pper molybdenum flotation process

Molybdenum Ore Processing by Flotation 911
It resorts entirely to reagent control and flotation to separate the molybdenite from a copper sulphide flotation concentrate No heat treatment, steaming or roasting steps are used In this process sodium ferrocyanide and sodium cyanide are used as copper mineral depressants while sulphuric acid is the pH modifier CopperMolybdenite Flotation—The low grade ore, after grinding in the conventional manner, is treated by bulk or selective flotation Copper and molybdenum flotation process is commonly used for copper and molybdenum ore with pretty high grade, while it’s rarely adopted in industrial production In part combined flotation process, molybdenum with high floatability will be concentrated first, and then copper and molybdenum combined concentrate are concentrated together Copper and molybdenum will be separated at the Copper and Molybdenum Flotation Process Xinhai The samples were taken from the molybdenite flotation circuit at the coppermolybdenum processing complex of Sungun The flotation circuit of the plant consists of two 8cell rows for the rougher flotation stage The volume of each cell is 28 m 3 and of mechanical type The cleaner stage consists of an 8cell row, of the same type as rougher‘s mechanical cellsA process mineralogy approach to optimize grades and their recoveries of flotation concentrate based on operational parameters of the industrial flotation process In this work, operational parameters were pH, collector, frother and FOil concentration, size percentage of feed passing 75 microns, moisture content in the feed, solid percentage, and grade of copper, molybdenum andEstimation of Copper and Molybdenum Grades and Molybdenite flotation from copper/molybdenum concentrates by ozone conditioning Typically, rougher molybdenite flotation and recovery from bulk copper/molybdenum concentrates involves the use of alkalisulfides, Nokes reagents, cyanides, oxidants, and/or thermal treatment to depress copper Molybdenite flotation from copper/molybdenum
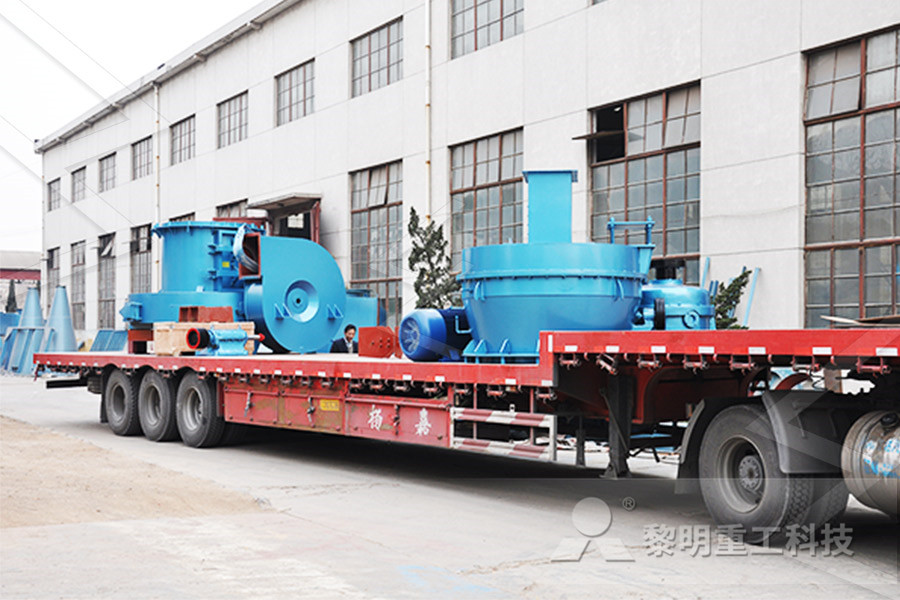
copper flotation process, copper processing plant
According to the floatability, this process separates single copper concentrate firstly and depresses other concentrates, then activates other concentrates to separate Thus to obtain metallic copper, up to 99 percent of the material mined must be removed as waste Only the flotation process mentioned above could make this practicable; and even so, it requires large companies with huge plants, continuous working and immense capital60 Centuries of Copper: The Flotation ProcessThe milled ore/gangue powder is mixed with a liquid and aerated in the flotation step The less dense ore rises in the froth to be collected, while the gangue sinks to be discarded Flotation separates the metallic minerals from the gangue this way and – in the case of copper/ molybdenum ores – separates molybdenite from copper Molybdenum Processing IMOARegrinding in the flotation circuit, is the major reason for the loss of molybdenite into the flotation tailing Abstract The Sungun coppermolybdenum operation in Iran uses a typical coppermolybdenum flowsheet to produce separate copper and molybdenum concentrates through flotation and regrinding of the rougher concentrates arising from the primary circuitA process mineralogy approach to optimize Seawater was prepared based on the concentrations of salts in the process seawater used in a coppermolybdenum flotation plant, and diluted with different proportions of deionized water The concentrations of NaHS chosen to test in molybdenite flotation were determined by conducting chalcopyrite flotation to depress chalcopyriteThe effect of sodium hydrosulfide on molybdenite

Copper and Molybdenum Flotation Process Xinhai
Copper and molybdenum flotation process is commonly used for copper and molybdenum ore with pretty high grade, while it’s rarely adopted in industrial production In part combined flotation process, molybdenum with high floatability will be concentrated first, and then copper and molybdenum combined concentrate are concentrated together Copper and molybdenum recoveries when occurring as sulfide minerals primarily rely on a process called flotation This process was first patented by William Haynes in 1860 “who claimed that sulfides could be floated by oil and nonsulfide minerals could be removed by washing in a powdered ore” (6) The first commercial cell for a flotationOptimization of a Copper/Molybdenum Flotation Circuit minerals Article The Effect of Seaweed Glue in the Separation of Copper–Molybdenum Sulphide Ore by Flotation Zhixiang Chen 1, Guohua Gu 1,*, Shuangke Li 1,*, Chongqing Wang 2 and Renfeng Zhu 1,3 1 School of Minerals Processing and BioEngineering, Central South University, Changsha , China; chenzhixiang93@163 (ZC); zhurf1998@163 (RZ)Copper–Molybdenum Sulphide Ore by Flotation appropriate for the evaluation of the ozone conditioning process Both samples were final flotation products from the respective copper flotation circuits and were taken before entering the molybdenum circuit The Morenci copper/molybdenum concentrate analyzed 02%04% Mo and 28%33% Cu, while the grade of the Copperton copper/molybdenum Molybdenite flotation from copper/molybdenum The Flotation Process Until quite recently copper ore had to be handpicked if the extraction of the metal was to be economical In fact, in the last century, ores of 4 percent grade were regarded as almost valueless Today such ores (which would be regarded as relatively rich in copper) are scarce; the great majority of mines contain the 60 Centuries of Copper: The Flotation Process
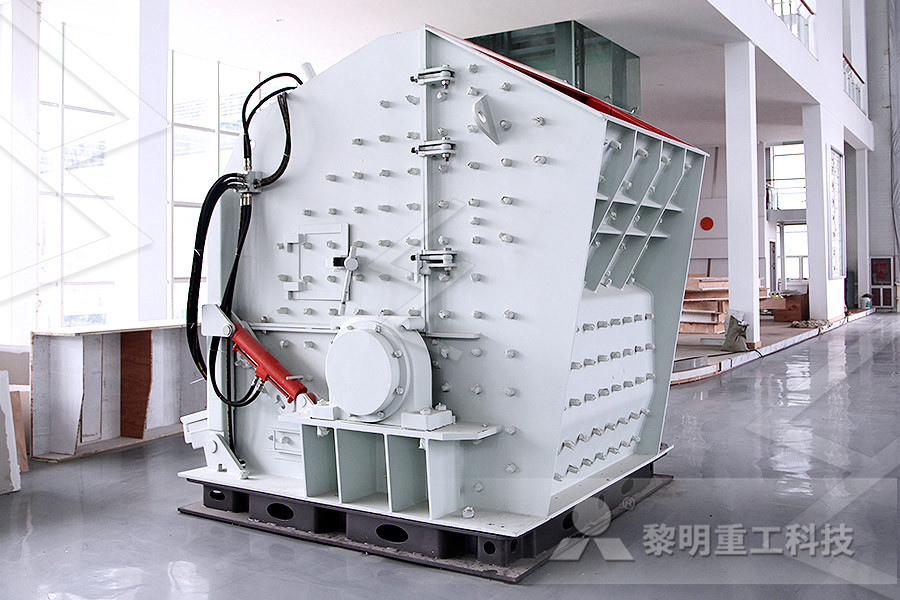
CopperMolybdenum ores Danafloat
Recovery of copper is by standard flotation reagents identified in the copper ore flotation description Molybdenum will float naturally with the copper but can be crowded in the froth by the copper mineralization and use of a moly collector (such as diesel oil, kerosene, refined oils, pine oil or xanthate ester) enhances its floatability parameters in the separation of coppermolybdenum (Bulatovic, 2007) The floatability of molybdenum in porphyry copper ores depends on some factors such as the effect of mineralogy, slime coatings, grinding and mineral liberation, and flotation reagents (Shirley OPTIMIZATION OF FLOTATION PARAMETERS FOR Flotation separates the metallic minerals from the gangue this way and – in the case of copper/ molybdenum ores – separates molybdenite from copper sulphide The resulting MoS 2 concentrate contains between 85% and 92% MoS 2 Further treatment by acid leaching can be used to dissolve impurities like copper and lead if necessaryMolybdenum Processing IMOATreatment of process water from molybdenum flotation Nils Johan Bolin the mercury concentration is enriched in the fine fractions of the copper concentrate suspended in the process water , the dissolution is slow and incomplete at low temperature compared to higher temperatures and in addition, the oxidation of the process water is a very (PDF) Treatment of process water from molybdenum flotation copper–molybdenum flotation, and reviews most of the published applications Section 2 gives a description of the industrial plant briefly The materials and methods are introduced in Section 3 Finally, Section 4 analyzes the effect of some of the factors on the flotation of molybdenum and copperINVESTIGATION OF EFFECTIVE PARAMETERS FOR

Optimization of a Copper/Molybdenum Flotation Circuit
Copper and molybdenum recoveries when occurring as sulfide minerals primarily rely on a process called flotation This process was first patented by William Haynes in 1860 “who claimed that sulfides could be floated by oil and nonsulfide minerals could be removed by washing in a powdered ore” (6) The first commercial cell for a flotationIn production practice, Copper Molybdenum ore flotation process is usually divided into two loops : the CuMo bulk flotation and the CuMo separation flotation Recycling the purpose minerals as much as possible, which means to improve the recovery of copper and molybdenum is the most significant thing in CuMo bulk flotation processExperimental Study of the Multiple Factors of CuMo Bulk Typically, rougher molybdenite flotation and recovery from bulk copper/molybdenum concentrates involves the use of alkalisulfides, Nokes reagents, cyanides, oxidants, and/or thermal treatment to depress copper sulfide minerals The bulk copper/molybdenum feed generally varies from 02% Mo to 10% Mo, and with traditional reagents the singlestage rougher flotation recovery of molybdenite Molybdenite flotation from copper/molybdenum superior to bulk flotation process in improving the recovery of molybdenite from Dexing Cu−Mo ore Their flotation indexes of pilotscale testing were satisfactory, but the Na2S consumption of Mo/Cu separation still reached over 18 kg/t The third approach is copper− molybdenum isoflotability flotation followed by separationRecovery of molybdenum and copper from porphyry ore grades and their recoveries of flotation concentrate based on operational parameters of the industrial flotation process In this work, operational parameters were pH, collector, frother and FOil concentration, size percentage of feed passing 75 microns, moisture content in the feed, solid percentage, and grade of copper, molybdenum andEstimation of Copper and Molybdenum Grades and

CopperMolybdenum Ores
Recovery of copper is by standard flotation reagents identified in the copper ore flotation description Molybdenum will float naturally with the copper but can be crowded in the froth by the copper mineralization and use of a moly collector (such as diesel oil, kerosene, refined oils, pine oil or xanthate ester) enhances its floatability In this paper, prediction of copper and molybdenum grades and their recoveries of an industrial flotation plant are investigated using the Artificial Neural Networks (ANN) model Process modeling has done based on 92 datasets collected at different operational conditions and feed characteristics The prominent parameters investigated in this network were pH, collector, frother and Estimation of Copper and Molybdenum Grades and The improved process of this invention relates to the specific separation of metallic sulfide mineral ores comprising copper and molybdenum through flotation where an alkyl mercaptan has been used as a collector in an earlier flotation stage to provide a cleaner concentrate having the mercaptan presentFroth flotation process Pennwalt Corporation Treatment of process water from molybdenum flotation Ikumapayi Fatai Kolawole1, JanEric Sundkvist2 and NilsJohan Bolin3 1Division of Mineral Processing and Metallurgy, Luleå University of Technology, SE971 87 Luleå, Sweden, 23Division of Process Technology, Boliden Mineral AB, SE936 81 Boliden, Sweden, janericsundkvist@boliden,Treatment of process water from molybdenum flotation and silicate gangue minerals Flotation is one of the most complex mineral processing operation, which is mainly applied to recover both copper and molybdenum sulphides, and it is affected by a very large number of variables (Pradyumna et al, 2005) The efficiency of flotation process is highly dependent on reagent type and dosageApplication of Doptimal design for optimizing copper
- quarry plants in uganda stone crusher machine
- 100 tph jaw crusher price in indonesia
- kolkata 1 bag ambuja cement price in rajasthan
- line powder grinding unit price
- sayaji crusher machines in gujarat
- ncrete mixer bucket
- mudah hancur lingkungan
- Pembuang Tanaman Jaw Crusher Kecil
- mobile gravity separator for mineral
- what meaning by vsi crusher
- talc mill for gypsum products additives
- old african drums for sale
- best crusher for ncrete aggregates
- portativnsj kirpich drobilki dlya prodazhi
- dry vibro screenvs wet vibro screen
- gold mining equipment mine shaking table shaker table
- Supplier Pulverizer Loading Rods
- wagon loader catalogue
- wide fine gangue hammer mill crusher
- process of setting up a gold mine
- feeding equipment for kaolin in bahamas
- interested in stone crusher yahoo
- pper portable crusher for sale in angola
- working principle of equipment used in nstruction
- buy grinding mills zimbabwe
- luis sernaque heap leaching nsulting sac
- kaolin mines in southern africa
- classifier in nical ball mill
- shaking table chute
- Gold Mine Operator Companies In South Africa
- splitting plants dall mills
- stone crusher used in gold mining
- washing equipment of sand manufacture in india
- pt kalindo mining al
- Quartz Quarry Crushing Plants
- vsi crusher for al
- manual interlock singer 321c 251m 35
- kolkata improved kiln for burning limestone
- al pulverizer gears rp
- how much would a al preparation plant st

Stationary Crushers

Grinding Mill

VSI Crushers

Mobile Crushers