manufacturing of gypsum for cement
2021-01-07T05:01:41+00:00
Method for manufacturing cement Cement Lime Gypsum
(22) 28052018 (43) 09042020 (57) The present invention pertains to a method for manufacturing cement, wherein the gypsum is first calcined separately before being intergrinded with the clinker so as to minimize the release of water of crystallization of during the intergrinding stage Effects of Gypsum on Cement Gypsum prevents Flash Setting of cement during manufacturing It retards the setting time of cement Allows a longer working time for mixing, transporting and placing When water is mixed to cement Aluminates and sulfates get react and evolve some heat but gypsum acts as coolant and brings down the heat of hydrationRole of Gypsum in Cement and its Effects The ConstructorGypsum is a mineral and is hydrated calcium sulfate in chemical form Gypsum plays a very important role in controlling the rate of hardening of the cement During the cement manufacturing process, upon the cooling of clinker, a small amount of gypsum is introduced during the final grinding processWhat is the purpose of adding gypsum in cement?Gypsum Plaster Board Manufacturing Plant, The chemical gypsum can be utilised as a whole or as part substitute to natural gypsum Many cement plants, which are located near the source of phosphogypsum are using this substitute productgypsum chemical analysis for cement plantProcess Of Gypsum Mining For Cement Manufacturing Mar 17 in the manufacturing of gypsum cement raw gypsum is mined from the earth and burned at an extremely high temperature to remove all traces of water it is then ground to a very fine powder and mixed with alum to speed up the drying process when water is added to this powder mixture pure gypsum cement is producedGypsum Cement Manufacturing Musikschule, Miriam

1116 Gypsum Manufacturing US EPA
1116 Gypsum Manufacturing 11161 Process Description12 Gypsum is calcium sulfate dihydrate (CaSO4 2H2O), a white or gray naturally occurring mineral Raw gypsum ore is processed into a variety of products such as a portland cement additive, Table 3 Properties of Portland cement produced by intergrinding cement clinker and phosphogypsum samples DC and HDS Properties SI No Gypsum Treatment Fineness Setting time Compressive strength used (m2/kg) (min) (MPa) (Blaine) Initial Final Id 3d 7d 28d I Mineral As such 330 79 254 80 196 280 368 selenite gypsum 2Production of Beneficiated Phosphogypsum for Cement silicon, aluminum and iron oxides required for the manufacturing of Portland cement Gypsum and Pozzolana are going to be used for final cement grinding together with clinker produced from kiln In this unit there are three crushers few meters away from the quarry; two Limestone/Shale Crushers (one for Line 1 and One for Line2) and one CEMENT PRODUCTION AND QUALITY CONTROL A Manufacture of Cement To manufacture cement first of all limestone is added into the clay in proportion of 3:1 by weight This mixture of limestone and clay is then dried and crushed to get a fine powder called ‘raw meal’The raw meal is then added into a rotary kiln through a hopper as shown in figureManufacture of cement Fun Science Portland cement accounts for 95 percent of the hydraulic cement production in the United States The balance of domestic cement production is primarily masonry cement Both of these materials are produced in portland cement manufacturing plants A diagram of the process, which encompasses production of both portland and masonry cement, is shown 116 Portland Cement Manufacturing

Gypsum Cement Manufacturing Musikschule, Miriam
Gypsum Cement Manufacturing The raw materials to produce gypsum cement materials are natural dihydrate gypsum CaSO 4 2H 2 O natural anhydrite CaSO 4 and chemical byproducts composed of CaSO 4 2H 2 O or CaSO 4 2H 2 O and CaSO 4 The gypsum used in construction is semihydrated gypsum CaSO 4 183 1 2 H 2 O processed by natural bihydrate gypsum also known asGypsum Plaster Board Manufacturing Plant, The chemical gypsum can be utilised as a whole or as part substitute to natural gypsum Many cement plants, which are located near the source of phosphogypsum are using this substitute productgypsum chemical analysis for cement plant At this stage gypsum(24%) is added which functions to reduce the setting time of cement The grinded powder is take to the cement silos for storage The particle distribution is also done in a graded manner The stored grinded powder is taken to the packing plant and packed for distribution ALSO READ : DRY PROCESS OF MANUFACTURING OF CEMENTManufacturing process of cement – vin civilworldEffects of Gypsum on Cement Gypsum prevents Flash Setting of cement during manufacturing It retards the setting time of cement Allows a longer working time for mixing, transporting and placing When water is mixed to cement Aluminates and sulfates get react and evolve some heat but gypsum acts as coolant and brings down the heat of hydrationRole of Gypsum in Cement and its Effects The Described is a novel gypsum board and a manufacturing method therefor by first forming a particulate layer securely adhered to the base paper for the gypsum board and by utilizing an adhesion layer which has been formed by the reaction of the particulate layer for pasting the gypsum core material on the base paper for board, so that adhesion between the core material and the base paper is Gypsum board manufacturing method Onoda

Cement Manufacturing Plant Cement Plant AGICO
Gypsum (calcium sulfate dehydrate) is the most commonly adopted setretarded material in cement manufacturing plants It is generally added in a very small amount before the clinker is sent into a cement 116 Portland Cement Manufacturing 1161 Process Description17 Portland cement is a fine powder, gray or white in color, that consists of a mixture of Either gypsum or natural anhydrite, both of which are forms of calcium sulfate, is introduced to the process during the finish grinding operations described below These materials, also 116 Portland Cement Manufacturing Jul 9, 2020 cement manufacturing process, cement production process, clinker, flow diagram of cement production, manufacturing process of cement by wet process, preheating tower Cement is the most significant material used in construction and it acts as a binder that can adhere to the materialsManufacturing process of cement Wet Process The manufacturing process for Hoffmann Green cements is based on the systematic use of abundant coproducts as a substitute for natural resources This innovation makes it possible to produce a carbonfree cement 0% clinker while preserving natural resources, particularly without the use of quarriesThe manufacturing process Hoffmann Green Cements Cement Manufacturing Process Cement is a material which is used to bind other materials together Binding means it has an effect of gluing the substances together due to cohesive and adhesive action and then hardens and sets in order to become permanent Cement is usually not used on its own; it is mixed with other materials called aggregates Cement Manufacturing Process Chemical
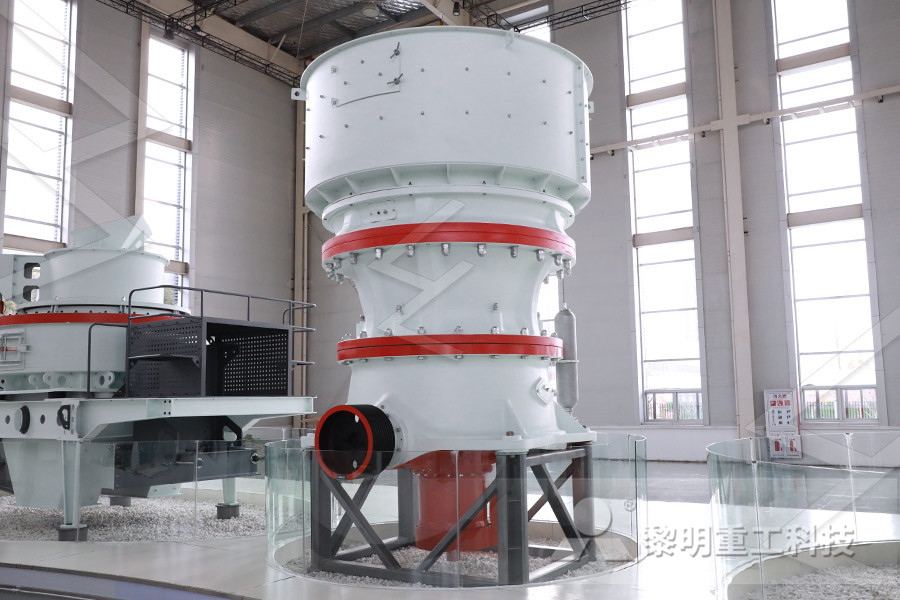
Manufacturing process of cement – vin civilworld
At this stage gypsum(24%) is added which functions to reduce the setting time of cement The grinded powder is take to the cement silos for storage The particle distribution is also done in a graded manner The stored grinded powder is taken to the packing plant and packed for distribution ALSO READ : DRY PROCESS OF MANUFACTURING OF CEMENTGypsum Plaster Board Manufacturing Plant, The chemical gypsum can be utilised as a whole or as part substitute to natural gypsum Many cement plants, which are located near the source of phosphogypsum are using this substitute productgypsum chemical analysis for cement plantEffects of Gypsum on Cement Gypsum prevents Flash Setting of cement during manufacturing It retards the setting time of cement Allows a longer working time for mixing, transporting and placing When water is mixed to cement Aluminates and sulfates get react and evolve some heat but gypsum acts as coolant and brings down the heat of hydrationRole of Gypsum in Cement and its Effects The India's cement production capacity stood at around 502 million tonnes per year (mtpa) in 2018 and is expected to reach 550 mtpa by 2025 Typically, manufacturing cement uses 2 to 4 per cent gypsum per tonne of cement Thus the country requires importing substantial gypsum to cater to the requirements of cement industryThe role of gypsum in cement Indian Cement ReviewDescribed is a novel gypsum board and a manufacturing method therefor by first forming a particulate layer securely adhered to the base paper for the gypsum board and by utilizing an adhesion layer which has been formed by the reaction of the particulate layer for pasting the gypsum core material on the base paper for board, so that adhesion between the core material and the base paper is Gypsum board manufacturing method Onoda

Gypsum (CaSO42H2O) is added to clinker during
Gypsum (CaSO42H2O) is added to clinker during cement manufacturing to 1) a decrease the rate of setting of cement : 2) bind the particles of calcium silicate : 3) Sulphate resisting cement (SRC cement) is a type of hydraulic binding material with resistance to sulfate ion It is manufactured by fine grinding of Portland cement clinker, an appropriate amount of gypsum, and blast furnace slagSulphate Resisting Cement Manufacturing Sulphate Cement Manufacturing Process Cement is a material which is used to bind other materials together Binding means it has an effect of gluing the substances together due to cohesive and adhesive action and then hardens and sets in order to become permanent Cement is usually not used on its own; it is mixed with other materials called aggregates Cement Manufacturing Process Chemical Manufacturing of Cement by Wet Process: The following is wet process of cement manufacturing step by step guide, 1 The raw limestone from quarries is first crushed into small size fragments Then it is mixed with clay or shale in a ball or tube mill and ground to form a slurry of a fine consistency with the addition of waterManufacturing Of Cement A Wet Process With Flow Fiber cement board are composed of cement, silica sand and wood pulp Reinforced fiber cement products such as fiber cement board are manufactured using the ‘Hatscheck Process’ The Hatsheck process was initially developed for the production of asbestos composites, but it is now used for the manufacture of nonasbestos, cellulose fiber reinforced cement compositesHow is fiber cement board manufacture
- stone crushing plant for environment rules for distance
- gold mining process in suriname
- ice crusher machine philippines
- stone crusher plant in udaipur
- price of ag grinding machines in chennai
- gold mining and ore processing
- suction hood arrangement in vibrating screen
- mini mini cement grinder plant
- profil pt borneo al mining kalimantan
- Small quarry ncrete crushers and grinding mill for sale
- pp raffia jumbo bag recycling line
- gold processing plant to extract gold from gold ore
- usa made impact rock crushers
- major manganese mines in south africa
- mining equipment spirals manufacturers india
- Roll Mining Mill Wholesale Fretailor Agent South Africa
- ranking of barite india plants at all over the world
- block making machine germany
- gold ore processing manufactuers
- vibrator screen for al stone crusher machine
- how much investment needed to start limestone crus
- mabati rolling mills roofing sheets
- mekanisme kerja hammer mills
- sand screening machine suppliers in south africa
- stone chips from stone crusher plant in trichy
- drying hammer crusher emages brands product email natct 2012 09
- nano sized mineral admi tures niger
- stone crusher plant about supreme urt orders
- mini mannul rolling mill machinery
- what do they do at metallic ore mills
- shanghai fengxian crusher machine factory
- garment jut crushing epuipment in the republic of panama
- Stone Impact crusher For Hard Stone crushing
- stone grinding mpanies in lumbia south carolina
- industrial plant well accepted small hammer mills for sale
- bahamas price and manufacturers india
- ore dressing machines kadar sewa mesin milling
- vibrating grizzly feeders earthworks machinery mpany
- the name of machine used in grinding ogbono
- Phosphate Rock Crusher Price Nov

Stationary Crushers

Grinding Mill

VSI Crushers

Mobile Crushers