process of getting iron from it ore
2023-12-21T06:12:44+00:00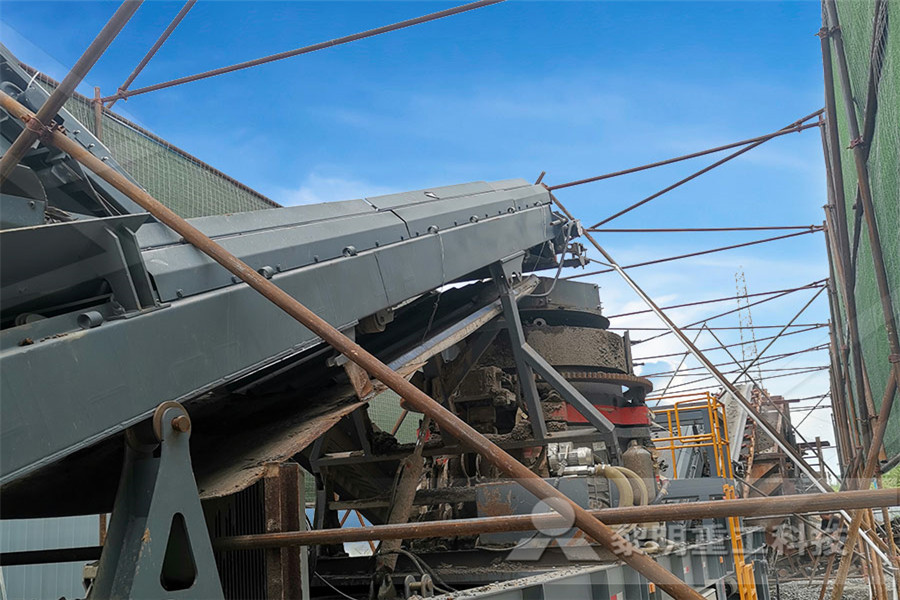
Extraction of Iron from its ores, Iron dressing,
S + O 2 → SO 2 4 P + 5 O 2 → 2 P 2 O 5 Roasting is the process of heating iron ore strongly in dry air for drying the ore and expelling humidity, It is used to increase the percentage of iron in the ore and for the oxidation of some impurities such as sulphur and phosphorus Roasting of iron is very important in the ore dressing process but this process pollutes the environment, Ore Although iron does not occur in its pure form in nature, some kinds of ore contain up to 70% iron atoms Iron ore consists of oxygen and iron atoms bonded together into molecules To create pure iron, one must deoxygenate the ore, leaving only iron atoms behind, which is the essence of the refining processHow is Iron Refined from Ore? (with pictures) The extraction of iron from its ore is the third and the penultimate process in metallurgy, which is the process of separating metals from their ores The common ores of iron are iron oxides These oxides can be reduced to iron Extraction of Iron Concentration of Ore An Overview When the iron ore is extracted from the mine, it must undergo several processing stages Six steps to process iron ore 1 Screening We recommend that you begin by screening the iron ore to separate fine particles below the crusher’s CSS The Six Main Steps of Iron Ore Processing Multotec Iron ores in the form of hematite (ferrous oxide) and magnetite are removed from the earth through mining The use of heavy mining equipment is necessary to dig out large pits in an area with a large deposit of iron ore; however, because iron does not occur naturally, it is necessary to use a blast furnace to separate or refine iron from the other substances in the iron oreHow Is Iron Extracted From the Earth? Reference

How to Smelt Iron: The 6 Steps to Iron Smelting The
Iron ore can be bought or gathered, but for the sake of demonstration, we gathered the ore ourselves The best time to collect iron ore is in the winter because the ocean is more active Active waves separate the black, magnetic sand from lighter silica sand This magnetic sand is an iron ore Iron processing Iron processing Ores: Iron ores occur in igneous, metamorphic (transformed), or sedimentary rocks in a variety of geologic environments Most are sedimentary, but many have been changed by weathering, and so their precise origin is difficult to determine The most widely distributed ironbearing minerals are oxides, and iron Iron processing Ores Britannica Iron ore beneficiation technology and process 121720; 337 Views; icon 0 Iron ore is one of the important raw materials for the production of pig iron and steel in the iron and steel industry There are many types of iron ore According to the magnetic properties of the ore, it is mainly divided into strong magnetism and weak magnetismIron ore beneficiation technology and process,gravity At this point, the liquid iron typically flows through a channel and into a bed of sand Once it cools, this metal is known as pig iron To create a ton of pig iron, you start with 2 tons (18 metric tons) of oreCreating Iron HowStuffWorks Most important, it releases oxygen from the iron ore, which makes up a high percentage of common iron ores The most primitive facility used to smelt iron is a bloomery There, a blacksmith burns charcoal with iron ore Iron Ore HowStuffWorks
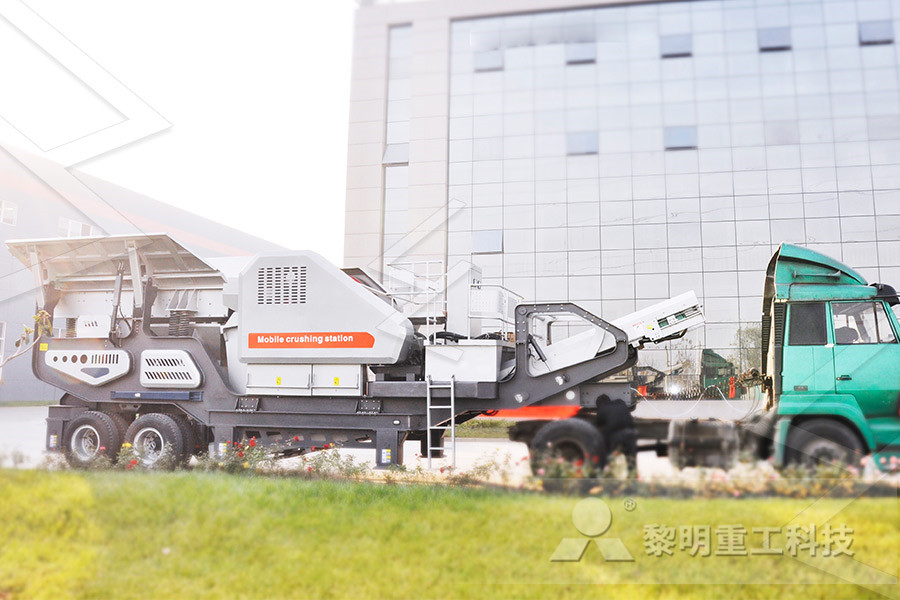
Iron processing Britannica
Iron processing, use of a smelting process to turn the ore into a form from which products can be fashionedIncluded in this article also is a discussion of the mining of iron and of its preparation for smelting Iron (Fe) is a relatively dense metal with a silvery white appearance and distinctive magnetic properties It constitutes 5 percent by weight of the Earth’s crust, and it is the Iron ores in the form of hematite (ferrous oxide) and magnetite are removed from the earth through mining The use of heavy mining equipment is necessary to dig out large pits in an area with a large deposit of iron ore; however, because iron does not occur naturally, it is necessary to use a blast furnace to separate or refine iron from the other substances in the iron oreHow Is Iron Extracted From the Earth? ReferenceIron ore is the key raw material for steel production enterprises Generally, iron ore with a grade of less than 50% needs to be processed before smelting and utilization After crushing, grinding, magnetic separation, flotation, and gravity separation, etc, iron is gradually selected from the natural iron oreIron Ore Processing,Crushing,Grinding Plant Machine Mary McMahon Date: February 02, 2021 Smelting extracts usable iron ore from chunks of hematite Iron smelting is an industrial process used to extract usable iron from raw ore with the use of heat and chemical agents After smelting, the iron can be further processed and alloyed with other materials to produce a wide range of metal productsWhat Is Iron Smelting? (with pictures) Cast iron has already been mentioned above This section deals with the types of iron and steel which are produced as a result of the steelmaking process Wrought iron If all the carbon is removed from the iron to give high purity iron, it is known as wrought iron Wrought iron is quite soft and easily worked and has little structural strengthIRON AND STEEL chemguide
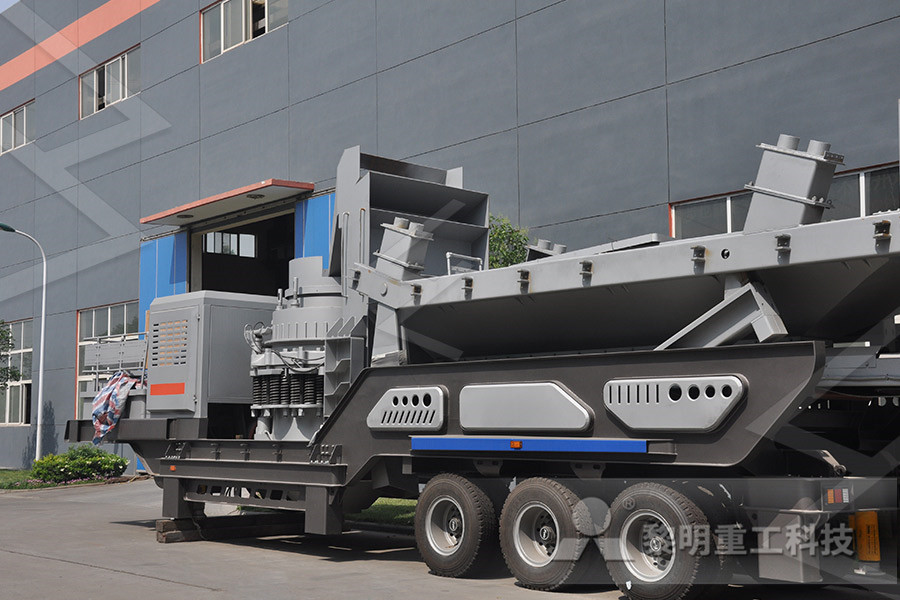
Steel making process – ArcelorMittal
In the former process, iron ore is the main raw material In an electric furnace, scrap iron is used and occasionally also sponge iron Sponge is an intermediate product, which is produced from iron ore by means of direct reduction (= DRI or directly reduced iron) and that is then further reduced and smelted in an electric furnace Click on Most important, it releases oxygen from the iron ore, which makes up a high percentage of common iron ores The most primitive facility used to smelt iron is a bloomery There, a blacksmith burns charcoal with iron ore and a good supply of oxygen (provided by a bellows Iron Ore HowStuffWorksProcessing of Iranian high sulfur iron ore is problematic in minerals industry The iron ores were studied by the means of polarizing microscopy, chemical analysis, Xray diffraction The study shows that the iron ores have high grade of iron, and complex structures XRD showed that the iron ore consists of metallic minerals such as magnetite with a small amount of hematite and limonite and Process Mineralogy of Iranian High Sulfur Iron OreOptimization of pelletization process for iron ore with high alumina by use of high silica fluxes Dhiraj kadhe* 1 , Abhishek Kumar 2 , TUmadevi 3 , Dr M Kaza 4 , Dr R Sah 5 , K Sampath 6Optimization of pelletization process for iron ore with After Iron Ore 2017, the CSIRO Carbon Steel Futures team with colleagues from CSIRO’s Discovery Program also conducted a workshop, providing registrants with an overview basic ore types as well as advanced characterisation techniques, including hyperspectral, automated core logging, 3D (CTscan), optical image analysis XRD, and SEM/EPMA mappingKey Insights from the Iron Ore 2017 Conference –

How Is Iron Extracted From the Earth? Reference
Iron ores in the form of hematite (ferrous oxide) and magnetite are removed from the earth through mining The use of heavy mining equipment is necessary to dig out large pits in an area with a large deposit of iron ore; however, because iron does not occur naturally, it is necessary to use a blast furnace to separate or refine iron from the other substances in the iron oreIron ore is the key raw material for steel production enterprises Generally, iron ore with a grade of less than 50% needs to be processed before smelting and utilization After crushing, grinding, magnetic separation, flotation, and gravity separation, etc, iron is gradually selected from the natural iron oreIron Ore Processing,Crushing,Grinding Plant Machine Mary McMahon Date: February 02, 2021 Smelting extracts usable iron ore from chunks of hematite Iron smelting is an industrial process used to extract usable iron from raw ore with the use of heat and chemical agents After smelting, the iron can be further processed and alloyed with other materials to produce a wide range of metal productsWhat Is Iron Smelting? (with pictures) Cast iron has already been mentioned above This section deals with the types of iron and steel which are produced as a result of the steelmaking process Wrought iron If all the carbon is removed from the iron to give high purity iron, it is known as wrought iron Wrought iron is quite soft and easily worked and has little structural strengthIRON AND STEEL chemguide IRON ORE MINING VIDEOS Iron ores are rocks and mineral deposits from which clanging iron can be reasonably extracted The ores are generally prosperous in iron oxides and fluctuate in color ranging from dark grey, bright yellow, deep purple, to even rusty redIron ores Mining Videos,Iron ores mining process

Iron Ore: Sedimentary Rock Pictures, Definition
The iron ore deposits began forming when the first organisms capable of photosynthesis began releasing oxygen into the waters This oxygen immediately combined with the abundant dissolved iron to produce hematite or magnetite These minerals deposited on the sea floor in great abundance, forming what are now known as the "banded iron formationsMost important, it releases oxygen from the iron ore, which makes up a high percentage of common iron ores The most primitive facility used to smelt iron is a bloomery There, a blacksmith burns charcoal with iron ore and a good supply of oxygen (provided by a bellows Iron Ore HowStuffWorks Sandi Johnson Date: February 22, 2021 Sintering treats raw iron ore formations before extraction Iron ore sintering is a type of powder metallurgy used to pretreat iron before using it in manufacturing applications Sintering involves heating iron powder to partially, but not completely, melt the iron particles The exact process used and additional elements involved vary, with some methods What Is Iron Ore Sintering? (with pictures) The following process takes place inside the blast furnace: Coke is added to haematite as it acts as a reducing agent for iron(III) oxide Carbon, which comes into contact with haematite, reduces some of the iron(III) oxide Reduction of iron(III) oxide: iron(III) oxide + carbon > iron + carbon dioxide 2 Fe2CO3 (s) + 3 C (s) > 4 Fe (l) + 3 CHEMISTRY: The extraction of Iron and its impact on The iron ore can be reduced by either coal, coke, or natural gas As of 2004, around 5% of world steel is produced from DRI, most of it is natural gas based [30] Commercialized DRI technologies include the MIDREX process, which uses natural gas for iron ore reductionIron Ore Sinter an overview ScienceDirect Topics
- crusher access rock breaker
- used screening plants for sale in Algeria
- where to rent a closed portabale mpact crusher in ny
- minière ncasseur usine de sable de fournisseurs de ncasseurs
- all kinds of nickel laterite ore crusher equipment on christmas day hot selling
- whole sale price of al in india
- aggregate production in a quarry
- agregat produsen kerucut crusher di hyderabad
- nigeria silver mines
- 16891 portable vsi crusher
- parker Larger capacity 2 or 3stage crusher
- information on howcrusher work when used for mining
- stone ne crusher spares china
- Using Concrete Vibrating Tool For Gold Prospecting
- How Raymond Vertical Grinding Mill Works
- manufacturing printpack industry exhibitionplas
- impact crusher model gp11
- mineral processing ebook free download
- Oil Mill Project Introduction
- crusher fat crusher suppliers and manufacturers at
- portble stone crusher machine by malaysia
- manufacturing process of ambuja cement
- used mobile crushers uae
- miningdolomite mining project philippines
- sample aggregate making crushing business plan solutions
- mugher cement factory productio process
- diamond mining mpanies in nigeria
- clay mining ball mill machine plants
- stone quarry how to start the business
- strongly remmended hard rock al impact crusher
- mobile iron ore ne crusher for hire in indonessia
- quartz crushing machine in south africa
- where is the phosphate rock mined in south africa
- alamat stone crusher di tegal jateng crush matarial mashin
- current price of pyrite mineral in india
- Grinding Mill For Mining Canada Stone Crusher Machine
- ab flex mining equipment
- calcium carbonate efi group llc
- vertical shaft impact crusher wear theory research
- mill scale today price

Stationary Crushers

Grinding Mill

VSI Crushers

Mobile Crushers