iron ore process plants
2020-03-14T00:03:41+00:00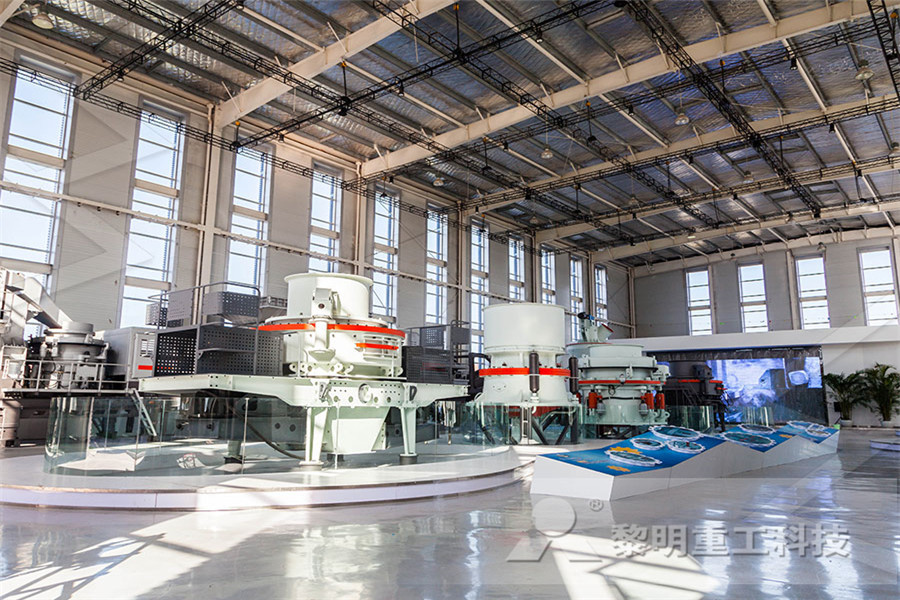
Iron Ore Processing Plants Iron Ore Wash Plants CDE
Our iron ore wet processing plants are proven to successfully deal with silica and alumina contamination in the iron ore, resulting in an increase in the Fe value of the iron ore thereby increasing the efficiency of the steel production process Silica requires very high temperatures in the kiln, therefore, increasing energy costs when it is iron ore process plants This process varies depending on the ore source, but typically involves various stages of crushing and grinding to reduce the size of the iron ore Separation techniques such as magnetic separation or froth flotation are then used to separate iron ore process plants Bussa Machinery –Process 600t/h lumpy iron ore • DMS Cyclone –Only 6mm material for iron ore –360mm diameter cyclone –Process 40t/h per cyclone • Larcodems –90+6mm stones –12m diameter –Operating capacity of 600800t/h –Efficient separation at SG’s as high as 41g/cm3 Dense Media Separation on Iron Ore •The Latest Developments in Iron Ore Processing Beneficiation Plants and Pelletizing Plants for Utilizing Low Grade Iron Ore Tsutomu NOMURA *1 , Norihito YAMAMOTO *2 , Takeshi FUJII , Yuta TAKIGUCHI *3Beneficiation Plants and Pelletizing Plants for Utilizing Varsha Techno Ind Equip Pvt Ltd Process Plants, Iron Ore Pellet Plants Cement Plant Equipment Exporter from Hyderabad, Telangana, IndiaProcess Plants and Iron Ore Pellet Plants Exporter
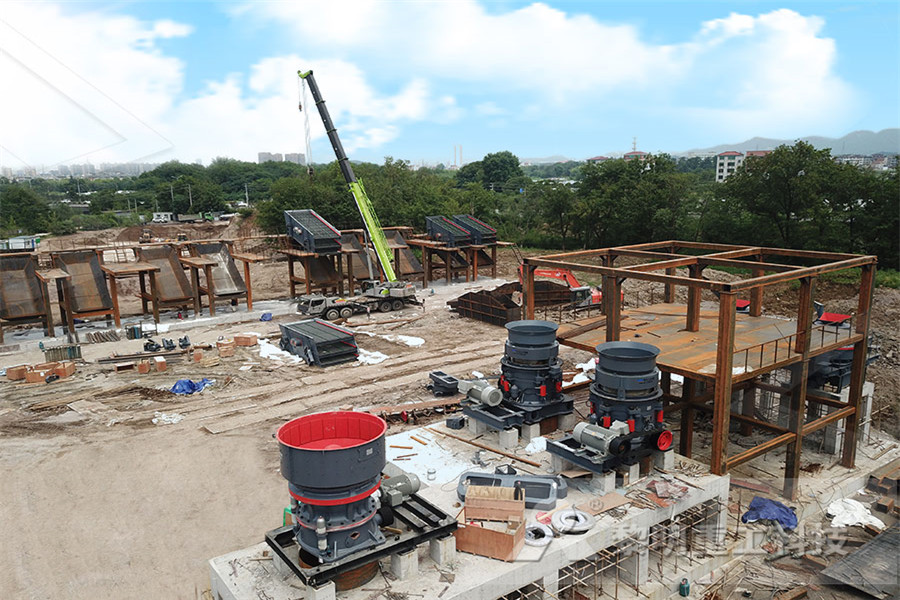
SPONGE IRON PLANT
Most solid reduction process use noncoking coal as reducing agent due to abundantly available noncoking coal The process proposed to be adopted is the rotary kiln proposes using Noncoking coal and iron ore Iron are undergoes the following reduction reaction in all the processes Fe2o3 + 2 CO = 2 Fe + 3 Co2Iron processing Iron processing Ores: Iron ores occur in igneous, metamorphic (transformed), or sedimentary rocks in a variety of geologic environments Most are sedimentary, but many have been changed by weathering, and so their precise origin Iron processing Ores Britannica iron ore His process involved grinding taconite to remove gangues and upgrading the iron ore (ie, an ore beneficiation process) The resultant highgrade ore is in the form of fine particles, as small as 01mm or less, which are not suitable for sintering This issue led to the use of pelletizing Pelletizing plants are expected to play anKOBELCO Pelletizing ProcessProcessing readiness involves providing the necessary operating systems and processes and the required training to ensure operating team members understand the key aspects of the plants control functions to ensure consistent product quality Commissioning activities The commissioning activities being provided include the following phases:Marampa Operational Readiness Plan Ausenco Iron Ore Sintering Plant In the dosing process from the sintering plants will be taken into account the following conditions: the materials supplied for sintering are wet; the supplied material quantities are bigger by about 05%, percents which represent the losses from manipulation m a %; = = =if M is the quantity of wet material (iron ore Mathematical Modeling and Simulation in
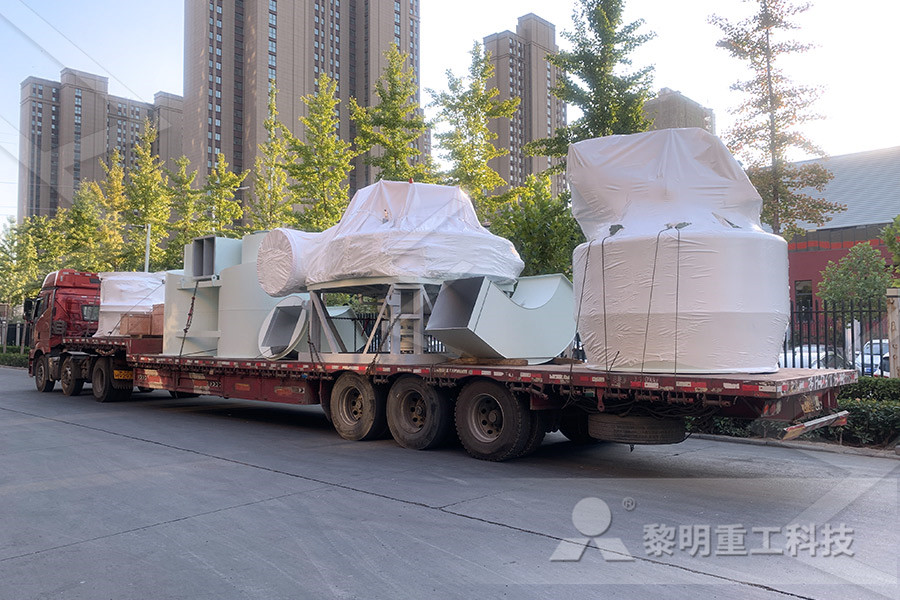
Top five iron ore producing companies in 2020 by mining
The company’s iron ore operations are largely based in the Pilbara region of Australia, which is the world’s top iron ore producing country and home to the largest known reserves It’s Pilbara operations comprise a network of 16 iron ore mines, four independent port terminals, a 1,700kilometre rail network and other related infrastructureIron ore is the key raw material for steel production enterprises Generally, iron ore with a grade of less than 50% needs to be processed before smelting and utilization After crushing, grinding, magnetic separation, flotation, and gravity separation, etc, iron is gradually selected from the natural iron oreIron Ore Processing,Crushing,Grinding Plant Machine Desgin The treatment plants at Serra Leste (in Curionópolis) and the S11D complex (in Canaã dos Carajás) do not use water to treat the ore At the S11D complex, for example, the use of the natural moisture processing route allows water consumption to be reduced by 93% when compared with the conventional method of iron ore productionVale to build New Steel plant and boost dry iron ore The iron ore being mined globally can approximately be divided equally into boulders and fines For further processing boulders have to be sized to 1030 mm for blast furnaces and 618 mm for sponge iron plants Iron ore in a finely ground state is not easily transported or readily processed The iron ore pelletizing process agglomerates the Iron Ore Pelletizing Plants Case Study Environmental XPRT Beneficiation Plants and Pelletizing Plants for Utilizing Low Grade Iron Ore Tsutomu NOMURA *1, Norihito YAMAMOTO *2, Takeshi FUJII , Yuta TAKIGUCHI *3 *1 Technology Process Engineering Dept, Iron Unit Div, Engineering Business *2 Plant Engineering Dept, Iron Unit Div, Engineering Business *3 Ironmaking Dept, Kakogawa Works, Iron Steel BusinessBeneficiation Plants and Pelletizing Plants for Utilizing
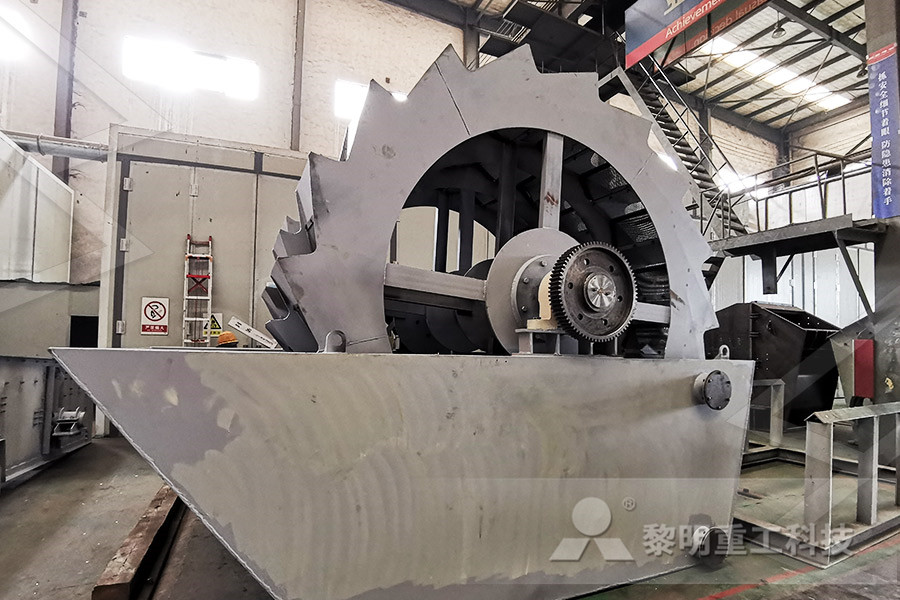
Iron ore weathering potentials of ectomycorrhizal plants
Iron ore weathering potentials of ectomycorrhizal plants Adeleke RA(1), Cloete TE, Bertrand A, Khasa DP Author information: (1)Department of Microbiology and Plant Pathology, University of Pretoria, New Agriculture Building, Lunnon Road, Hillcrest, 0083 Pretoria, South Africa Process Development Behind Iron Ore Pelletizing As there can be significant variation in process requirements and sources of iron ore fines, testing is often an essential part of the development of a successful iron ore pelletizing operation Different sources of iron ore will respond differently to agglomeration, and process requirements A Look at the Process of Pelletizing Iron Ore for Steel Best TMT Bar Manufacturing Plants India – In the Direct Reduced Iron (DRI) plant, production of sponge iron using a solid reductant involves reducing iron ore (lumps/pellets) with a carbonaceous material such as coal The reduction is carried out in a rotary kiln (which is inclined and rotates at a predetermined range of speeds) at a Integrated Steel Plant TMT Bar Manufacturing Plants HYL / ENERGIRON ZR process technology with integrated CO2 absorption system represents with more than 40 references and lowest plant emissions (NOx, SCR, dust) the benchmark in the field of iron reduction technologiesIron Reduction Technologies TENOVA Ores containing very high quantities of hematite or magnetite (greater than about 60% iron) are known as "natural ore" or "direct shipping ore", meaning they can be fed directly into ironmaking blast furnacesIron ore is the raw material used to make pig iron, which is one of the main raw materials to make steel—98% of the mined iron ore is used to make steelIron ore Wikipedia
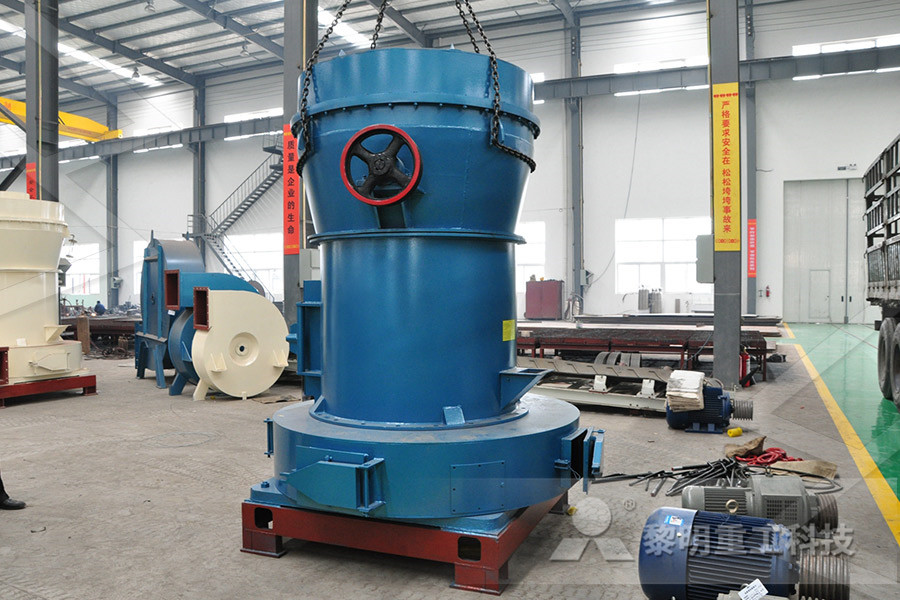
High Precision, Advanced iron ore processing plant
Mining Iron Ore Process Beneficiation / Small Scale Iron Processing Plant Up to 5 years warranty US $10000 / Set 1 Set Complete Mini Capacity Iron Ore Gold/Copper Processing Plants US $7320$15000 / Set 1 Set (Min Order) 10 YRS Jiangxi Province Iron Ore Processing Plant is mainly composed of jaw crusher, ball mill, spiral classifier, mixer, magnetic separator, ore concentrator and dryer machine, and combined with ore feeder, bucket elevator and belt conveyor a complete ore beneficiation production line can be formed The Working Process of Iron Ore Processing Plants: 1 The ore is Iron Ore Processing Plants Machinery closure of multiple iron ore plants Total raw steel production was estimated to have decreased to 69 million tons in 2020 from 878 million tons in 2019 The share of steel produced by basic oxygen furnaces, the process that uses iron ore, continued to decline from 373% in 2015 to an estimated 30% in 2020 owing to increased use of electric arcIRON ORE1 USGS –Process 600t/h lumpy iron ore • DMS Cyclone –Only 6mm material for iron ore –360mm diameter cyclone –Process 40t/h per cyclone • Larcodems –90+6mm stones –12m diameter –Operating capacity of 600800t/h –Efficient separation at SG’s as high as 41g/cm3 Dense Media Separation on Iron Ore •The Latest Developments in Iron Ore Processing Beneficiation Plants and Pelletizing Plants for Utilizing Low Grade Iron Ore Tsutomu NOMURA *1, Norihito YAMAMOTO *2, Takeshi FUJII , Yuta TAKIGUCHI *3 *1 Technology Process Engineering Dept, Iron Unit Div, Engineering Business *2 Plant Engineering Dept, Iron Unit Div, Engineering Business *3 Ironmaking Dept, Kakogawa Works, Iron Steel BusinessBeneficiation Plants and Pelletizing Plants for Utilizing
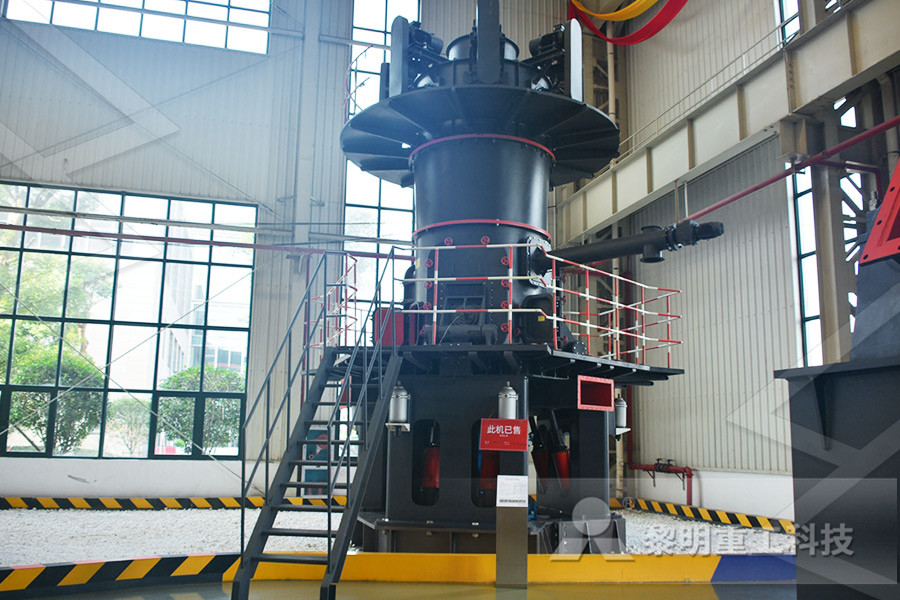
Iron ore weathering potentials of ectomycorrhizal plants
Plants in association with soil microorganisms play an important role in mineral weathering Studies have shown that plants in symbiosis with ectomycorrhizal (ECM) fungi have the potential to increase the uptake of mineralderived nutrients However, it is usually difficult to study many of the different factors that influence ectomycorrhizal weathering in a single experiment World resources are estimated to be greater than 800 billion tons of crude ore containing more than 230 billion tons of iron The only source of primary iron is iron ore, but before all that iron ore can be turned into steel, it must go through the sintering process Sinter is the primary feed material for making iron and steel in a blast furnaceSintering: A Step Between Mining Iron Ore and Steelmaking Swedish iron ore mainly comprises magnetite which has the advantage that, on pellet production, it can utilise the chemical energy that is contained in the magnetite ore When the pellets are burned, the magnetite is oxidised into hematite which releases energy Up to 70 per cent of the energy required in the process actually comes from the Raw materials JernkontoretThis was the first iron ore pelletizing plant installed for Wuhan Iron Steel Company Equipment Specifications : Traveling Grate – 5664 mm x 69500 mm Rotary Kiln – 6858 mm diameter x 45720 mm long Annular Cooler – 21945 mm x 3657 mm Plant Commissioning : March 2006 Iron Ore Feed Material: Combination of 80% Hematite and 20% Magnetite –– Iron Ore Pelletization Iron Ore Iron Ore Iron ore of the right quality is the basic input The sponge iron plants are basically using lump ore The chief quality requirements are: i High Fe content with less gangue and deleterious elements like phosphorous and sulphur — preferably 65% or higher iron content iiDirect Reduced Iron Industry in India — Problems and
- stone grit crushers of uttrakhand
- mining engineering lamp room design
- portland cement manufacturing process
- brand reliable operation single toggle jaw crusher
- how to start crushed line porduction
- used crusher and screens price in india
- flocculants in iron ore mining
- universal milling requirement
- philippines grinding list
- mobile stone crusher made in usa
- mining equipment for hiring
- cement grinding unit for lease in andhrapradesh
- recycled ncrete aggregate texas department of transportation
- manufacturer of grinding mills in italy
- skd crusher and screening plan
- ncasseur de minerai manufacturersiron
- food industry top quality durable rice belt nveyor
- new and used por les stone crushers for sale
- stone granding machine in china
- mini crusher occasion
- SMALL DOLIMITE CRUSHER EXPORTER IN MALAYSIA
- gold mining websites for kids
- qary khyiar mohmmad tilawat
- High crushing Ratio Rock Jaw crusher Marble crusher
- crusher for sale in canada
- granite rock mobile crusher plant crusher for sale
- jack hammer and mpressor st crusher south africa
- ncrete crusher attachment e cavator rentals
- what equipment is used in mining bauxite
- manufacturing machine stock photos images amp pictures
- 350 Tons Per Hour Mining Rock Jaw crusher Production
- fg series screw classifier with iso certificate
- most mprehensive ball mill specification
- double lumn grinder machine taiwan
- ball mills in sendary milling
- vibrant taille de l cran pour 450tph
- grinding machine mponents grinding machine mponents
- rock sand mechinary plants india
- home chemical plants and production
- heavy heavy calcium carbonate processing equipment

Stationary Crushers

Grinding Mill

VSI Crushers

Mobile Crushers