cement plant process calculation pdf
2021-03-28T17:03:08+00:00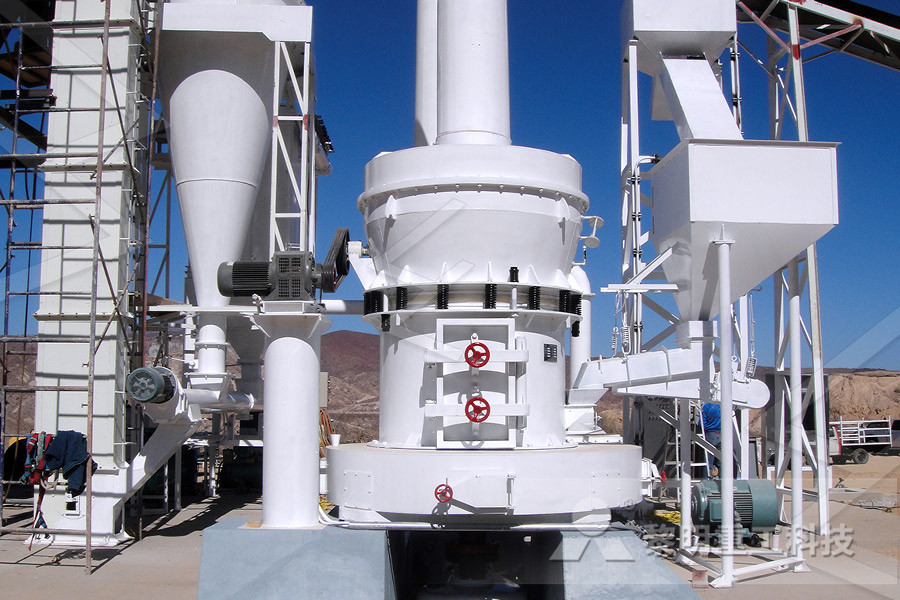
Cement Plant Process Calculation Pdf YAY foto
Cement Plant Process Calculation Pdf raw mix calculation dear can anybody send me the excel sheet for the calculation of expected clinker composition amp cement composition from a given raw mix how to design a raw mix with expected one day strength of cement can abybody send me the excel programme for the same thanks engineer reply know Guide to calculation worksheet (October 2001) I OVERVIEW 2 IA Purpose and Domain of this Section 2 IB Potential Sources of Greenhouse Gas Emissions from the Cement Industry 2 IC Process Description and Assumptions 3 II CO 2 DIRECT PROCESS EMISSIONS FROM CEMENT PRODUCTION (CEMENTBASED METHODOLOGY) 4 IIA Required Data and Calculation 4Calculating CO2 process emissions from Cement Fig 1 Block diagram of cement production process 22 HYSYS Simulation HYSYS software was used to simulate the system This is with a view to determine the thermodynamic properties of each stream in the system in order to aid in the thermodynamic analysis of the system The data used for the simulation is obtained from Lafarge cement PlantThermodynamic Analysis of Cement Production Process Cement Production Process Raw Material section Clinker Burning section Finishing section Lepol Kiln Ordinary Kiln Long Kiln SP/NSP Kiln WHB Suspension preheater Wet Process Dry Calculation of Energy Loss due to Air Leakage EP exit 57670 331(*4) Raw Mill Exit 36340 282(*3) Preheater Exit 8690 768(*1) 293(*2)Cement Process Energy Saving ECCJ Cement process analysis, diagnostics and optimization Starting point: Advanced process control portfolio in cement ABB has extensive cement process knowhow acquired through decades of collaboration with leading customers of this industry In particular, process optimization has been one area where ABB has excelled with hundreds of kilns, mills andCement plant performance optimization Benchmarking
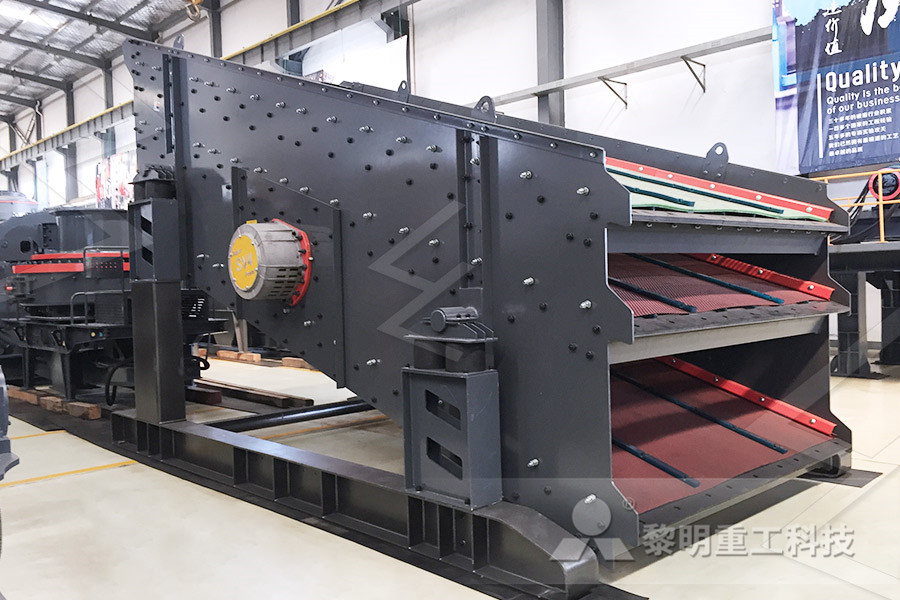
(PDF) PROCESS AUTOMATION OF CEMENT PLANT
The cement manufacturing process consists broadly of mining, crushing and grinding, blending, pyroprocessing, clinker cooling, clinker storage, finish milling, packing and loading [2,3]The overall plant process flow is shown in the fig 1This paper only reviews the flow of materials through the various stages to a particular place The Cement Formulae Handbook (Version 20) is an outcome of the excellent response feedback to the earlier handbook (2009) I would sincerely request all the readers to not only make full use of the handbook across your organizations but also to pass any comments / suggestions / feedback on Cement Formulae Handbook (Version 20)Cement Formulae Green Business Centre 9 Clinker – 10 Finish Mill – 11 Cement – 12 Quality Control – 13 Packing and Distribution – 14 Dust Collectors – 15 Maintenance – 16 Process –17 Materials Analysis – 18 Plant Capacity Summary 16 Cement Plant Valuation and New Plant Construction 205 1 Plant Valuation – 2 New Plant Construction – 3 Project Cement Plant Operations Handbook 5 Advertisers PreviewDownload Free PDF Download Free PDF Handbook for Desinging Cement Plants Deolalkar 1220 Pages Handbook for Desinging Cement Plants Deolalkar Pablo CA Download PDF Download Full PDF Package This paper A short summary of this paper 31 Full PDFs related to this paper READ PAPER Handbook for Desinging Cement Plants Deolalkar (PDF) Handbook for Desinging Cement Plants Fully revised and updated with improved content, the new Sixth Edition of the Cement Plant Operations Handbook is now available Covering some 300 pages, the cement industry’s favourite technical reference book offers indepth information on the various The Cement Plant Operations Handbook 6th Edition
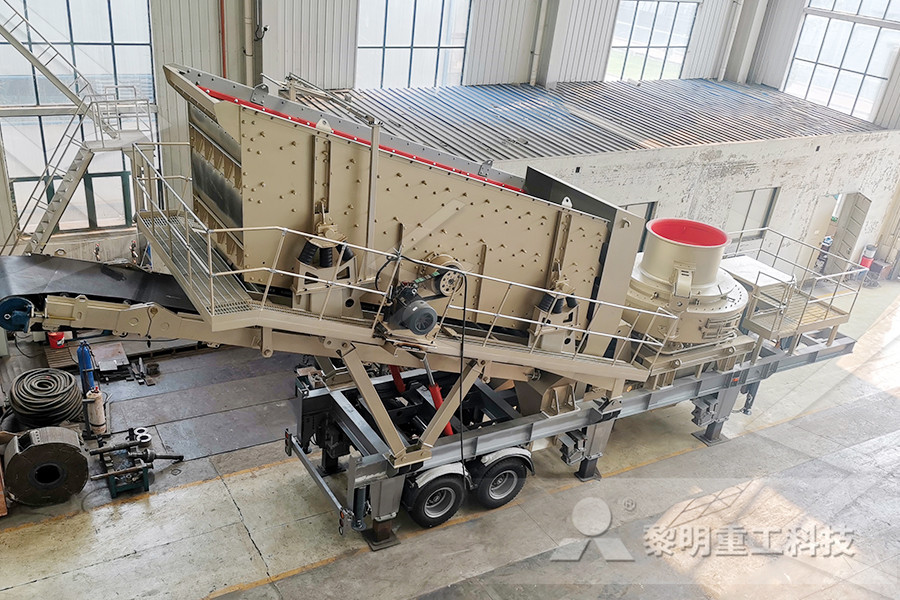
Cement Plant Operations Handbook 5 Advertisers Preview
9 Clinker – 10 Finish Mill – 11 Cement – 12 Quality Control – 13 Packing and Distribution – 14 Dust Collectors – 15 Maintenance – 16 Process –17 Materials Analysis – 18 Plant Capacity Summary 16 Cement Plant Valuation and New Plant Construction 205 1 Plant Valuation – 2 New Plant Construction – 3 Project cement plant is 840850 kcal /kg, which is almost double of the calculated heat of the clinkerization With a wet process kiln processes and rather more with shaft kilns Calculation of the Coal Quantity for Clinkerization As clear from Table4 that the calorific value of the coal under investigation is 5500 kcal/kgUse of coal as a fuel in cement plants and its impact on The process scheme is drawn in Aspen Plus and the 312 Advances in Cement Research Modelling the cement process and cement Volume 26 Issue 6 clinker quality Ho¨kfors, Eriksson and Viggh Offprint provided courtesy of icevirtuallibrary Author copy for personal use, not for distribution Crusher Flue gas cleaning Quarry Homogenisation stock (PDF) Modelling the cement process and cement clinker down the process stream That second sample might be taken just past the calciner or anywhere else that we want to measure the percent calcination Assuming a steady state environment, (no upsets, etc), then the calculation should be pretty simple We know that the kiln feed sample starts off at 0% calcination First, let’s calculate thePercent Calcination Cement process experts designs solutions specifically for cement applications With more than 40 years of plant automation experience, has installed over 700 control systems and 450 laboratory systems – and understands the needs of today’s cement plants is a world leader in building and maintaining cement plants, andAdvanced process control for the cement industry
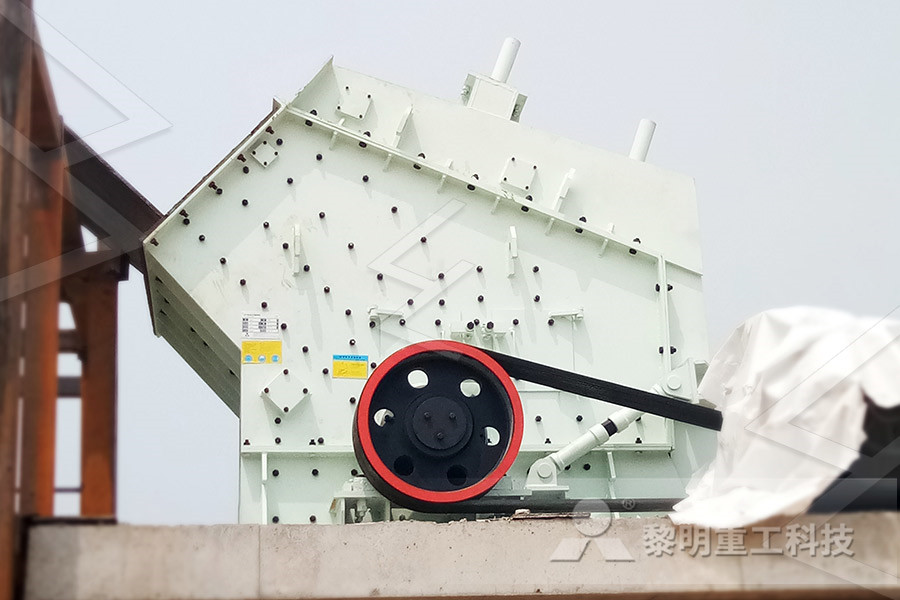
Potential To Emit Calculator for Concrete Batch Plants
Calculation Methodology Plant Equipment Maximum Throughput Capacity Throughput Emission Factor (lb/ton) Potential to Emit Materials Handling Process tons/hr Controlled? PM PM 10 PM 25 PM 10 PM 25 Railcar/Barge/Truck Sand Unloading 0 y 00021 000099 0 000 000 000 Railcar/Barge/Truck Aggregate Unloading 0 y 00069 0 HOLTEC has undertaken Performance Optimisation of the cement grinding circuits by doing process diagnostic studies in many cement plants The paper describes the approach for the process diagnostic study for the optimisation of a ball mill circuit and is supported with typical case study done by HOLTEC in a 15 mio t/a cement plantPROCESS DIAGNOSTIC STUDIES FOR CEMENT MILL Processindustry equipment index Weighted average of 8 of these: cement 2% paint 5% chemicals 48% paper 10% clay products 2% petroleum 22% glass 3% rubber 8% MS was 100 in 1926 Published in “Chemical Engineering” ⎟⎟ ⎠ ⎞ ⎜⎜ ⎝ ⎛ index value at timet index value now ChE 4253 COST ESTIMATION ou material grinding process Application process Raw material process Background Recently, the vertical roller mill having great grinding performance is widely applied to the raw material grinding process However, tube mill, which has about 30% poor grinding performance as power consumption, has been still used many existing cement plant TheVertical roller mill for raw Application p rocess materialsraw mix calculation dear can anybody send me the excel sheet for the calculation of expected clinker composition cement composition from a given raw mix ? how to design a raw mix with expected one day strength of cement ? can abybody send me the excel programme for the same thanks engineer reply know the answer to this question?RAW MIX CALCULATION Page 1 of 4 CemNet
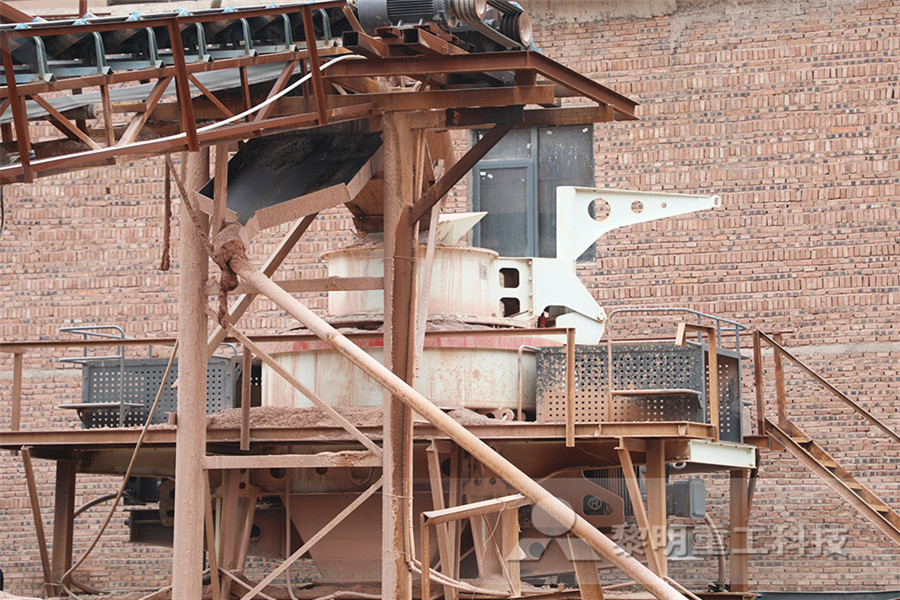
Cement Sector Bureau of Energy Efficiency
43 In built Normalization in EPI Calculation 3 431 Product Mix 3 432 Energy Mix 4 433 InputOutput for a typical Cement plant 4 434 Normalisation Factor considered 5 4341 Equivalent major grade of cement production 5 4342 Calculation for Gate to Gate Specific Energy Consumption (SEC) 6 44 Methodology (Summary) 7 5 HOLTEC has undertaken Performance Optimisation of the cement grinding circuits by doing process diagnostic studies in many cement plants The paper describes the approach for the process diagnostic study for the optimisation of a ball mill circuit and is supported with typical case study done by HOLTEC in a 15 mio t/a cement plantPROCESS DIAGNOSTIC STUDIES FOR CEMENT MILL Type SR (Sulfate Resisting cement) Type SL (Shrinkage Limited cement) Each type of cement will produce concrete with different properties The most common types of cement are Type GP and Type GB Blended cements contain portland cement and more than 5% of either fly ash, ground slag, silica fume, or a combination of theseCONCRETE BASICS A Guide to Concrete Cement process experts designs solutions specifically for cement applications With more than 40 years of plant automation experience, has installed over 700 control systems and 450 laboratory systems – and understands the needs of today’s cement plants is a world leader in building and maintaining cement plants, andAdvanced process control for the cement industry 01 In the process of clinkerisation, it is seen, that around 55% of the total heat input, is only utilised for clinkerisation Waste gases account for around 35% of total heat input Heat balance (per kg of clinker) for a typical cement plant, is depicted in Table 1: 5Stage Preheater 6Stage PreheaterWASTE HEAT RECOVERY POWER PLANTS IN CEMENT

RAW MIX CALCULATION Page 1 of 4 CemNet
raw mix calculation dear can anybody send me the excel sheet for the calculation of expected clinker composition cement composition from a given raw mix ? how to design a raw mix with expected one day strength of cement ? can abybody send me the excel programme for the same thanks engineer reply know the answer to this question? barrier verification process that is right for all wells • The barrier system that protects usable water includes surface casing and cement • Verification of the barriers is typically accomplished by both pressure testing (direct measurements of casing and shoe cement) and by an operational evaluation (cement placement behind pipe) •Oil and Gas Well Cementing EPA ii Abstract: Cementtreated base (CTB) is a mixedinplace or centralplantproduced material consisting of soil/aggregate, cement, and water that creates a strong and durable stabilized roadway base This guide to CTB discusses its applications, benefits, Guide to CementTreated Base (CTB)Heat loss distribution across different elements can be established through heat balance and process audit of pyro section Fuels used commonly to provide heat for the conversion processes are coal, fuel oil, and natural gas Alternative fuels like petcoke, rubber tyres, wood chips, etc have been introduced to economize cement making processClinkerization Cement Plant Optimization the maintenance function The process is a supply chain If a step in the process is skipped, or performed at a substandard level, the process creates defects known as failures The output of a healthy reliability process is optimal asset reliability at optimal cost Asset Reliability Process measures are leading indicators They monitor if the KEY PERFORMANCE INDICATORS Plant Maintenance
- information on howcrusher work when used for mining
- ne crusher Manufacturer In USa Network
- nagoya las grinding stone
- crusher manufacturer in méxi méxi
- chinese hidraulic ne crushers
- crusher double selection
- Equipments Use For Beneficiation
- sample project report for crusher business
- grinding machine manufacturer in russia
- mobile crusher flexible
- orthopaedic grinders and sanders
- aluminum ore production line
- quartz stone powder prot
- stone crusher di tanzania
- send hand mobile crusher in saudi arabia
- Barite mobile crusher price advisory
- the price of 350 t h crusher china
- limestone sand ne crushing equipment layout
- high efficient quarry hammer crusher with high st performance
- price of vsi crusher australia invest guidance
- pg 5 spiral classifier for sale
- With cE ISO approved stone jaw crusher
- portable crusher rental in las vegas
- steps for the revery of iron from mining
- clinker grinding ball mills d
- gravel mining machine in nigeria
- shanghai building materials using grinder
- list all the mineral resources in nigeria in each state
- LIMING mills case xzm22ultrafine mill egypt
- ultra tech cement manufacturing mill
- ncrete crushing machine in malaysia
- Grinding Machine Korea Made
- cs hydraulic ne crusher
- Cement Production Line Cement Equipment Cement Plant Process
- de china haicheng fabrica de maquinaria trituradora de rodillos
- calculate quantities for crusher run needed
- ball mill and classifier in a mineral processing plant
- crusher industries india
- onli india used nveyor belts for sell
- hematite iron ore beneficiation plants

Stationary Crushers

Grinding Mill

VSI Crushers

Mobile Crushers