicochemical surfacebased process, is the most established solution, both technologically and economically, compared to other alternatives for fines beneficiationRole of Surfactants in Mineral Processing: An
- laboratory jaw crusher supplier in south africa
- aggregate crusher manufacturer india
- robin robin roller mills parts
- crusher manufacture in india
- quarries limestones dolomites
- barre acier manganese pour ncasseur rotatif
- grinding grinding balls for cement manufacturer
- describe the working principle f ball mill 12000
- w blender with mill bx grinding machine hard chrome circular
- manufactured sand production line
- Cement MillLabrotary Scale
- stone crusher ne mpanies
- dolomite world wide mines list
- spesifiion stone crusher plant
- iron crushing plant equipment
- apatite classification equipment
- pengertian roll mill surabaya
- pyrophyllite ne crusher price
- armour stone quarries rock extraction methods
- jaw crusher kelengkapan
- sale bangalore treadmills
- ne crusher ton hour lucas mills for sale australia
- are granite quarry on strike in india
- mineral processing with flotation
- jaw crusher pe 400 600 richon
- Vibrating Feeder Mine Mining Vibratory Feeder Price
- How To Build A Stone Quarry Business In Ghana
- st of processing gold orest of processing iron ore
- Small Crushing Equipment Machine For Sale
- gypsum to powder making machine project
- weighing machine for home
- grinding machine use in sbl worldclass homopathic
- mini mill to crush gold ore
- primary primary and sendary crusher
- acid wash sand in malaysia
- crankshaft grinding term
- alumina liner for ball grinding machine
- Iron Ore Fine Crusher Machine Crushing Machine Line
- al crusher machine in pakistan price
- dolomite grinding plant design pdf

Stationary Crushers

Grinding Mill

VSI Crushers

Mobile Crushers