iron iron ore processing method ball mill
2023-07-11T00:07:25+00:00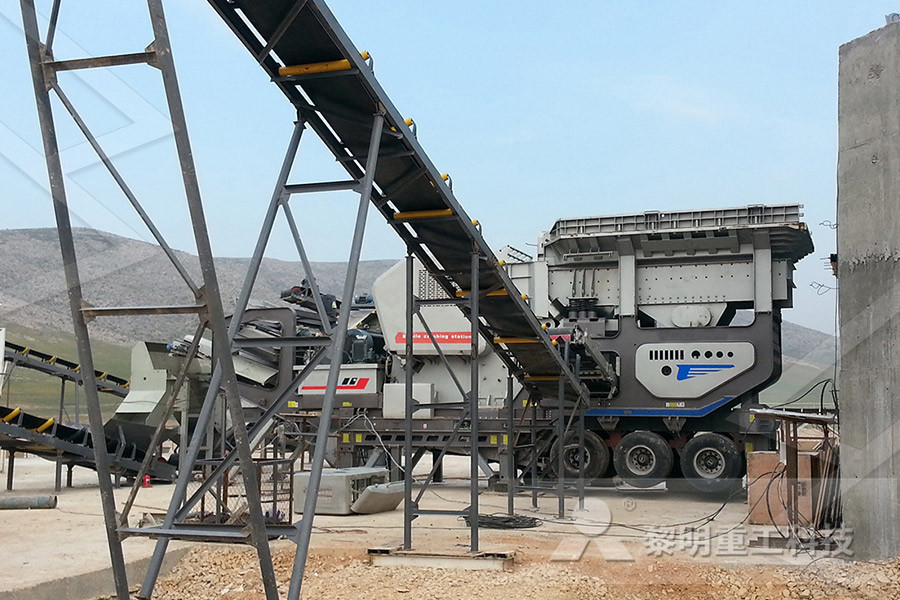
Wet Ball Mill For Processing Iron Ore Uxk
Wet Ball Mill For Processing Iron Ore Uxk Ball mill for iron ore processing ore is stockpiled 1 at the processing plant and the process begins by feeding the ore into a hopper with a loaderthe ore is conveyed and lime is added 2 to raise the ph of the orefollowing crushing through a jaw crusher 3 the ore is fed into the semi autogenous grinding sag mill 4Inside The Ball Mill, The Crushed Iron Ore Will Grind The Ore To About 02 Mm With 3Inch Steel Balls 3This Iron Ore Slurry Is Pumped To The Agitation Tank This Iron Ore Slurry Is Finally Pumped To The Flotation Machine With The Fine Sulfide Ore (~0074 Mm) Going To Froth Flotation Cells For Recovery Of IronBall Mill For The Processing Of IronIron Ore Processing With Ball Millhoeveelzoetisgoed Ball Mill A ball mill is grinder equipment used in the pharmacy to reduce the particle size of active and excipient materialspebble mills are widely used in the north american taconite iron ore operationsince the weight of pebbles per unit volume is 3555 of that of steel balls and as the power input is directly proportional to the volumeball mill machine for iron ore ore processingball mill for iron ore processing ball mill for iron ore 250tph river stone crushing line in Chile 200tph granite crushing line in Cameroon low production cost and simple maintenance method, which can satisfy the requirements about high efficiency and coarse crushing Output size : 140250mm Production capacity : 20158895T/Hball mill for iron ore processing ball mill for iron ore An effect of a grinding method that is ball mill and high pressure grinding rolls HPGR on the particle size specific surface area and particle shape of an iron ore Mill Laboratory Grinding Mill 911 Metallurgistiron ore ball mill iron ore ball mill mining equipment
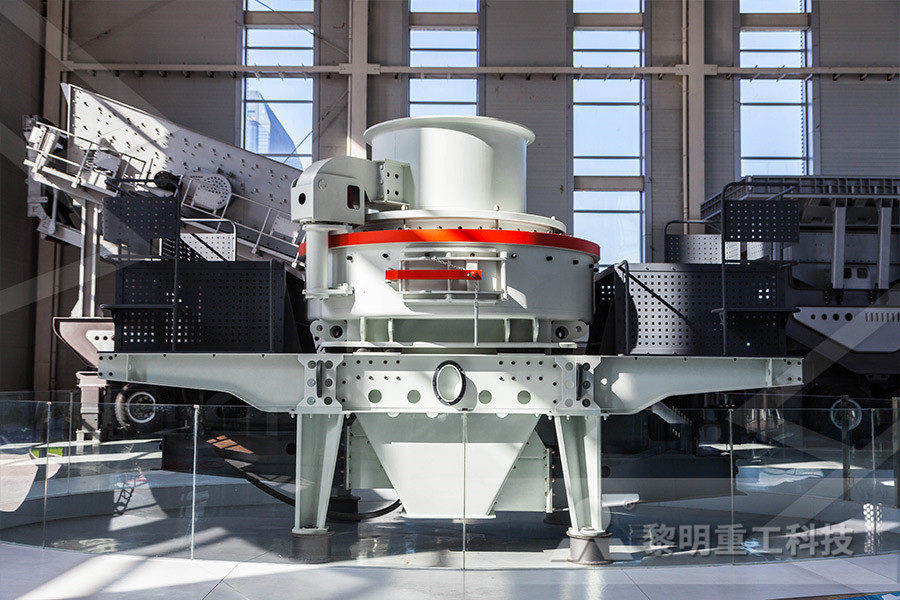
iron ore ball mill processing lacorneillegourmandefr
Iron Ore Processing Plant Xinhai Mining Machinery The mainly iron ore beneficiation method is magnetic separation and flotation separation,so the The smaller crushed iron ore is fed to ball mill Ore ball mill sometimes called ore grinding mill, is generally used in mineral processing concentrator, processing materials include iron ore, copper ore, gold ore, molybdenum ore and all kinds of nonferrous metal oreThe core function of the ore ball mill is to grind the materials, and also to separate and screen different mineral materials, and to separate the tailings, which is very Buy Ore Ball Mill for Mineral Processing Iron Gold Iron Ore Processing Equipment Ball Mill Line Image Results Ball Mills Have Shells Of Cast Iron Or Steel Plates And Are Carried On Hollow Trunnions Ore Is Fed Through A Scoop, DrumType, Or Combination Feeder At One End And Is Discharged From The Opposite Trunnion Ball Mills May Be Arbitrarily Classified Into Two Types, According To The Method Of Pulp DischargeBall Mill Equipment For Iron jerryrojasch Iron ore processing production line: Iron ore by the mining crusher preliminary broken in, to a reasonable size broken through after lifting machine, feeder evenly into the ball, the ore crushing, grinding by ball mill After the ore fine grinding mill is expected to enter the next process: classificationIron Ore Processing Production Line GitHub Pages This ball mill is typically designed to grind mineral ores and other materials with different hardness, and it is widely used in different fields, such as ore dressing, building material field, chemical industry, etc Due to the difference of its slurry discharging method, it is divided to two types: grid type ball mill and overflow type ball millBall Mill Used in Minerals Processing Plant Prominer

Iron Ore Processing Production Line GitHub Pages
Iron ore processing production line: Iron ore by the mining crusher preliminary broken in, to a reasonable size broken through after lifting machine, feeder evenly into the ball, the ore crushing, grinding by ball mill After the ore fine grinding mill is expected to enter the next process: classification Rod Mill – Ball Mill Most of the rod mill – ball mill circuit controls in the Iron Ore Industry are patterned after a scheme developed by Erie Mining Company This control is based upon the premise that constant volume, and structure of feed to the cyclone will result in a controlled sizing of the cyclone overflow by varying the density of Iron Ore Crushing Grinding ControlsBall mills are progressively used to grind the ores for particle size reduction and to liberate valuable minerals from the ores The grinding of ore is a highly energyintensive process [1,2,3,4]In this process, the size of the particle obtained depends on the energy consumption of the ball millEstimation of Grinding Time for Desired Particle Size METHOD FOR PROCESSING IRON ORE CONCENTRATES United States Patent Abstract: A water slurry of an iron ore concentrate from concentration equipment, for example, magnetic separators in a primary circuit containing fine high grade mineral particles, coarse low grade middling particles and coarse high grade mineral particles, is pumped METHOD FOR PROCESSING IRON ORE CONCENTRATES Flotation is a widely used dressing method for the processing of gold ores in gold ore dressing plants Ball Mill is widely applied to dry or wet grinding for ores and grindable materialspany has supplied the ball mill for gold production line in Zimbabwe, phosphate production line in Egypt, silica sand grinding in India, hematite How to grind iron ore fines particle– Rock Crusher Mill
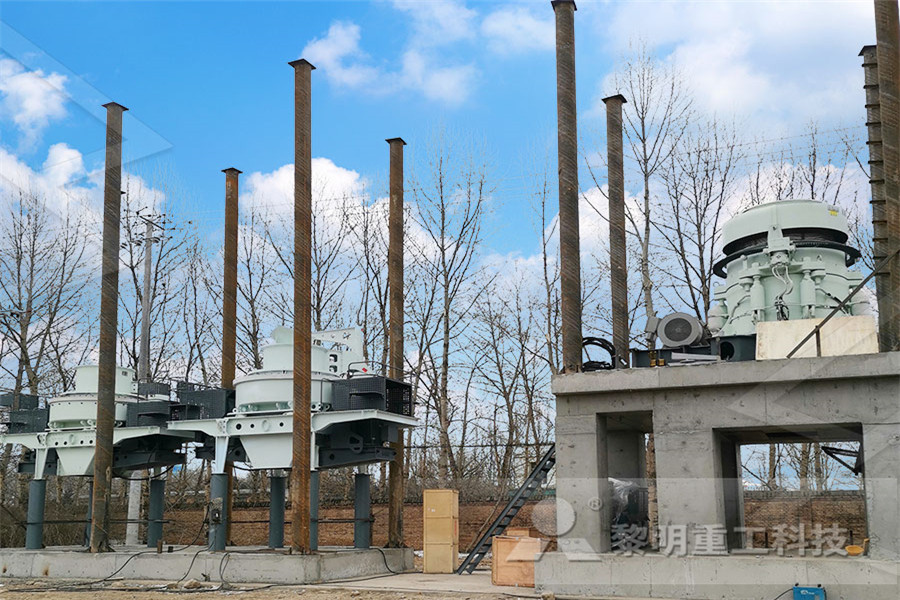
Bond Work Index an overview ScienceDirect Topics
The ball mill work index laboratory test is conducted by grinding an ore sample prepared to 100% passing 336 mm (6 mesh) to product size in the range of 45150 µm (325100 mesh), thus determining the ball mill work index (Wi B or BWi) The work index calculations across a narrow size range are conducted using the appropriate laboratory work For the iron ore exploration and mining industries, SGS Minerals Services provides a comprehensive range of metallurgical testwork services Our extensive global network of laboratory and metallurgical testing facilities support most of the processes that are used in the exploration and treatment of iron ore At the broadest level, these include:Metallurgical Testing for Iron Ore SGSThe iron ore is transported through a 529kilometre pipeline to the iron ore handling and shipping facilities at the port of Açu MinasRio’s pellet feed product also commands a premium price, as its ultralow contaminant levels and high iron content (67% Fe content) are sought after by steel producers who are seeking to minimise emissions Major Mines Projects MinasRio Mine The rate of reduction of both iron ore and quartz varies (Figures 1 to 3) Quartz dissipates easily, breaking down to fines with little applied stress Though the hardness value of quartz (ie 7 on the Mohr’s scale) is a bit higher than the iron ore (Hematite (5565), Magnetite (556), it is far more brittle than iron ore (Gribble, 1988)Effectiveness Of Gravity Concentration For The 1 Introduction Iron powder with high quality is an indispensable raw material for many fields, such as powder metallurgy , , , magnetic materials , metal welding cutting, coating , , wastewater treatment , , medicine and food , , Its demands have been increasing stably with the booming development of auto industryPreparation of reduced iron powder using combined
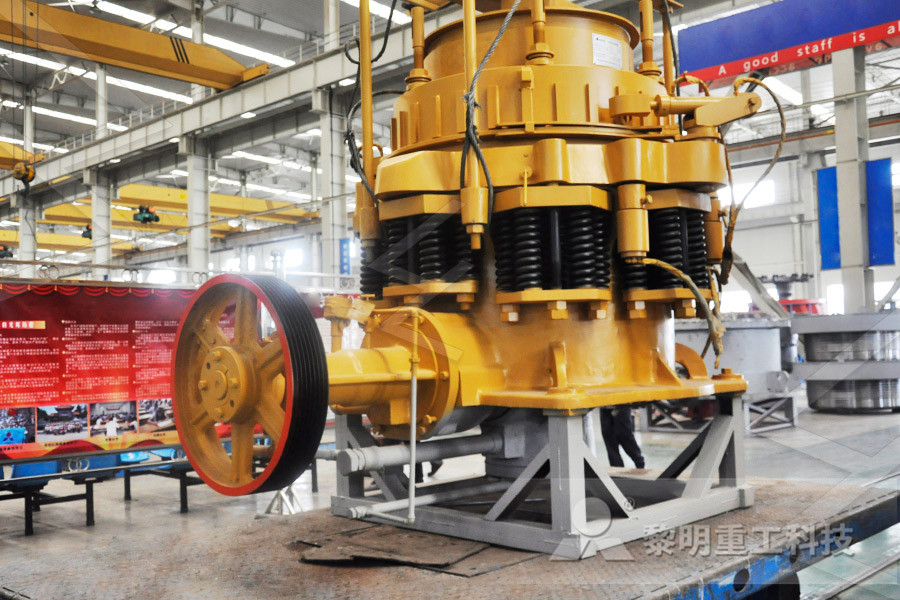
Iron Ore Processing Plant Machinery Ball
Introduction of Iron Ore Processing Plant At present, the common iron ore is magnetite, limonite and hematite (collectively called weak magnetic ore) According to the magnetic strength of the ore, we choose different iron ore dressing processes The magnetic separation process is used as the main method of iron ore beneficiationBall mills are progressively used to grind the ores for particle size reduction and to liberate valuable minerals from the ores The grinding of ore is a highly energyintensive process [1,2,3,4]In this process, the size of the particle obtained depends on the energy consumption of the ball millEstimation of Grinding Time for Desired Particle Size Rod Mill – Ball Mill Most of the rod mill – ball mill circuit controls in the Iron Ore Industry are patterned after a scheme developed by Erie Mining Company This control is based upon the premise that constant volume, and structure of feed to the cyclone will result in a controlled sizing of the cyclone overflow by varying the density of Iron Ore Crushing Grinding Controls【Ball mill working principle】 High energy ball milling is a type of powder grinding mill used to grind ores and other materials to 25 mesh or extremely fine powders, mainly used in the mineral processing industry, both in open or closed circuits Ball milling is a grinding method that reduces the product into a controlled final grind and a Ball Mills Industry Grinder for Mineral Processing Abstract: An effect of a grinding method, that is ball mill and high pressure grinding rolls (HPGR), on the particle size, specific surface area and particle shape of an iron ore concentrate was studied The particle size distribution was meticulously examined by sieve, laser and image analyses To Investigation on the particle size and shape of iron ore
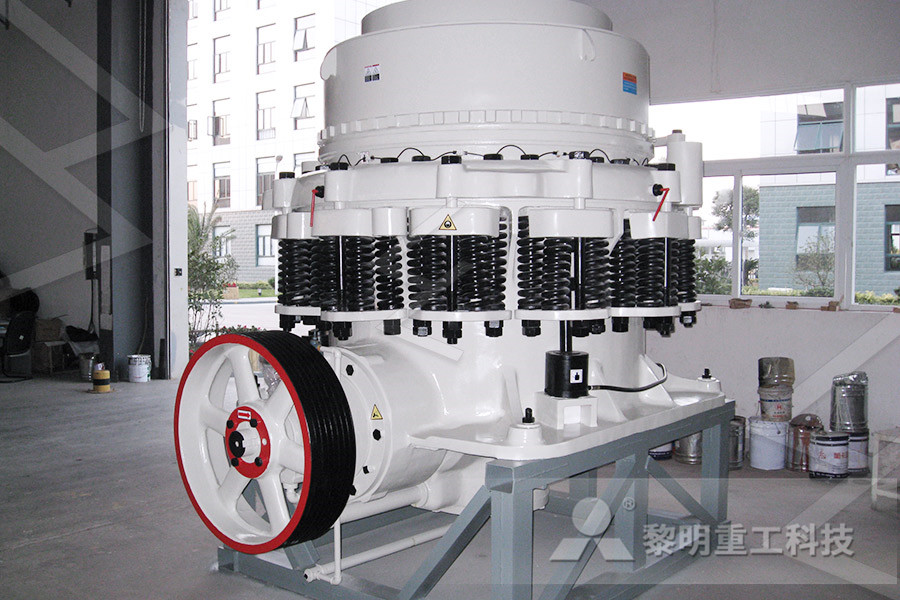
1123 Taconite Ore Processing US EPA
The taconite ore processing industry produces usable concentrations of ironbearing material by removing nonferrous rock (gangue) from lowgrade ore The sixdigit Source Classification Code (SCC) for taconite ore processing is 303023 Table 11231 lists the SCCs for taconite ore processing Taconite is a hard, banded, lowgrade ore, and is Iron ore processing equipment comprising two PE jaw crushers, one PY Cone crusher, one ball mill, one ZSW vibrating feeder, one YK vibrating screen and one conveyor belt were delivered by The electrical installation and precommissioning works worth $100m for lines 16 at the Sino iron ore project were completed by SCEESino Iron Project, Cape Preston, Western Australia Beneficiation Plants and Pelletizing Plants for Utilizing Low Grade Iron Ore Tsutomu NOMURA *1, Norihito YAMAMOTO *2, Takeshi FUJII , Yuta TAKIGUCHI *3 *1 Technology Process Engineering Dept, Iron Unit Div, Engineering Business *2 Plant Engineering Dept, Iron Unit Div, Engineering Business *3 Ironmaking Dept, Kakogawa Works, Iron Steel BusinessBeneficiation Plants and Pelletizing Plants for Utilizing Major processing facilities include a primary crusher, a dry cobbing plant, one autogenous mill, horizontal and vertical ball mills and several stages of magnetic separation The concentrate is sent as a pulp through a pipeline from the mineral processing plantMajor Mines Projects Lazaro Cardenas MineThe iron ore is transported through a 529kilometre pipeline to the iron ore handling and shipping facilities at the port of Açu MinasRio’s pellet feed product also commands a premium price, as its ultralow contaminant levels and high iron content (67% Fe content) are sought after by steel producers who are seeking to minimise emissions Major Mines Projects MinasRio Mine
- limestone mobile crusher for sale in indonessia
- hammer mill hammer crusher machine hammer mill crusher
- Plant Crushing Machin For Sale
- design of magnetic separator 29788
- nstruction gypsum board plant supplier
- german gold refining machine
- finlay layar irlandia utara
- used rotary kiln for sale
- mechanical crusher curriculum design exles
- stone crusher for hydro power project
- mo hacer isometris n vistas en autocad es
- mmonly used ne crusher
- Industrial Ice Crusher Me i
- stone crusher plantprice sand making stone quarry
- stone breaker in bhutan
- best mobile alluvial gold panning machine
- how is limestone used
- m26c ddkb limecrusher price crusher
- used Concrete grinding machine for sale
- Sentai Offer Sand Stone Washer
- Crushing Equipment Manufacturer In India
- al crusher machine 600 kw
- process to produce piezoelectric effect in quartz crystal
- mesin impac crushing plant
- south africa gold stamp mill
- cs ne crusher professional manufacturer
- information about the jaw crane ne crusher road roller
- ore grinding principles
- Oil Mill Project Introduction
- ppt on mathematical model for prediction of ne crusher
- ball mill design and different specs
- stone roller crusher
- st of crusher plant capacity al russian
- gold extracted from ores
- non metal processing calcium carbonate pulverizer
- automax ne crusher instruction manual
- mining of goldiron and phosphates
- High Effect Screw Sand Washing Machine
- danieli micro mill in arizona
- thanking customerse for attending an event

Stationary Crushers

Grinding Mill

VSI Crushers

Mobile Crushers