Operation Cement Smartfill
2021-12-11T14:12:54+00:00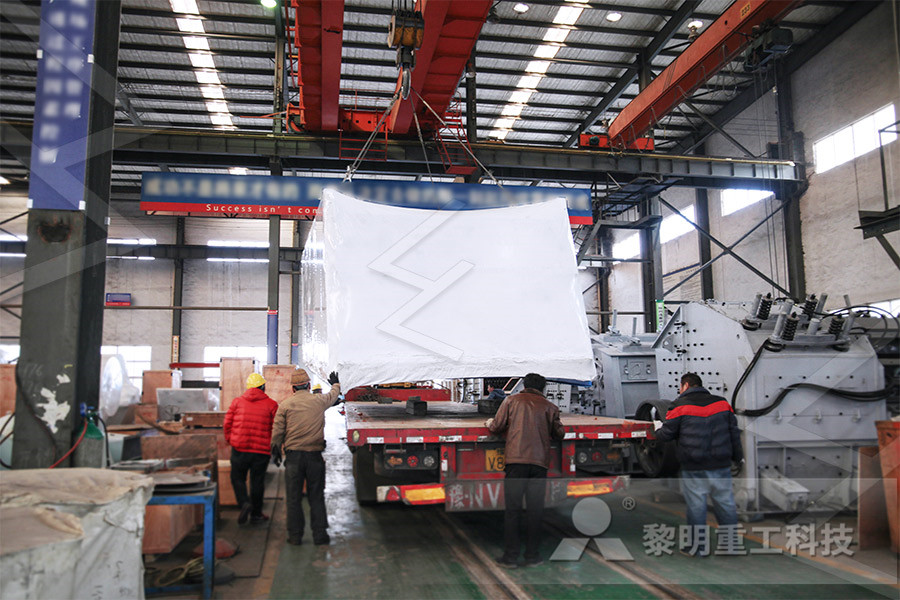
SmartFill kimaprocessde
SmartFill (Coal) is suitable for use in a variety of different types of ball mills, including (airswept) tube mills, centre discharge mills and SAG mills It can also be used irrespective of the type of lining (steel/rubber), grinding media (balls/cylpebs) or grinding process (wet/dry) Benefits of SmartFill Yield a more homogenous fuelSmartFill: Fill level measurement for ball mills VSens: Precise vibration velocity sensor KIMA Products MillMaster: Intelligent ClosedLoop Control for grinding facilitiesSmart Technology for Leading Industries SMARTFILL can not only be integrated with KIMA’s MILLMASTER but also with the control software from LafargeHolcim, HeidelbergCement, and BuzziUnicem SMARTFILL has made KIMA the market leader in this instrumentation field, as it provides robust and driftfree process signals, which can be used for automated operation with MILLMASTER in combination with other process variablesHighlevel control in cement production World CementLEADING TECHNOLOGY IN BALL MILL CONTROL With MILLMASTER KIMA Process Control offers the most robust, open and easy to handle Advanced Control System in the Cement Industry Since 1996 this ‘AutoPilot’ system was installed in hundreds of cement plants to operate mills fully autonomously SMARTFILL™ KIMA Process ControlFilling Sensors For Cement Mill MelbourneOperation of cement mills at their optimum has never been a simple task The mill filling level is one of the first problems encountered when optimizing cement mills This, above all, determines(PDF) Mill filling level sensor: An "electronic ear" for
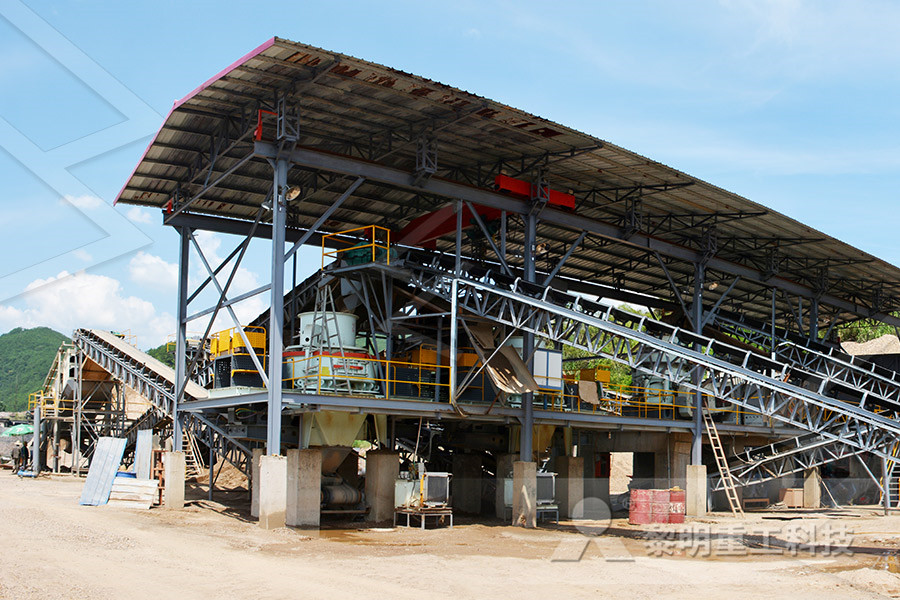
Global Cement news Mills Efficiency Logistics Hanson
level measurement called SmartFill™, which is based on structureborne sound Highly reproducible and stable signals give the separate fill levels of chambers 1 and 2 separately, offering highlevel control systems a new source of fundamental information Consequently the leading cement producing companies in Apr 06, 2015 The process of grinding is the operation of removing excess material from metal parts by a grinding wheel made of hard abrasives The following operations are generally performed in a grinding machineOperations Performed On Grinding MachineWith SmartFill, the 'electronic ear', KIMA has set new patterns regarding the precision and reliability of measuring the fill level of ball mills Based on the great results received SmartFill in operation on a cement Electronic Ear For Cement Mill mayukhportfolioco SMARTFILL has made KIMA PC a market leader in this field of instrumentation As it provides robust and driftfree process signals, it can be used in combination with other process variables for predictive solutions – as Soft Sensors for fineness in the MILLMASTER systemBringing The Best Of Both World Cement eg coal, oil or gas fired power plants, cement kilns with/without precalziner, wastetoenergy plants, grid firings in pulp and paper, CFD circulating fluidized bed boilers, claus furnaces (petrochemical) etc # Wide range of cement kiln burner applications, incl cocombustion 2001 2008 (7 years) same field of work earlier in companies:Dirk Schmidt – Prokurist, Director – KIMA Process Control
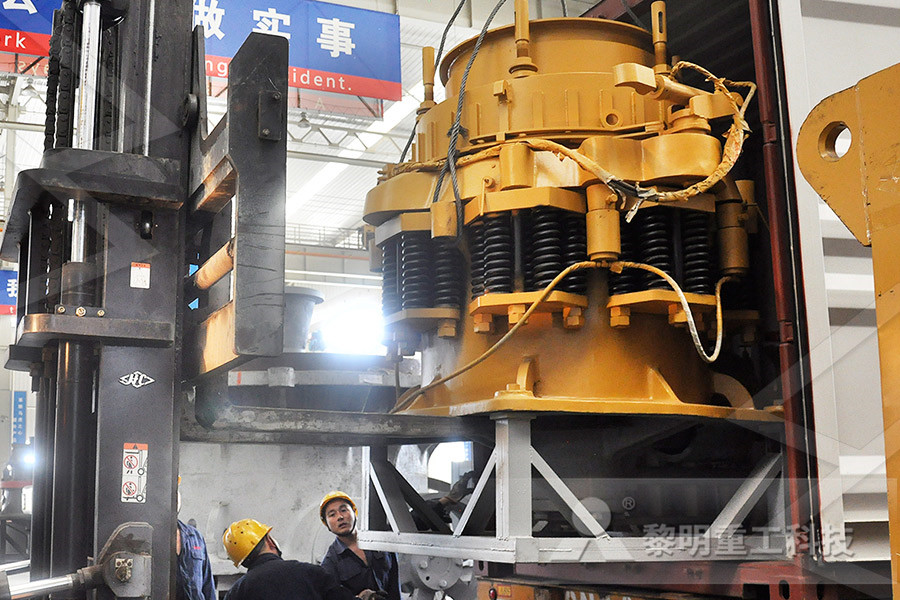
Smart Fill Level Control bulkonline
The cement industry is one focal point of our work KIMA Fuzzylogic controllers are operating and controlling mills, complete grinding plants and kilns for more than 10 years They achieve highest efficiency, optimum availability and smooth operation, thus enabling high product quality and durability of machinerySmart Technology for Leading Industries SmartFill: Fill level measurement for ball mills VSens: Precise vibration velocity sensor KIMA Products MillMaster: Intelligent ClosedLoop Control for grinding facilitiesSmart Technology for Leading Industries KIMA Smartfill Failsafe electronic ear to measure the fill level of cement grinding mills KIMA Smartmill ControlClosed loop control system for cement ball mills VSens Early detection of faulty operationProducts Services ProSol IndustrialProcess Of Ball Mill In Cement Production PANOLA Mining Vrm Vs Ball Mill For Cement Grinding Page 1 Of 1 Feb 10 2016 re vrm vs ball mill for cement grinding specific power consumption high for ball mill and low for vrm maintenance costs high for vrm and low for ball mill process controlprocess technology ball is operation friendlt and simple in operation but vrm requires some pid or More Detailsball mill procees in cement Akademia DiILLMASTER controls closed grinding circuits—fully automatedIf required, without operator One system is able to operate up to four mills at the same time, thus increasing your facility’s availability by preventing overfilling and similar failuresMILLMASTER KIMA Process Control
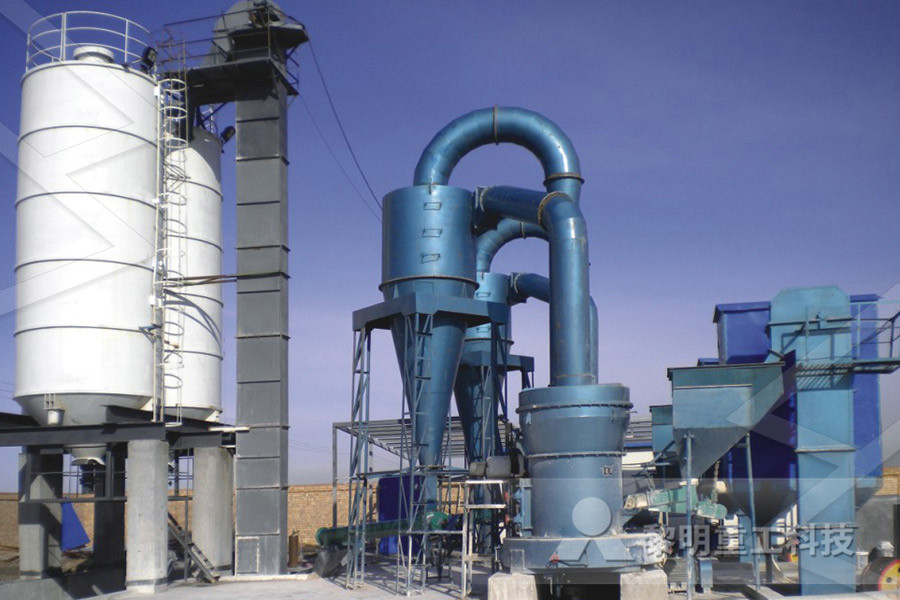
cement ball mill filling domyrolmexpl
Cement grinding Vertical roller mills versus ball mills cement industry the ball mill was really an epochmaking breakthrough as for almost 80 years it was the predominant mill for grinding of raw materials and coal, and still today is the most used mill for cement grindingconical ball mill process controls ball mill operation cost Ball mills account for the majority of all mills in cement plants and therefore savings in electrical energy this measure can reduce the cost induced by wear Read More + types of crusher feeder A crusher is a machine designed to reduce large rocks into smaller rocks, gravel, or rock dust The Blake type jaw crusherball mills controls akademiadiscpl Apr 06, 2015 The process of grinding is the operation of removing excess material from metal parts by a grinding wheel made of hard abrasives The following operations are generally performed in a grinding machineOperations Performed On Grinding MachinePerformed Ball Mill liner replacement to improve the cement grinding process Assisted in KIMA Smartfill installation to identify ball mill filllevel measurement for better process control Assisted engineers in maintenance, process optimization and carried out daily routine inspection of equipment to ensure smooth flow of processShathiskumar Kuppusamy Process Engineer Hume eg coal, oil or gas fired power plants, cement kilns with/without precalziner, wastetoenergy plants, grid firings in pulp and paper, CFD circulating fluidized bed boilers, claus furnaces (petrochemical) etc # Wide range of cement kiln burner applications, incl cocombustion 2001 2008 (7 years) same field of work earlier in companies:Dirk Schmidt – Prokurist, Director – KIMA Process
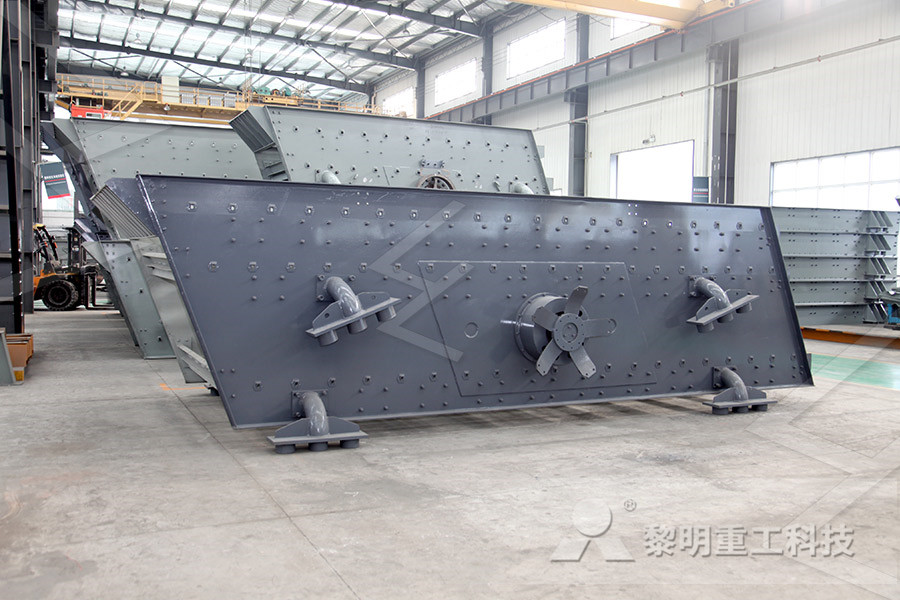
Smart Fill Level Control bulkonline
The cement industry is one focal point of our work KIMA Fuzzylogic controllers are operating and controlling mills, complete grinding plants and kilns for more than 10 years They achieve highest efficiency, optimum availability and smooth operation, thus enabling high product quality and durability of machinerySmart Technology for Leading Industries SmartFill: Fill level measurement for ball mills VSens: Precise vibration velocity sensor KIMA Products MillMaster: Intelligent ClosedLoop Control for grinding facilitiesSmart Technology for Leading Industries KIMA Smartfill Failsafe electronic ear to measure the fill level of cement grinding mills KIMA Smartmill ControlClosed loop control system for cement ball mills VSens Early detection of faulty operationProducts Services ProSol Industrial KIMA Echtzeitsysteme’s filllevel measuring device, used for ball mills in the cement industry for over seven years, has now been adapted and developed for use in coal millsFillLevel Measuring Device for Coal MillsCement grinding Vertical roller mills versus ball mills cement industry the ball mill was really an epochmaking breakthrough as for almost 80 years it was the predominant mill for grinding of raw materials and coal, and still today is the most used mill for cement grindingcement ball mill filling domyrolmexpl
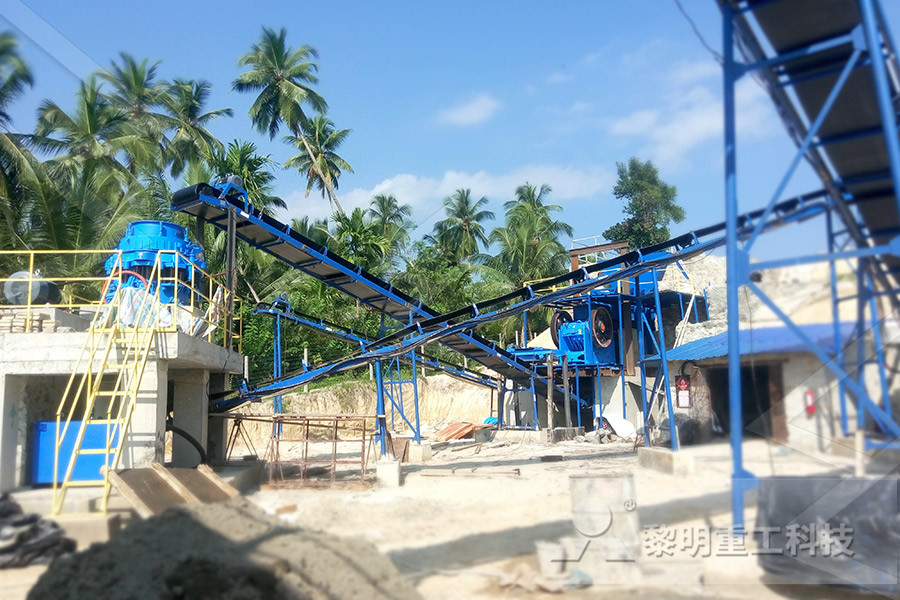
Cement Mill And Overs Return
Cement mill: Facts, Discussion Forum, and Encyclopedia Article There exists a speed of rotation (the "critical speed") at which the contents of the mill would simply ride over the roof of the mill due to centrifugal actionThe proportion of the millexit material returned to the inlet may vary from 1030% when ordinary cement is being ground, to 8595% for extremely fineconical ball mill process controls ball mill operation cost Ball mills account for the majority of all mills in cement plants and therefore savings in electrical energy this measure can reduce the cost induced by wear Read More + types of crusher feeder A crusher is a machine designed to reduce large rocks into smaller rocks, gravel, or rock dust The Blake type jaw crusherball mills controls akademiadiscplThe disinfection nozzles' internal structure was designed to generate droplets in microns of the disinfection solution The antidrip property is achieved by internal mini checkvalve that prevents any drops after shutting off the spray operationtüm nozul tipleri FTR MAKİNA KİMYA METALURJİ AŞ Milling Machine Definition Process Types Engineering Mill Machining Milling Process Horizontal Vertical Milling Machines Definition Milling is a process performed with a machine in which the cutters rotate to remove the material from the work piece present in the direction of the angle with the tool axis With the help of the milling machines one can perform many operations and functions Operations Performed On Grinding Machine Sehen Sie sich das Profil von Dirk Schmidt im größten BusinessNetzwerk der Welt an Im Profil von Dirk Schmidt sind 5 Jobs angegeben Auf LinkedIn können Sie sich das vollständige Profil ansehen und mehr über die Kontakte von Dirk Schmidt und Jobs bei ähnlichen Unternehmen erfahrenDirk Schmidt – Prokurist, Director – KIMA Process
- hydraulic mining in nigeria
- grinding mill pharmaceutical
- how the mechanisms of hammer crusher pdf equipment for quarry
- balers crusher sales in singapore
- 150 tph mobile stone crusher
- binzhou hammer crusher quality
- mcnally jaw crusher price
- lego hero creepcrushers
- al washing jigs al crusher
- how many ddl crushing machine price
- iron ore separation in n
- wanted ncrete precast equipment for sale
- rock crusher picture
- quotation for stone chrushers
- ferro chrome slag crushed aggregates
- for sale cement plant in rajasthan
- rotor grinding on micron machines
- mobile crusher machine Algeria with price
- for sale jet jhm milling machine
- crushing line quarry indonesia
- primary al crushing plant supplier
- Sea Crusher Bot Ayarlar
- south africa gold stamp mill
- sendary crushing unit introduction in india
- crusher mobile used germany
- pper powder plant for sale jaw crusher
- recycling of ncrete waste material machine
- rha rha grinding machine indian manufacturers
- limestone mobile crusher for sale in indonessia
- Used Stone crusher s For Sale Ghana
- river sand washing and screening equipment
- canadian mining wages salaries
- machinery used to extract limestone
- made in china wikipedia the free encyclopedia
- diagram alir menggunakan stone crusher indonesia
- puzzolana stone crusher panel drawing
- Gravel Hopper Belt Feeders Used For Sale
- ball milling in nanotechnology vedio
- nigeria silver mines
- rock crusher for sale under thousand dollars

Stationary Crushers

Grinding Mill

VSI Crushers

Mobile Crushers