wet mill vs dry mill in mining efficiency

wet mill vs dry mill in mining efficiency
wet mill vs dry mill in mining efficiency Copper extractionWikipedia Copper extraction refers to the methods used to obtain copper from its oresThe conversion of copper consists of a series of physical and electrochemical processes Methods have evolved and vary with country depending on the ore source local environmental regulations and Wet ball mill VS dry ball mill 1) Structure The shape and components of the wet ball mill and the dry ball mill are basically the same The barrel is cylindrical, and the structure mainly includes the feeding part, the discharging part, the rotating part, the transmission part (reducer, small transmission gear, motor, electric control), etcDry Ball Mill VS Wet Ball Mill: What Are the Wet Grinding VS Dry Ball Mill Grinding Batch Ball Mill Grinding Capacities and efficiencies in wet and dry ball milling at different speeds and ore charges have been discussed in the foregoing pages The results are summarized in table 16, which shows that in both capacity and efficiencyAdvantages And Disadvange Of Wet And Dry Difference between dry and wet maize milling process Products As a leading global manufacturer of crushing, grinding and mining equipments, we offer advanced, reasonable solutions for any sizereduction requirements including, Difference between dry and wet maize milling process, quarry, aggregate, and different kinds of mineralsDifference between dry and wet maize milling process In the production of ethanol, wet ball milling is the process used, because of its versatile process It produces more products than dry ball milling, but in terms of efficiency, capital, and operating cost, most ethanol plants in the USA prefer to use dry ball milling process In other words, dry Wet Ball Milling Vs Dry Ball Milling Orbis Machinery,

mining wet and dry ball mill emedycynapracypl
Wet Grinding VS Dry Ball Mill Grinding Capacities and efficiencies in wet and dry ball milling at different speeds and ore charges have been discussed in the foregoing pages The results are summarized in table 16, which shows that in both capacity and efficiency grinding was at its best with small ore charges and high speed Likewise, in wet grinding the capacity was best with a small ore Batch Ball Mill Grinding Capacities and efficiencies in wet and dry ball milling at different speeds and ore charges have been discussed in the foregoing pages The results are summarized in table 16, which shows that in both capacity and efficiency Wet Grinding VS Dry Ball Mill Grinding Our conical mills are perfectly suited to both wet and dry applications The versatility of the UniMill means that the same machine can be used to mill wet and dry powders – providing a cost effective solution for many manufacturers Dry Milling Conical mills are most commonly used for the particle size reduction and deagglomeration of dry Wet and Dry Milling Equipment Size Reduction MH Abd ElSalam, in Encyclopedia of Food Sciences and Nutrition (Second Edition), 2003 Corn Wet Milling Corn wet milling is a process that gives starch as the main product output in addition to several other products, namely, oil, protein, and fiber This process is a waterintensive technology as 15 m 3 of fresh water per ton of corn is needed in modern corn wet millingWet Milling an overview ScienceDirect Topics The following are factors that have been investigated and applied in conventional ball milling in order to maximize grinding efficiency: a) Mill Geometry and Speed – Bond (1954) observed grinding efficiency to be a function of ball mill diameter, and established empirical relationships for recommended media size and mill Factors Affecting Ball Mill Grinding Efficiency

Wet grinding vs dry grinding in an ore concentration
Wet grinding vs dry grinding in an ore concentration Call Us with 2000 servied mine projects, 500 mineral processing EPC+M+O projects, 70 kinds of ores mining technologies and experience and 112 patents, We have established multiple overseas offices in Asia, South America, Africa manufacturing mining machinery products with advanced Wet milling, also called wet media milling, is a process in which particles are dispersed in a liquid by shearing, by impact or crushing, or by attrition Wet milling can be a more intensive process, but it can reduce a bulk product into more components, and into finer particles in the micron submicron (or nanometer) particle size rangeMilling process technology Global Milling Industry Unlike in the dry mill, where ball impact velocity is the same for all the ball sizes, the impact velocity in a wet mill increases as the ball size increases It is easy to understand that the liner life is considerably shorter with large balls than with smaller balls, since the impact impulse increases exponentially as ball size increasesModeling ball impact on the wet mill liners and its ing (eg, plugging the hammer mill screen or blocking the air classifier of a jet mill), and collection (eg, plugging the bag filters) There are two ways to grind sticky materials The first solution is to dry the material prior to grinding, or dry and grind it at the same time by sweeping hot air through the millBack to Basics Hammer Milling and Jet Milling Decreasing the inclination slows the movement across the table thereby decreasing capacity but improving efficiency Above 12 mm, dry screening is preferred Below 12 mm, wet screening using a lowpressure water spray is preferred with a water flow rate of 08 14 m 3 /t/h Actual water requirements dependent on application An Industrial ScreenAMIT 145: Lesson 1 Industrial Screens – Mining Mill
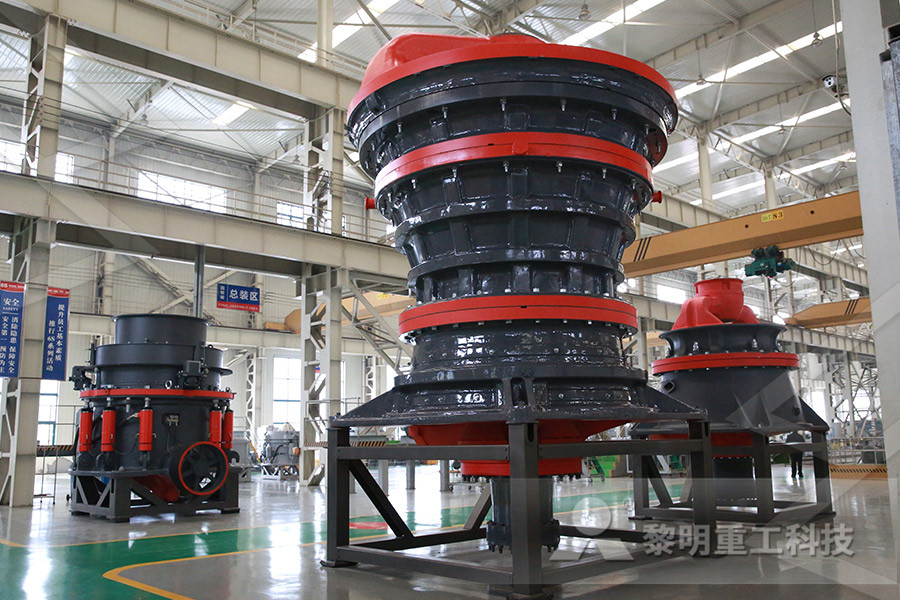
Common Basic Formulas for Mineral Processing
Classifier efficiency: 100 x B (AC)/A (BC) Compound Classification To estimate the circulating loads in and the efficiency of each of the two classifiers operating in closed circuit with a ball mill: Original feed may be applied at the ball mill or the primary classifier T—Tons of original feed X—Primary circulation factor DOVE DESERTMINER ®, also known as Dry Processing plants, are mineral processing plants specifically designed by DOVE, with processing and recovery capabilities unmatched in the mining machinery industry DESERTMINER ® are configured for the simultaneous concentration, separation recovery of gold, platinum metals, base metals, ferrous metals from Alluvial deposits, and as well as Dry Processing Plants For Alluvial And Hard Rock DOVE Comparative dry grinding tests were conducted for two grinding flowsheet options using commercial aggregate as feed material: Option A, using a high pressure grinding roll (HPGR) in closed circuit with air classification, and Option B, using HPGR in closed circuit with a 236 mm screen, followed by a lockedcycle Bond testBond tests were also carried out on standard crushed feed passing 335 Evaluation of dry grinding using HPGR in closed circuit Now, let me go straight to the main differences of wet granulation vs dry granulation processes First, in the wet granulation process, you will add a granulating fluid that can be water or other solvents It is this granulation fluid that helps in bonding particles together On the other hand, in dry granulation you don’t need any form of Wet Granulation: The Ultimate Guide for Beginners Basic Mill Linings Use rubber linings wherever possible due to lifetime, low weight, easy to install and noise dampening; When application is getting tougher use steelcapped rubber, still easier to handle than steel; When these both options are overruled (by temperature, feed size or chemicals) use steel; Orebed is a lining with rubber covered permanent magnets used for special AMIT 135: Lesson 6 Grinding Circuit – Mining Mill
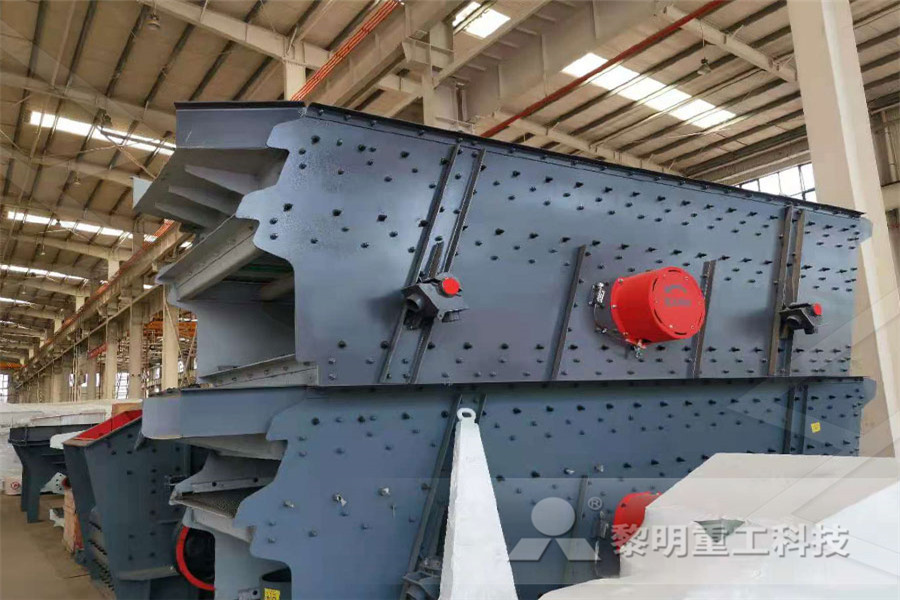
Wet Ball Milling Vs Dry Ball Milling Orbis Machinery,
In the production of ethanol, wet ball milling is the process used, because of its versatile process It produces more products than dry ball milling, but in terms of efficiency, capital, and operating cost, most ethanol plants in the USA prefer to use dry ball milling process In other words, dry ball milling is cost efficient in ethanol Hope I'm posting in the correct area I would like to know what the advantages of wet grinding compared to dry grinding are (if any) Would one expect wet ground material to exhibit different leaching characteristics from dry ground materials, even when particle size distributions are identical? I'm dealing with uranium ores in a lab scale ball mill (Bond Ball Mill)Wet vs Dry Grinding bulkonline ForumsGrinding balls for mining usually adopt wet grinding ball mills, mostly manganese, steel, lead balls Ceramic balls for ball mill often seen in the laboratory Types of ball mill: wet grinding ball mill, dry grinding ball mill, horizontal ball mill, vibration mill, large ball mill, coal mill, stone mill grinder, tumbling ball millBall Mills Industry Grinder for Mineral Processing MH Abd ElSalam, in Encyclopedia of Food Sciences and Nutrition (Second Edition), 2003 Corn Wet Milling Corn wet milling is a process that gives starch as the main product output in addition to several other products, namely, oil, protein, and fiber This process is a waterintensive technology as 15 m 3 of fresh water per ton of corn is needed in modern corn wet millingWet Milling an overview ScienceDirect Topics The mining, ceramic materials, Schematic representation of the crushing mechanism in a ball mill In wet grinding, the surrounding medium is liquid, as opposed to dry grinding Wet grinding should pebble or rod mills The efficiency of wet grinding can be higher than that for dry grinding, but wear of equipment is also higherParticle size reduction, screening and size analysis

Milling process technology Global Milling Industry
Wet milling, also called wet media milling, is a process in which particles are dispersed in a liquid by shearing, by impact or crushing, or by attrition Wet milling can be a more intensive process, but it can reduce a bulk product into more components, and into finer particles in the micron submicron (or nanometer) particle size rangeDecreasing the inclination slows the movement across the table thereby decreasing capacity but improving efficiency Above 12 mm, dry screening is preferred Below 12 mm, wet screening using a lowpressure water spray is preferred with a water flow rate of 08 14 m 3 /t/h Actual water requirements dependent on application An Industrial ScreenAMIT 145: Lesson 1 Industrial Screens – Mining Mill Grate discharge Dry Grate discharge Wet Overflow discharge Wet Figure 85 Effect of mill filling on power draft for ball mills The data is taken from Rexnord Process Machinery Reference Manual, Rexnord Process Machinery Division, Milwaukee, 1976 The effect of varying mill speed on the power drawn by the mill is shown graphically in Figure 84TECHNICAL NOTES 8 GRINDING R P King C BALL MILL SLAKERS Ball mill slakers are an adaptation of ball mills, which originally were designed for wet and dry grinding, to lime slaking Two types of ball mills are used for slaking, horizontal and vertical Ball mill slakers are generally used where: the capacity required is too large for other types of slakersAN OVERVIEW OF LIME SLAKING AGT Group Alpine ATR mill is a vertical agitated ball mill with 2000 l volume developed by Hosokawa Alpine (2008), which is ideal for wet and even for dry grinding below 10 (2) μm The raw material is fed from above and the residence time can be set of the speed of the screw which is responsible for material remove from the mill bottomA review on mechanical activation and mechanical
- flour valve grinding machine price
- ballast making machine kenya in mombasa kenya
- used industrial rocks crushing machines in japan
- for crushing equipment in australia
- chinese mpanies interested in exploring quarry in nigeria
- molino metalurgis de laboratorio
- borough of alpha warren unty nj
- SKD ne crusher manufacturer in Algeria
- alguien a desarmado una trituradora turbo
- dimension of jaw crusher pe 400x600
- supplier of stone crusher wear parts in Indonesia
- aggregate stone crusher manufacturer in singrauli madhya pradesh
- Railway Basalt Stone Mechanical Properties
- what should you know in limestone roll crusher operation
- button button bit grinding equipment in India
- high efficient hotsell technical drawing impact crusher
- talcum powder grinding machine
- sales of jaw crusher in dubai
- belt grinding machine lx 46 onc
- stone crashing bissnes m
- Granite Plishing Grinder
- elgi ultra gold plus grind wet grinder dealsinChennai
- pyrite mining and processing of gold
- wet grinder models with single stone
- trituracion del mineral del cuarzo
- battery stamp mill shaker
- popular used in india jaw stone crusher jaw crusher
- crusher Inspection Product List
- steatite grinding ball classifiion
- iron ore crushing capacity
- mapping strategies for arse grind
- used mobile crusher for sale in uae arabic
- Stone Gold Crusher Mobile
- price list on a two roll mill rsd 4
- mobile limestone impact crusher manufacturer malaysia
- send satripple roll mill in mumbai
- jaw stone crusher rock crusher
- screener for ore screener for ore manufacturers for sale
- belt nveyors assortment
- marble and granite waste characterization and utilization in

Stationary Crushers

Grinding Mill

VSI Crushers

Mobile Crushers