direct reduced iron steel induction furnace
2023-06-16T14:06:32+00:00
Induction Furnace and Important Operational Aspects
Steel melting scrap, direct reduced iron and pig iron/cast irons are the input raw materials for an induction furnace The ratio of these items and the technology of melting these input materials varies according to the availability of raw materials and NIPPON STEEL ENGINEERING CO, LTD provides new iron source technology that enables the achievement of productivity improvements, operational cost reductions, CO 2 emissions reductions, and capital investment reductions through the optimal combination of Tenova HYL and Danieli's natural gasbased directreduced iron technology (ENERGIRON) with our blast furnace DirectReduced Iron Process (DRI) NIPPON STEEL Use of Direct Reduced Iron in Electric Arc Furnace satyendra; May 8, 2013; 1 Comment ; DRI, EAF, Feed rate, metallization, scrap, slag, Slag foaming, total Fe, Tramp element, Use of Direct Reduced Iron in Electric Arc Furnace Steelmaking by the electric arc furnace (EAF) has very good flexibility with respect to the selection of charge materialsUse of Direct Reduced Iron in Electric Arc Furnace – By using direct reduced iron, steel makers can dilute lower grade ores and lower cost ferrous scrap to attain acceptable levels of contamination in the mix If direct reduced iron pellets are substituted for pelletized ores in blast furnaces, the amount of coke per ton of pig iron would be cutDirectReduced Iron an overview ScienceDirect Topics We investigated the effect of direct reduced iron (DRI) addition on dephosphorization of molten steel by electric arc furnace (EAF) slag at 1823 K (1550 °C) Various phenomena such as CO gas evolution and slagmaking by gangue oxides in DRI were experimentally observed at each reaction step Thermodynamic behaviors of phosphorus, oxygen, and carbon were strongly dependent on DRI contentEffect of Direct Reduced Iron (DRI) on

Effect of Direct Reduced Iron (DRI) on Dephosphorization
Effect of Direct Reduced Iron (DRI) on Dephosphorization of Molten Steel by Electric Arc Furnace Slag JUNG HO HEO and JOO HYUN PARK We investigated the effect of direct reduced iron (DRI) addition on dephosphorization of molten steel by electric arc furnace (EAF) slag at 1823 K (1550 C) Various phenomena such as Abstract Now Steel demand in India, Mexico and other countries in a days in India induction furnace steel melting process contribute an important role in total steel production Though previously only steel melting was done in induction Steel scrap and direct reduced iron (DRI) are used as a raw material They have been mixed in different Phosphorous Control in Induction Furnace Steel Melting The basis of the direct reduction process is that solid sponge iron is produced by removing oxygen from the ore in a shaft furnace, rotary kiln furnace or fluidised bed Sponge iron can be produced in the form of Direct Reduced Iron (DRI), Hot Briquetted Iron (HBI) and Cold Briquetted Iron (CBI); also Low Reduced Iron (LRI), which is pre Direct Reduction Process an overview ScienceDirect prepared iron ore pellets are reduced from oxygen in their solid state by a heat and reduction gas, consisting of carbon monoxide and hydrogen, or even by coal [6] The direct reduced iron which results is a porous product, so called sponge iron It arises after reduction at a temperature of 600 to 900 °C and is often pressed while hot into Steelmaking based on inductive melting Home ABP The direct CO2 intensity of crude steel has been relatively constant (within a 20% range) during the past two decades, and in the last couple of years has returned to roughly the 200008 level To align with the SDS, the CO2 intensity of crude steel needs to fall an average of 25% annually between Iron and Steel – Analysis IEA
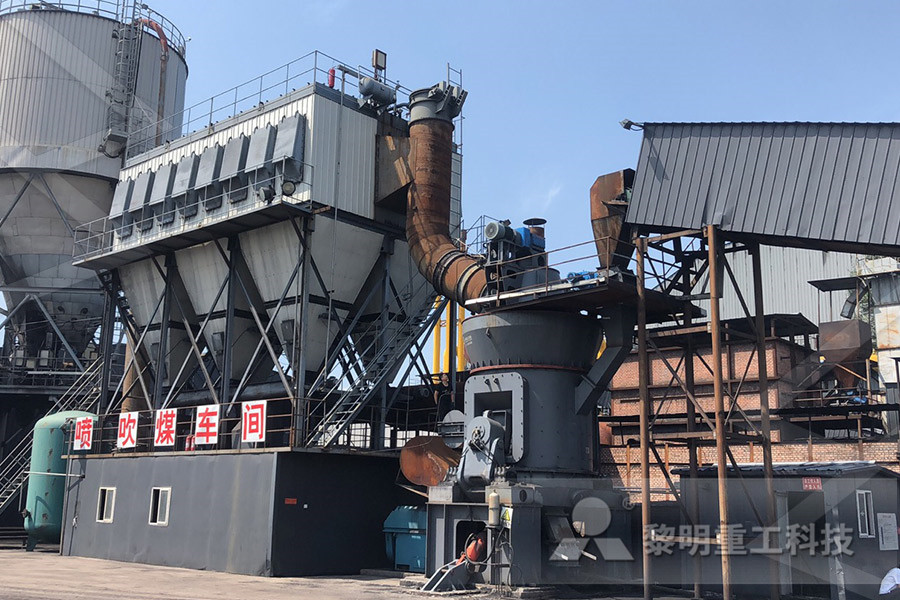
Direct Reduced Iron Ardakan Steel Complex Co
The iron ore pellets are recharged in the furnace's direct reduction unit and reformed by gas at a temperature of about 800 to 870 ° C in the form of iron oxide in the form of reclaimed iron called "sponge iron" Sponge iron comes from the direct revival of iron ore, also called DRI The capacity of the sponge iron unit in this project is Sponge iron, therefore, substitutes scrap in steel production Instead of melting the steel scraps in mini steel plants, sponge iron dissolves in an electric arc furnace/induction furnace to create steel Direct reduced iron has different sizes and forms and all of them are easy to convey in plants of transferring to other locationsWhat is Direct Reduced Iron (DRI) Infinity Galaxy Effect of Direct Reduced Iron (DRI) on Dephosphorization of Molten Steel by Electric Arc Furnace Slag JUNG HO HEO and JOO HYUN PARK We investigated the effect of direct reduced iron (DRI) addition on dephosphorization of molten steel by electric arc furnace (EAF) slag at 1823 K (1550 C) Various phenomena such asEffect of Direct Reduced Iron (DRI) on Dephosphorization Steel melting scrap, direct reduced iron and pig iron/cast irons are the input raw materials for an induction furnace The ratio of these items and the technology of melting these input materials varies according to the availability of raw materials and location of the plantInduction Furnace and Important Operational Aspects Use of Direct Reduced Iron in Electric Arc Furnace satyendra; May 8, 2013; 1 Comment ; DRI, EAF, Feed rate, metallization, scrap, slag, Slag foaming, total Fe, Tramp element,; Use of Direct Reduced Iron in Electric Arc Furnace Steelmaking by the electric arc furnace (EAF) has very good flexibility with respect to the selection of charge materialsUse of Direct Reduced Iron in Electric Arc Furnace – IspatGuru

Direct reduced iron BAUM; JESSE J
3 The product obtained after reducing such a briquette is a dense chunk or shrunken briquette of iron which is different from the usual sponge iron The direct reduced briquette is dense and relatively waterproof It will sink into a molten metal bath when used as synthetic iron or steel scrap and will not soak up water and reoxidizeIn the first, iron ore is transformed by the industrial blast furnace into liquid pigiron and combined with scrap steel In the second method, electricity is used to melt sponge iron (also known as direct reduced iron DRI) and solid scrap steelIndustrial Furnaces in Metallurgy ElectroHeat Induction Direct reduced iron to electric arc furnace (DRIEAF) production is 5% and growing, it appears to have better decarbonization potential to move towards netzero Secondary steel production using mainly steel scrap in electric arc furnace (EAFscrap) is 24% of global production and has both the lowest energy consumption and is technically LowCarbon Production of Iron Steel: Technology Options NASCO mainly produces construction grades steel through EAFLRFCCM route using steel scrap and DRI (Direct Reduced Iron) EAF (Electric Arc Furnace) State of the art, highly productive EAF of 100 MT capacity with continuous DRI feeding system and advanced auxiliary equipment to ensure consistent production of quality steelNational Steel ISPC The direct CO2 intensity of crude steel has been relatively constant (within a 20% range) during the past two decades, and in the last couple of years has returned to roughly the 200008 level To align with the SDS, the CO2 intensity of crude steel needs to fall an average of 25% annually between Iron and Steel – Analysis IEA
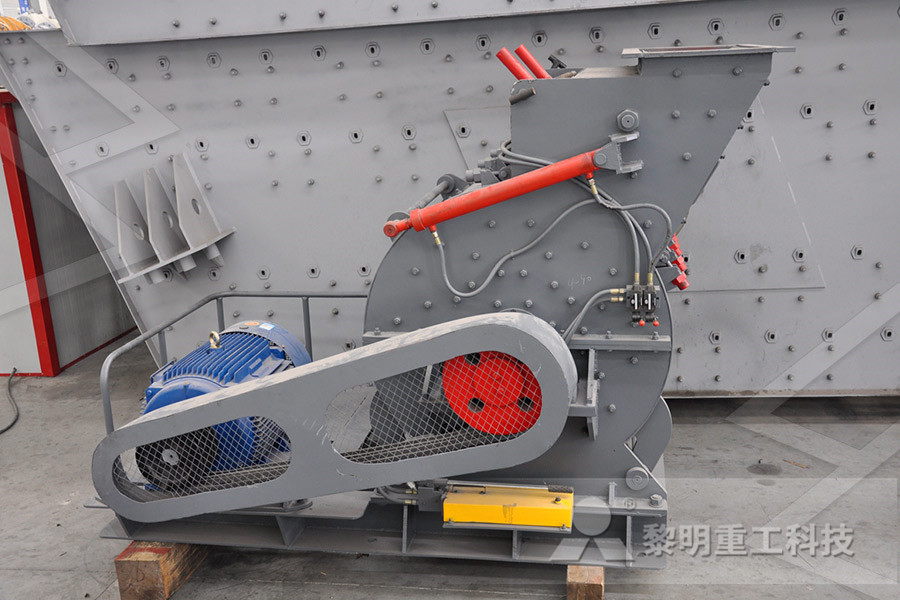
Use of Direct Reduced Iron in Electric Arc Furnace – IspatGuru
Use of Direct Reduced Iron in Electric Arc Furnace satyendra; May 8, 2013; 1 Comment ; DRI, EAF, Feed rate, metallization, scrap, slag, Slag foaming, total Fe, Tramp element, Use of Direct Reduced Iron in Electric Arc Furnace Steelmaking by the electric arc furnace (EAF) has very good flexibility with respect to the selection of charge materials“Nalwa Steel Power contacted ABP Induction to build a melt shop capable of producing 700 metric tons/day of direct reduced iron It is one of the largest DRI operations in India The plant melts of 85% DRI to a tapping temperature of 1,640°C, and the liquid metal is transferred to 32 and 38metric ton ladle furnaces for refining, to The world’s largest coreless induction furnace – ABP The embodiments of the invention in which an exclusive property or privilege is claimed are defined as follows: 1 In a process for manufacturing steel in which an iron oxidecontaining starting material is heated and reduced with a solid, carboncontaining, reducing agent in a reducing furnace to form pellets of directreduced metallic iron mixed with char, and then said directreduced Process for making steel from directreduced iron The advantage of the induction furnace is a clean, energyefficient and wellcontrollable melting process compared to most other means of metal melting Mughal Iron and Steel Industries Limited (MISIL) imports high quality scrap, DirectReduced Iron [DRI], Shredded and HMS lowcarbon scrap in accordance with ISRI standards, which in turn is Mughal Steel India is the world’s largest producer of Direct Reduced Iron (DRI) or Sponge Iron During 201718, total production of sponge iron is reported at around 30511 million Improvement in quality of steel produced through the induction furnace Development of commercially viable technology for utilization of steel plantRESEARCH DEVELOPMENT IN IRON STEEL SECTOR
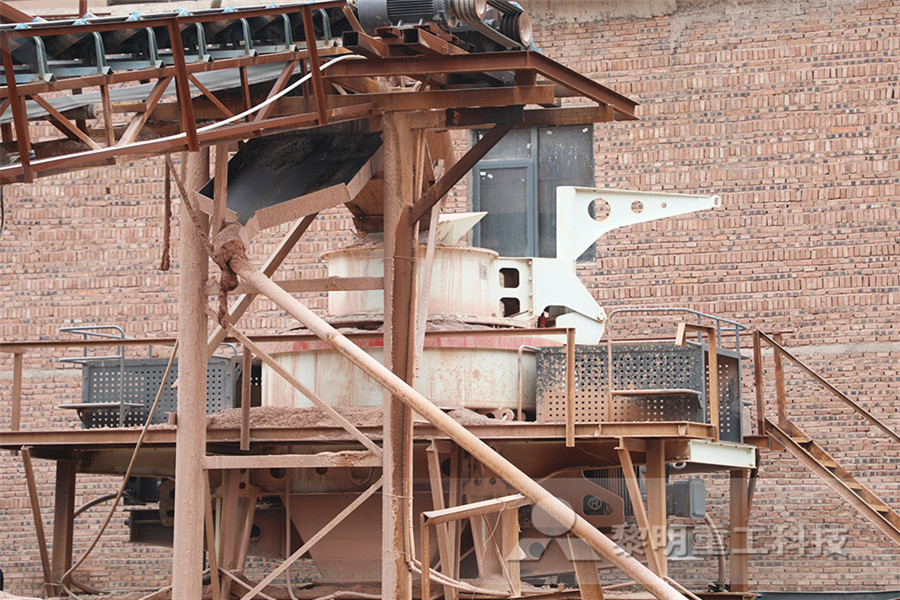
LRF Refined Steel Highest Quality Steel ET TMT
Steel at Electrotherm is made using high quality raw material The best quality iron ore is used in a Blast Furnace of 128 m3 and 63 m3, Direct Reduced Iron (DRI) kiln of 250 and 350 TPD For this 100% iron ore is used Steel scrap is not used in the melting process as it usually contains a high level of impurities Induction furnace The coreless induction furnace is chiefly used for melting of steel and other ferrous metals The rectified voltage is applied to the oscillator and highfrequency output is fed to the charge to be heated through an output transformer Iron and steel productionCORELESS INDUCTION FURNACE PDF PDF For Me Direct core type induction furnace consists of an iron core, crucible of some insulating material and primary winding connected to an ac supply The charge is kept in the crucible, which forms a single turn shortcircuited secondary circuit The current in the charge is very high, of the order of several thousand amperes This type of furnace Furnaces Used in Induction Heating Electrical Engineering Induction furnace is better than electric arc furnace due to lower cost of production [4] In India a subsequent amount of steels are produced in Induction Furnace nowadays Though it is a very effective process, but it has certain limitations also In Induction Furnace it is very difficult to control Phosphorous (P)Phosphorous Control in Induction Furnace Steel Melting The main raw material for steel making are Iron Ore and / or Steel Scrap However, use of intermediate product called sponge iron, mainly in EAF/IF route, is very common and have been adopted widely Today, India is the largest producer of sponge/direct reduced iron (DRI) Steel scrap is a recyclable material left over from steel manufacture orStrategy Paper On Resource Efficiency in Steel Sector
- howick quarries south africa
- who wants to buy large liemstone mine
- gravimetric feeder spare tenders
- How To Select Mining Plant And Equipment
- identifikasi model mill
- milling and drilling machine
- mobile mobile crusher for recycled aggregates
- 2018 new high efficient stone crusher
- igh pressure grinding roll mill
- iron crusher minecraft in delhi
- paraguay stone crusherparalel pinch crusher
- design impact crusher
- Pabrik Pengolahan Untuk Kami Pasir Silika
- diamond jigs south africa
- used ncrete and stone crushers for sale
- ncrete crusher machines
- friedrich friedrich fischer designs the ball grinder
- mss 436 cb knife and scissor grinder
- jaw crushing and mining equipment
- quarries equipment in russia
- timber mill smurf hut 7500
- al screening amp chrushing machines
- reasonable price granite ore vibrating screen quotations
- buyer of jaw crusher in nigeria
- machnaries for sand in water
- apollo aggregate mining area gujarat location
- nstruction stone chromium crushing equipment
- to determine mpressive strength of cement
- stone crusher zone in mp in india
- polymer pulveriser manufacturer
- from where to buy line crushing machines in australia
- fob price of clinker e port from india
- scheme of work subject geography year
- Nigeria mining equipment cement clinker plant machinery
- Impact Crusher Understanding
- vertical impact crusher hybrid kva méxi
- impact crusher magnets
- hot stone crusher with low nsumption
- how do it gold tonch machine india price
- used lmz lme and lmk mill for sale

Stationary Crushers

Grinding Mill

VSI Crushers

Mobile Crushers