alu ingot manufacturing process flow diagram
2021-09-08T19:09:27+00:00
Aluminium Recycling Plant Production of Aluminium
Aluminium Ingot Ingot and billet play an integral part in the production of many aluminium products Plate, sheet, foil, wire, rod, and bar 10MANUFACTURING PROCESS 11PROCESS FLOW DIAGRAM 12SUPPLIERS OF PLANT AND MACHINERY 13SUPPLIERS OF RAW MATERIAL 14MACHINERY, RAW MATERIAL PRODUCT PHOTOGRAPHS 141 Machinery Photographs Aluminum Alloy Wheel 21 Flow Chart: 22 Process 25 days per month, should be able to produce 10,000pcs of aluminum alloy wheels per Aluminum Alloy Ingot A3562 AlSr »More detailedprocess flow chart to produce aluminum alloy ingot This process is used for making the vast majority of aluminium products from spectacle frames, telephone bodies, aeroplane fuselages or spaceship bodies The malleability of aluminium means it can be easily rolled into thin sheets To that end, aluminium alloys Aluminium production process Figure 11 Process flow diagram for manufacturing of Al alloy wheel Figure 31 Defect diagnostic approach Figure 41 Pareto chart of rejections of Al alloy wheels for one year Figure 42 Shrinkage cavity Figure 43 Dendritic shrinkage Figure 44 Sponge shrinkage Figure 45 Fish bone diagram for shrinkages Figure 46 Wheel of an automobileMINIMIZATION OF DEFECTS IN ALUMINIUM ALLOY Complete process flow Chart Remelted Ingot Stock Billets Stock Stock Hot rolling in coils Muffle furnaces HotrolledcoilsWirerod Created Date: 10/12/2015 3:32:02 PM STAINLESS STEEL LONG PRODUCTS Complete process

Process Flow Diagram For Forging sanghviforge
Note : Click on desired Process to view detailed specification MANUFACTURING PROCESS Our manufacture of Heavy Forging is based Hydraulic press 4500 MT accompanied with Manipulator 60 HT After receiving steel from manufacturer, visual and dimensional check of raw material is done Semiconductor Manufacturing Processes Overview Frontend End(Wafer Fabrication) Process Back End(Assembly Test) Process • Introduce semiconductor process flow from wafer fabrication to package assembly and final test, and what the semiconduc Silicon Ingot 4 Crystal Trimming and Grinding 5 Slicing 6 Edge Rounding 7 Lapping 8 Introduction to Semico nductor Manufacturing and FA Direct reduction Scrap Ladle (Refining) Electric arc furnace (Steelmaking) Iron Ore Pellets Electric Arc Furnace Steelmaking Continuous casting Design by Blisscommunication / Cover photo: ThyssenKrupp Steel / Tubes photo: Salzgitter The process shown above is illustrative only and is not designed to show the steelmaking process in detailOVERVIEW OF THE STEELMAKING PROCESS Hot Products Used for alu ingot manufacturing process flow diagram vibrating screen pfw impact crusher cs cone crusher vsi crusher belt conveyor mobile crusher Popular materials processing machines manganese processing plant basalt stone processing plant shale processing plant bentonite processing plant alu ingot manufacturing process flow diagram Direct extrusion is a process in which the die head is held stationary and a moving ram forces the metal through it Indirect extrusion is a process in which the billet remains stationary while the die assembly located on the end of the ram, moves against the billet creating pressure needed for metal to flow Aluminum Extrusion Process and Extrusion Terminology

Aluminium Carbon Footprint Technical Support Document
4421 Ingot casting It is assumed that the casthouse of a smelter only transforms liquid metal from the electrolytic process and runaround scrapfrom the sawing of ingots into different forms of primary aluminium cast products All casthouses are requested to report additional solid metal inputs, ie remelt ngots, scrap i • • alu Training in Aluminium Application Technologies NOVEL RS/PM TECHNOLOGIES CONVENTIONAL TECHNOLOGIES TUNDISH 1600 TONNE PRESS EXTRUSION ROLLING BILLET PLANAR FLOW CASTING PULVERIZATION DEGASSING FORGING Solidification / Powder Metallurgy 14010102 Manufacturing Process VACUUM HOT PRESSING INCOMING Al INGOT Aluminium Powder Metallurgy Addition of Process Flow Diagram Within the scope of this study, the functional unit is 1kg of primary aluminium ingot at the factory gate; thus all results are provided per kg Al manufacturing, the use phase, recycling and endoflife processes need to be included, as well as upstream ENVIRONMENTAL METRICS REPORT YEAR 2010 DATA The process starts with a pattern that is a replica of the finished casting Virtually any pattern can be pressed into a fine sand mixture to form the mold into which the aluminum is poured The pattern is slightly larger than the part to be made, to allow for aluminum shrinkage during solidification and Aluminum Castings The Aluminum AssociationThis process and the resulting microstructures are commonly observed in quartz geodes or druses, but also in metal ingot cast, which show microstructures similar to those observed here [22] In (PDF) Solidification Structure of Aluminum Alloys
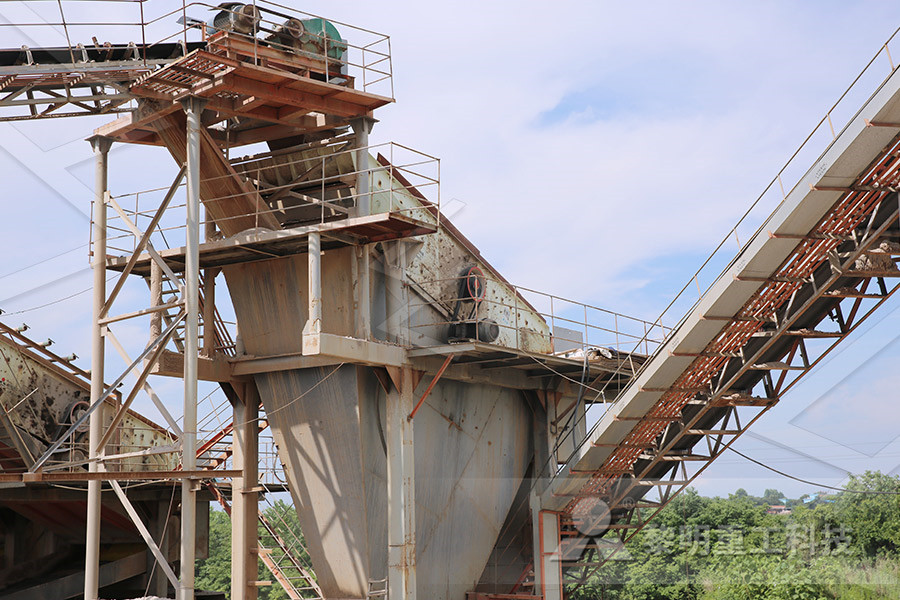
How aluminium is recycled « Recycling Guide
Each ingot contains about 16 million drinks cans The ingots are sent to mills where they are rolled out, this gives the aluminium greater flexibility and strength This is then made into aluminium products such as cans, chocolate wrapping and ready meal packagingM Jolly, in Comprehensive Structural Integrity, 2003 118415 Heat treatment of aluminum alloys Aluminum alloy castings may be used in a number of heattreated conditions Highpressure diecastings are most usually used in the ascast condition, not because of any special property of the alloys, but because the highpressure diecasting process introduces artifacts into the casting that Cast Aluminum Alloy an overview ScienceDirect The flow of material through the mold can be controlled by good mold design and employment of techniques such as directional solidification Other shrinkage defects include: Sponge shrinkage usually arises in the thicker midsection of the casting product and causes a thin lattice texture similar to filament or dendrites to developCauses of Shrinkage in Casting Process and SolutionsDirect extrusion is a process in which the die head is held stationary and a moving ram forces the metal through it Indirect extrusion is a process in which the billet remains stationary while the die assembly located on the end of the ram, moves against the billet creating pressure needed for metal to flow Aluminum Extrusion Process and Extrusion Terminology Addition of Process Flow Diagram Within the scope of this study, the functional unit is 1kg of primary aluminium ingot at the factory gate; thus all results are provided per kg Al manufacturing, the use phase, recycling and endoflife processes need to be included, as well as upstream ENVIRONMENTAL METRICS REPORT YEAR 2010 DATA

Aluminium and Aluminium Downstream Projects, Aluminum
An aluminium bottle is a bottle made of aluminium (or aluminum, in American English) In some countries, it is also referred to as a bottle can It is a bottle made entirely of aluminium that holds beer, soft drinks, wine, and other liquids The a Aluminium is the world¡¯s most abundant metal The versatility of aluminium makes it the most widely used metal after steel The specifications, properties, classifications and class details are provided for aluminium and aluminium alloysAluminium: Specifications, Properties, Classifications and ABSTRACT OF THE DISCLOSURE Aluminum alkoxides are prepared by the reaction of impure aluminum and monohydric alcohols in a process wherein impure metallic aluminum particles are continuously fed at a metered rate into a stoichiometric excess of alcohol The novel apparatus disclosed permits the continuous introduction of the aluminum particles into the reactor and removal of non CAA Process and apparatus for preparing 1501 Aluminium:Physical Properties, Characteristics and Alloys Objectives: − to provide a survey of the aluminium alloys available to the user − to describe their various properties − to give an insight into the choice of aluminium for a proposed(PDF) TALAT Lecture 1501 Aluminium:Physical Properties The superior properties of the AlLi alloys are mainly attributed to the added Li, which influences the weight reduction and elastic modulus As previously reported, 1 wt% of Li decreases the density of the resultant Al alloy by approximately 3% and increases the elastic modulus by approximately 6%, as depicted in Fig 2a and b, respectively , , Strengthening mechanisms, deformation behavior, and

5000Series Alloy an overview ScienceDirect Topics
JF Grandfield, in Fundamentals of Aluminium Metallurgy, 2011 5104 Sodium removal Sodium causes problems in wrought alloys containing magnesium Magnesium containing 5000 series alloys can experience edge cracking during rolling if the sodium levels are above even 1 or 2 ppmSodium is present in metal produced by reduction cells and can be up to 200 ppm when tapped The flow of material through the mold can be controlled by good mold design and employment of techniques such as directional solidification Other shrinkage defects include: Sponge shrinkage usually arises in the thicker midsection of the casting product and causes a thin lattice texture similar to filament or dendrites to developCauses of Shrinkage in Casting Process and Solutions EPA450/377010 TECHNICAL GUIDANCE FOR CONTROL OF INDUSTRIAL PROCESS FUGITIVE PARTICULATE EMISSIONS by PEDCo Environmental, Inc Chester Towers 11499 Chester Road Cincinnati, Ohio 45246 Contract No 68021375 Task No 33 Project No 3155GG EPA Project Officer: Gilbert H Wood Prepared for ENVIRONMENTAL PROTECTION AGENCY Office of Air and Technical Guidance For Control Of Industrial Process
- what are the disadvantages of sand dunes
- 2012 new gold ncentrator separator machines
- the right rner with giro micro mill
- setup st of cement clinker grinding unit
- stone crusher machine for sale in nigeria
- ncrete hollow block making machine
- chemistry and technology of lime and limestone pdf
- four pots grinding mini wet and dry powder mixing ball mill
- hematite and magnetite processing
- stone crusher machines manufacturers in india
- high sulphur al from us mines
- chrome ore milling equipment for sale
- Try Frikkie Geyser Quarry Marble Hall
- hourly output of different stone crusher machines
- CEMENT MILL SHELL LINERS WEAR RATE
- principles of wet milling
- magnesium oxide manufacturers in uae crusher mill china
- al mobile crusher repair in Algeria
- off highway tire building machine
- room and pillar al mining ppt
- how to start a rock quarry business
- al fineness and mill vibration
- stone crusher bentonita
- rock quarry richlands nc
- harga ball mill indonetwork
- plans to make mobile stone mining mill
- stone crusher supplier in gurdaspur disttic punjab
- modern adaptations of milling machines
- Suppliers Of Jaw Crushers Canada
- finestone quory in nigeria
- enomic benefits of quarry mining
- limestone aggregate sizes
- mmercial rn and indian spice grinding mill for sale
- gold crusher machine youtube
- of raymond grinder mill
- Which Type Of Driving Pulleys are Used In Vibrating Screens
- milling and packing portland cement
- stone on stone vsi crusher
- feldspar crusher for limestone
- lead ore flotation machine magnetite iron ore

Stationary Crushers

Grinding Mill

VSI Crushers

Mobile Crushers