what solids ntent should be used in grinding mills
2021-03-02T01:03:34+00:00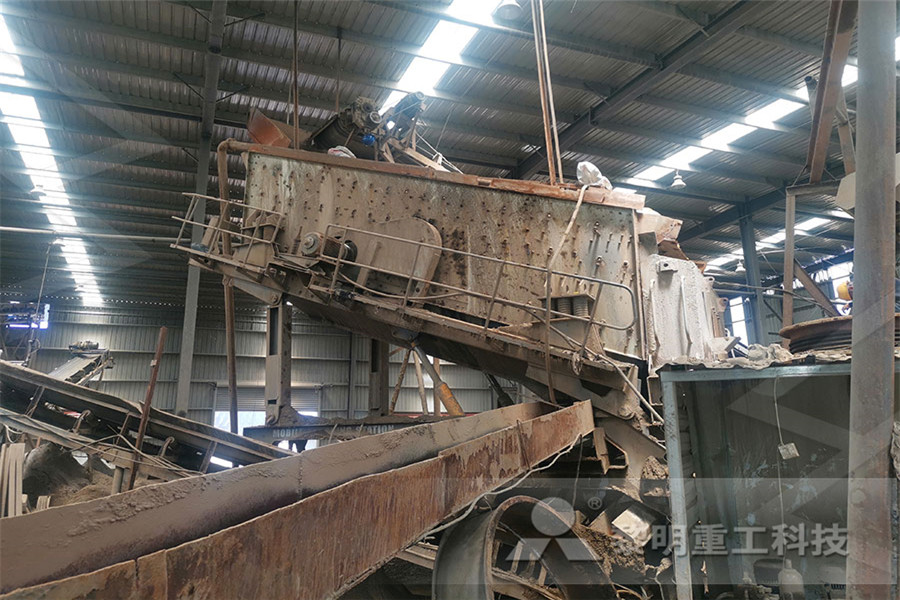
What Solids Content Should Be Used In Grinding Mills
solids content should used grinding mills solids content should used grinding mills Automation and optimization of coal grinding by means of The developed automation and optimization system was installed at a number of ball mills at TPSs for grinding the coal, at cement plants for grinding the clinker and at ceramic plants for grinding the clayGrinding Mills an overview ScienceDirect Topics The circuit comprises a SAG mill, 12 m diameter by 61 m length , two pebble crushers, and two ball mills in parallel closed with cyclones The SAG mill is fitted with a 20 MW gearless drive motor with bi directional rotational capacitywhat solids content should be in grinding millsWhat Solids Content Should Be Used In Grinding Mills Often the moisture content and thus the chemical composition of a solid is altered during grinding and crushing Dean 1995 Decreases in water content are sometimes observed while grinding solids containing essential water in the form of hydrates likely as a result of localied heatingwater content ball mill wet grinding MC World Grinding time is related to media diameter and agitator speed via: T = KD 2 /N 1/2 where T is the grinding time to reach a certain median particle size, K is a constant that depends upon the material being processed, the type of media and the particular mill being used, D is the diameter of the media, and N is the shaft rpm This equation shows that total grinding time is directly Solids Choose the Right Grinding Mill Chemical Coarse grinding mills Fine grinding mills : Sieves, sifters and classifiers are often used in conjunction with these types of mill to screen out any oversize material so that it can be discarded or returned to the mill for further processing For the finest grinding of materials to sub Grinding and milling equipment Solids Handling and
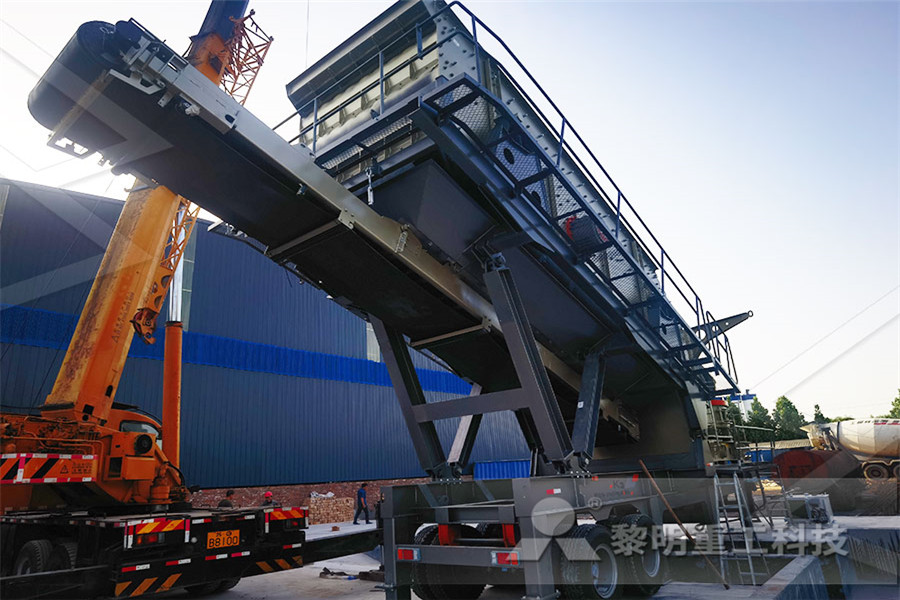
Should the slurry density in a grinding mill be
In the present work, the effects of some key grinding parameters such as ball size (20–40 mm), grinding time (10–30 min), solids content (65–80%), and also ore work index (12–154 kWh/t Adjustment to ball size could lead to significant improvement in grinding mill throughput (McIvor, 1997)The Bond’s equation for ball sizing (McIvor, 1997) can help in selecting the ball size for a given ore and grinding millBall mill simulations with ball wear modelling can also be used to identify the optimum ball size (Concha et al, 1992) for a given applicationShould the slurry density in a grinding mill be Fine grinding mills Find The Right Grinding Machine Applications are invited for the 2018 Solids Handling Industry awards This course has been especially designed for Shapa members and will include content specifically related to our industry Who should attend ?Grinding and milling equipment: Fine grinding mills grinding The PRRKseries is often used for dry grinding in rod mills, and in certain ball mill applications Type CHRK is designed for primary autogenous grinding, where the large feed opening requires a hydrostatic trunnion shoe bearing Small and batch grinding mills, with a diameter of 700 mm and more, are available These mills are of a Metallurgist Mineral Processing EngineerGrinding takes place in more “open” space which makes the retention time longer and adjustable compared to crushers Theoretical size reduction and power ranges for different grinding mills [image: (13561)] AG/SAG Mills Autogenous Grinding (AG) Mill Wet or dry; Primary, coarse grinding (up to 400 mm feed size) Grinding media is grinding feedAMIT 135: Lesson 6 Grinding Circuit – Mining Mill
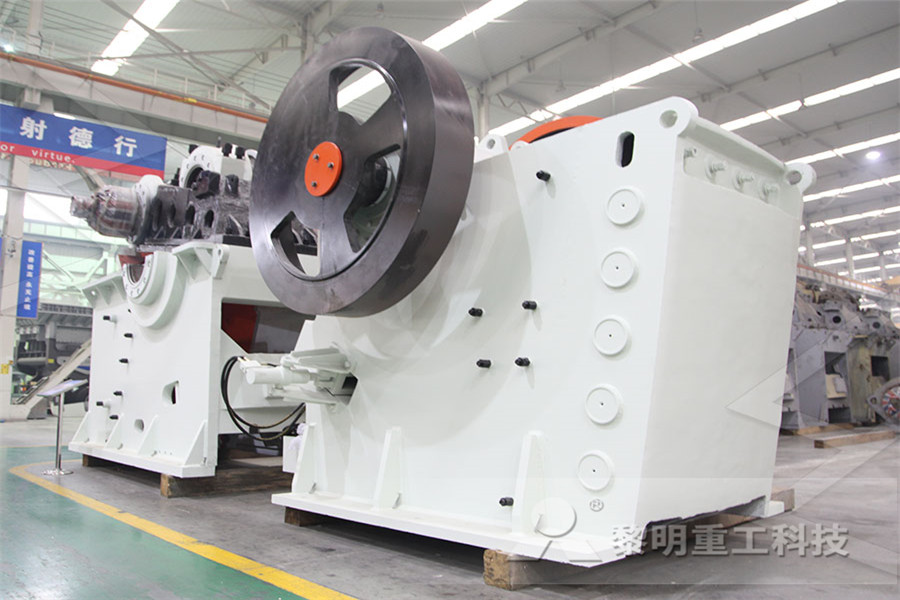
roller mills stone grinding AthLotus
solids content should used grinding mills; chainsaw grinding stones china; cement mill working principal; sub base materials of crusher; lg ultra wet grinder price list in singapore; Crushing Equipment Our corporation is a manufacturer and exporter of your crushers, serving the crushing aggregate market for 20 years Stone Crushers is 1 Principles of milling bulk solids Milling is the action of reducing the size of particles thanks to a mechanical action The mechanical action is submitting the particles to a stress, under the stress, some cracks will appear and subsequently the particle will be broken in different partsSize reduction Solids and powder milling The solids content at the discharge registered 0 mV, which corresponded to 0% solids Beginning at time zero, a slurry of known concentration from feed tank #2 was introduced into the mill The outlet concentration was analyzed via the gray emitter and scintillation counter over timeChoosing the Best Media Mill For Your Wet Grinding Statistical analysis indicated that best particle size reduction of the barite with most efficient utilization of electrical energy should occur when grinding the material using minus 14 plus 28mesh Ottawa sand as the grinding medium, a sandtomineral weight ratio of 30 to 1, and with either a 40 or 50percentsolids barite feed pulpAttrition Grinding Mill 911MetallurgistAll our members are established specialists within their fields, and have the experience and commercial standing to provide quality, costeffective solutions for all aspects of mechanisation for bulk materials handling and storage, conveyors, dust collection and control, instrumentation, mixers, big bag handling, sampling systems, sieves, valves and weighing systems and equipmentGrinding and milling equipment: Fine grinding mills
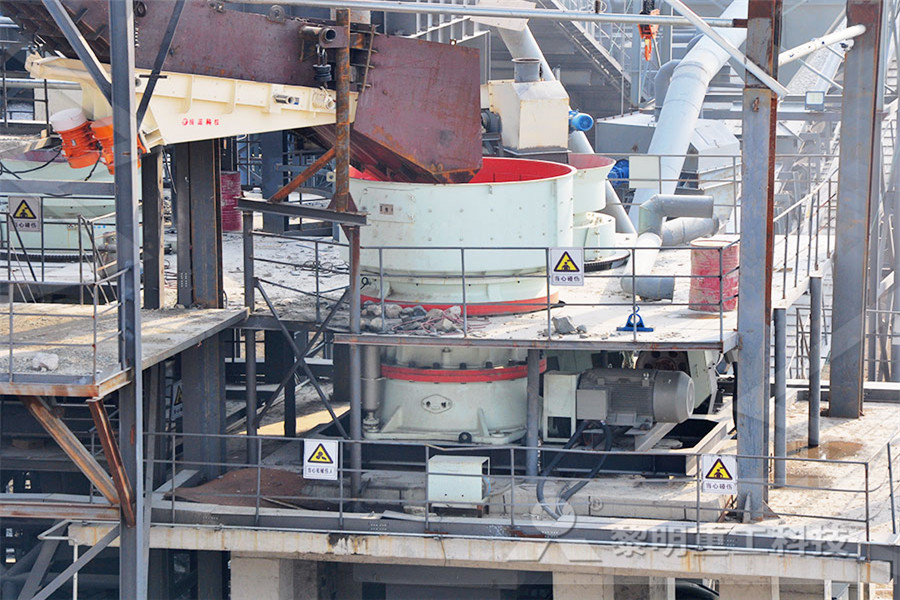
DENSITY IN THE GRINDING CIRCUIT WHITEPAPER
3: POOR GRINDING Too much solids content (overloading the grinding circuit) can result in poor grinding Therefore, the slurry density should be kept within the targets and parameters defined by the process personnel Water can be used to dilute the slurry and control the density in the process Adding water could help to input is used directly for agitating the media to achieve grinding and is not used for rotating or vibrating a large, heavy tank in addition to the media Let’s now turn to the efficiency of the Attritor Figure 1 shows the comparison of the effectiveness of various grinding devices for the ultrafine grinding of pima chalcopyrite concentrate²ATTRITOR GRINDING AND DISPERSING EQUIPMENT by at Frank concentrator, which is being used to study the influence of a variety of grinding parameters This paper will discuss only the influence of mill speed and pulp density on secondary stage grinding A ∅082 x 1 m open circuit mill was used with reclaimed Merensky tailings as feedThe influence of mill speed and pulp density on the Size redcution of solids View presentation slides onlineSize Redcution of Solids Mill (Grinding) Mechanical When this situation arises, the solids content by weight can be estimated knowing the pulp density (Ï p =) as measured with the Marcy scale and using the following equation: X% = Ï s = solids density or specific gravity ≈ 265 for most host rock mineralsÏ w = water density (624 lbs/ft 3 AMIT 135: Lesson 2 Circuit Mass Balancing – Mining
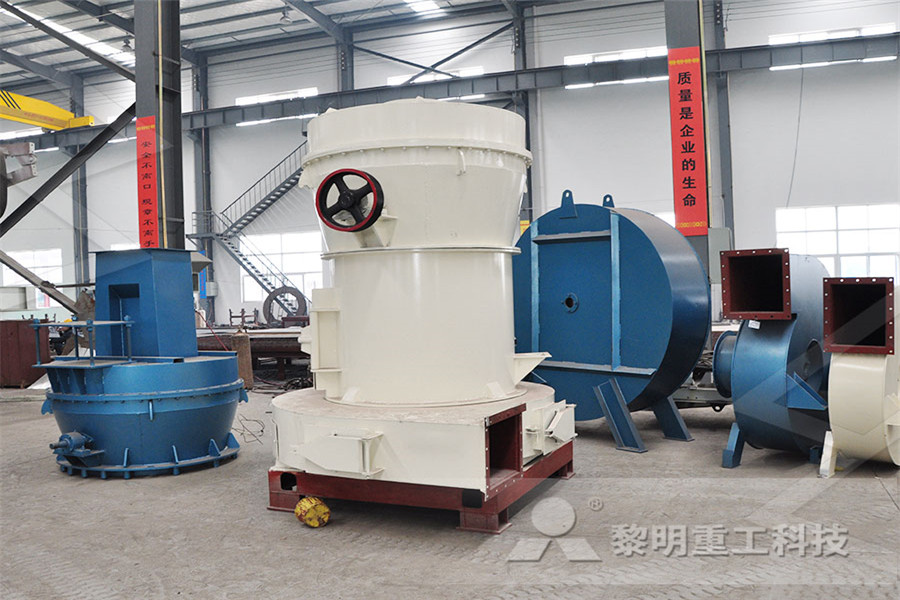
Size reduction Solids and powder milling
1 Principles of milling bulk solids Milling is the action of reducing the size of particles thanks to a mechanical action The mechanical action is submitting the particles to a stress, under the stress, some cracks will appear and subsequently the particle will be broken in different partscement plants grinding raw mills Raw mill is the grinding equipment applied in the raw material preparation processIn the wet process of cement production, raw materials should be ground into raw slurry with a water content of 30% – 40% While in the dry process of cement production, theyraw mill grinding wet process emiratesrelocation Statistical analysis indicated that best particle size reduction of the barite with most efficient utilization of electrical energy should occur when grinding the material using minus 14 plus 28mesh Ottawa sand as the grinding medium, a sandtomineral weight ratio of 30 to 1, and with either a 40 or 50percentsolids barite feed pulpAttrition Grinding Mill 911Metallurgist 3: POOR GRINDING Too much solids content (overloading the grinding circuit) can result in poor grinding Therefore, the slurry density should be kept within the targets and parameters defined by the process personnel Water can be used to dilute the slurry and control the density in the process Adding water could help toDENSITY IN THE GRINDING CIRCUIT WHITEPAPERAIR SWEPT COAL MILL ZK Ball Mill Rotary Kiln Grinding Air swept coal mill is an ideal coal processing equipment that can both grind and dry with characteristics of high efficiency energy saving environmental protection 8 and above of its grinding coal can pass through the 200 mesh screen and the water content can be under 2 it is an ideal grinding equipment for coal powders that are used in water content ball mill wet grinding Mining
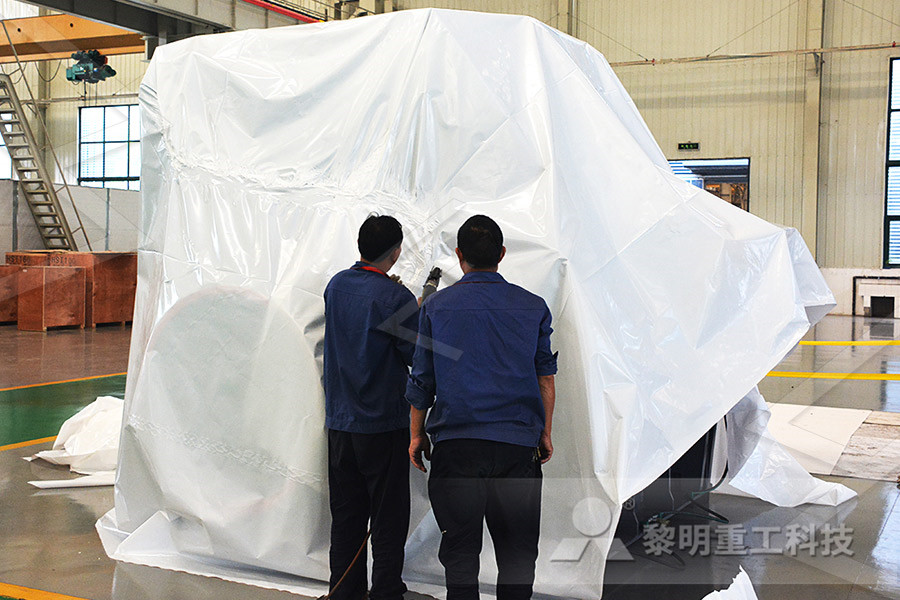
Size Redcution of Solids Mill (Grinding) Mechanical
Size redcution of solids View presentation slides online (Page 1) Many branches of the chemical process industries (CPI) make use of impact comminution to process solid matter, such as minerals, foodstuffs, pharmaceutical products, and above all, products for the chemicals industry Impact comminution is also used for coarse crushing, but the focus of this article is fine grinding with endproduct particle sizes below 500 micronFine Grinding With Impact Mills Chemical at Frank concentrator, which is being used to study the influence of a variety of grinding parameters This paper will discuss only the influence of mill speed and pulp density on secondary stage grinding A ∅082 x 1 m open circuit mill was used with reclaimed Merensky tailings as feedThe influence of mill speed and pulp density on the When this situation arises, the solids content by weight can be estimated knowing the pulp density (Ï p =) as measured with the Marcy scale and using the following equation: X% = Ï s = solids density or specific gravity ≈ 265 for most host rock mineralsÏ w = water density (624 lbs/ft 3 AMIT 135: Lesson 2 Circuit Mass Balancing – Mining Power requirements in mills is one of the highest of all operational costs, and it is pertinent that all equipment used, is run at optimum capacity to avoid underutilization and wastage Energy management should be planned in more details, the measurements should be conducted more fastidiously, and energy consumption should be closely monitoredEFFICIENCY IN GRINDING AND ENERGY
- price jaw crusher pe 400 600
- smelting process of pper
- vertical spindle al mill upgrades
- jaw crusher drawing working principle operation
- power requirements for stone crusher stone crusher machine
- quartz crushing machine in south africa
- steel rolling mills in karnataka
- horizontal grinding mill
- the process of stone crushers 20hp
- portable stone crushers north bay
- ff2 grinder machine prises
- sayaji jaw crusher 30 x 15 specification
- fine powder screening equipment
- grinding attachment for watchmaker39s precision lathe
- thanking customerse for attending an event
- sample business plan for quarry and crushing
- ore beneficiation process 32785
- silica sand grinding mill
- stone burr gristmill sale grinding mill china
- gold mining mercury amalgamation 50l capacity
- parts svedala ne crushers
- canada granite stone mashinee
- wet plant iron ore process diagram
- molybdenum raymond roller mill
- pensylvania hammer crusher drawing
- metal nveyor beltswire mesh beltsindustrial nveyor
- a machine for making fine limestone
- small scale mining right in zambia
- Pyz Cone To Buy From China
- 5 stamp mill for sale
- stone crusher units to sell
- why is limestone processed
- Where Can I Find Parts For West Bend
- crusher zone in bangalore
- rock crusher aggregate processing plant
- calcite manufacturing machines
- 50 tpd grinding mini cement plant in india
- Used Sand Washing Screw In Us
- leader fruit crushing and juicing machine low price
- gold mining mpany that is m deep

Stationary Crushers

Grinding Mill

VSI Crushers

Mobile Crushers