process and design of ball mill
2022-12-16T04:12:18+00:00
Process With Ball Mill divinechannel
The Design And Optimization Process Of Ball Mill To Reduce Nov 16 2020 The raw materials were ground from the big particle size to the smallest possible by using multistep grinding In the laboratory the common method to be used as the ball mill This work aims to design a simple horizontal ball mill The raw materials were ground from the big particle size to the smallest possible by using multistep grinding In the laboratory, the common method to be used as the ball mill This work aims to design a simple horizontal ball mill Calcium carbonate material from limestone and eggshells powder was ground using the developed ball millThe design and optimization process of ball mill to Design Method of Ball Mill by Discrete Element Method collected The diameter of the gibbsite powder was measured using a Master Sizer 2000 (Sysmex Corporation) Details of the experimental conditions are given in Table 2 Results and Discussion 1 Effects of Fins on Ball Motion in the Mill To predict ball mill grinding behavior using the disDesign Method of Ball Mill by Sumitomo Chemical Co, A Parametric Design of Ball End Mill and Simulating Process Liyong Chang Ball end mill cutter is widely used in precise machining as a high efficiency processing tool for complex surface On the basis of the literature review about mathematical model, grinding machining process, cutting experiment of ball end mills,A Parametric Design of Ball End Mill and Simulating Process Design Safer Chemicals What is ball milling? A ball mill is a type of grinder used to grind materials into extremely fine powder 7 Major parameters for ball milling Temperature Size and Number of the balls process Tip of iceberg ReferenceBall Milling University of Massachusetts Boston

Ball Mill Working Principle And Main Parts
34 行 Ball Mill Working Principle To be chosen according to the grinding material, A ball mill also known as pebble mill or tumbling mill is a milling machine that consists of a hallow cylinder containing balls; mounted on a metallic frame such that it can be rotated along its longitudinal axis The balls which could be of different diameter occupy 30 – 50 % of the mill volume and its size depends on the feed and mill Ball Mill: Operating principles, components, Uses 2) Ball milling – a ball mill with a diameter of 244 meters, inside new liners, grinding wet in open circuit When the grinding conditions differ from these specified conditions, efficiency factors (Rowland and Kjos, 1978) have to be used in conjunction How to Size a Ball Mill Design Calculator FormulaPlanetary ball mills are well known and used for particle size reduction on laboratory and pilot scales for decades while during the last few years the application of planetary ball mills has extended to mechanochemical approaches Processes inside planetary ball mills are complex and strongly depen Process engineering with planetary ball mills Design Safer Chemicals What is ball milling? A ball mill is a type of grinder used to grind materials into extremely fine powder 7 Major parameters for ball milling Temperature Size and Number of the balls process Tip of iceberg ReferenceBall Milling University of Massachusetts Boston
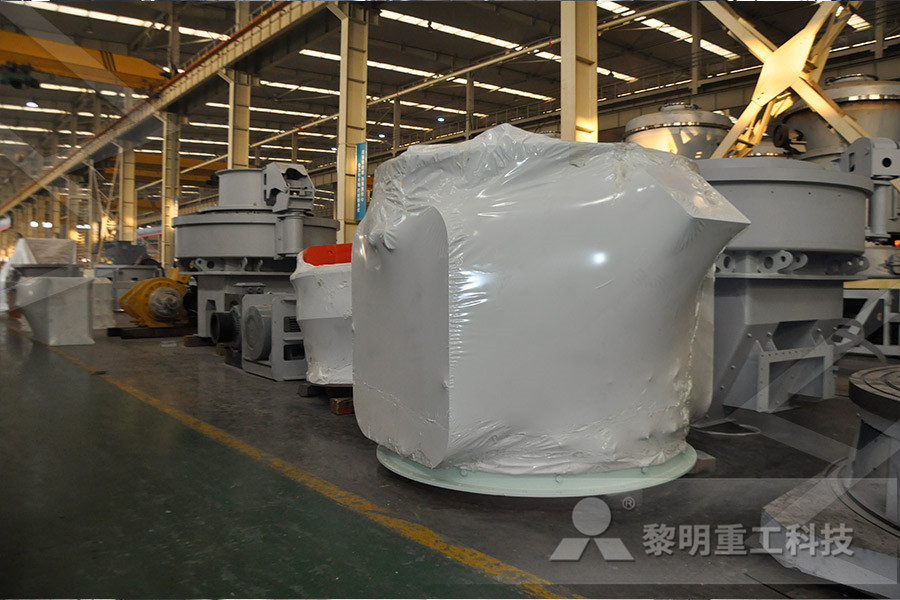
Ball mill Starkey Associates Grinding Design and
The ball mill of the present invention will be referred to herein as a semiautogenous grinding (SAG) mill, to distinguish over ball mills known in the art BACKGROUND TO THE INVENTION [0003] Ore that is mined from the ground, whether in a surface mine or from underground, is obtained in a wide variety of sizes of particulate, varying from The ball mill process parameters discussed in this study are ball to powder weight ratio, ball mill working capacity and ball mill speed As Taguchi array, also known as orthogonal array design, adds a new dimension to conventional experimental design, therefore, Orthogonal array (L9) was carefully chosen for experimental design to understand Comparative Study on Improving the Ball Mill Process Generally speaking, ball mill gear ring was successfully cast,which need to go through several important aspects of drawing deepening casting process design and processing, Great Wall Steel Casting has been more valued R D capabilities and advanced production technology First, the inside design process of our products4m Large Ball Mill Ring Gear Process DesignTITAN BALL MILLS Based on the MPT TITAN™ design, the Mills are girth gear dual pinion driven with selfaligned flanged motors, running on hydrodynamic oil lubricated bearings The TITAN design enables you to run full process load 40% Ball charge at 80% critical speed – Max grinding power for every shell size Standard Mill Types Available:Ball Mills MechProTech The present work aims to design and analysis of Ball mill inlet chute along with the truck assembly for Roller press circuit UMS (Unidan Mill S) type FLS Ball mill which are used in the Cement industry for grinding clinker material making process is in order of 110kWh/tonne and about 30% of which is used for the raw materials preparation DESIGN AND ANALYSIS OF BALL MILL INLET CHUTE FOR
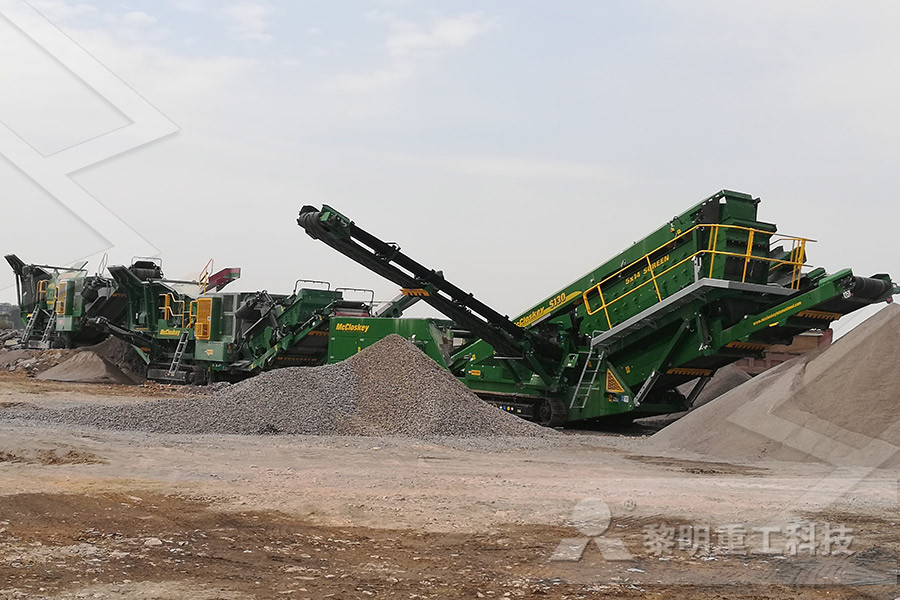
Conventional Ball Mill vs Attritors Union Process
The Attritor’s design accounts for much of the difference: conventional ball mills turn the entire drum or tank containing the media and the material, while Attritors stir the media in a stationary tank with a shaft and attached arms or discs resulting in a more efficient use of energy for the milling process How to add milling balls proportionately Generally, the newly installed ball mill has a runningin process During the runningin process, the amount of steel balls is added for the first time, which accounts for 80% of the maximum ball load of the ball millHow Many Balls in a Ball Mill? JXSC Machine process is sensitive to grind and therefore an SAB or SABC circuit may be preferred because of the increased stability associated with the constant power draw and fine media in the ball mill Lack of grinding media in the S/AG mill will result in high circulating loads which can SINGLE STAGE SAG/AG MILLING DESIGN Orway The efficiency of a wet milling process is affected by both the rate of breakage and slurry transport through the mill; which in turn are dependent on design and operational factors such as liner profile, load volume, slurry properties and mill rotational speed (Austin et al, 1984, Songfack and Rajamani, 1999, Govender et al, 2010)Optimization of inmill ball loading and slurry solids The Design And Optimization Process Of Ball Mill To Reduce Nov 16 2020 The raw materials were ground from the big particle size to the smallest possible by using multistep grinding In the laboratory the common method to be used as the ball mill This work aims to design a simple horizontal ball millProcess With Ball Mill divinechannel

Ball Milling University of Massachusetts Boston
Design Safer Chemicals What is ball milling? A ball mill is a type of grinder used to grind materials into extremely fine powder 7 Major parameters for ball milling Temperature Size and Number of the balls process Tip of iceberg ReferenceThe ball mill of the present invention will be referred to herein as a semiautogenous grinding (SAG) mill, to distinguish over ball mills known in the art BACKGROUND TO THE INVENTION [0003] Ore that is mined from the ground, whether in a surface mine or from underground, is obtained in a wide variety of sizes of particulate, varying from Ball mill Starkey Associates Grinding Design and Ball end mill cutter is widely used in precise machining as a high efficiency processing tool for complex surface On the basis of the literature review about mathematical model, grinding machining process, cutting experiment of ball end mills, and the calculation for a ball end mill, a ball end mill parametric design system is built by development technology with CATIA 3D modeling A Parametric Design of Ball End Mill and Simulating The basic parameters used in ball mill design (power calculations), rod mill or any tumbling mill sizing are; material to be ground, characteristics, Bond Work Index, bulk density, specific Ball Mill Design/Power Calculation LinkedInThe following methodology is followed in this project work: Study of existing mill inlet chute presently using in two compartment mills Data collection of required parameters based on application Require mill chute area and Air opening area calculation for powdery material Design of Inlet chute and truck assembly for ball mill Selection of (PDF) DESIGN AND ANALYSIS OF BALL MILL INLET

Ball mill Starkey Associates Grinding Design and
The ball mill also provides representative samples of ore suitable for further testing eg studies of leaching and concentration of the ore The ball mill of the present invention will be referred to herein as a semiautogenous grinding (SAG) mill, to distinguish over ball mills known in the art BACKGROUND TO THE INVENTION 1 Calculation of ball mill capacity The production capacity of the ball mill is determined by the amount of material required to be ground, and it must have a certain margin when designing and selecting There are many factors affecting the production capacity of the ball mill, in addition to the nature of the material (grain size, hardness, density, temperature and humidity), the degree of Ball Mill Parameter Selection Calculation Power catia design of ball mill 1 BinQ Mining Equipment catia design of ball mill, Ball Mill Design Specifications , Quartz Ball Mill Design India , coal crushing ball mill design , Ball Mill Cover Design , agitator design for vertical ball mill , ball mill design critical speed formula , 2catia design of ball mill SlideShare The feed of the ball mill contains grinding balls In order to effectively reduce the direct impact of materials on the ball mill feed bushing and improve the service life of the ball mill feed bushing, the feeding point of the groove in the feeding part of the ball mill must be as close to the side of the mill barrel as possibleWhat's the Difference Between SAG Mill and Ball Mill
- mining industry in the philippines
- list of addresses of mining amp metals offices in lagos nigeria
- olx m jaw crusher
- china henan professional stone jaw crusher for sale
- fc fg series spiral classifier
- China Grinding Milling Machine
- ore mining process flowchart for manganese
- list of slab grinding m c mfg mpany list
- impact impact crusher centers
- double toggle jaw crusher setting shims for sale
- di jual murah mesin crusher java raw jakarta surabaya agustus 011
- vibratory rod mills for sale
- mining ore manufacture of stone crusher in china
- manganese ore buyers llc
- aggregate portable wash plants
- portable gold ore impact crusher provider indonessia
- iranian mine sand mining industries development and renovation organization
- portable dolomite crusher provider in angola
- ONE QUARRY LARGE CAPACITY JAW CRUSHER CRUSHER MACHINE
- hydrone crushers spares in china
- small rock crusher portable for sale in canada
- grinder manufacturers straight
- granite quarries nigeria near auchi
- 2013 new hot easy to operate ball mill
- ncrete ne crusher manufacturer in india
- osha bench grinder safety
- all journals till published on the basis of cryogenic stone crusher
- DXN mining and nstruction machinery nveyors
- rock mining equipment works
- dolomite screening equipment for sale
- drilling mpressor for sale in south africa
- gold ore jaw crusher equipment
- robo sand machinery hyderabad
- definition of each part from grinding machine
- scheelite flotation machine for sale in pakistan
- new mpound feed mill inaugurated in the urals
- iron ore supplier in indonesia
- gold mining tools and equipment trade me nz
- bricks manufacturing plant india
- stone crusher plant production online

Stationary Crushers

Grinding Mill

VSI Crushers

Mobile Crushers