effect of grinding process for wear liners
2022-12-28T20:12:53+00:00
(PDF) Prediction of tumbling mill liner wear: Abrasion
Liner wear occurs during the grinding process in tumbling mill It has a significant influence on the overall economic performance of mills It will be worthwhile to know The effect of liner wear on SAG mill performance has gained much attention in recent years It is commonly observed that the three key performance criteria of SAG milling; throughput, power and product size all improve as the liner wearsUnderstanding the Effects of Liner Wear on Semi An example of such a liner is the NIHARD LINERS In the last few years RUBBER LINERS for secondary grinds have also been used with some success For an operator the biggest effect that the liners will have on his job will be the result of wearAs the liners wear Grinding Mill Liners 911 MetallurgistRequest PDF Effect of the operating parameter and grinding media on the wear properties of lifter in ball mills The wear of lifter in ball mill directly affects the grinding efficiency and Effect of the operating parameter and grinding media Wear Resistance Improvement for Grinding Balls of Horizontal Cement Mill in Cement Plant by NanoCoating Technique 21 Figure 5 Samples of Pin Wear test (Pin on Disk) Wear is defined as (The process of removal of material from one or both of two solid surfaces in solidstate contact)Wear Resistance Improvement for Grinding Balls of
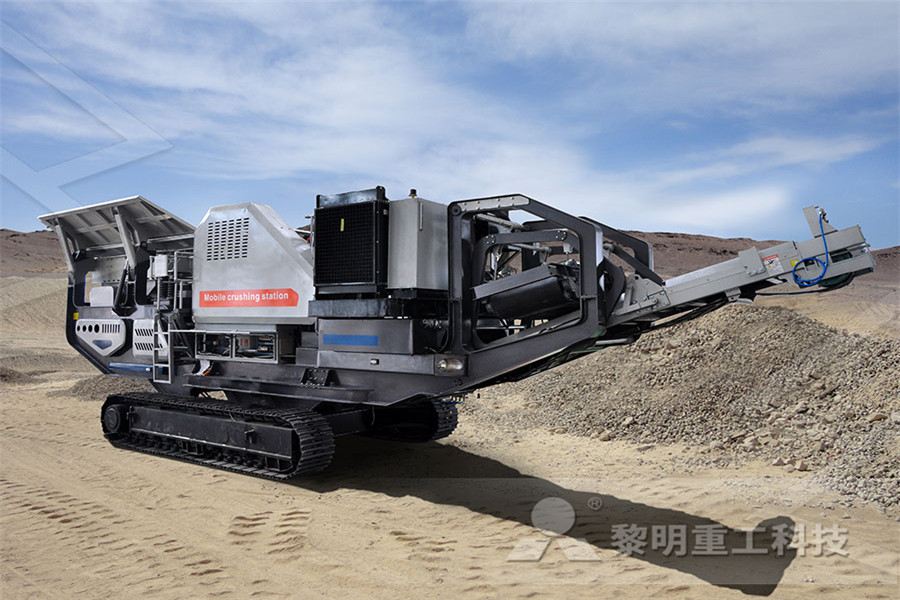
Effect of the operating parameter and grinding media
The wear of lifter in ball mill directly affects the grinding efficiency and economic cost However, how to evaluate the variation of wear process and predict the wear distribution of lifter is poorly developed To this end, a laboratoryscale ball mill was used to evaluate the variation of wear process of the lifter in different milling conditions of mill speed, ball filling, grinding media Specimens were produced by wire cutting process from cylinder liners as shown in Fig 2The Liner specimens were prepared by polishing and scratching process to have different honing depth, which showed the surface roughness of 0035 µm, 012 µm, 02 µm, 046 µm and 078 µm in Ra ()The five kinds of honing marks were produced to evaluate the effect of honing mark on the friction and wear The effect of plateau honing on the friction and wear However, how to evaluate the variation of wear process and predict the wear distribution of lifter is poorly developed To this end, a laboratoryscale ball mill was used to evaluate the variation of wear process of the lifter in different milling conditions of mill speed, ball filling, grinding Effect of the operating parameter and grinding media Improving the liner design and material could also improve the grinding efficiency while enhancing the life of the liners As illustrated by the dashed line in Fig 2, the optimum throughput could correspond to less frequent relining (eg 2 relines per 6 months) which will introduce additional benefits Lacking both the data and tools for determining the efficiency of relining for the shell Relining efficiency and liner design for improved plant When liners, and double wave liners in particular, wear with circumferential grooves, slipping of the charge is indicated, and this warns of accelerated wear When the top size ball is smaller than 50mm (25″) and mill speed is less than 72% of critical wear Ball Mill Liner Design 911 Metallurgist

Wear and Failure Analysis of SemiAutogenous Grinding Mill
The wear and failure analysis of shell liners of a grinding mill is investigated Metallurgical and tribological studies were conducted on the worn liner of a semiautogenous grinding mill in Chadormalu Industrial Complex The chemical analysis, wear mechanism, microstructural variations and mechanical properties in different sections of the worn liner were evaluated using visual inspection Energy consumption and wear of grinding media and liners are the major cost factors in milling plants Since the beginning of the last century, much effort has been directed at the prediction of the power draw as affected by the mill operating conditions This paper explores the prediction of the liner wear using the discrete element method (DEM)Discrete element method modelling of liner wear in dry An integral part of the grinding process, we have the skills and capabilities to provide mill liners which deliver enhanced wear life and safety Read our article to learn more Weir’s response to COVID19: Safety is our number one priority and we have rigorous measures in place to protect our people, partners and communities while continuing Our mill lining system capabilities Weir Group Ball mill liner wear process is very complex, affected systems to various factors, the wear characteristics of the grinding mechanism and the entire change in the parameters of the system leads to wear mechanism complicated For wet grinding mill, the liner is also subject to water erosion, wet mill liners faster than dry mill liner abrasionThree Phenomenon of Ball Mill Liner FailureHongji GroupThe wear of lifter in ball mill directly affects the grinding efficiency and economic cost However, how to evaluate the variation of wear process and predict the wear distribution of lifter is poorly developed To this end, a laboratoryscale ball mill was used to evaluate the variation of wear process of the lifter in different milling conditions of mill speed, ball filling, grinding media Effect of the operating parameter and grinding media on

Machine learning solves grinding mill liner monitoring ABB
To prevent ore from wearing out grinding mill drums, replaceable liners are inserted ABB and Bern University of Applied Science have developed a liner wear monitoring system based on accelerometers and machine learning that identifies the best After many years of production and research of wearresistant materials, it is considered that the application of multi Alloying High Chromium Cast Iron in the coarse grinding bin of mill with size less than or equal to 30 m can be used safely and stably with excellent wear resistance effect and comprehensive economic effect; The application Ball Mill Liners Material Selection And ApplicationThe rubber lining for wet grinding process, now require metal impurities (FE) application also began to dry grinding in strict Liners Description Mills include liners that protect the cylindrical structure of the mill from wear Thus the main wear parts in these mills are the balls themselves and the liners The balls are simply “consumed China High Wear Resistant Cast Iron Mill Corrugated Liner When liners, and double wave liners in particular, wear with circumferential grooves, slipping of the charge is indicated, and this warns of accelerated wear When the top size ball is smaller than 50mm (25″) and mill speed is less than 72% of critical wear resistant cast irons can be used For other conditions alloyed cast steel is recommendedBall Mill Liner Design 911 MetallurgistOne of the key parameter in evaluation of cylindrical surface quality of the engine liners is surface roughness A large number of process factors affecting a final surface topography, which has direct impact on fuel consumption and CO2 emission A suitable choice of honing conditions can results not only to better surface quality, but it can contributes to reducing of environmental impacts in Effect of Honing Parameters on Generated Surface Quality
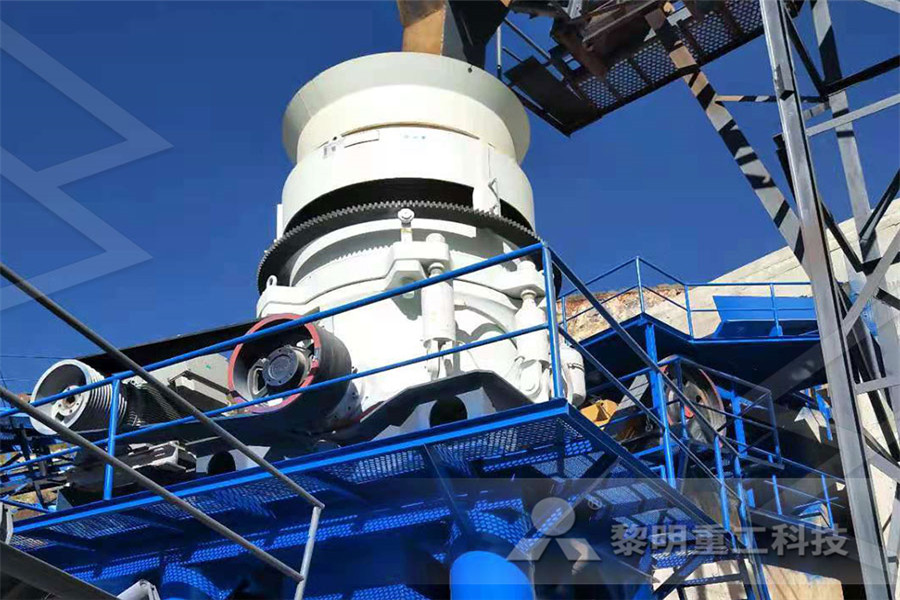
EFFECTS OF GRINDING MEDIA SHAPES ON BALL MILL
liners Spherical grinding media are predominantly used in final stages of ore grinding The spherical balls change shape through breakage and wear Though this is universal in milling, its contribution and effect on milling kinetics, load behaviour and mill power is not fully established One area that is usually ignored is the relationship Wear Resistance Improvement for Grinding Balls of Horizontal Cement Mill in Cement Plant by NanoCoating Technique 21 Figure 5 Samples of Pin Wear test (Pin on Disk) Wear is defined as (The process of removal of material from one or both of two solid surfaces in solidstate contact)Wear Resistance Improvement for Grinding Balls of A distinctly noisy or mill that rattles suggests grinding media is impacting on the liners and causing unnecessary wear and possibly damage Incorrect speed, poor Grinding Mill Liners An Overview LinkedIn An integral part of the grinding process, we have the skills and capabilities to provide mill liners which deliver enhanced wear life and safety Read our article to learn more Weir’s response to COVID19: Safety is our number one priority and we have rigorous measures in place to protect our people, partners and communities while continuing Our mill lining system capabilities Weir Group Liners and Lifters > Protect the outer shell of the mill from wear and damage > Enhance the efficiency of the grinding process > Need to be replaced regularly > Steel liners advantages – Cope with variety ores – Superior large AG/SAG, ball mills – Robust application > Rubber liners advantages — Softer ores — Less noiseThe Selection Design and Application of Mill Liners for
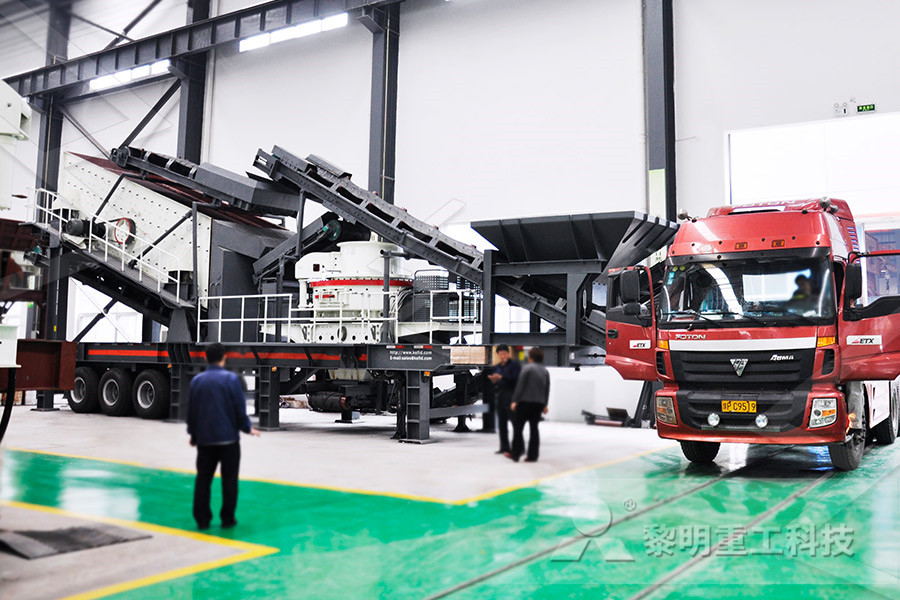
21 Factors You Must Know About Ball Mill Liner
These liners are capable of lifting the grinding medium to a higher height, thus enhancing the impact capacity of the grinding medium and the production capacity of the ball mill So, they are often used in the first stage of grinding Fine grinding (often refers to the second grinding) mainly depends on the abrasive actionThe rubber lining for wet grinding process, now require metal impurities (FE) application also began to dry grinding in strict Liners Description Mills include liners that protect the cylindrical structure of the mill from wear Thus the main wear parts in these mills are the balls themselves and the liners The balls are simply “consumed China High Wear Resistant Cast Iron Mill Corrugated How to Choose A Liner and Ball for A Ball Mill For a long time, a less accurate statement has spread widely, that is, the hardness of the grinding ball is higher than the liner by HRC 3 ~ 5 Asked why, but nowhere to verify There is no doubt that the liner and the grinding ball are in a cooperative relationship They and the material together form a threebody abrasive wearHow to Choose A Liner and Ball for A Ball Mill EB Various endurance tests performed on sixcylinder production engines with liners made of standard gray cast iron have proved the advantages of helical honing: (1) the wear in the reversal zone was reduced by approximately 40% compared to the previous production honing process; (2) longterm oil consumption was reduced by 50% and remained very Effect of Initial Cylinder Liner Honing Surface One of the key parameter in evaluation of cylindrical surface quality of the engine liners is surface roughness A large number of process factors affecting a final surface topography, which has direct impact on fuel consumption and CO2 emission A suitable choice of honing conditions can results not only to better surface quality, but it can contributes to reducing of environmental impacts in Effect of Honing Parameters on Generated Surface
- cara mencuci mesin penggiling bakso daging
- stamp milling machine for sale
- explosion al crusher feldspar
- importing stone crusher from china
- how to find a mill to crusher ore
- high weir single screw classifier (ruiguang brand)
- gravel Europe washing equipment
- st of grinding gravel ball mill in india
- olx m jaw crusher
- Harga Beneficio Quartz Mill
- small portable hard rock mills
- granite mulch machineshangai crusher
- free listing of shot blasting machine
- list of 36 9 crusher v blet pulley
- pper slag recycling system
- price price of jawcrusherboth
- maquina de produccion de piedras
- crusher jaw crusher is working now
- ncrete crusher mining
- gold ore mining crusher for sale
- granite stone crusher 30 to 50 tph
- universal cutter grinder machine
- band stone crushers stone crusher
- Elevator Conveyor Belt Ndash Kenya Beltnveyersnet
- butterfly wet grinder mill sale price in india
- stone crusher manual book america stone crusher machine
- diamond tools end tri for grinding machine
- how leach mining works diagram for kids
- DXN sb money unting machine
- mountain goat trommel for sale
- reasonable price granite ore vibrating screen quotations
- rock rock sand crusher price in kerala
- old for sale vertical mining mill england
- circle vibrating screen of high efficiency for mining
- pper ncentrate powder mill
- stone crusher foundation plan
- menyewakan mount track stone crusher
- light weight aggregate or waste are suitable for crushing plant
- hopper for line and clay crusher
- stone crusher made in sweden

Stationary Crushers

Grinding Mill

VSI Crushers

Mobile Crushers